All About Hydraulic Press For Car Service
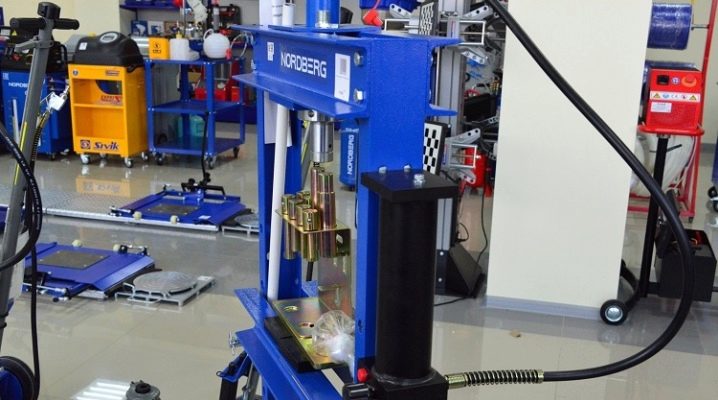
For the full-fledged operation of a car service, a manual hydraulic press must be included in its equipment. The use of such a small-sized but effective equipment makes it possible to successfully and without additional labor costs implement many technological operations associated with the assembly and dismantling of structural elements of all kinds of technical devices, in addition, with straightening and changing the configuration of products made of metal.


Device and functions
The hydraulic press is a device that is specialized for processing workpieces and parts by means of high pressure. This unit functions due to the pressure of the liquid, which affects its constituent structures. The structure of the overwhelming mass of hydraulic presses assumes a vertical arrangement of the hydraulic cylinder, however, there are also modifications in which it is placed in a horizontal position. Various modifications of presses are capable of producing working forces on a scale from tens to several thousand tons. The principle of functioning of the hydraulic press is based on Pascal's law, which we know from the school curriculum in physics.
The design of the unit includes 2 different-sized working chambers or cylinders bearing another name. The mechanism of the hydraulic press, in short, is as follows. In the smaller of its working chambers, a high pressure of liquid is formed, which is used as a carrier of energy, which enters the cylinder of a larger size through a hydraulic channel and acts on the piston, which is aggregated with the working mechanism. The latter presses on the part being processed, which is located on a rigid support, which does not allow it to move under its influence. In the role of a liquid used as a carrier of energy, specialized oils are practiced in all units.


Hydraulic presses have found especially active use in the implementation of the following measures on metal parts - bending, forging, straightening, stamping, extrusion of tube blanks and other profiles. At the same time, through such units, packaging, pressing of all kinds of materials is carried out (for the most part, a mini-press is practiced for these purposes).
The device of the hydraulic press makes it possible to intensively practice it both in the production of rubber, wood and plastic products, and in other areas. A large number of options and areas of use of this equipment determine the presence of its various modifications.
For example, on sale you can find a tabletop unit, a mini-press, a floor-standing hydraulic press, a hand press, units equipped with instrumentation and without equipment.



Design
Basic components of the construction of these units.
- The reservoir containing the liquid used as a carrier of energy, pumped into the hydraulic cylinder.
- Discharge valve and shut-off valve, which ensure the safe operation of the hydraulic press.
- Lever arm, a triggering mechanism that ensures the flow of the working fluid into the chamber of the hydraulic cylinder. The consequence of this is the piston stroke, the rod of which forms the pressure exerted on the actuator of the equipment.
The use of a lever structure for pumping a liquid used as an energy carrier distinguishes a manual floor-standing or table-top unit from stationary equipment of this direction. A structural feature of hydraulic presses for automotive service, garage or home workshop is the additional fact that the installation of the rod in a specific position relative to the element to be processed is carried out by the user. This makes it possible to practice a hydraulic press for performing technological operations in relation to parts located in inaccessible areas of the structure.
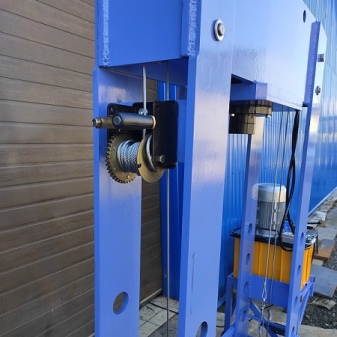

