Description and selection of grooved boards

What grooved boards, where they are used, how they differ from ordinary sawn timber - all these questions often arise among people who choose wood for construction and decoration. Indeed, laying timber and other elements with an unusual edge allows you to get a strong connection, while the flooring remains breathable, safe for the environment and human health. But how to choose and mount 36 mm tongue and groove and other sizes for walls and floors in the house, it is worth understanding in more detail.
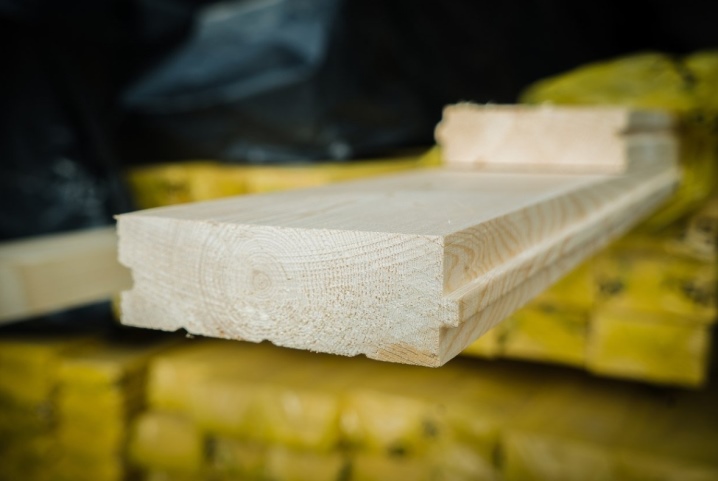
What it is?
Tongue-and-groove board - a type of lumber with a special edge shape. On one side there is a longitudinally located protrusion, on the other - a groove for its exact entry. The grooving of the board means the formation of such a connection, its name comes from the German word spund - cork, plug. The lumber is passed through a grooving machine, for this purpose high quality dry wood is selected. In terms of its properties, the finished tongue-and-groove is superior to similar spike elements.
Let's analyze in detail the process of making such a board.
- Sawing logs. Only the core is suitable for the manufacture of the sheet pile, the rest of the material is not used.
- Drying. The resulting blanks are dried in a heat chamber.
- Machining. The future grooved board is planed, receiving a base with precisely specified geometric characteristics.
- Milling... At this stage, the spikes and grooves are cut.
- Additional processing. Most often it includes the application of an antiseptic or flame retardant impregnation.
- Package. The finished lumber is placed in a protective polyethylene sheath, excluding changes in the moisture level during storage and transportation.

In addition to the production of boards of different sizes, such processing of the ribs is used in the manufacture of timber, moisture resistant plates... This method of edge processing is used in cases where it is necessary to evenly distribute the load on the material in the volume. Sometimes this type of board is also called parquet due to the nature of the styling. Profiled shaped lumber during installation, they form a lock, excluding the appearance of through cracks, heat leakage.
The use of a grooved board is quite varied. In the construction of houses and baths, it is used in the ceiling cladding, for wall decoration and flooring of the final floor.


Overview of varieties
The grooved board, like any shaped lumber, has division into varieties according to established standards... The main differences here are in the presence and number of defects that are allowed when processing the front of the product. There are 4 varieties in total.

Extra
It is also referred to as euro groove... Products in this category do not have color differences over the entire surface, they are uniform, no visible defects, no knots allowed. Euro groove is more expensive than other categories, such products are intended for indoor use, finishing work.


First
He is more often denoted by the letter A. Products should not have large cracks and knots in the array. Permissible differences from Extra class products include slight difference in surface color, sporadic spots. This grade is also focused on the interior decoration of buildings and structures; it is not used in the exterior cladding.

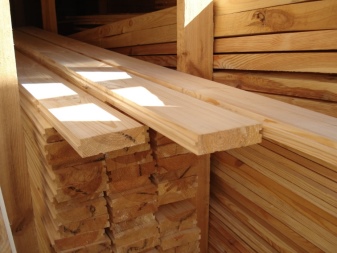
Second
More often denoted letter B. In the products of this class, the presence of captive knotty inclusions in the solid wood is allowed. The presence of visible cracks or cores is not considered a defect. Defect includes the appearance on the surface of the material of blue spots and other traces of fungal infections.
The 2nd grade grooved board is suitable for interior wall and floor cladding in non-residential premises. In residential buildings and structures, it is used for cladding for painting.
It is not used for finishing without additional processing.

