Cutting discs for a grinder for metal: features and varieties

LBM, or "grinder", is a type of grinder used for cutting and grinding metal, stone, concrete, wood and other materials used in construction. The physical principle of its operation is based on the friction of material against material at high speeds. The desired effect is achieved by heating the surface of the processed object at the point of contact to high temperatures, which leads to controlled mechanical damage: polishing, cleaning, cutting. Replaceable cutting / grinding elements of this power tool are special wheels. The most common of these are cutting discs.


What is it?
Cutting discs for "grinder" - hard circles of dark gray color, rough to the touch, with a mounting hole in the center, framed by a galvanized steel ring. They differ in material of manufacture, size, configuration and other characteristics determined by the type of work that must be performed using angle grinders. In construction practice, circles for metal are widely used.
The cutting effect is created by high-strength artificial materials, crushed into small chips. Electrocorundum is used - superhard, refractory, chemically resistant compounds based on aluminum oxide.

In accordance with the intended purpose of the circle, electrocorundum can be used on the following bases:
- magnesium-silicon;
- lame titanium;
- mono-corundum;
- zirconium;
- titanic;
- chromium.
Cutting discs angle grinder for metal is a consumable that is not supplied by the manufacturer along with the grinder. The tool manufacturer is not responsible for the quality and durability of consumables.
Consumable cutting materials for the "grinder" have an increased wear rate, as they are subject to high mechanical stress in the form of friction and heating. At the time of operation, an abundant production of orange sparks occurs. They are red-hot particles of the disc and the processed material. In the process of wear, the circle becomes smaller in diameter, which reduces its efficiency.


Varieties and their sizes
Cut-off wheels have a smaller profile section - thickness than grinding wheels. The work uses their end part, which, in contact with the metal, literally frays it. This type of disc has two configurations that differ in thickness: 1.5 and 2 mm. The central mounting hole is the same in all types of discs: it corresponds to the diameter of the grinder's mounting shaft. There is a single standard for this value on the Eurasian continent. All general purpose angle grinders have the same mounting shaft diameter on which the replacement wheel is fitted.
The main differences between cutting wheels are reduced to the difference in the outer diameter. This parameter allows you to use discs on grinders of different sizes and capacities.

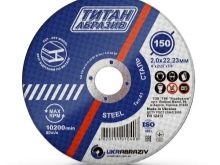
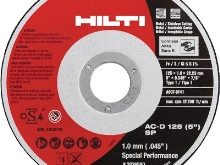
The uniform standard diameters are listed below:
- 115 mm;
- 125 mm;
- 150 mm;
- 230 mm.
There are specialized circles designed for sawing products from "problem" metals: soft, viscous, high-carbon. To distinguish them among other varieties, manufacturers use marking codes. With the help of such notation, you can determine which circle is better to use:
- for working with steel - steel;
- for cutting stainless steel - inox;
- cutting of cast iron products - castiron;
- sawing soft metals - aluminum.


Selection Tips
First of all, you should pay attention to the diameter of the circle. It must match the size of the grinder's protective casing and fit into it so that it can rotate freely. The diameter of the disc is usually indicated on the face of the disc. It is enough to compare this indicator with the permissible value given in the passport of the angle grinder. To choose a cutting wheel for metal, it is worth considering for what work it will be used, on which tool and under what circumstances.
When sawing metal with a thick profile, it is worth using a thicker cut-off wheel. This will reduce the percentage of wear and tear and reduce the risk of destruction. During operation, the cutting element heats up to high temperatures. The thicker the metal, the higher the degree of heating. When the permissible temperature threshold is exceeded, abrasive particles begin to detach from the bulk more intensively, as a result of which its accelerated destruction occurs.


Thin-section metal "scratches" the disc when sawing, accelerating its wear. Therefore, a circle with a thinner profile is better suited for such work, since it has a smaller area of contact at the point of friction. Important criteria when choosing a cutting disc for metal are its price bar and production brand. Domestic manufacturers supply the market with inexpensive materials of this category with low quality characteristics. Such circles are short-lived and unsafe to use. Overseas suppliers offer higher quality options at a higher price.
It is worth considering the ratio of price and quality with the characteristics of the work carried out. If you are planning a one-time and short-term use of a removable disk, then it is more profitable to purchase its inexpensive equivalent. When it is supposed to work for a long time on metal cutting and the requirements for the quality of the saw cut are high, then the cheap option should be excluded.


How to use?
Initial preparation
Operation of the "grinder" cut-off wheel begins with the observance of the rules of installation and removal.

Installation
Check the position of the lower lock nut on which the disc rests. Its slot must match the slot of the grinder shaft. Slide the circle onto the shaft. The side containing the marking data must be visible.
Screw on the top lock nut. Holding it with your hand, try to turn the disc in the direction of its movement. In the process of cutting metal, the difference in the directions of rotation of the disc and the nut creates a self-tightening effect. When installing, it is not necessary to tighten the upper nut with a wrench.


Picking up
Wait until the rotation stops completely. Disconnect the grinder from the mains. Insert the “horns” of the special key into the holes of the upper locknut and squeeze the lock button.
Rotate the key counterclockwise. When the nut is pulled out of place (due to the initial force), it can be unscrewed by hand. Any angle grinder is equipped with a handle connector. Do not work with the handle removed.


Security measures
Before starting work, you need to think about how the cutting will be carried out (the position of the "grinder" in space in relation to the cutting site), determine the direction vector of the flow of sparks, which will accompany the immersion of the disc into the metal. Remove all flammable objects and substances from the spark line. If necessary, cover the finished surfaces exposed to sparks with protective equipment.
Inspect the power tool itself for water, dirt, sand, and check the integrity of the power cord. Carry out a test run to check that the unit is running smoothly and that the cutting disc can rotate freely. Assess the object of the cut: it must be firmly fixed, not have deforming stress, and be away from electrical wires.
It is strictly forbidden to start working with angle grinders without observing safety measures and personal protection.


Eyes should be protected with special goggles that give a wide and clear view. Glasses with tinted lenses are not recommended. The safest face protection is a transparent plexiglass mask. If the disc breaks during cutting, its fragments are scattered in the direction of the initial centrifugal force at a high speed. This mask will protect the front of the head from getting into it. The hearing organs also need protection. For this, construction headphones or silicone earplugs are used.
The equipment of the LBM operator must meet the following safety measures:
- robes made of durable and natural material;
- Moderately loose, but overly long sleeves are unacceptable;
- gloves that fit tightly on the hands, made of strong material that can hold the primary cut;
- closed shoes with composite toe inserts.

Progress
At the moment of turning on the "grinder" it should be held with a force sufficient to overcome the starting torque. The angle grinder released from the hands at the moment of start-up can harm the operator's health and damage the finished surfaces. Keep the working "grinder" straight, avoiding sharp rotation of its body. Bring the rotating disc close to the metal piece slowly. Immerse without effort, allowing the unit's own weight to create the required coefficient of friction.
When the cut-off wheel is submerged in the material by 10–20%, you should pay attention to the smoothness of sawing. If the angle grinder twitches and tries to pull forward, it may be worth changing the angle of inclination of its body or reducing the pressure of the disc on the metal. If the metal workpiece has internal stress, cut 90% and finish the process by hand. Otherwise, the release of metal stress at the time of sawing can lead to a sharp seizure of the blade and its destruction.

In the next video, you will find tests of cutting discs for a grinder and a comparison of popular brands.
The comment was sent successfully.