Discs for grinders for concrete: features and types

The grinder is convenient for cutting hard materials such as brick or concrete, ceramic tiles. The compact and convenient tool allows, in the most confined conditions, to precisely cut the material to size, adjust the joints of individual products and perform finishing (grinding and polishing) right on the spot. But to work with such tough materials as concrete, you will have to use special types of tools. Unsuitable discs (for example, for cutting metal) can be made of too soft material and immediately dull when working with concrete.

What it is?
To make a slit in a concrete structure, you will need a specially designed disc. Due to the high hardness of ceramics and stone, the cutting coating of discs for a concrete grinder is made of diamond chips. Such discs are several times more expensive than those made of solid abrasive. In discs for processing concrete and ceramics, the base of the disc is made of robust steel for long-term processing. The heat-resistant material of the steel base of the disc allows the tool to work for a long time even in poor cooling conditions. A multilayer coating of a mixture of diamond powder and a viscous base is applied over the outer edge of the metal disc.
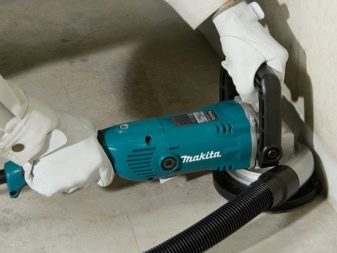
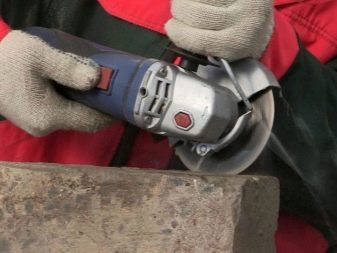
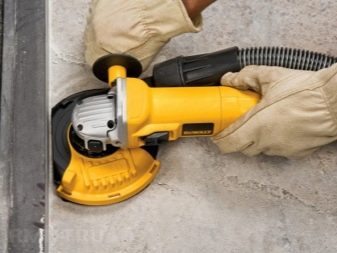

As the base wears away, new layers of diamond powder are exposed. Despite the fact that the coating with an abrasive mixture is rather thin, the high hardness of the diamond provides a good tool life. Productivity increases, which justifies the cost of an expensive tool.
Functions
Any abrasive tool serves only one function - to remove part of the processed material. In this case, the working surface of the tool deteriorates itself. For example, a grinding disc for a grinder on concrete can be completely "eaten up" in just half an hour. Concrete is generally a "difficult" material. Stones with a fairly high hardness are combined in this building structure with a viscous bonding base.


Moreover, in reinforced concrete structures, the grinder's disc can meet with the metal elements of the frame reinforcement. For cutting such building structures, special types of tools are used. Reinforced concrete cutting discs meet both the requirements for high hardness and the ability to process tough material. Hardness is required to cut natural sand and stone, which are fillers of reinforced concrete mass. Strength and the ability to handle sticky materials are required for sawing metal reinforcement.


Other parameters will be important for grinding concrete surfaces: sufficiently fine and uniform grain size of the abrasive material and a very even surface of the working area of the grinding attachment. Discs capable of cutting reinforced concrete are distinguished by a complex multi-lobe design. The division of the cutting edge into separate sectors allows intensive use of the tool without fear of changing its shape and jamming due to heat. Wide gaps between the sectors (lamellas) facilitate quick removal of cutting waste and allow water to penetrate to the working edges of the lamellas.

Water supply when cutting reinforced concrete is highly desirable. The functions of water are multifaceted:
- helps to wash out debris;
- cools the tool;
- is a lubricant in the cutting process.


For grinding concrete, abrasive discs of a special design are used.As a rule, they are not disc-shaped, but a cup or hemisphere. This allows the craftsman to handle complex surfaces. Concrete grinding discs are usually made with diamond powder. This leads to the fact that such discs are very expensive. But the high productivity of work with such a tool fully justifies the costs.

Varieties
The angle grinder (angle grinder) is the basis of a wide variety of hand-held electric tools. With the help of attachments of various devices and different shapes of angle grinders, you can carry out almost all construction operations with any materials. The sanding attachment will help to make the surface of the material even and smooth. The cut-off abrasive disc is indispensable if you need to cut a metal profile or tile exactly to size. The grinding disc for angle grinders will facilitate the removal of flux after welding and will allow the surface of the structural material to be prepared for painting.

The whole variety of abrasive tools for grinders is available in a wide range of attachments. The primitives are in the form of a simple disc. For special types of processing, abrasive nozzles in the form of cones, balls and cups are used. When choosing a nozzle for angle grinders, pay attention not only to the material of the abrasive tool. The tips for some special types of work differ not only in the hardness of the "teeth", but also in the properties of the binder.

While hard ceramics require high-strength discs and cups, concrete work requires medium to low hardness tips. This saves the instrument from overheating and prolongs its life. Surface grinding is carried out in several successive stages. Therefore, the grinding discs are available with excellent cutting grit sizes. Grinding has to be started with the coarse grained discs. Final sanding is performed with the smoothest discs with the smallest abrasives.

