Features of gas silicate bricks
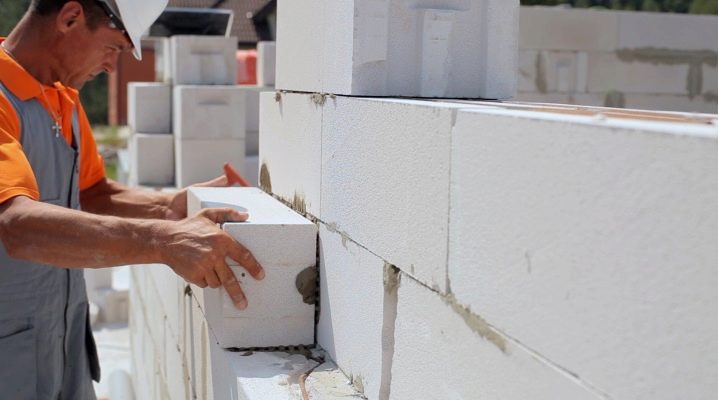
Silicate brick appeared on the building materials market relatively recently, but has already gained immense popularity among our compatriots. Its technical characteristics allow the construction of buildings and structures that meet all modern quality criteria. And if we consider the material from the point of view of price / quality, then gas silicate products will surely take one of the leading places.
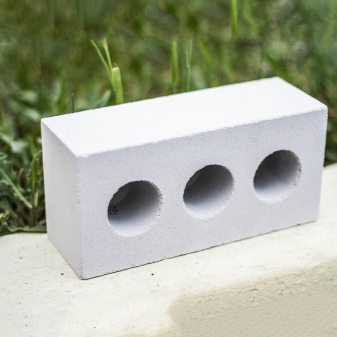
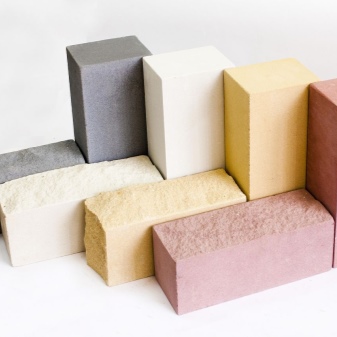
What it is?
Simply put, gas silicate brick is one of the varieties of porous concrete. At the exit, the material turns out to be rather porous, but at the same time its strength characteristics fully correspond to the parameters of concrete. The main difference is weight. Gas silicate blocks are less heavy - a decrease in the parameter is achieved due to the voids inside the pores.
In the 18th century, builders often added the blood of a bull or a pig to concrete and obtained a kind of prototype of modern aerated concrete: when mixing the components, the blood protein entered into a chemical reaction with other substances, and as a result, foam appeared, which, when solidified, was transformed into a durable building material.

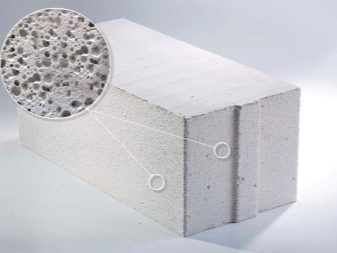
One of the most famous engineers in the Soviet Union, M.N.Bryushkov, back in the 30s of the last century, noted that when a plant called "soap root", growing in the republics of Central Asia, was added to the cement, the mixture immediately began to foam strongly and increase in size. During solidification, the porosity was retained, and the strength increased significantly. However, the most significant role in the creation of gas silicate was played by the Swedish technologist Albert Erickson, who created a unique technology for the production of the material by adding gas-forming chemical components to the cement.
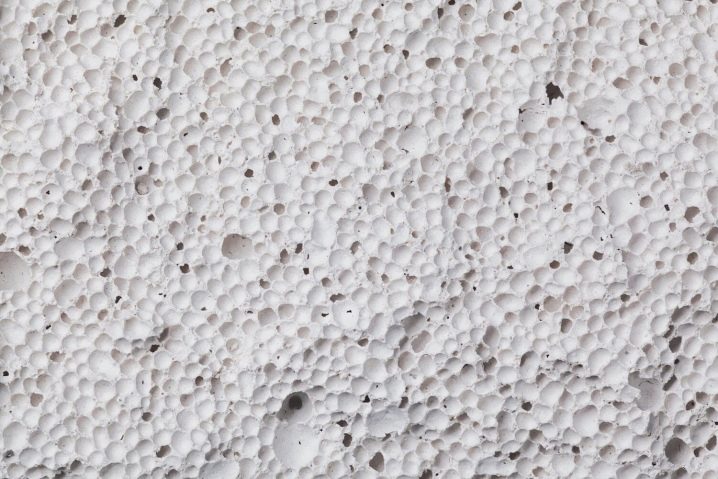
Today, gas silicate bricks are made from cement with the addition of sand and slaked lime. Then the mixture is passed through autoclaves and subjected to foaming with the addition of special magnesium dust and aluminum powder.
