All about engineering boards

If you are looking for a natural finish flooring, you should take a closer look at engineered planks. It will cost much less than solid parquet and will last much longer than laminate flooring. Such a finishing floor is characterized by high moisture resistance, unpretentious maintenance and decorative appearance. In this article, we will cover everything about engineering boards.


What it is?
Any engineering board has a multi-layer structure consisting of a plywood base veneered with durable wood species. The product can be varnished or sold without it - in the latter version, sanding and subsequent varnishing is performed on the spot during the installation of the parquet. The composition of such a board includes such three layers as:
- first layer - this is a protective coating based on paintwork materials or wax impregnation; its main task is to protect the tree from the adverse effects of dust, dirt and moisture;
- second layer represented by natural veneer - it is he who provides a decorative look to the dies, it is thanks to him that the flooring looks expensive and presentable;
- third layer - multilayer plywood; it is responsible for the deformation stability of the base, is not subject to decay, therefore it is optimal for creating a substrate.


The use of plywood sheets in the manufacture of boards significantly reduces the cost of production in terms of each square meter. Such a covering is much cheaper than traditional block parquet. Product design largely depends on the manufacturer and the characteristics of a particular collection. In the factory, a variety of veneer processing methods can be used, due to which the products acquire the texture of an expensive solid wood.


Materials (edit)
As a rule, to create an engineered board, valuable varieties of wood and plywood are taken in a ratio of 75% to 25%, artificial vinyl materials are not used. The top layer in most cases is made of beech, oak or ash. They are renowned for their hardness, strength and durability. Some manufacturers offer engineered planks in which the bottom layer is made from budget wood, usually knotty hardwood or softwood.
Such products are cheaper, but they are thicker and in many respects, in particular, in terms of resistance to wear, they are significantly inferior to boards with a plywood base.


Dimensions (edit)
The dimensions of the engineering board can be any, so you can choose the right option for both spacious rooms and the smallest ones. The most widespread are the following modules:
- length - from 50 to 300 cm, 600 cm boards are allowed, in the latter case they are made to order;
- width - from 10 to 45 cm, most often they buy models in the range from 15 to 25 cm, wide boards are used less often; this parameter directly depends on the type of wood used;
- thickness - depends on the size of the layers, but in most cases ranges from 15 to 25 mm.


Advantages and disadvantages
Any finishing material has its advantages and disadvantages, therefore, before choosing a floor covering, it is necessary to scrupulously study its main features. The tree looks elegant and beautiful, but with the wrong choice of boards or mistakes during maintenance, it will not last long. Among the main advantages of the finishing floor under consideration, the following can be distinguished:
- durability - the material is characterized by resistance to abrasion, even with prolonged use, scuffs and scratches do not appear on it, it can be mounted in rooms with the highest traffic;
- resistance to unfavorable environmental factors - with temperature fluctuations, contact with moisture, as well as under the influence of ultraviolet radiation, aesthetic and technical and operational properties are fully preserved;
- good maintainability - the veneer is represented by a rather thick layer, therefore, when the coating wears out, it is possible to remove 1–2 mm and carry out scraping, as a result, the wood returns its aesthetic appearance, and the density of the coating does not suffer;
- high insulating parameters - the multilayer structure of durable plywood layers dampens noise much better than laminate boards and solid wood parquet strips;
- engineering plates of various shapes and sizes are on sale; they can have a small or large pattern.


Among the disadvantages of the board, the following should be noted:
- the difficulty of installation in the absence of finishing skills;
- high material price.
The cost of one square meter of varnished board starts at 2 thousand rubles. To this you will have to add the purchase of glue and payment for the installation of the coating.
However, all these expenses will fully pay off with durability.


Comparison with parquet and laminate
Inexperienced users often confuse engineered planks and parquet floors. Visually, they are similar to each other; they differ significantly in operational parameters and structure. The material made of plywood is much cheaper than its analogue made of wood dice, although in terms of user characteristics it wins in many ways. Engineering board, in contrast to traditional parquet, is characterized by greater moisture resistance, it is much less susceptible to damage by fungus, mold, as well as warping, swelling and other types of deformations. In terms of resistance to scratches and mechanical damage, both coatings are approximately the same.
The parquet board is quite thick, so it can be looped many times. Engineering is inferior in this parameter, so it can be restored no more than 1-2 times. If you compare an engineered board with a laminate, the difference is obvious. The first is more practical and durable, and it looks more respectable. But the laminate is easier to install and wins in terms of maintainability.