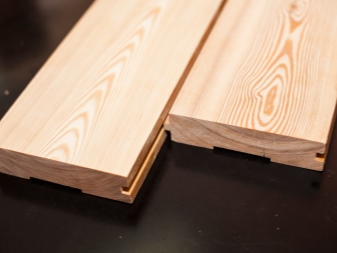
Third
Class 3 (or category C) includes all products that have multiple defects. This includes a grooved board with cracks, a large number of knots, including falling out. An unevenly colored surface, resin pockets, and cracking also indicate that the wood belongs to grade 3.
Its purpose is sub-flooring, wall cladding in non-residential and utility rooms.


Materials (edit)
When classifying different types of grooved boards, considerable attention is paid to the type of wood used in the production process. If chipboard is often created from waste, then the selection of raw materials is taken very seriously. Several tree species are considered the most in demand.
- Conifers... First of all, these are spruce and pine, rather soft, but affordable. Such finishing of the floor or walls requires additional protection from external influences, contact with moisture. Due to the low abrasion resistance, a tongue-and-groove board made of these materials can only be used in rooms with low traffic.


- Larch... Material with a solid and dense structure, great for verandas and terraces, not afraid of contact with moisture. Larch wood does not require a special protective treatment, it resists rotting and other external threats well, it has an attractive pattern.

- Linden and aspen. These types of wood are considered a good choice for decorating rooms in a bath, they have medium strength, high moisture resistance. Linden and aspen sheet piling is not intended for use under significant mechanical stress. The wood is rather soft and does not resist abrasion well.

- Cedar... Unlike soft conifers, this material is considered hard and very durable. It resists moisture well, has a dense structure that is not subject to decay and deterioration. Cedar is highly valued for the attractiveness of the pattern of its fibers, it releases aromatic substances into the air that have an antibacterial effect.
Such wall or floor cladding is very beneficial for the health of people living in the house.


- Oak, ash, beech. The hardwoods of these hardwoods used in the production of tongue-and-groove boards are elite. In addition to mechanical strength, these rocks have an attractive structure and do not require additional finishing. Such wood is durable, practical, but quite expensive.

These are the main types of wood that are used in the production of grooved boards. The choice of a specific option largely depends on the conditions in which it will be operated.

Dimensions (edit)
According to the established requirements, the dimensional parameters of the grooved board are determined GOST 8242-88. For it, the DP marking is installed, which determines the main purpose of profiled sawn timber - for flooring. The standard approved sizes DP-21, DP-27, DP-35.
In addition, manufacturers often produce tongue and groove according to technical specifications. In this case, the size range varies within the following limits:
- thickness 20, 22, 27, 28, 36, 40, 45, 50, 70 mm;
- width in the range of 64-250 mm;
- length from 1 to 6 m, step 50 cm.

It is worth considering that for shaped sawn timber, one of the most important quality indicators is also the level of moisture. For high-grade products, it is set within 9-12%, low-grade products allow an increase in this characteristic up to 18%. The geometric parameters of the board in the area of the spike and groove must be unchanged, a deviation of 3 mm is allowed in length, and no more than 1 mm in width and thickness.

Selection Tips
When choosing a suitable grooved board for construction and finishing work it is recommended to keep in mind a number of key points that are important.
- Grade of material. When it comes to floorboards, class A material is a rational choice. It is quite good for finishing installation, but it is not very expensive. Small inclusions of knots will make this coverage more "lively" and natural. For the ceiling and walls, the material of the Extra grade will be a more preferable solution.

- Correct storage. A high-quality grooved board is supplied in a plastic wrap package. If we are talking about products of a well-known brand, the company logo and brand name will be printed on the protective coating. The packaging at the time of purchase must not have any signs of opening.


- Finish type... If the board is chosen for subsequent painting, you can save money by choosing a material of a lower grade. Possible defects will not be visible under a layer of paintwork.

- Wood species. Soft woods are suitable exclusively for wall cladding, but spruce and pine, due to their high resin content, cannot be used in heated rooms in a bath or sauna. On the floor, it is worth selecting a tongue-and-groove made of solid hardwood.

- Visual characteristics. It is important to inspect the boards before purchasing, to make sure that they correspond to the specified grade, do not show signs of damage received during storage and transportation.
Any traces of warpage - changes in the correct geometry - indicate that the board does not meet the stated requirements.

- Dry wood. A high-quality tongue and groove will make a ringing sound when tapped. In addition, trade organizations should have special instruments for measuring humidity. With their help, you can make sure that the wood indicators for this parameter do not exceed the established 12%.

