Grinder discs for metal: varieties and tips for choosing

The grinder is an indispensable tool for construction work and is extremely useful on the farm. Thanks to angle grinders, you can easily cut hard materials or process any surface. But the main component of any grinder is the cutting disc.
The quality, convenience and safety of work depend on the correct selection of the disc.
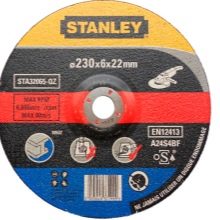


Peculiarities
Consider what a cutting wheel for a grinder is. In fact, this is the main device in the process of cutting or processing material. The engine in the grinder spins the diamond disc, which has a certain amount of cutting crystals. It is these strong crystals that cut the surface.
The milling cutter can be designed for different types of work, depending on the material with which it is necessary to work, and according to its functional purpose. There are cutting wheels for metal, wood, plastic and even stone. Over time, the circle gradually grinds down and becomes smaller.

Views
Depending on their purpose, nozzles for angle grinders can be classified into several types.
Cutting discs are perhaps the most popular model of cutting discs. They are used for cutting all sorts of materials. In turn, cutting discs can be subdivided according to the material for which they are reassigned.
- Metal cutting blades are among the most durable. They vary in size, thickness and diameter.


- Wood cutting discs differ in their appearance from metal discs. Sharp teeth are located on their edges, which cut the wooden surface. Handle such discs with extreme care. There are numerous cases where workers have been injured from these very circles.
At a high rotation speed, the tool can fly out of the hands, therefore, it is not recommended to use high turns of the grinder when working with a disc on wood.
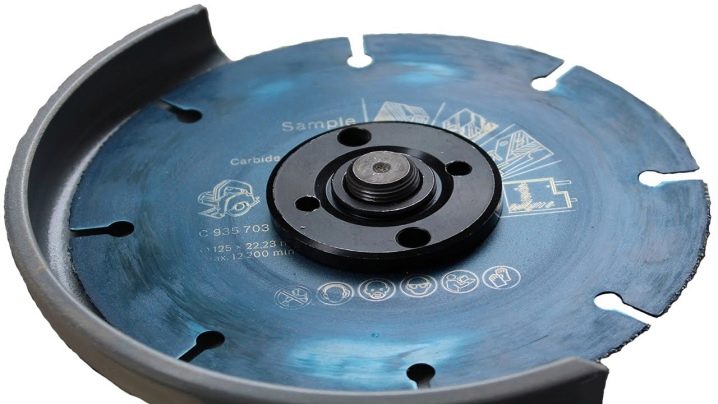
- Discs for stone outwardly do not differ in any way from circles for metal, but their composition is different. These discs use different abrasive materials.
- Diamond blades are one of the most versatile attachments for all materials. Ultra-strong crystals that grow into the composition of the circle are able to cope with metal, and with stone, and with concrete. These discs can differ in the size of the spraying (fine and coarse), as well as the cutting edge (solid and individual cutting sectors).



This completes the classification of cut-off models. Next, it is worth considering the types of grinding discs and polishing wheels. These models differ in their coverage. They may contain sandpaper, felt. And also the grinding discs can be spongy or cloth.
Usually, disks with sandpaper are used for rough and initial grinding, but felt and cloth wheels are used for final polishing.

It is also worth noting such types of grinder discs as sharpening and roughing (or stripping). There are also some varieties among them. For example, a disk with twisted cones. These circles are a round steel wire brush.
Sharpening consumables are usually small in diameter. They are used, as a rule, for cleaning welded seams or for sharpening tools. Diamond grinding wheels are distinguished by the fact that work with them is carried out exclusively by the peripheral part of the wheel.
It should be said about the materials from which the cutting wheels are made. They can be diamond, carbide, abrasive and metal wire wheels.
- Diamond discs are diamond-coated, and they themselves are usually made of steel. On carbide discs, instead of diamond spraying, high-carbon steels are used, to which nickel and chromium are added.
- Abrasive discs consist of thick latex paper, between the layers of which there is a reinforcing mesh. These discs usually have the most affordable price.
- Wire discs are intended for stripping work. Cutting hard materials with such circles is quite difficult.



Models
In the modern market of tools, there are circles for grinders from various manufacturers from different countries. German-made discs have earned great prestige. Cutting wheels from Germany are distinguished by high reliability, accuracy and cleanliness of the cut.
It is also worth noting disks of the brands Bosch, Distar and Hitachi. The products of these brands also received high ratings and good customer reviews.... In the production of such nozzles, high-quality and heavy-duty materials are used. The seams are even and smooth, and there are no defects on the circles themselves.

