Heat-resistant sealant: features and scope
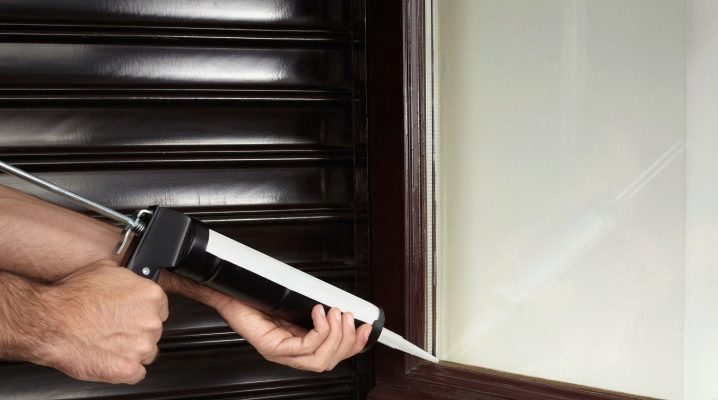
Under the word "sealant" it is customary to mean a polymer composition having a viscous consistency, which is applied to various seams and joints in order to seal the structure. When carrying out construction or repair work, there is often a need for sealed joints that must withstand the load when working in a high-temperature environment. One way to cope with this problem is to use heat-resistant sealants.
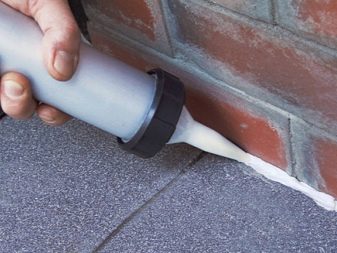
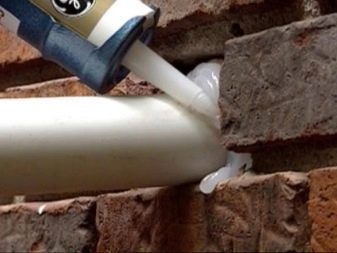
Peculiarities
The main active ingredient in the sealant is a polymer material. Depending on the purpose of application, this can be silicone, silicate, rubber, bitumen. The sealant is produced in tubes intended for manual use or using a special feeding device - a mounting gun.
Depending on its composition, heat-resistant sealant is produced in three types - one-, two- or three-component.
- One component sealant Is a product that can be used ready-made, and the composition polymerization process takes place at room temperature for several hours. At the same time, it is not required to apply a sealant with a thick layer - a layer with a thickness of 2 to 10 millimeters will quite cope with the task assigned to it. Each manufacturer indicates more specific parameters on the packaging of their products and they may differ for different brands.
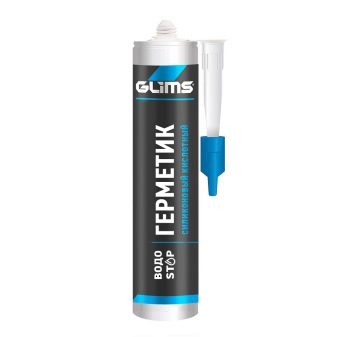
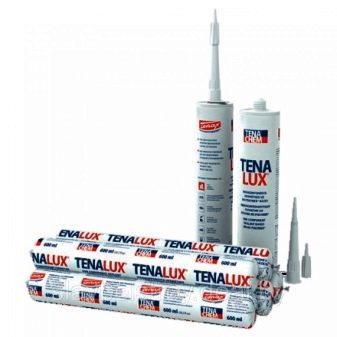
- Two-component sealant consists of a base and a catalyst. The polymerization process takes place when these two components interact. The resulting mixture must be used immediately, since it cannot be stored.
- Three-component sealant consists of a main component, a curing compound and a catalyst that accelerates the vulcanization process.
