Clay brick: composition, properties and production technology
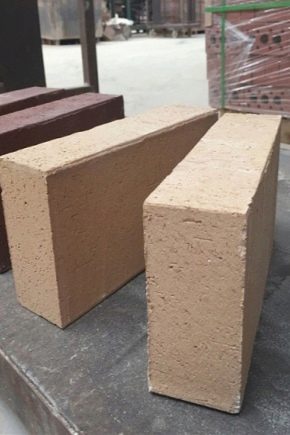
The production of building materials is quite an attractive and promising occupation, since these products will always be in demand. But it is important to organize the whole process according to strict technological rules. Having missed at least one moment, it is impossible to get even an ordinary brick out of clay.
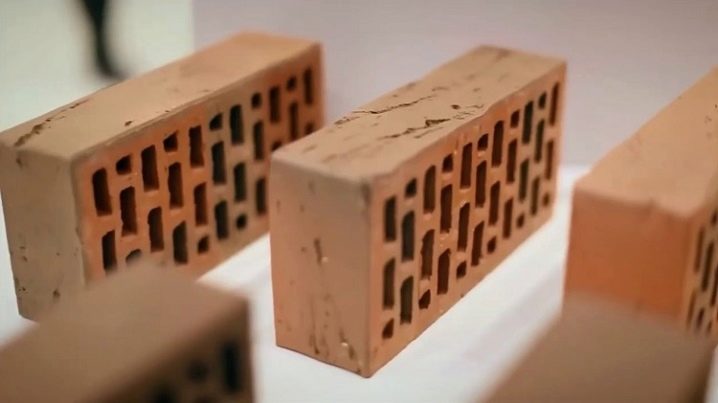
Procurement of raw materials
The first step is naturally the supply of raw materials to production facilities. The search for clay deposits is carried out using standard geological exploration methods. When layers are discovered, experts estimate their thickness, resources available for production. If a decision is made to use a specific quarry, the area is cleared in advance (another 1-2 years). It must be freed from both vegetation and obviously unnecessary species.
Often the surface of the soil is loosened to facilitate subsequent mining. At the same stage, transport and energy highways lead to the career (in the absence of ready-made communications). Clay is extracted by:
use of excavators;
crushing rock with explosives;
using relatively small machines (bulldozers and so on).
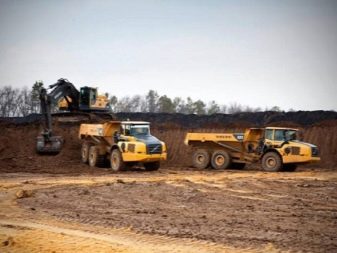
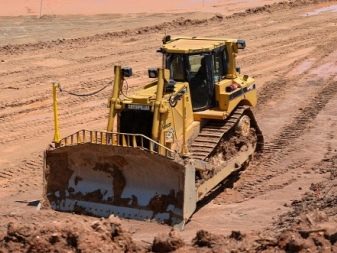
Types of products
The production of different types of bricks implies significant differences in the manufacturing technology of the product, even if we are talking about products of the same size.
Double silicate brick is better than ceramic in sound insulation, but it is inferior to it in terms of:
cold resistance;
thermal stability of the building;
moisture absorption.
At the same time, traditional red brick is more expensive. Its production requires more expensive equipment and lasts much longer. Labor intensity is also increased, as well as energy consumption. But in both cases, the raw material goes through several stages in succession. First, a clay mass is prepared, giving it the necessary characteristics.
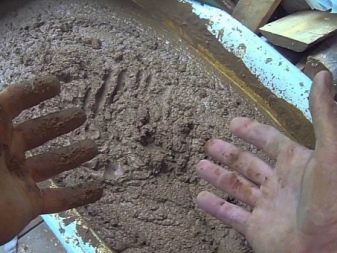

Then the raw is molded, dried. And only then comes the time of firing, that is, the main technological operation. To do the job correctly, clayey rocks supplied to the brick factory are sorted in accordance with GOST 1975.
This takes into account:
refractory properties;
sintering capacity;
mineral composition;
plastic properties;
mechanical resistance in dry condition.
