Laying options for engineering boards

Laying an engineered board has many subtleties. It can be placed on plywood and on a screed; various technologies and installation methods can be used. Silane glue for installation deserves attention, as well as how to properly lay it with a herringbone.



Basic ways
Glue
For laying the engineered board, one-component or two-component adhesives can be used. The vast majority of manufacturers create formulations based on polyurethane compounds. The reason is simple - these substances form the compounds most resistant to water ingress. Modern compositions can be used for the installation of an engineering board on:
- screed;
- wood sole;
- chipboard;
- oriented slabs;
- plywood;
- multimol with a strengthening effect (analogue of reinforcing glass fiber wall).


But it is worth noting that the manufacturers of the engineering board do not recommend mounting it on top:
- plaster-based self-leveling floor;
- cork backing;
- cable heating floor.
The adhesive solution is suitable for standard and curved boards. In both cases, the layout is done after preliminary calculation.

Combined
This option involves the use of not only glue, but also specially selected self-tapping screws. Instead of them, sometimes they use "hairpins"... Fasteners are driven into the grooves of the lamellas at an angle of 30 to 45 degrees. This technique is considered better than other types because it is very reliable and ensures the durability of the assembly. However, the cost of consumables is quite high, and you will have to spend a lot of time for installation.


Floating
This name was given to the installation of an engineering board with standard Click system locks. The material to be laid will not be mechanically bound to the substrate in any way. The design will be made quite tightly and reliably. No additional processing is required. However, this solution is of little use for tongue-and-groove and keyway options, for work it is necessary to involve trained specialists, and the base must be prepared as carefully as possible.

Into key
This method is widely used for joining boards made using the “thorn-groove” technology. The technology has been worked out for the arrangement of houses made of poorly dried timber. The insertion elements will not be particularly affected by shrinkage. The geometric design is kept within the normal range. The installation of an engineered board in a dowel, experts also advise for the most damp regions and areas, such as the Primorsky Territory or the Black Sea coast.
Long fragments are best placed, shifting them by about a third. Then tying the products in a circle at the ends will not be difficult. Visual correspondences and discrepancies between the individual planks must also be taken into account in order to create a clear and consistent pattern. Therefore, it is obvious that before laying out in any way, the lamellas should be carefully laid out and distributed in a certain way.
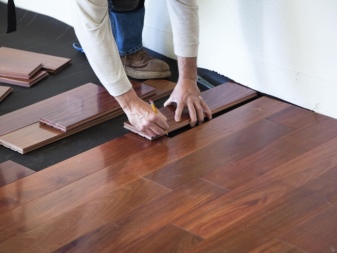

The laying on a concrete screed deserves special attention. This option is most often practiced. But a prerequisite is sufficient evenness of the base itself. If its geometry is broken, you will have to level the substrate with plywood. It is best if the moisture content of the screed on the surface does not exceed 6%. In this case, you can refuse to use waterproofing materials.
Plywood is almost always placed on top of wooden subfloors.The exception is those situations when the rough base is already in perfect condition. And even then you need to think three times before giving up the mediating substrate. After all, the grassroots floor can be damaged by a variety of dangerous factors. Plywood is put especially on logs when complex preparation is needed.


Tools and materials
The engineered plank can be laid on top of the wood flooring with one-component silane adhesive. Its principle of operation is not the same as that of polyurethane glue. When such a substance is used, an elastic joint is formed. As a result, a change in the moisture content of the wood will not particularly affect the mechanical properties of the joint and its reliability. Silane formulations harden quickly and finishing can be started in a short time.
Also, in favor of silane adhesives, they speak of safety for humans, the ability to do without complicated grinding work. If such a substance gets on your hands, it will be quite simple to remove. The same, note, applies to glue spots on the floor or other surface. With skillful use, such an objection as the rather high price of silane compounds disappears.


Important: you cannot use any water-based adhesive mixtures - they will negatively affect the wood, the adhesives themselves are always applied with a notched trowel or a special roller.
Also useful for work:
- screwdriver;
- special tool for fastening staples;
- self-tapping screws and dowels of a suitable size (it is not recommended to replace them with nails);
- plywood or final screed (providing final alignment);
- mallet;
- surface leveling compound;
- deep penetration soil;
- saw, hacksaw or parquet floor;
- sandpaper;
- Angle grinder (for larger-scale grinding);
- a nozzle in the form of a whisk for mixing the solution;
- tightening belts (needed when you have to work with grooved parts or curved products);
- wooden wedges for spacer;
- construction tape;
- a good pencil (or better a marker);
- square.


