How to make a wall-cutting attachment for a grinder with your own hands?

It is difficult for professional electrical installers to do without a proprietary wall chaser. Such units help to efficiently and quickly carry out large amounts of work. At the same time, the workmanship is at the highest level. The only drawback of such units is the high price. If, for example, it is necessary to make 20 linear meters of strips for electrical wiring in the country, then it is not necessary to buy expensive equipment for this. You can make a wall chaser with your own hands from a grinder on which a nozzle is installed. A similar tool will help in the manufacture of high-quality gutters for communications.

Design features
All chasers are created according to the same principle: there are two circles on which there is a special layer, which makes it possible to work with a wide variety of materials. The distance between the circles is adjustable. This significantly reduces the time it takes to create the groove. It is important to ensure that the same depth is maintained and that the edges of the cutout are perfectly flat. All these conditions are necessary so that the wiring can be installed without any difficulties.


The unit is based on a special metal plate - a platform. Special devices called sleds are also attached to it. The platform is used to increase stability as well as to effectively adjust the slot parameters. The slide makes it possible to easily move the wall chaser along the wall. When the tool finishes working, it is removed from the cut groove. The slide closes to cover the cutting edges of the discs. This design reliably protects the worker from mechanical injury.




A powerful air duct with a vacuum cleaner is always used for the work of the chaser. Otherwise, dust will interfere with the work process and adversely affect the health of the foreman.
The advantages of using a grinder attachment are obvious:
- with the help of such a tool, you can perform a large amount of work with high quality;
- correct cutting of the groove makes it possible to save a large amount of building material;
- the strobe is done in one pass;
- a wall chaser is much quieter than a hammer drill;
- with a properly organized matter, the concentration of dust in the room is rather low (if the exhaust device of the unit is working properly);
- when working with a wall chaser, the vibration level is zero, which is important for dilapidated buildings;
- the time it takes to cut the grooves is short, and the quality of work is ideal.



When assembling a homemade nozzle, it is located at an angle of 90 degrees in relation to the platform. This installation greatly reduces energy costs. The tool rests on the working surface, it can be smoothly advanced along the markings. A special adjustment makes it possible to precisely control the depth of the cut to be cut. It should be mentioned that the depth of the groove can only be made using a special device - the second circle. This requires correction (or even alteration) of the angle grinder. However, to carry out a set of measures that will allow you to use the grinder as a wall chaser, not technically difficult.


A groove is nothing more than a groove that has two grooves in parallel. It has its own depth and width, that is, parameters that allow you to install various communications (pipes, cables, etc.) into it.Usually the grooves are from 4 to 52 mm in size, the depth of the cut ranges from 6 to 12 mm. The bottom of the recess itself should be flat, without defects. Strobes are also made at a certain angle. In this case, the parameters increase by 12-14 percent.
It is important that the tool makes even cuts, otherwise excess material will be consumed, which will increase the cost of the project.

The gap from the axial point of the excavation to the adjacent units must be at least 125 mm, to the gas pipeline - 400 mm. It is important under all circumstances to use the hood and dust collector during the work process, even if the material is soft (eg foam concrete) and does not generate a lot of dusty formations. An equipped wall chaser solves the issue by attaching a vacuum cleaner, which must have a filter and an adapter.

It is also necessary to use the correct attachments (frames with wheels), through which it is possible to greatly facilitate labor and mechanical stress on the hands. The attachment must meet some basic criteria:
- the ability to arrange the second circle;
- the presence of a socket for the exhaust device;
- the presence of a closing cover that protects against dust and large mechanical particles;
- a recess in which the cyclone of the vacuum cleaner is fixed;
- compliance with conditions suitable for operation with such an accessory.

The length of the shaft should be such that a second disc can be installed on it (it will make the second wall of the gutter). An important point is the size of the circle. It sets the depth of the groove, ensures safe work. When the shaft rotates, the movement of the disc should be directed towards the worker, and not vice versa. Only then will the total torque push the tool away from the groove.
It should be borne in mind that for panel houses, slitting is allowed only to a certain shallow depth. Reinforced concrete slabs have such performance characteristics that do not allow cutting the material by more than 5-10 mm. Otherwise, the supporting structures will lose their strength factor. The same can be said about old houses built in the 60s. Slitting there should be done very carefully. In addition, it is forbidden to work with a hammer drill on such objects, because increased vibration can also adversely affect the strength of the supporting structures.


Appointment
The wall-cutting attachment is prepared as follows:
- protection is removed from the gearbox;
- another sleeve is placed, which can be crimped using a special clamp;
- a diamond wheel is installed on the shaft (diameter 160-235 mm);

Too large disks should not be installed, because during the slitting, the loads on the dynamic nodes increase, which leads to the formed wear of the working nodes. The diamond wheel is very comfortable and functional. It allows you to work with almost any material, it is especially convenient to use such a disc to slit concrete walls for wiring. The material has an increased strength factor. A diamond-coated and victorious disc can ideally work on:
- concrete;
- tree;
- foam concrete;
- brick.


It is imperative to put a special washer on the bushing, which will serve as reliable support. Washers are usually supplied with the tool, they make it possible to create a certain groove width - grooves. After mounting the disc, a nozzle is attached, which allows you to work with virtually no dust. The grinder gearbox is attached to the control handle. It should be remembered that any nozzle designed to create grooves and grooves (which fits on a grinder) has a seat that is intended for a removable handle. It comes in the same dimensions as the standard pen.