The finished substance is poured into molds, subjected to drying and hardening, which is achieved in two main ways:
- in vivo;
- in an autoclave under high temperature and strong pressure.
Higher quality blocks are obtained by autoclaving. In this case, they become more durable and resistant to external adverse conditions.
Thus, it can be seen that the gas silicate block is a rather uncomplicated composition of inexpensive and widely sold components, so the material is quite profitable for residential construction.
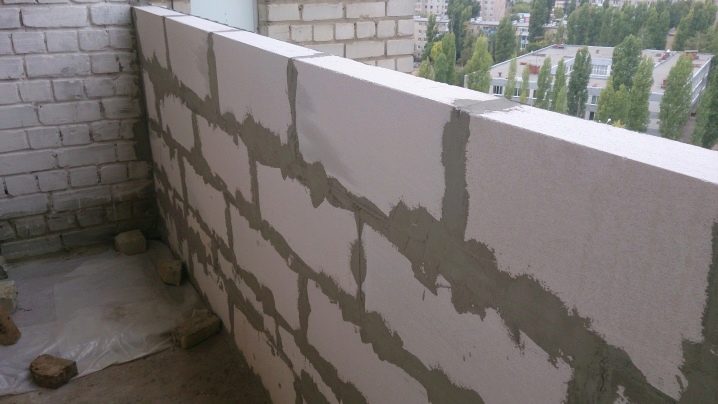
Characteristics and composition
The gas silicate material contains the following components.
- Portland cement of the highest quality, which is produced in accordance with applicable GOSTs. It is composed of calcium silicate (its share is at least 50%), as well as tricalcium aluminum (6%).
- Sand that is compliant with regulatory requirements. This brand is characterized by a minimum amount of silty and all kinds of clay inclusions, the content of which should be no more than 2%. It also contains quartz, approximately 7-8%.
- Process water.
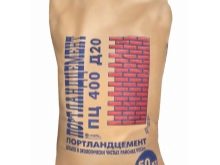
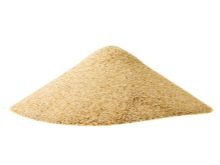
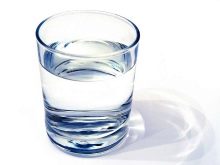
- Calcium lime, which is called "boiling pot", to create porous concrete requires a composition of at least the 3rd grade category. The rate of extinguishing of such a component is 10-15 minutes, while the proportion of burnout does not exceed 2%.The boiling pot also contains calcium and magnesium oxides, the total share of which reaches 65-75% and more.
- Aluminum powder - added for increased gassing, materials such as PAP-1 and PAP-2 are used.
- Sulfonol C is a surfactant component.
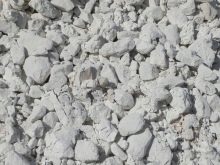
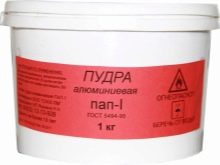
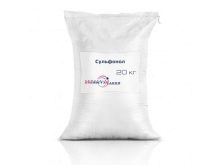
The composition and features of the technology determine the properties of the material, among which both positive and negative are noted.
The advantages of gas silicate bricks include the following characteristics.
- Reduced thermal conductivity. During the production of the material, the initial mixture is saturated with a large number of bubbles due to the content of aluminum powder; during solidification, they are transformed into pores, which significantly affects the thermal conductivity. That is, the more pores, the better the material retains heat.
Let us explain with simple examples. If you live in northern regions with harsh winters, then a wall 50 cm thick is quite enough to keep the heat inside the living space. You can get more, but, as a rule, a half-meter barrier is enough. In places with a warmer climate, the thickness can be 35-40 cm, in this case, even on cool nights, a favorable microclimate and a cozy atmosphere will remain in the rooms.
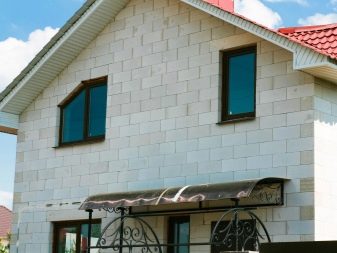
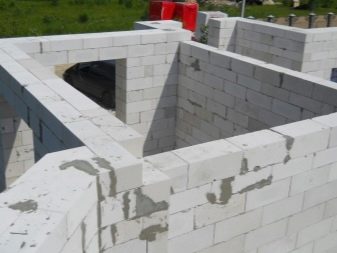
- An equally important feature of aerated concrete is good vapor permeability. If the humidity level in the room is higher than outside the house, then the walls begin to absorb excess moisture from the air and send it outside. If the situation is the opposite, then everything happens exactly the opposite: gas silicate bricks absorb moisture from the outside and transfer it to the room, this is especially true when the heating is turned on, when the air in the heated room becomes too dry.