- Groove compatibility. For boards from the same batch, they must match exactly. If this parameter cannot be checked immediately, serious problems may arise during installation later. The depth of the groove should exceed the size of the spike, so that during the installation process there are no difficulties with joining the elements. It is worth checking the distance from the surface of the board to the groove and the ledge - it should be the same throughout the game.

- Dimensional parameters. The optimal width of the board is 130-150 mm, which allows you to optimize the time spent on installation. Options over 200 mm can change the geometry at the ends when dry after installation, forming a bend. This will cause the floor or walls to become ribbed. The thickness also matters - the smaller it is, the more frequent the step will be to place the lags.

These are the main parameters that are recommended to pay attention to when choosing grooved boards for finishing a house, bathhouse, other residential or non-residential object.
Installation features
Since the grooved board belongs to the category of flooring, most often its fastening is carried out precisely during the installation of this covering. Not relying on the good faith of manufacturers and sellers, laying is carried out in 2 stages, taking into account its possible shrinkage and deformation. The grooves and tenons selected by the milling cutter in production usually fit together quite effectively. Therefore, during the initial assembly, it is customary to fasten the floor to the logs not entirely, but after several floorboards, with a pass of 4-5 boards.
In this form, the coating is left for a year. After this period, the floor is carefully sorted out, gaps are eliminated, warped elements are replaced. Each board is already planted on self-tapping screws without gaps.If the floor is arranged in the premises of a residential building, initially it is fastened roughly with the wrong side up to avoid abrasion or contamination of the coating. This will give you a clean finish.

Mounting method
Usually grooved shaped boards are fastened not just in grooves to each other, but also fixed to the base. This is done using different types of hardware. Nails have their own advantages - resistance to damage due to warpage. They can bend, but they won't break. The self-tapping screw does not have such advantages, but it allows you to change the pressure force or even replace damaged strips. When choosing this type of fastener, you should give preference to the special yellow, rather than the usual black wood screws.


There are several ways to fix the tongue and groove on the joists.... The following options are distinguished.
- Into the bed. In this case, nails and screws end up on the front surface of the coating. The option with a face mount is not the most aesthetic, but it fully justifies itself in terms of reliability.
- With concealed installation in a groove. The self-tapping screw is screwed into its lower plane at an angle so that the head of the hardware does not prevent the spike from entering the mount in the future. The method is inferior to the previous one in reliability, since only the lower third of the board will be fixed during torsion. This will lead to cracking of the insufficiently dry material.
- Into the tongue... This method of fastening is considered hidden, it provides for fixing a nail or self-tapping screw for a spike, which takes up to 2/3 of the thickness. It is more difficult to adjust the flooring in this case, but the aesthetics of the coating does not suffer.
All countersunk mounting methods require preliminary drilling of holes in the thickness of the material. When installing at an angle, you need to choose long - up to 75 mm - screws and nails with a rod diameter of 4-4.5 mm.

General recommendations
When laying a finished floor based on a tongue-and-groove board on concrete or cement screed, use substrate made of chipboard, which makes it possible to reduce deformation loads on the material connected into the groove. It fits under the sheets waterproofing... For wall cladding, a vapor barrier is used. Previously, the material is kept indoors for 3-4 days.
If this is possible, logs are used and the floor is laid on them, even if there is a concrete base below.

There are a number of general guidelines to help make the job process easier. To perform all the necessary manipulations, in addition to fasteners, you will need a drill, a hammer, and a screwdriver.
Here is the procedure.
- Installation of a waterproofing layer.
- Setting lag. They are mounted on a level using mounting wedges made of wood, plastic. Fastened to concrete with anchor dowels.
- Installation of thermal insulation in the form of mats or sheets of mineral wool. It should fit snugly against the edges of the created floor battens. It is better to lay a vapor barrier film on top.
- The first row is laid with a gap from the wall. It is enough to retreat 5-7 mm. At this distance, a board is attached to the face with a gap of about 10 mm from the edge of the entire plank. When fixing in a spike, an area with a groove is placed against the wall.
- Each row is knocked out or pressed with screw clamps. Installation is carried out so that all elements are joined with the most snug fit, without gaps and distortions.
- The fastening continues until the entire floor is covered with the boards. If trimming is required, it is best to prepare a miter saw in advance. It will allow you to get a cut with a perfectly perpendicular geometry, without chips and other defects.
- Completion of work. The last board used in the decking is mounted with a 5-7 mm gap. Padding or wedge can be used. Fastening is done in the same way as the first floorboard.
Considering all these tips, you can cope with the installation of a tongue-and-groove board on the floor with your own hands as quickly, simply and efficiently as possible.


In the next video, you will learn how to make a tongue and groove floor.
The comment was sent successfully.