How to make do-it-yourself lugs?
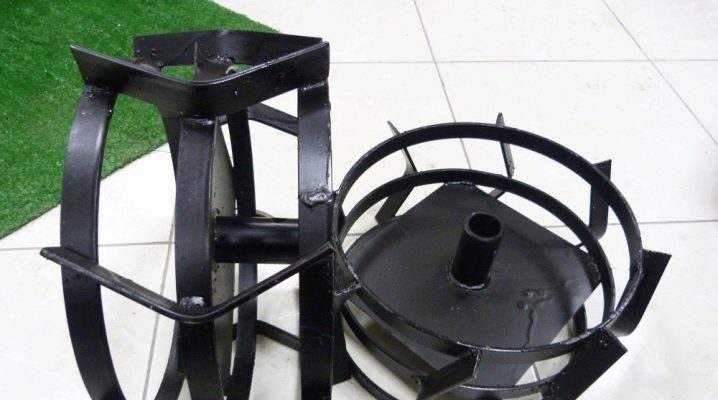
Grousers are a popular type of attachment that is widely practiced in various fields of human activity. Their relevance is justified by a simple device, a long term of work, a low price and the possibility of making it with your own hands.
Purpose
The most common options for using lugs (iron wheels) are walk-behind tractors, mini-tractors and motor-cultivators. Despite the fact that some modern mechanisms and devices have these hinges in their own basic configuration, more often they still need to be purchased separately from the unit or made with your own hands.
Iron wheels are used in situations where it is required to increase the coupling of equipment with the ground., thus increasing the traction force and the ability to overcome obstacles. So, motor vehicles equipped with iron wheels behave much more stably on loose and loamy soils. This enables the unit to perform thorough soil tillage without the danger of getting stuck or burrowing in it. The use of iron wheels for cars and mini-tractors significantly increases their cross-country ability in muddy conditions.
However, the possibilities of operating lugs with road and agricultural machinery do not end there. In a slightly different form, these devices are used to more firmly fix the greenhouses on the soil, as well as additionally to tie the wood foundation to the ground. The device of construction lugs is somewhat different than that of wheel lugs. They are rods of iron reinforcement up to a meter long with a plate welded at one end.
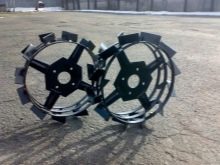
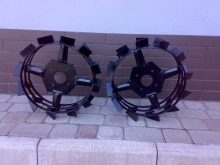
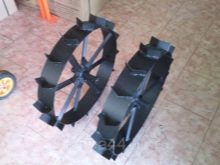
Varieties
Today the market is oversaturated both with motor vehicles themselves and with attachments for them. Iron wheels are no exception. Motorcycle lugs differ in several ways.
By use:
- multifunctional - suitable for any model of walk-behind tractors, differ in size;
- specialized - their dimensions (diameter and width) are adapted to a specific model of a motor-cultivator.
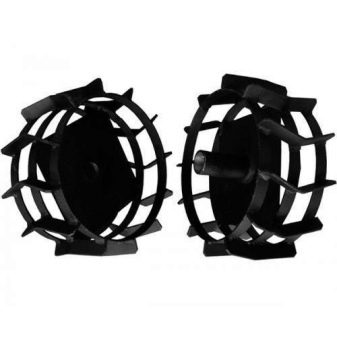
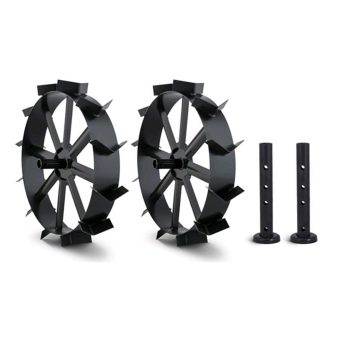
Origin:
- industrial;
- homemade.
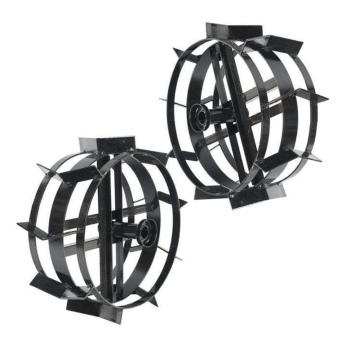
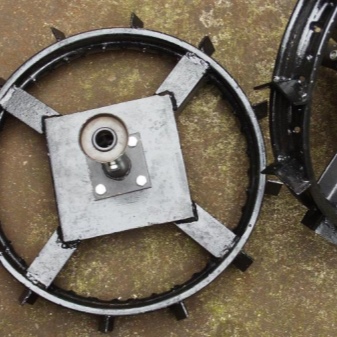
By design, there are 2 types.
- Iron wheels that require dismantling of the main wheel for installation. Such elements are fixed on the axis of the walk-behind tractor with specialized clamps. They look like real iron wheels for motor vehicles.
- Products that are put on the outside of the wheels and do not need to be attached to the axle of the unit.
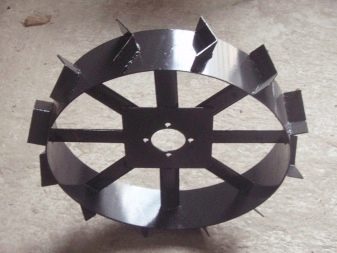
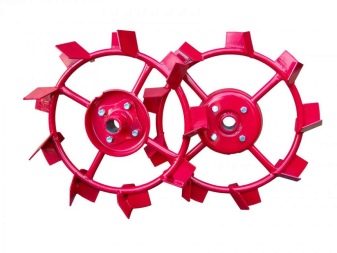
Self-production of the simplest elements
There are several techniques for making homemade iron wheels. Let's talk about different options that differ in the degree of complexity and the scale of the required activities.