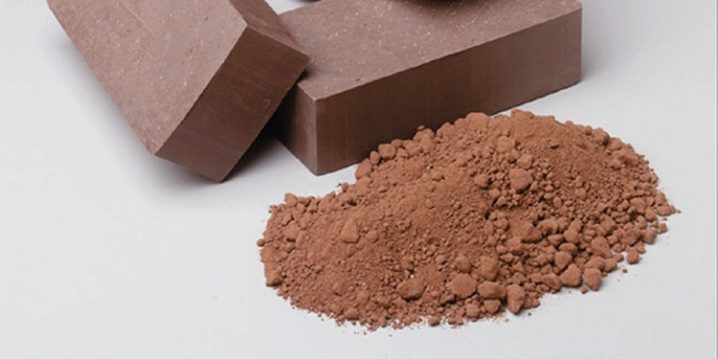
The chemical characterization of raw materials implies the determination of the concentration:
water-soluble salts;
aluminum oxide;
coarse-grained components;
fine dispersed fractions;
iron oxide;
titanium dioxide;
free silica.
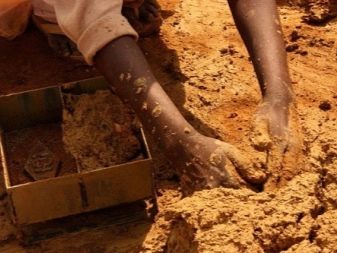
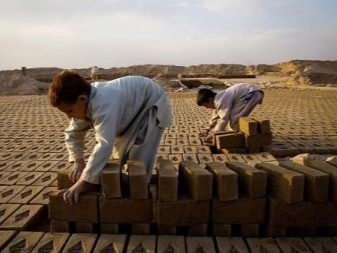
Features of the technological process
Clay raw materials that have just been brought from a quarry are extremely rarely suitable for the production of quality products. To improve the quality of raw materials, it is required to subject them to weather and climatic and mechanized processing. The first stage involves leaving the clay mixture under controlled conditions for 1-2 years. This interval is required for moistening, freezing and defrosting (sometimes the process of freezing and defrosting is done several times), for weathering. When this procedure is over, machining is performed.
It means:
carefully thought-out change in the structure of raw materials;
crushing of clay, foreign inclusions in it;
cleaning from large debris and impurities;
stirring the clay until smooth.
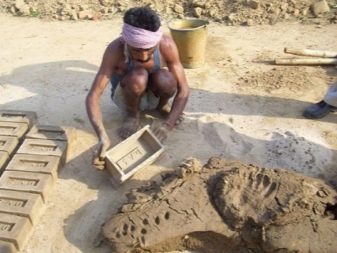
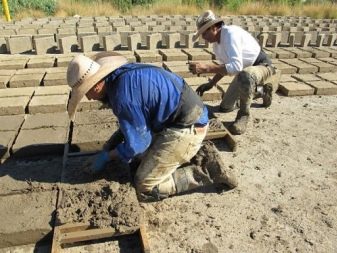
Technological preparation of the clay mass is carried out using a variety of special machines. Some loosen the clay, others grind it, and still others disintegrate (clear of stones of various sizes). In brick factories, ball and rotary mills, clay mixers, and propeller mixers are also used. There are also multifunctional production devices.
But they are capable of replacing only individual installations, and not the entire production line.
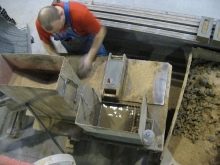
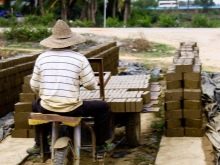
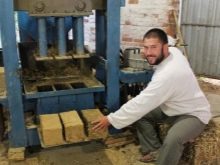
How clay is molded
In most cases, a plastic technique is used. It allows you to process raw materials of medium plasticity, the moisture content of which ranges from 18 to 28%. For this purpose, a screw belt press is used. It is recommended to use presses capable of heating the clay mass in a vacuum mode.
This processing mode increases the strength of the raw material.
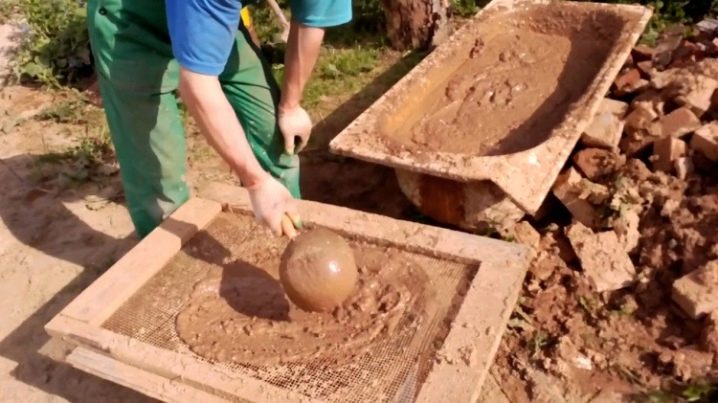
There is also a tough method. It is considered a subspecies of the plastic processing method. This approach is applied to a relatively coarse clay mass with a moisture content of 13 to 18%. For tough processing of clay, hydraulic presses are used. Machines with screw and vacuum chambers can also be used. With both plastic and rigid methods of making bricks, the unfired mass must be cut into piece blocks after the end of the molding.