Selection recommendations
For reinforced concrete, you will have to use a high-performance tool. For the processing of massive building structures, heavy grinders are usually used, which allow working with discs with a diameter of 230 mm. Usually, a grinder is quite sufficient for construction work, allowing the use of equipment with a diameter of up to 125 mm. This is the most widely accepted standard for professional tools and angle grinders for widespread use.

If it is necessary to make shallow cuts (if the cutting depth is not planned more than 3-5 cm), widespread corundum discs are quite applicable for cutting metal. To work at great depths, you will have to stock up on special discs designed specifically for working on reinforced concrete. When choosing a tool attachment for an angle grinder, such a moment as the size of the grinder's spindle is also important. The most common nodes are 22 and 23 mm in diameter. The difference, at first glance, is small, but it can lead to inaccurate fastening of the tool, distortion during work and jamming.

There is a good way to attach discs and nozzles of different diameters to the grinder's spindle: use "adapter rings". Having a grinder with a 22 mm spindle, with the help of an adapter ring, you can use discs with a 23 mm landing standard. Compact angle grinders usually have not only small spindles, but also protective covers of reduced dimensions. Before purchasing an accessory for it, make sure that the outside diameter of the disc or cup will allow it to be used with your guard.

The professional tool is designed to work with grinding and cutting discs with an outer diameter of 125 mm. Compact semi-professional machines can have a limitation of the diameter of the used equipment 115 mm.Ultra-compact (especially battery-powered) grinders may have a protective cover that does not allow the use of grinding and cutting attachments larger than 95 mm. Consider this when buying.
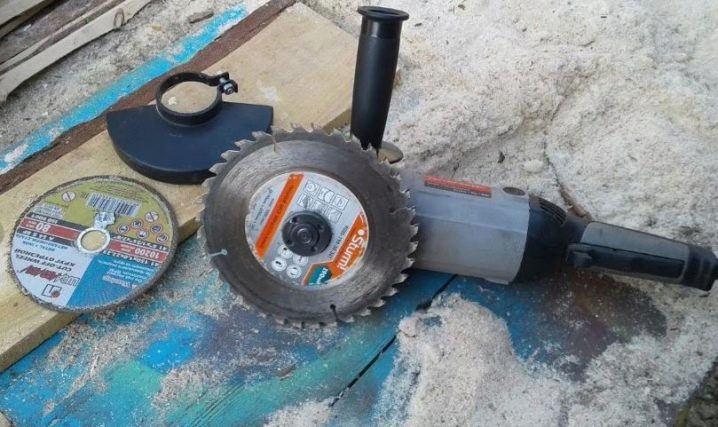
Working with an angle grinder is a hazardous activity. Special attention should be paid to the conformity of the marking of the tool and the permissible stress on it. For attachments to the grinder, an important parameter is the maximum permissible speed of the tool. For abrasive discs and nozzles, it is necessarily included in the marking of the tool and can be clarified with the seller before purchasing equipment for your angle grinder. Never buy attachments with a permissible rotational speed less than the "idle speed" parameter of your grinder!

Features of working with disks
The most used type of tool for a grinder is a simple cylindrical grinding wheel. It can be used with equal success for grinding flat and curved surfaces, fine adjustment of mating surfaces and even for rough cutting of long profiles "to size". If it is necessary to cut a bore hole in a concrete wall for a household electrical outlet, a diamond cutter for concrete in the form of a cup or crown will be indispensable. The grinding cup is the most common type of equipment for angle grinders and allows you to grind not only flat surfaces, but also complex-shaped parts.

Where is the specialization of cutting discs. They are flat and thin. Such discs wear less when making long cuts, which is why the name "cutting". It is they who are used if you need to cut a piece of metal profile or sheet material, getting pieces of exactly the specified length. But such a tool tolerates end forces much worse. If the blade is skewed in the depth of the cut, the tool will jam at best. In an unfortunate combination of circumstances, the disk can burst and fly apart into wounding fragments.

Always choose a grinder cutting attachment depending on the type of work you are going to do. If it is necessary to cut a strong structure made of reinforced concrete, it is rational to use an expensive specialized disc - a multi-blade design with a thin cutting edge made of diamond or carbide materials. But almost all types of cemented floor screeds are successfully sawn with metal cutting discs.

For work on concrete in the case of "wet cutting" it is better to use multi-blade discs with wide gaps between the lamellas. If the water supply is undesirable or impossible, it is better to cut with solid discs of a thin profile. At the same time, efforts should be made to the tool with short, confident movements of the grinder. After each cut, the tool should be switched off and removed to cool. At this time, it is necessary to brush away the accumulated dust and concrete chips from the working area with a brush.

Never neglect personal protective equipment. When working with a grinder, especially on concrete, it is imperative to use durable gloves, a face shield (or goggles) and a respirator.
For information on how to choose discs for a grinder on concrete, see the next video.
The comment was sent successfully.