- For residential buildings, the fire resistance of the material is of fundamental importance. Gas silicate walls can withstand contact with the flame for about 3 hours, as a rule, this time is quite enough to extinguish the fire, so in the event of a fire, the chances of saving the house are quite high.
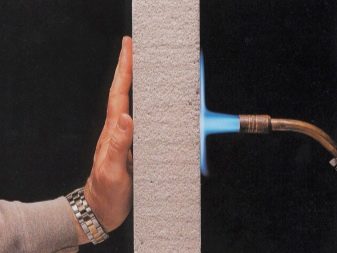
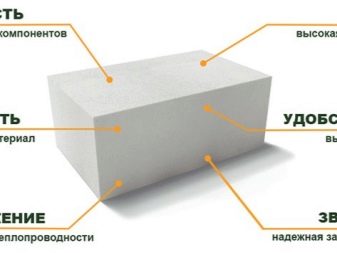
- The low weight of the bricks is also one of the undoubted advantages of the material. It is easy to transport, raise to a height, in addition, the structure does not create a large load on the foundation, and this significantly increases the service life of the house.
- Gas silicate blocks are made from natural components, so the material is environmentally friendly. It is quite possible to use it in the construction of preschool and educational institutions, clinics, residential areas and other buildings, where the absence of toxic emissions is of fundamental importance.
- Well, excellent sound insulation, which is possible due to the same porosity of gas silicate, will be a pleasant addition.
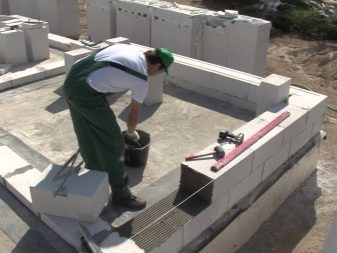
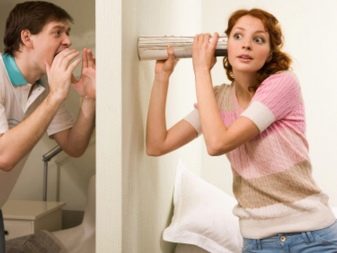
In order to get the most complete picture of the properties and characteristics of the material, it will not be superfluous to mention its shortcomings.
- The material has a rather low resistance to low temperatures. Without additional surface treatment, the composition can withstand no more than 5 freeze and thaw cycles, after which it begins to lose its strength rather quickly.
- Gas silicate complicates the repair work, for example, it is impossible to screw a dowel into such a material, it starts to fall out right there, and accordingly, even hanging a shelf in a house with gas silicate walls becomes a difficult task.
- In addition, gas silicate does not adhere to sand-cement plaster, therefore, it is unrealistic to decorate the wall with such material, it will fall off in a very short time.
- The pores absorb moisture quite intensively and retain it inside themselves. This leads to the gradual destruction of the material from the inside, and also creates an environment favorable for the growth of fungi, mold and other bacteria hazardous to health.
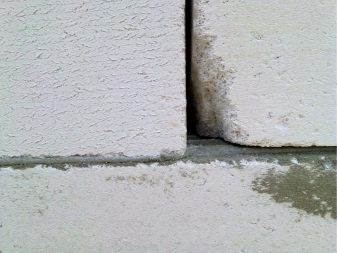
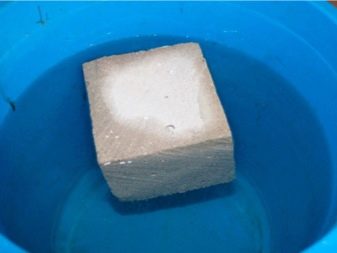
However, with proper processing of the material, many disadvantages can be leveled, so gas silicate does not lose its popularity among Russians.And the low price is still becoming a decisive factor when choosing a building material in our difficult times.