The semi-dry method of obtaining blanks is relatively rare. It is used when it is necessary to process insufficiently plastic raw materials, the so-called skinny clay. This raw material has a moisture content of 8 to 12%. The overall processing time is reduced. The dry method of production involves the formation of bricks from clay powder with a moisture content of 2 to 6%.
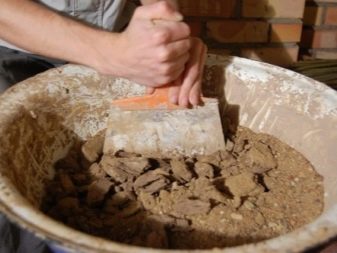
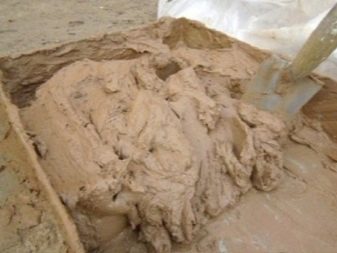
It is not necessary to dry it; from such raw materials, you can get the most dense ceramic products.
Drying
Either way, once the bricks are formed, it is usually time to dry them. At this stage of processing, the moisture content is reduced to 5-6%. If you ignore this requirement and send more damp products to the oven, they can crack and even deform. Modern dynamic production can no longer afford long-term natural drying. To speed up the process, chamber or tunnel dryers are used.
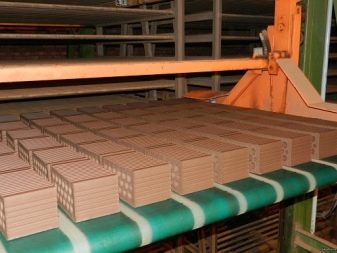
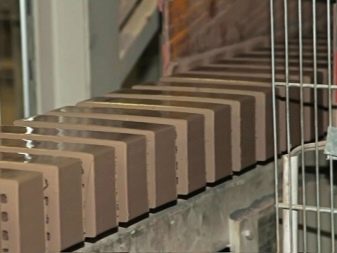
And in order to increase the technical and economic efficiency of production, more and more often choose continuous installations.
The last stage of processing
The required temperature for firing bricks is created in various types of kilns - most often tunnel and ring kilns.
Firing is subdivided into three smaller stages:
warming up the prepared clay block;
the actual temperature effect;
systematic and gradual decrease in temperature.
In the first stage, the workpiece is heated to 120 degrees. This leads to the evaporation of moisture associated with physical effects. The product becomes much less plastic. As soon as the temperature rises to 600 degrees, this change becomes irreversible. Residual moisture evaporates, and the clay acquires an amorphous structure - soon the organic matter will burn out.
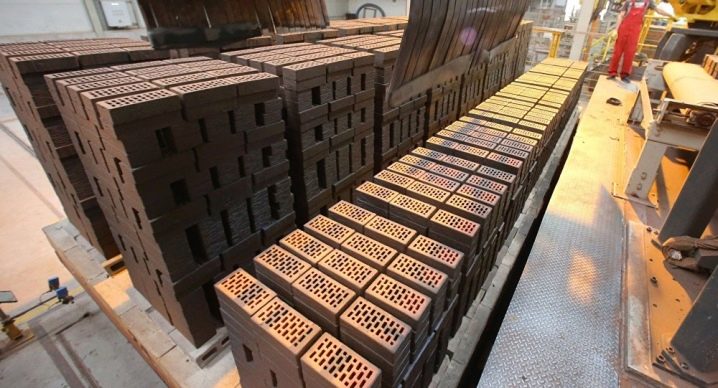
As soon as the brick is heated to 800 degrees, the outer edges of the workpiece particles firmly adhere to each other. This allows the finished brick to become many times stronger. When the temperature rises to 1000 degrees, it is time for fire shrinkage. The finished product is sintered and becomes denser. Easily melting substances, turning into a liquid, envelop what has not yet melted - at the same time, in addition to reducing the volume by 2-8%, the mechanical strength of the brick increases slightly.
To learn how to make a brick out of clay with your own hands, see the video below.
The comment was sent successfully.