All about rip saws

The saw is considered the most efficient for the job if it is equipped with a saw blade. The quality of the cut itself, the speed of work, as well as the proportion of rejected elements and the presence of waste, largely depend on the correct choice of this circle. Depending on the features of this device, longitudinal and transverse types of sawing are distinguished.
Sawing types
The saw is a cutting sharp tool with a large number of blades that is capable of working in a closed cut. A kerf is a rather narrow gap that appears in wood when cutting shavings with sharp teeth of a working tool. Usually, the sidewalls are distinguished from the cut, as well as the bottom, it is with them that the blade enters into interaction. Depending on the angle of inclination and the location of the saw in relation to the wood, several types of sawing are distinguished.
- Longitudinal. In this case, the plane is parallel or approximately parallel to the wood fibers. Sawing frames operate according to this mechanism, as well as band and circular saws used for sawing logs, as well as beams into boards, when the material is cut in the longitudinal direction both in length and in width.
- Transverse. Here the saw is located perpendicular or approximately perpendicular to the fibers. In this case, the sawing itself is carried out manually using cross-cut saws and hacksaws, as well as on miter machines. This method of processing wood fibers is used for cutting into round billets, removing wood defects, as well as for giving lumber the required quality and dimensions.
- Mixed. In this case, the plane of the tool can be located in the range from 10 to 80 degrees in relation to the wood.



Speaking about which method of sawing is better, it should be noted that the transverse one is considered more simplified, since this scheme does not have a complex gearbox, which is required to rotate the axis by 90 degrees, the gears function much more efficiently, thanks to which the crosscut saws are more durable, the risk of the motor coming out of tuning is much lower and overall the instrument lasts longer.
At the same time, it should be understood that some types of work cannot be done in any other way than longitudinal. That is why it is worth dwelling in more detail on the main parameters of rip sawing.


Peculiarities
Rip sawing is a sawing process that runs parallel to the natural grain of the wood. In this case, circular discs are used, in which the incisors are inclined, their pointed edges effectively cut the fibers, they begin to flake off and form sawdust. In the process of such processing, irregularities often appear on the surface of a wooden part, as well as mossiness and gouges - their appearance is explained by the properties of the fibers formed during the life of the tree.
The final surface profile is influenced by the way the kerf is widened, as well as the size of the set-off and the shape of the teeth. Usually the latter are sharpened like a triangle, so you can work with such a disc only in one direction.

Saw blade design
Choosing the right blades for effective rip sawing.It is noted that the larger the teeth, the easier such a sawing is (for comparison, when working with cross cuts, large teeth act very roughly and literally tear wood, which leads to chips). The cavities between such teeth must also be as deep as possible - in this case, the removal of chips will be of better quality. The optimal number of teeth for longitudinal cutting varies from 20 to 24 pieces.
If in your work you need to carry out both types of sawing, then it is better to give preference to the tool on circles with medium-sized teeth, a total of 46–48 pieces.


Fine-toothed discs should not be used when working with rip cuts, this is fraught with a decrease in the speed of work, significant overheating of the device and such unpleasant consequences:
- the saw blade starts to glow;
- the saw often goes sideways from the cutting line;
- in areas of overheating, the material begins to "swell" and friction increases significantly;
- the saw deforms and looks more like a propeller than a cutting surface.
In order to reduce the likelihood of rapid overheating, small slots and holes are made in the saw blade, which act as thermal compensators. They are usually placed on the edge along the radii.



On some models, they are partially filled with copper compounds, which reduces noise levels and helps to quickly cool the engine. Sawing wheels are usually poured from one metal (they are called monolithic) or with the inclusion of solders from various hard alloys. Each of the options has its own pros and cons.
- Monolithic, as a rule, quickly become dull, so they have to be sharpened and corrected. However, this procedure is quite simple and uncomplicated, so it is quite possible to carry out it yourself at home. Typically, such blades are used for both rip and cross cuts. The cost of such equipment is quite affordable.
- Carbide circles are much more expensive, at the same time, the period of their use until the very first sharpening is longer. Sharpening of this tool can only be carried out on specialized equipment. Despite this, it is precisely such canvases that are more in demand among consumers, since their cost pays off much earlier than the need for resharpening arises. Carbide wheels do not only work well on wood, but also on materials such as metal, laminate or pressed board.



Special attention should be paid to several parameters of electric saws for longitudinal use.
- Radial or face runout. For carrying out particularly accurate work, one of the most important indicators is the deviation of the circle from the main cutting plane. If there is a radial or end runout, then it can disrupt the sharpness of the cut. The optimum allowable runout is 0.15 mm, and the highest quality models have a parameter within 0.05 mm.
- Keep in mind that rip cuts should not be made with miter saw blades; they have a different path of movement of the blade in the wooden part. For example, the wheels for pendulum tools are usually at a negative angle - this reduces the load on the motor, and the cutting edges are faster and easier. As a result, the efficiency increases when compared with a disc disc with teeth located at a positive angle. If such a disc is mixed along the trajectory of the pendulum, then the saw will simply cut into the fibers with not the sharpest parts of its teeth. All this leads to an increase in the load on the motor, overheating and a decrease in work efficiency. If discs with negatively sharpened teeth are used for a circular slab, the wood will begin to repel, and the sawdust will not come out well - in this case, the cut is much slower.
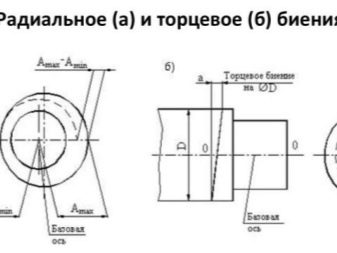

Subtleties of choice
Rip saws are best bought from specialized stores. - unlike small outlets, here the product comes with a complete instruction and description for users, and the sellers have the necessary knowledge and can give detailed advice. Be sure to study the information located on the disc itself. Usually, here, using arrows, indicate the direction of cutting (across or along), as well as the maximum cutting speed in revolutions and the angle of inclination of the teeth. Typically, a negative angle is denoted as neg and a positive angle as pos. A letter is usually indicated in front of these designations - it shows the magnitude of the degrees.
It is necessary to visually inspect the disc and make sure its quality. Keep in mind that, for example, blunt teeth can be sharpened, but if the body turns out to be weak, it is not possible to correct this defect.


Be sure to check the quality of the sanding. If the saw blade is good, then pronounced grinding circles will diverge from the center to the edges. They indicate that after stamping, such a wheel was necessarily calibrated, then polished and brought to the most efficient working condition.
If the circles are cheap, then usually they are not subjected to additional refinement, the maximum is to grind the whole sheet. Resin with chips sticks to a poorly sanded surface, which significantly interferes with work.
In more expensive models of electric saws, the inscriptions are applied with a laser, due to which the marking remains during the entire period of use, which is very important for the subsequent sharpening of the tool.



See the next video for more details.
The comment was sent successfully.