All about grinder accessories

Grinder attachments greatly expand its functionality, they can be installed on impellers of any size. With the help of simple devices, you can make a cutting unit or a machine for cutting grooves (grooves in concrete), which will ensure the quality of work at the highest level. The need to purchase an expensive professional tool disappears, since a good job can be done with homemade improvised means.


Varieties of devices
Grinder attachments exist with a wide variety of functions:
- for smooth cutting;
- for grinding;
- for cutting bars and pipes with a diameter of 50 to 125 mm;
- for peeling old layers from surfaces;
- for cleaning and grinding;
- for polishing;
- chain saw for cutting wood;
- for collecting and removing dust during operation.



These fixtures are also called accessories. They are often purchased separately from the main unit. Some of them can be made independently from available material or old technology.
Manufacturers
The most common and popular attachments are cut-off wheels. Good discs for metal are produced by Makita and Bosch. The best diamond bits are produced by Hitachi (Japan) - such discs are universal and can successfully cut any material.



Grinding attachments from the American DeWalt company are appreciated. They differ in the material from which they are made, can be: from a sponge, matter, felt.


For working with stone and metal, special peeling nozzles are used. The highest quality of them are the products of the companies DWT (Switzerland) and "Interskol" (Russia). The products of the latter company stand out for their combination of price and quality. The named companies also produce good roughing discs, which are diamond-coated.


In addition, DWT manufactures high quality angle grinder tips called cones. They are used to remove old paint, cement, primer.


Fiolent produces a variety of very good quality turbine nozzles. Prices for attachments from this manufacturer are low. "Fiolent" appeared on the market relatively recently, but has already gained a good reputation and authority.
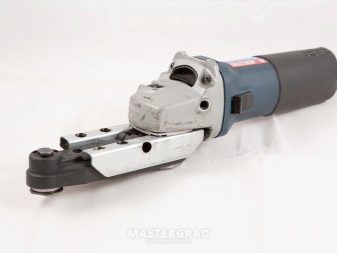
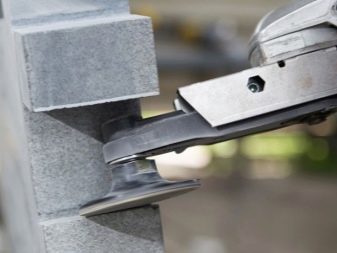
The company "Bort" from China (Bort) also makes good attachments for grinders. As you know, the products of Chinese manufacturers are traditionally distinguished by a low price.


How to do it yourself?
Before doing, for example, any machine using angle grinders (the device is quite simple), it is recommended that you familiarize yourself with the schematic drawings that can be found on the Internet or special literature. They will help you better understand the principle of the arrangement of the grinders themselves, as well as how the various attachments that may be required are made. The nodes will have to be selected empirically, focusing on the actual dimensions that are available for this particular turbine model. Such a unit can be ideal for cutting and facing various workpieces.
There are dozens of different attachments, which can be of very different sizes, so the parameters of the working elements should be selected when this particular model is in front of your eyes.


Creating a machine for sawing wood
Two pieces are cut from the corner (45x45 mm). More precise dimensions should be viewed according to the dimensions of the angle grinder gearbox. In the corners, 12 mm holes are drilled (angle grinder is screwed to them). If the factory bolts are too long, they can then be cut off. Sometimes, instead of bolted fasteners, studs are used, this does not in any way affect the quality of the connection. Often, the corners are welded, such a fastening is the most reliable.

A special support is made for the lever, the unit is attached to it, for this, two pieces of pipes should be selected so that they enter one into the other with a small gap. And to make the marking more accurate, it is recommended to wrap the fragments with adhesive mounting tape, draw lines with a marker. A cut is made along the line, a pipe element with a smaller diameter should be smaller (1.8 cm). For the inner diameter, it will be necessary to find two bearings that are inserted into a more massive pipe, then a pipe with a smaller diameter is inserted into a pipe of a larger diameter. The bearings are pressed on both sides.