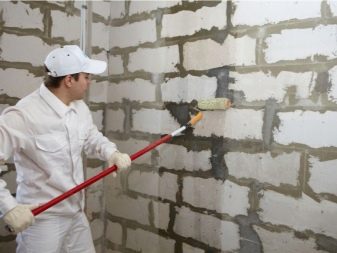
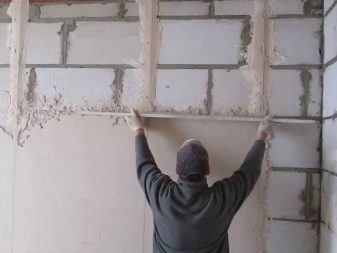
Weight and dimensions
One of the main advantages of aerated concrete building materials is their size, which is much larger than that of all other types of bricks. Due to such dimensions, the construction of buildings is much faster. According to some estimates, the lead can be up to 4 times, while the number of joints and connections is minimal, and this, in turn, significantly reduces all labor costs for construction and the consumption of anchoring mortar.
The standard size of a gas silicate brick is 600x200x300 mm. Also, builders distinguish a wall half-block with parameters 600x100x300 mm.
You can find products with different parameters from different manufacturers:
- 500x200x300 mm;
- 600x250x250 mm;
- 600x250x75 mm, etc.
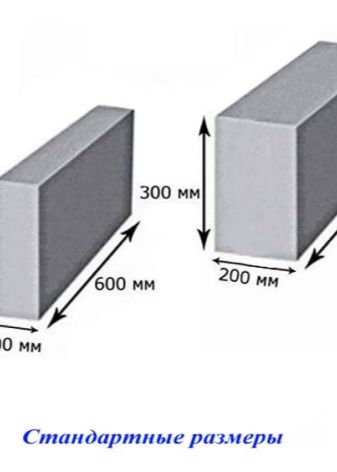
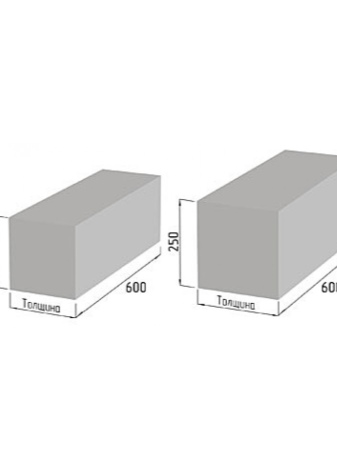
In hardware stores, you can almost always find products of the exact size that you need.
As for the weight, here the ratio is obvious: the larger the brick, the greater its mass. So, a standard block weighs 21-29 kg, the differences can be determined by the density indicator of a particular foam block. Weight is one of the basic advantages of the material. So, the weight of 1 m3 of gas silicate is about 580 kg, and 1 m3 of ordinary red brick is 2048 kg. The difference is obvious.
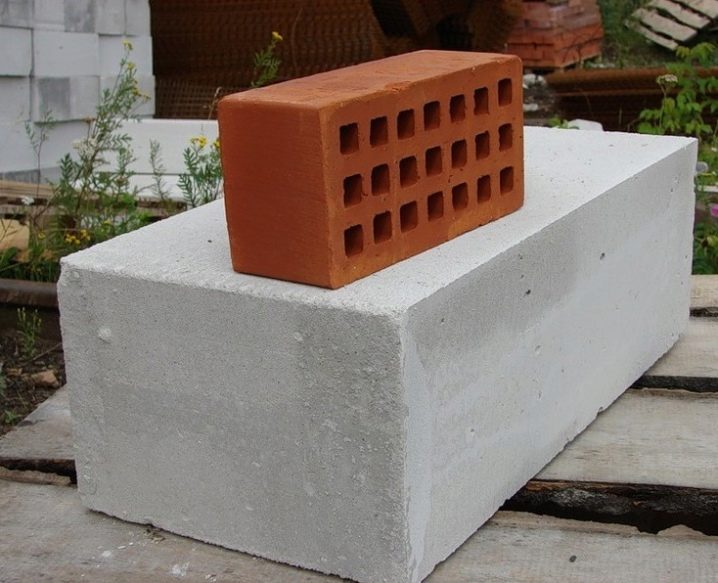
Areas of use
Depending on the technical parameters of the gas silicate brick, the scope of its use is also largely determined.
- Blocks with a density of up to 300 kg / m3 are most often used for insulation in wooden houses as a top layer.
- Blocks with a density of up to 400 kg / m3 are intended for the installation of load-bearing walls and partitions in single-storey construction. It can be both residential buildings and outbuildings.
- Gas blocks with a density of 500 kg / m3 will be optimal for buildings and structures of 3 floors.
- For multi-storey construction, blocks with an indicator of 700 kg / m3 are taken, while thorough reinforcement of the entire structure is required.