The classification of manual hydraulic presses is made according to several parameters.
- Direction of movement of the working rod. According to this indicator, modifications of manual hydraulic presses are distinguished, the rod of which is able to move upward or downward. In the main component of modern modifications, the stem performs downward movements.
- The method by which a floor-standing or table-top unit is put into operation. To operate such equipment, a hand pump is used, which in some samples can be replaced with an electrically driven pump. With such a rotation, the productivity of the presses increases.
- Possibility of equipping the stem with all kinds of attachments... The use of auxiliary nozzles is provided for by the structure of most modern modifications of manual pressing equipment, which significantly increases the functionality of these units.
- Equipment mobility. Floor modifications, like a tabletop hydraulic press, can have specialized wheels in their structure, which increases the maneuverability of these units, makes it possible to move them quickly and without additional labor costs to the location of the part or structure that needs to be processed.
- The main parameter that you need to pay attention to is power - the ultimate force applied by the rod to the material being processed. So, for any type of work with passenger cars, a press with a pressure of up to 30 tons is sufficient, while purchasing less than 15 tons is undesirable, since most 10-ton trucks are not able to cope with replacing silent blocks on modern cars. And when working with trucks or heavy jeeps, it is advisable to find a press with a maximum pressure of 100 tons and at least 50 tons.
By the way, the manual device creates a force of up to 20 tons.

How to do it yourself?
Before you start making a pressing unit with your own hands, you should decide on the necessary tools and materials.
For the manufacture of a press structure, such materials will be required.
- Channel... Experts recommend purchasing items about 14 centimeters high and 6 centimeters wide.
- Pipes... For the manufacture of the unit, pipes with a size of at least 4x4 centimeters are practiced. Products of round and rectangular cross-section are suitable.
- Steel corners... The elements are practiced in making the skeleton of the base frame. They will also be needed when assembling the transport table. In length and width, each metal corner should be 5 centimeters.
- Metal sheets... They are mounted to level out possible irregularities on the surface. For the manufacture of a hydraulic press, metal sheets with a thickness of 7-8 mm are used.
- Metal plates... Used for additional reinforcement of the structure. In this case, dense plates of approximately one centimeter thickness are installed.
- A piece of pipe measuring 10-15 centimeters, put to connect the jack rod.


The following tools are required:
- threaded plug;
- grinder for cutting metal products;
- level;
- roulette;
- electric drill;
- hacksaw for metal;
- welding unit and electrodes for joining steel elements.
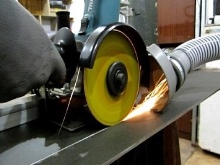

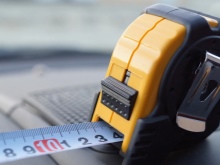
Before proceeding with the assembly of the unit, it is necessary to draw its diagram in advance. And also it is necessary to resolve the issue with the dimensions of the hydraulic press. The press is supposed to start with the assembly of the frame. It must be strong, able to withstand the work of the jack.
It is made by adhering to the accepted molds, achieving a kind of platform. The width of the frame is determined by the components for which the unit is manufactured, and the height is determined by the size of the jack.



After creating the frame, a jack is fixed to its base. With the correct positioning of the jack, its upper part will be responsible for the emphasis of the pressed elements. In this part, a steel movable frame is mounted on which the working table is mounted. On the sides, the frame is equipped with a specialized device for returning the jack to its original position.
In accordance with the drawings of the hydraulic press, the return mechanism can include either one or 2 springs.

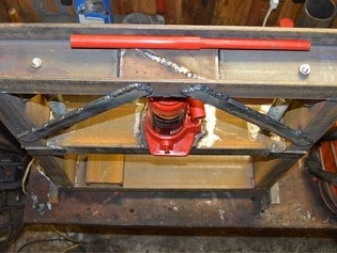
Operating rules
In order for a homemade device to last a long time, you should know how to use and maintain it correctly. When working, it is necessary to monitor the amount of oil in the hydraulic chamber. And you should also do:
- lubrication of moving parts;
- revision of the condition of the seals;
- reliability of fixing structural elements.
A homemade garage hydraulic press can be adapted for a wide variety of events. Collecting it at home is easy. The main thing is to first study the principle of operation of such units and the design features of some models.



The comment was sent successfully.