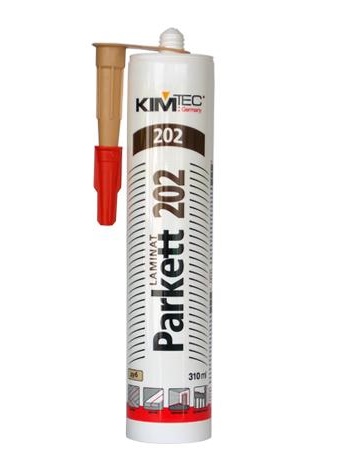
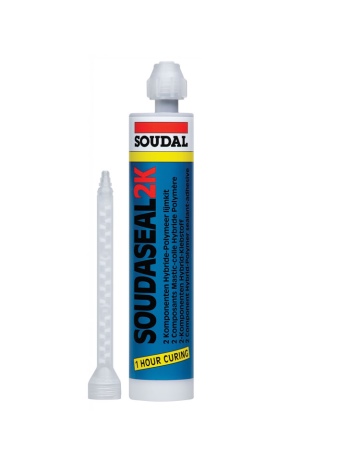
High temperature sealants fall into two categories.
- Heat resistant sealants withstand temperature load within 1300 degrees. The components of such a sealant are capable of contacting with an open flame. The product contains sodium silicate. In turn, heat-resistant sealants are either fire-resistant or fire-resistant. The difference between them lies in temperature conditions and a number of characteristics.
- Heat resistant sealants can be used in those areas of the structure that do not exceed a temperature of more than 350 degrees in heating. As a rule, these are elements of joints, joints and slots on the outer surfaces of the structure.
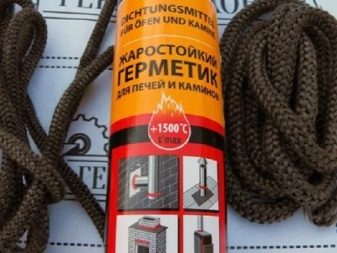
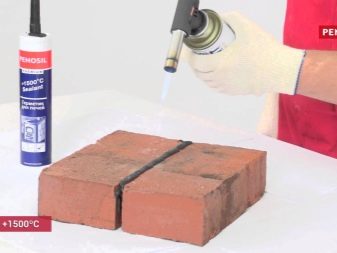
According to the composition of the polymeric substance, sealing products are of several types.
- Acidic - sealants which form acetaldehyde during polymerization. This substance can destroy or deform the surface that will react with it. Therefore, acidic sealants can only be used to a limited extent. So, for example, metal surfaces will quickly corrode, while concrete or cement will give powdery oxidation.
- Neutral - type of sealants, which consist of heat-resistant silicone and release water and ethanol during polymerization. Their use is safe for all types of surfaces, and therefore these sealants have a fairly wide range of uses. The silicone seam is perfectly restored after any deforming effects, and its service life is at least 15 years.
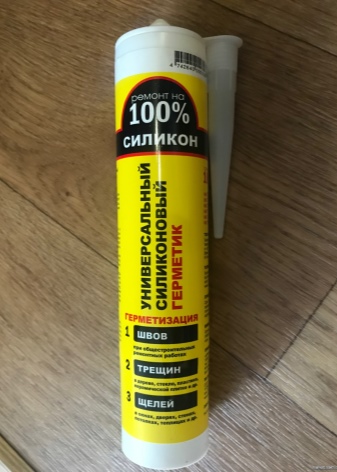
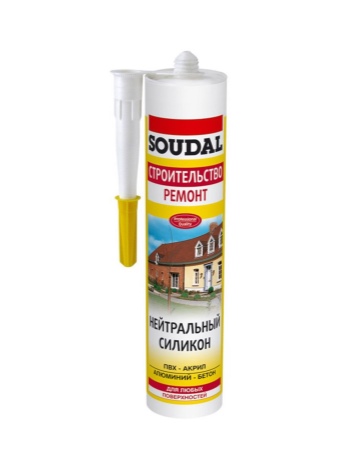
In addition to their distinctive features, all types of heat-resistant sealants share common properties.
- Adhesiveness - the polymer components that make up all heat-resistant sealing products have good adhesion to working surfaces. They can be used on brick, concrete, metal, glass, ceramic, wood or plastic construction.