After completing the preparatory work, it is imperative to check the correct alignment of both discs. Then the body is attached to the support of the lever, the operating mode is set, and test runs are made. In this way, it is checked how well the nozzle works.To put the second circle, you need to make a special nozzle for the angle grinder. You can buy it, it is inexpensive. You will need to put:
- additional disk;
- reference plane;
- protective screen.

To put an additional circle, you will need to purchase a special washer that will determine the size of the groove groove. Almost everything in this node depends on the parameters of the gearbox (its length). The distance can be adjusted using the supplied nuts. When working with the turbine, it is recommended to stop the machine every 20 minutes, giving it a “rest”. In this mode, the engine will not overheat. If you cannot find the required protective screen, then you can make it yourself. The simplicity of the design allows you to mount the desired element on your own. The screen can be made from:
- plywood;
- plexiglass;
- tin;
- sheet of metal.


The protective screen slides along the working plane without any particular difficulty, so there is no need to install additional devices (wheels). To cut the gutter, it is enough to nail a wooden plank and a chipboard board.
How to do it?
Creating a chasing nozzle yourself is not a very difficult task. The cost of such a device is also small. It is ideal for simple household chores, creating gutters. The attachment is functional and easy to use. Before you start creating such a knot with your own hands, you should find suitable drawings on the World Wide Web. When creating a homemade model, you need to consider the following factors:
- the wall chaser attachment will not work with a tool whose power is less than 1.6 kW;
- the diameter of the disc should be no more than 182 mm so that the engine does not overheat.


Also, when making a unit yourself, you will need:
- external protective screen (it will ensure the movement of the discs in the groove);
- a supporting element (steel plate), which will guarantee the smooth movement of the tool;
- external screen with a bell to remove mechanical microparticles;
- a set of washers for the gutter;
- nut for securing the second circle.

The screen is easy to construct from any lightweight material. Sometimes it is made from steel sheet 3 mm thick. The design must be tested on various materials. The hood can be made from a used vacuum cleaner. Models made in the Soviet Union are powerful enough and can work properly for a long time. The socket can also be constructed from plexiglass or plywood. The assembled structure can make high-quality identical gutters, which will allow mounting electrical wiring in all rooms. However, you should pay attention to the material with which you have to work.
If the walls are concrete, then the impeller motor may not be enough. Many modern houses are cast from good concrete. It is difficult to work with him; special equipment is needed here.


How to use?
A proprietary device for cutting strobes is made according to different canons, which differs from a homemade unit consisting of a grinder and a nozzle. The factory tool has quality assemblies that fit perfectly together. Tools from such manufacturers as Makita, Bosch, Interskol are especially good. Such devices work on the principle of transmitting a power impulse from the engine to the unit shaft. This is done using a bevel gear. It is quite enough to "take" solid surfaces from materials such as concrete, brick, metal. Branded tools have good power and performance. They are equipped with high-quality engines that can withstand long-term operation.


The grinder has a slightly different arrangement of functioning units. If the forces are too high, then the gearbox is subjected to increased stress, which leads to premature wear of the bearings. If another disc is installed, then the load increases.Therefore, it is appropriate to use the impeller to work with soft material for a short period of time (no more than 15 minutes). As already mentioned, if you have to deal with concrete walls in a new house, then it is wiser to rent a wall chaser of a well-known brand. It is impossible to “take” such material with a turbine with a homemade nozzle.
If the volume of work is small, then a well-made nozzle can successfully replace the wall chaser.

You should use the grinder with a nozzle with caution, otherwise you can "burn" the engine in a very short time. The grinder must not be allowed to overheat. When this happens, it smells like burnt metal. The brushes may start to spark, which confirms their wear. Excessive heating of the wiring is also possible, then a characteristic smell will certainly be felt. To make a high-quality screen for a chasing cutter, which will be used for large volumes, some rules should be followed. First of all you will need:
- a metal sheet;
- rectangular pipe;
- threaded studs;
- welding machine;
- bolts and nuts.


A metal sheet with a thickness of 3 mm is cut. You can cut with a jigsaw or a small grinder. A plane is welded to one half. Then the second is welded. In this case, a gap should be left so that the clamp can be fastened, as well as the movement of the tool itself should be regulated. After that, you need to make a grinder holder, to which the clamp mount is welded. There must be a clamp on it. The diameter of the clamp fastening must correspond to the dimensions of the angle grinder. Also, two plates are attached to it, in which there will be holes (wheels are attached to them). Then the air duct is installed.

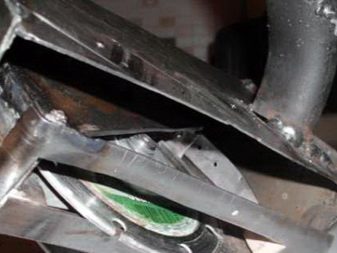
The electric engine is powered from the mains. The principle of operation is simple: the tool is tightly pressed against the plane and, without any special mechanical efforts, it is carried along the intended line (the cutting line). Two discs are involved in the work, which makes the gutter ideally even, of the same depth along its entire length.
When working flat, the disc should be immersed in the material carefully. Excessive mechanical forces applied to a working tool have a detrimental effect on the quality of work and the service life of the unit. If excessive vibration or spontaneous jerking appears, then you should stop working, because you can easily overheat the engine. If the diamond disc begins to blacken during operation, this also indicates that the material is under excessive stress. In this case, it is worth stopping cutting and letting the disc and the grinder itself "rest".

It is important to remember that at the beginning of the work, you should do a couple of test runs. This will raise the tool slightly upward.
For information on how to make a do-it-yourself wall chaser attachment for a grinder, see the next video.
The comment was sent successfully.