The simplest method to make something similar to industrial iron wheels is to modernize the ready-made factory elements. For this, "anti-slip strips" are made, which are put on the wheels.
Let's consider the process of their creation.
- A 2-3 mm iron sheet is taken.
- Using an angle grinder, a rectangle is cut out, which should be several centimeters wider than the tire contour and coincide with its circumference.
- The edges of the strips are folded inward to prevent sideways jumping and injury to the machine operator.
- The preparation of the lug component begins (for this purpose, sheet iron with a thickness of at least 0.04 centimeters is required, which is bent at an angle of 120 ° and cut into identical pieces).
- With a welding machine, the resulting elements are welded to the strips, keeping the same distance between them.
The same operations are performed for the second wheel. To tighten the structure, you will need bolt ties, which are also welded. Violation of the dimensional relationships between the studs (plates) on different wheels can provoke the fact that when moving forward, the unit will tilt to the right or left.
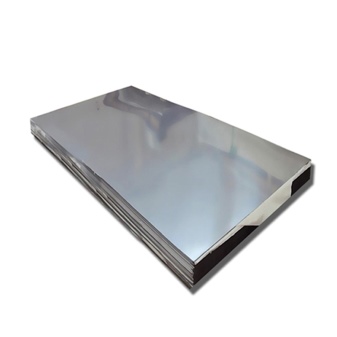
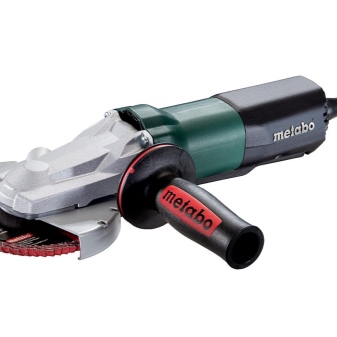
How to make from Zhiguli disks?
1 way
More complex elements can be created on the basis of a metal sheet or car disks. The exact adaptation can only be made in accordance with the drawing. Some make the drawing on their own, others use a ready-made version.
To create such products, they take:
- 4mm steel, which will serve as the discs of future iron wheels;
- metal 8mm sheet, which is necessary for the area to be submerged in the ground;
- electrical tools (welding machine, angle grinder, electric drill).
The manufacturing process is pretty simple:
- An angle grinder cuts 2 equal-sized workpieces in the shape of a circle, in the center of which holes are drilled for the studs and the hub.
- A jagged frame is made along the outer edge (no more than 100 millimeters in height).
- The second sheet of metal dissolves into triangles with rounded corners.
- The triangles are welded to the scalloped frame.

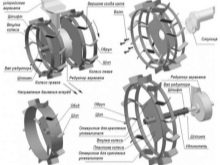
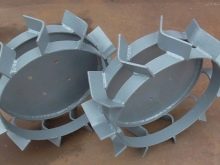
2 way
In this case, a complete set of disks is required. One pair can be fitted with tires and used for driving on asphalt, while the other can be made as classic lugs.
Let's consider the order of operations.
- We dissolve a metal corner with a shelf of 5-6 cm into pieces wider than the available discs.
- In the middle of one side, using an angle grinder, cut out a platform in the form of a triangle. It is with this part that they will begin to touch on iron wheels. Using a gas burner, we heat the corner and bend it a little. We "grab" with electric welding to strengthen the workpiece.
- Along the outer rim of the car disc, we weld the spikes from the corners at regular intervals (a step of 15 centimeters would be ideal), directing the pointed part in the direction of the motor vehicle.
- Similar actions are repeated for the other disk.
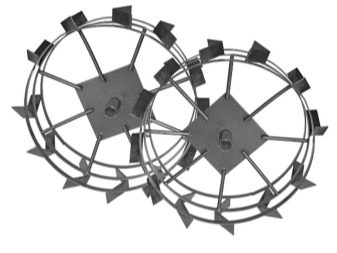
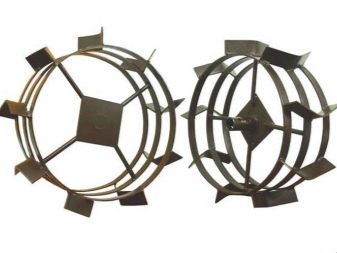
Products from a gas cylinder
Ordinary iron wheels for motor vehicles can be made in another way. An empty gas cylinder is useful for this purpose. In this case, you will need:
- make sure that there is no gas in the cylinder;
- fix the cylinder motionlessly on a stand or on the floor;
- cut from it 2 equal discs approximately 30 cm high and approximately 6-10 cm thick (they will play the role of rims);
- weld one iron plate to them;
- weld 6 teeth 15 cm in size to each of the plates (for use on lightweight units, it is required to weld teeth 5-10 cm in size to the plate).
For work, it is best to take only cylinders made of cast iron. This material is much more reliable and heavier than ordinary metal, thanks to which iron wheels can be used for a rather long period.
In general, lugs can be constructed from any material at hand, for example, from a piece of metal reinforcement and a tightening strap, or even from a mine trolley wheel.
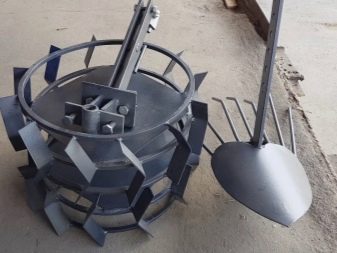
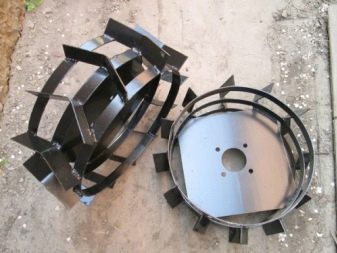
How to make lugs with your own hands, see the video below.
The comment was sent successfully.