Technology
Preparation
According to generally accepted rules in a professional environment, a deck or engineered plank can only be put on a stable base (tie). And stability is achieved only after a set of the necessary conditions by finishing pouring (which happens in about 30 days). This may require meticulous sanding of the screed. Of course, before the work itself, you will have to get rid of any dirt and dust - and this is also a significant component of preparation. Concrete is primed only with deep percolation compounds (all other mixtures are not effective enough).
A different approach is practiced when working with plywood substrates. To begin with, the sheets (with a layer of at least 1.5 cm) are cut into squares with the same side. Important: if there was already a wooden floor in the room before, all decorative covering must be completely dismantled. Plywood is placed in rows, carefully controlling so that there are no coincidences of adjacent joints. The cut fragments are placed so that minor compensating gaps remain.
It is best to fix the plywood backing with self-tapping screws. Hats are advised to be sunk completely so that they do not cling to anything and do not interfere with further work. If the curvatures are very large or cardinal insulation is planned, the plywood is supported with logs. Experts advise to check the geometry of the log using a hydraulic level. On the first and basement floors, you cannot do without laying out a waterproofing film.


Important: on top of the hydraulic barrier, plywood is not laid out in squares, but in the form of whole sheets. This is much more reliable and efficient. Plywood is sanded to compensate for possible subtle deformations. Residual dust, dry dirt can be removed with a vacuum cleaner. When this is done, a layer of soil is applied; additionally, it is worth considering that the largest allowable difference in the height of the substrate is 2 mm by 2 m.

It is impossible to refuse priming, because otherwise it is impossible to ensure decent adhesion. When using the lag, they will certainly mark their course. The lamellas of the engineering board themselves must be laid out at an angle of 90 degrees to this move. It is possible to attach longitudinal and transverse logs "in half a tree", although some people successfully use ordinary nails for this. The curvature of the wall is marked with dragging.
After the center lines of the lag are drawn on the sheet, you can start editing. First, one sheet is installed, and then other structures are attached to it. The material itself must be kept indoors for at least 72 hours to adapt to its climatic conditions. To cope with irregularities, the cavities are filled with cement mortar. Cracked areas and bumps are selected with a chisel or perforator.

Mounting
In order to properly lay the engineering board, you must first choose a clear installation scheme and then strictly follow this scheme. If it is decided to use glue, it will be possible to use boards of a regular or curved shape. However, the correct layout of the material becomes critical, because it will be almost impossible to dismantle and transfer it again. Sometimes it is necessary to mount boards of different lengths - and in this case, as already mentioned, a shift of 1/3 is necessary for the greatest reliability in the assembly.
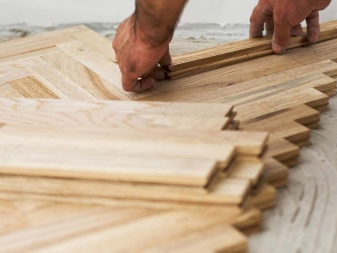

The side slats for the floor can only be laid after cutting. Important: they should be cut strictly according to the plan. The mortar applied with a notched trowel is leveled over the surface. Next, put the boards, which must be firmly pressed to the base. Particular attention is paid to the fit of all seams. The glue will set in 30-90 minutes, depending on the chemical composition and temperature conditions.
Quite a few people are interested not only in technical details, but also in how to lay an engineered board with a herringbone. In the English format, rectangular boards are used. If a "French herringbone" is used, then there should be cuts from the ends at 45 degrees.
Different types of deck masonry differ in how much the elements move in relation to each other. It is also worth considering that in case of deck laying, placement can be applied both in a straight line and diagonally.



To create a floating floor, you have to lay the engineered plank on a plywood, cork, duplex or softwood backing. A special multi-layer product (the same duplex) guarantees protection against moisture and dampens extraneous sounds. This material also improves the quality of ventilation. Coniferous structures increase sound insulation well and are generally environmentally friendly. The cork, again, dampens the sound, but not only - it has an excellent dampening effect, zero allergic activity, does not accumulate static electricity.
A very important topic is how to make a joint between a tile and an engineered board. With the right approach, you can do without a nut at all. It is impossible to completely do without the design of the joint, because these materials have different coefficients of thermal expansion. The gap should be between 6 and 14 mm, and the main problem is how exactly to close it. On the inner border of the room, the seams can be bridged with a classic wooden skirting board, sometimes PVC and MDF skirting boards are also used.
In some cases, it is still more correct to form a full-fledged threshold. These are strips of stainless steel, the same PVC, MDF or wood. It is customary to put the thresholds on glue. When installing floor coverings in one layer, you can simply overlap them with a sill with a small overlap, fastening is done with hardware that comes in the set. In more complex cases, surface pads are used that can compensate for differences - from 1 to 7 cm wide and from 90 to 300 cm long.


Sometimes thresholds with hidden fastening can also be used. At the bottom they have a pair of metal edges that form a kind of groove. A hole is drilled at the base where the dowel is inserted.The fasteners must be inserted into the longitudinal retainer. The structure is brought closer to the joint so as to completely close the resulting gap (the width of such sills varies from 2.5 to 10 cm, and their length can be either 90, 180, or 270 cm).
If you don't like any thresholds, you can install a cork expansion joint. The typical version is coated with a layer that protects against water and premature wear. The combined expansion joint contains strips of valuable wood. It is used to connect materials of different types, as well as in rooms decorated in an elite manner. But such compensating systems are incompatible with floors laid using floating technology - in such situations, it is more effective to use sealants or cork seals.


The following video talks about laying an engineered board.
The comment was sent successfully.