Which one to choose?
The engineering board is presented in three categories.
- Rustic. To create the outer layer, veneer is used, obtained by sawing at different angles. At the exit, the boards may differ in texture and colors, slight defects are allowed. Such products are cheaper than others.
- Natures. Lamellas are formed by the tangential (tangential) or radial (along) sawing method. Of the defects, there may be a slight difference in shade and texture. This product belongs to the average value group.
- Select. In this case, the veneer is used, obtained by sawing along the direction of the fibers. Boards of this type are identical in texture to each other and have no flaws. This variety is the most expensive.



Popular manufacturers
Consider the most popular manufacturers.
- Bolefloor (Holland). This manufacturer was the very first to bring to the market engineering boards with curved edges. The thickness of the veneer layer reaches 5 mm. Most of the products are made in a traditional style without any newfangled effects. The products belong to the elite category.
The price reaches 17 thousand rubles. per square meter.


- Marco Ferutti (Italy). The thickness of the decorative layer is not less than 3 mm. The production uses exotic types of wood (American walnut, Hungarian merbau, Burmese teak and others), as well as oak.The brand's products are available in a wide variety of patterns and decors. The average cost on the market is 8 thousand rubles. per square meter.


- Global-Parquet (USA / Malaysia). The company produces two- and three-layer boards. The thickness of the veneer is up to 5.5 mm. The modern Treffet technology is used for varnishing, due to which the operating period increases to 35 years. The products do not require additional maintenance. The cost on the market is 3.5 thousand rubles. per square meter.


- Bauwerk (Switzerland). These are two-layer engineering boards with a veneer layer up to 5 mm, presented in several collections. They are offered in various standard sizes, there are both exclusive models and democratic ones with a cost of 4 thousand rubles. per square meter.

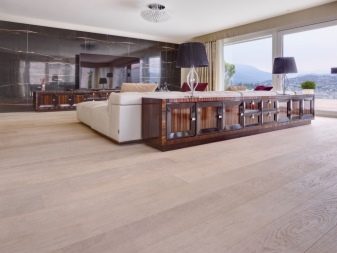
- Wood Bee (Holland). The veneer thickness is 7 mm; premium segment products are offered for sale, as well as budget options. The cost starts from 3 thousand rubles.


Laying rules
Planking of an engineered board is carried out indoors at a temperature background of +18 degrees and a humidity level of about 65%. In the room, you should turn on the heating in advance, as well as the ventilation system, since the material must lie down in this room for at least a day. The engineered board is placed on a carefully leveled surface, the base should not have any defects and protruding fragments.
Installation can be carried out in three ways, such as:
- on glue;
- for concrete mortar;
- on a synthetic backing.
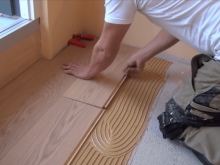


The most rational and practical is the option with the use of a special synthetic pillow. This material creates conditions for maintaining full air circulation and thus eliminates the occurrence of fungus and dampness. Installation directly on concrete is the cheapest, and besides, it is performed rather quickly. However, user experience has shown that laying on concrete without a backing will significantly shorten the life of the coating.
Let's dwell in more detail on the features of laying on a synthetic pillow, for this you need to follow the steps below:
- the screed is cleaned of sand particles, fine debris and other types of contamination;
- the surface is treated with a primer for porous substrates, after which a perforated pillow is laid, fixing it along the edges with glue;
- then proceed directly to the installation - the rows are laid, starting from the wall, while the perforated holes in the substrate must be filled with glue.



Important! The seams should go in different directions, so every second row should be started not from the whole board, but from its part. To achieve the maximum joining of the grooves, it is better to use a mallet.
Thus, the entire finish is laid, the glue must be applied to the surface right before fixing the board.
When designing the very last row, additional adjustment of the panels may be necessary. At this stage, small irregularities may appear at the junction of the slabs and the wall, they are masked with a plinth. After the glue has completely hardened, the floor can be used without any restrictions.