The mount is placed in the bearing, it is imperative to put the lock washer in the bolted mount. After the pivot assembly is prepared, a small piece of the corner should be fixed.
The vertical mount for the swivel unit is made from a corner of 50x50 mm, while the segments must be of the same size. The corners are fixed with a clamp and cut off.
It is recommended to drill the corners right away, and then you can attach them with the drilled holes to the swivel unit using nuts.
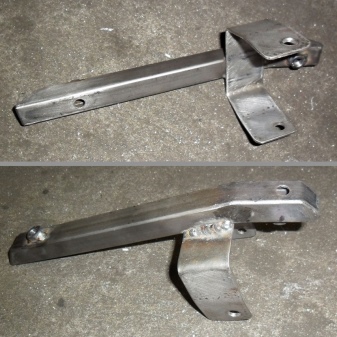

Now you need to figure out how long the lever will be needed - the angle grinder will be attached to it. A similar action is performed using the selection technology, while the parameters of the impeller should be taken into account. Often, parts are pre-laid out on a flat plane and analyzed, then the configuration and dimensions of the product become clear. The pipe is most often used square with a size of 18x18 mm.
Once all the elements have been fine-tuned, they can be fastened together by welding.

The pendulum unit is easy to place on any plane. This can be a wooden table that is sheathed with a metal sheet. A more rigid fastening is provided by welding two small fragments into which holes are drilled.
During installation, one of the main working moments is setting an angle of 90 degrees between the plane of the disc and the supporting surface ("sole"). In that case, you should use a construction square, which is attached to the abrasive wheel (it is mounted on a grinder). Welding a piece at an angle of 90 degrees is not difficult for a craftsman, it will take a little time.

An emphasis should also be made so that the workpiece is rigidly fixed during operation. A vice is often placed on a flat surface, which provides a reliable fastening. After all the operations performed, a protective coating (casing) should be made. It is recommended to take into account the size of the disk here. Before starting work, an exact template for the future part should be cut out of cardboard.
The protective screen can be made from two pieces of tin. An aluminum corner is attached to one of the blanks, it will allow you to securely fix the protective screen, using the crossbar. Such accessories are necessary for normal operation, since the grinder is a tool of increased injury.

Small holes are made on the screen, the prepared fragment is fixed with nuts and bolts. The protective cover can be painted with oil paint, and if done correctly, it will serve for a long time and reliably protect the worker.
The base-stand for the machine is sometimes made of silicate or red bricks.

Grinding machine for metal elements
There is another option that will allow you to process metal parts. To do this, take profile pipes (2 pcs.), Attach them by welding to a rectangle made of steel sheet 5 mm thick.Holes are drilled in the uprights and arm, and the dimensions can only be determined empirically.
Let's consider the stages of work.
- The lever is attached.
- A spring is attached.
- Holes are drilled for bolt fasteners.
- The rod can also be drilled (a 6mm drill will do).
- After preparatory work, the impeller can be mounted on the work plane.


The device is simple in design. It turns out a portable edging machine. In some joints, clamp fastenings can be made, the gaps can be laid with wooden dies.
For a more secure stop, an additional corner is screwed on. It is also permissible to attach a small grinder to a metal strip (5 mm thick), while it is also reasonable to use a clamp mount.
To remove dust during work, a dust collector is most often used. For the grinder, you can make an effective PVC nozzle of a container with a volume of 2-5 liters. A frame is made on the bottle with a marker, a rectangular hole is cut in the side. The dust collector is attached to the impeller, and an exhaust hose is mounted on the neck.
The gaps can be sealed with a special thermal putty, which is used to seal up wooden windows.