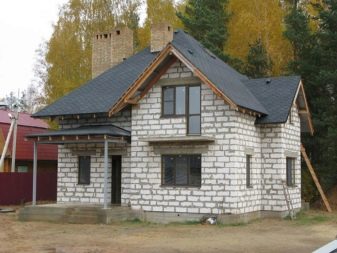
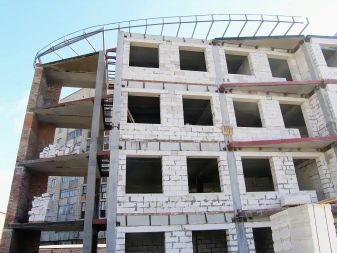
The use of gas silicate blocks allows you to reduce the overall level of costs, while the structures are quite unpretentious in maintenance and operation. However, it is important that all technology is fully followed. Any retreats are fraught with the collapse of the building, so the lack of reinforcement or improper use of finishing materials can lead to a great tragedy.
Taking into account the fact that aerated concrete has a fairly affordable price, and its installation requires a minimum of time, you can even build a house with your own hands without involving the labor of expensive hired professionals. Therefore, the material is often used for the construction of summer cottages, small houses and baths. Let us explain with an example: a house of blocks is built at least 4 times faster than a house of bricks. In addition, when working with bricks, assistants are required who will mix the mortar and bring bricks, which, by the way, are much more than blocks (one block is 16 bricks in size).
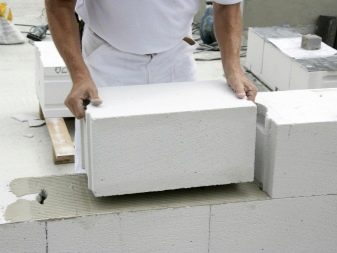
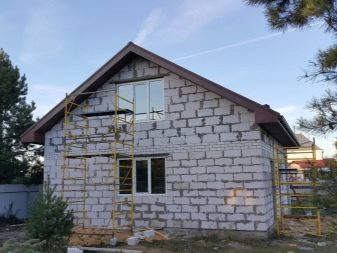
Thus, a quite obvious conclusion suggests itself - the use of gas silicate blocks is profitable and economically justified, which is why in recent years many developers have made their choice in favor of this material. However, professionals recommend adhering to some recommendations when using aerated concrete.
- When purchasing, you must personally check all purchased blocks. Various manufacturers allow deviations from GOSTs, therefore, chips, cracks and irregularities in the coating are often found on cheap bricks.
- When erecting 2 or more floors, it is necessary to install reinforcing support columns.
- Ceilings and walls made of aerated concrete cannot be left open, they require mandatory facing, otherwise the performance of the material is significantly reduced every year.
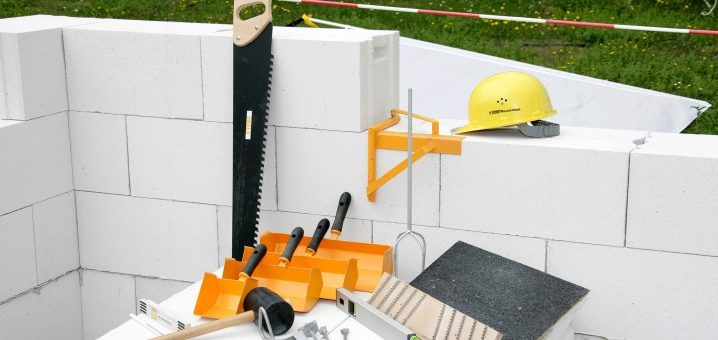
- It is strictly forbidden to erect aerated concrete structures on soils with a weak bearing capacity. During construction, it is imperative to equip a strip foundation, it is optimal for work using such materials. Keep in mind that gas silicate is a rather fragile material, therefore, with any displacement of the soil, it begins to crack, therefore, when building a house, it is important to correctly calculate all the parameters of the foundation and select the most resistant grade of concrete.
- When forming the first row of masonry, it is imperative to make a high-quality waterproofing of the basement in order to completely exclude moisture from entering the walls.
- The required size of the gas silicate blocks should be calculated in advance, the overlap of the seams is not allowed, as this can lead to a significant weakening of the masonry.
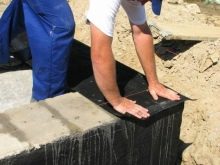
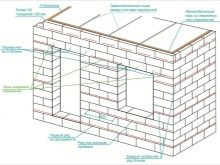
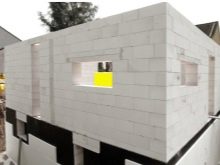
- Blocks with low density can collapse at high pressure, this suggests that before starting construction work, it is important to calculate the load on the material and draw up a detailed design plan.
For information on how the gas silicate block is used in construction, see the next video.
The comment was sent successfully.