Care
Natural wood is highly sensitive to external influences such as temperature fluctuations and moisture. This is not surprising, since the materials are of natural origin - in the natural environment, trees always obey natural phenomena, react to temperature, the movement of the sun, as well as humidity. That is why the surface of the finished floor must certainly be protected, usually oil or varnish is used.
The oil coating is environmentally friendly, safe, it has the ability to deeply penetrate the wood structure and create a high level of protection. The coating acquires high wear resistance, easily tolerates temperature fluctuations and high levels of humidity. In case of damage to the surface, it is not difficult to restore the appearance of the engineered board - you just need to grind the area and re-impregnate it.The oil does not form a film, so the wood retains its natural color and texture.

Varnishes are mainly used on a water basis, so they do not contain toxic substances. This composition does not penetrate into the structure of the wood, therefore, there is no interference with the material; over time, the varnish can always be replaced with an oil coating. This treatment will last 5 to 10 years under standard operating conditions. However, it is important to treat the varnished board with care, as it reacts very strongly to any point damage. There is no need to ride on it on rollers or defile on heels, and it is advisable to stick soft rubberized pads on the legs of the furniture.
Both types of coatings provide a good protective and decorative effect, but the oil should be preferred in the following situations:
- when the floor is laid in a room with a high level of humidity or long periods of unheated periods are planned;
- when installing the "warm floor" system;
- to create accents on the natural texture of wood.


The finishing floor from the engineered board should be maintained regularly.
Any contamination must be removed as quickly as possible, otherwise they will be completely absorbed, it will be almost impossible to remove them. It is important to dry clean every day and remove all solid particles of street dirt and sand, the best option would be to use a vacuum cleaner with soft pads. For wet cleaning, use soft textiles soaked in concentrated soapy water and carefully wrung out. Chemical detergents are not recommended, since the coating may dissolve, the lamellas will be defenseless against aggressive external factors.
If the pollution is small, then you can always do with plain water without any impurities. Traces of berries must be washed off with hot water, and blood only with cold water. It is better to rub old fat with acetone, but too frequent use of it will destroy the decorative coating. Freezing helps to get rid of traces of adhering gum, rubber shoes and bicycle wheels - the ice must be wrapped in a bag and put on a contaminated area, and after a while the frozen particles must be carefully scraped off with a knife.

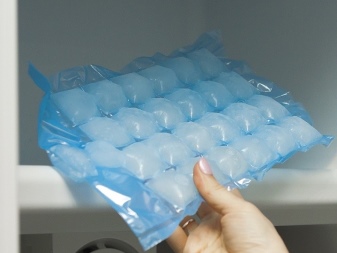
Review overview
User reviews about laying the engineered board are mostly positive. The product is distinguished by wear resistance, stylish appearance and durability; products made in Russia, Sweden and Germany are in especially high demand. The installation of the finishing floor does not require professional training and special tools. As practice shows, it is much more difficult to install plastic windows and adjust them. However, there is no need to rush during the work, since after the adhesive has hardened, it will be extremely problematic to change the position of the glued plate.


Examples in the interior
In the design of the premises, a variety of shades of engineered boards are used.
- Eclipse is the most popular among the dark ones. It is a black, non-glossy color that resembles charcoal.


- Brown engineering boards look impressive, for example, Emperador Dark Brown with imitation of marble and white veins.


- The color of the gray stones creates a neutral background. Stone Gray is often combined with white and pink hues, and is also offered in a noble version with a silver sheen or patina.
It is often used for finishing floors in kitchens and hallways.


- A warm white tone with an almost imperceptible presence of pink and yellow tints gives an imitation of limestone, it is laid with a "French Christmas tree". By its appearance, it evokes an association with the ancient stone walls of castles.


- Light shades add volume to the room, visually expand the boundaries of space and favorably set off the furniture.


- A nutty shade lasts out of time. Warm chestnut color harmoniously fits into most stylistic trends in design.


- Engineered board is very similar to solid wood, therefore its use in the arrangement of the premises creates an atmosphere of warmth and comfort in the living room.


See the following video for the main differences between laminate, parquet, engineering and solid boards.
The comment was sent successfully.