An exhaust device is necessary: it significantly helps in work when the grinder is used to clean various surfaces from old paint, insulation, rust, cement mortar. In this case, you can use various attachments with a metal mesh. These works are associated with the formation of a large amount of dust, so you should use personal protective equipment.
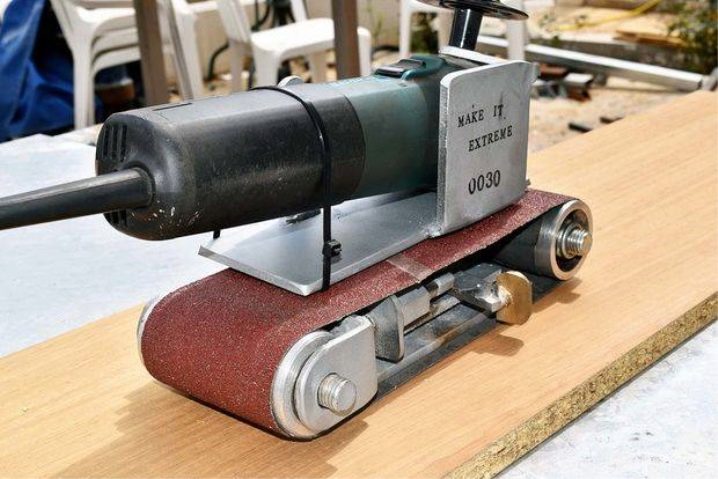
Making a pendulum saw
The pendulum saw is done as follows.
Brackets are suitable for rigid fastening, with which you can fix the grinder. To make the device, you need five identical pieces of metal reinforcement. They are welded to form a bracket-mount. A clamp-type mount is created that will fix the handle of the grinding head. A vertical support (“leg”) is attached to the front edge of the rods so that the bracket can be fixed. The bracket is mounted on a hinge, which makes it possible to rotate the assembly at any angle with respect to the working plane.



From the bike
Craftsmen often make a cutting machine out of a piece of a bicycle frame and an impeller. Old Soviet-made bicycles are ideal for these purposes. But more modern ones are also suitable, the frames of which are made of strong metal with a wall thickness of 3.0-3.5 mm, which allows it to withstand heavy loads.
On the Internet or in special literature, you can see drawings for the implementation of vertical mounts, and pedals can be used as a swivel mechanism. Taking the sample you like as a basis, you can independently bring to mind a new drawing.

A protective screen is easy to create from plywood or plexiglass. In addition to the bike frame, you will also need a mounting table, and brackets from the reinforcement can be welded as clamps.
It is optimal to use 12 mm reinforcement for these purposes.
The frame is freed from the steering wheel (you can cut off a fragment from it and use it as a handle). From the side of the fork, an element with a length of 12 centimeters is cut. The fork is shortened in accordance with the parameters of the impeller. Then it can be mounted using a metal base (a piece of metal 5-6 mm thick).

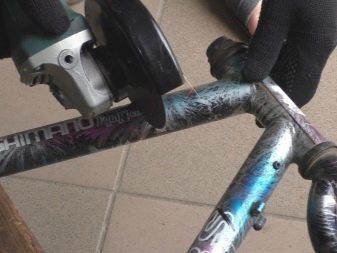
The base of the machine is made using a quadrangular piece of chipboard (3 cm thick), which is sheathed with sheet metal. A vertical post is welded to it. Two rectangular pipes are cut (the size is chosen arbitrary), they are welded at the corners of the future base at an angle of 90 degrees.
Insert a fragment of a bicycle “fork” into the vertical mount (which is already fixed on the “plate”). On the reverse side of the rack, a rudder element is fixed. A plate is also attached to the fork by welding, on which the impeller is held.
Finally, the stop strips are attached to the base (they are made from the corner). The finished block is carefully sanded, painted with an anti-corrosion compound and enamel.


Plywood
Plywood can be a reliable tool for creating equipment. From several sheets of plywood, fastened together, you can make a mounting table, its thickness should be at least 10 mm. And also plywood is ideal for creating a protective screen or casing. If the material is treated with a special primer, painted with metallic paint, then such a knot will be durable and will serve you for a long time. If the plywood is treated with a primer in several layers (3-5), then it will not be afraid of changes in temperature and humidity. This material has a number of advantages:
- low price;
- good strength factor;
- moisture resistance;
- light weight.


Several sheets of plywood sheathed with sheet metal can withstand high mechanical stress. Such a base is reliable; rather massive working units can be attached to it. In this case, the equipment will weigh a little, it will be easy to transport it.

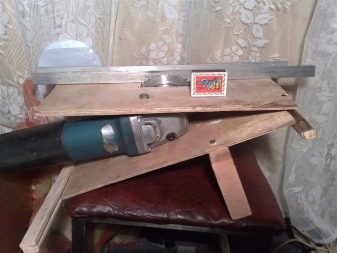
For information on how to make a stand for a grinder with your own hands, see the next video.
The comment was sent successfully.