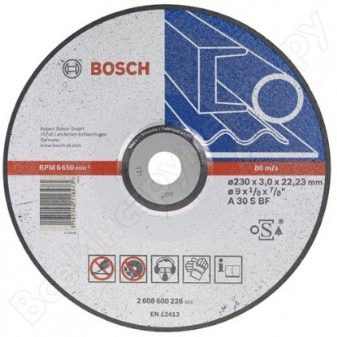
We can also highlight the products of domestic manufacturers. Among them Zubr, Sparta and Tsentroinstrument became very popular among buyers.... The price for the disks of Russian manufacturers is more attractive than for foreign ones.


How to choose?
In order to choose the right cutting wheel for a grinder, it is worth considering several important points. First you need to understand the labeling of the disks. It is difficult for an ignorant buyer to understand what certain colors, letters and numbers mean.
- Colors indicates the material for which the disc is intended. For example, the blue circle is for metal cutting, and the green circle is for stone. And also circles are usually accompanied by a signature about the material for which it is needed.
- The letters A, C, and AS refers to the material used to make the disc. The letter A stands for corundum, and the other two are silicon carbide and fused corundum, respectively.
- And also circles differ in their diameter... The minimum circle size is 115 mm and the maximum is 230 mm. Small diameter circles are usually designed for low power grinders. Diameters from 125 to 150 mm are intended for medium power grinders.
The highest sizes are for the powerful tools that professionals usually work with.


- Circle thickness can be 1 mm (thinnest) to 3 mm (maximum). A large diameter bit is thicker, and a smaller diameter wheel is thinner. Small wheels are usually used for cleaning and processing, but larger diameter wheels are used for cutting hard materials. A universal option would be a circle with a diameter of 150-180 mm. Such discs can both cut and process the surface.
How to use it correctly?
It is always worth remembering that the grinder is a traumatic tool. Particular attention should be paid to the cutting discs, since they often lead to deplorable situations. The sad statistics are that almost 90% of accidents when using a grinder are due to poor quality wheels.
When choosing a circle in a store, you should carefully inspect it for defects, that is, various chips, cracks, and so on.
If the disc is selected, then when working directly with the grinder, certain safety rules must be observed.
- Always wear a face shield before cutting or peeling material. Cutting and sanding creates sparks that can enter your eyes or burn your face. Therefore, a protective mask is indispensable when working with a grinding machine. It is also recommended to wear gloves that fit snugly around your hands.
- Do not cut material at the highest RPM.In this case, the grinder can simply become uncontrollable and fly out of the hands from strong vibration. Many modern grinders are equipped with soft start functions and a speed regulator. This makes the job much safer.

- Keep away any flammable materials and flammable liquids when working. As already mentioned above, from working with a grinder, sparks arise, from which a fire hazardous situation can arise.
- A standard stationary grinder operates on an electrical network, so it is highly discouraged to work with it in high humidity. And it is also worthwhile to carefully examine the insulation on the tool wire before starting work.
- When cutting, hold the grinder by the handles with both hands. In this case, the disc should rotate in the direction away from the worker.

- For beginners who have no experience in cutting with a grinder, there are also a few basic rules when working with a grinder.
- Before you cut the main material, it is worth practicing on some other object. For this, reinforcement or an unnecessary metal sheet may be suitable.
- While this is not always possible, it is advisable to keep the instrument in a different line with you.
- Not all grinders gain full speed immediately when turned on. It is advisable to wait a few seconds until the grinder picks up high power, and the disc is completely spinning.


Any circle is gradually grinded, and it must be changed. In order to replace the nozzle, you need to follow the following steps:
- it is necessary to replace the nozzle only on the grinder disconnected from the power supply;
- after shutdown, it is necessary to jam the rotary shaft on which the cutting wheel is installed;
- then a nut is unscrewed with a special key that holds the disc (usually the key is included with the grinder);
- then everything is simple - the old disk is removed, a new one is installed in its place and secured with the same lock nut and the same key;
- after that, you can use the tool again - sawing or processing the material.
A carved disc for a grinder is its main element, without which high-quality work on cutting or metal processing is impossible.
The main thing is to choose the right disc in the store, do not hesitate to contact a specialist for an explanation of the marking and follow the safety rules during work.
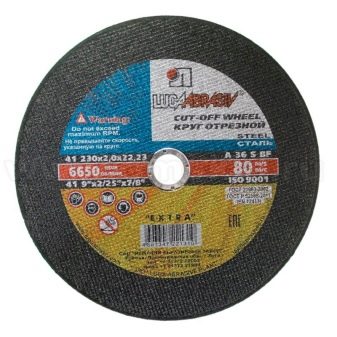

The following video is devoted to a practical comparison of discs for metal from different manufacturers.
The comment was sent successfully.