- Plasticity - the sealing joints after the end of the polymerization time have a certain plasticity. They do not crack, are resistant to vibration and temperature extremes.
- Water resistance - polymer materials are highly resistant to water and steam.
- UV Resistant - Polymer sealants are not susceptible to the damaging properties of UV rays.
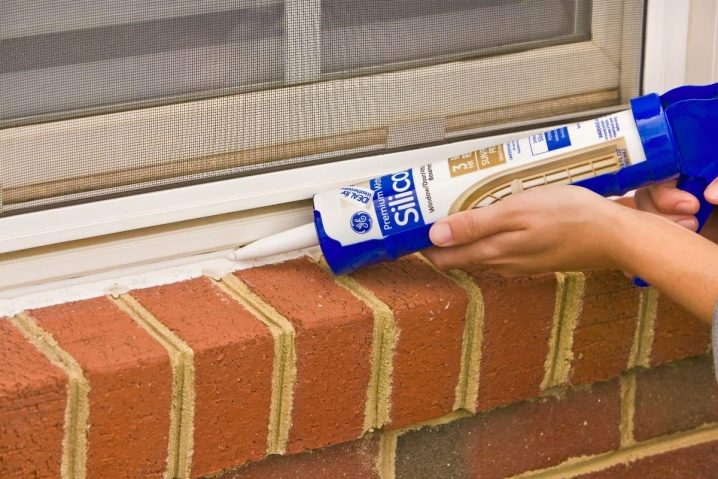
According to the scope of application, heat-resistant sealants can be divided into three types.
- for use in construction and installation works;
- used for the repair of motor vehicles;
- narrow-profile special-purpose sealants.
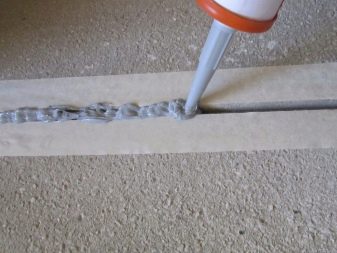
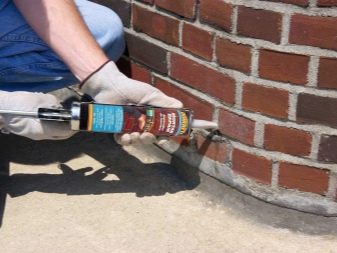
The choice of a heat-resistant sealant for sealing work directly depends on the conditions of its use and temperature conditions. To date, the composition and structure of sealants is quite diverse and meets the requirement of the stated technological characteristics.
Advantages and disadvantages
The most common area of application of heat-resistant sealants is high-temperature joints of furnaces, fireplaces, boilers, chimneys, and they are also used to repair various systems inside automotive and other equipment.
As with any product, heat-resistant sealing materials have their own advantages and disadvantages.
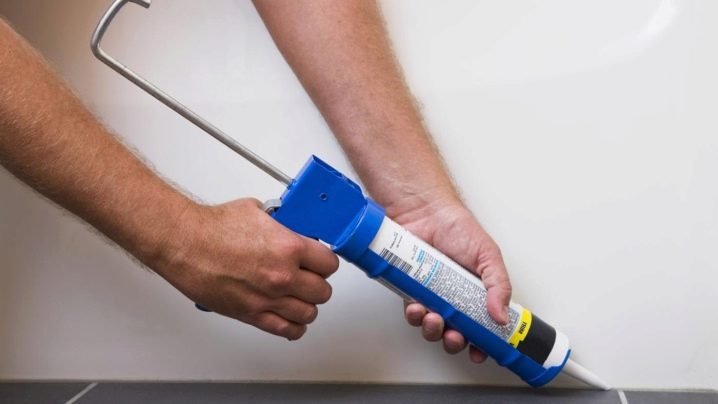
Positive properties.
- The operating mode of using heat-resistant sealant is in the range from 1200 to 1300 degrees, but its composition is capable of withstanding an increase in the working environment up to 1500 degrees for a short period of time.
- The use of heat-resistant sealants is universal - they are suitable for almost any surface, you just need to choose the right type of sealant.
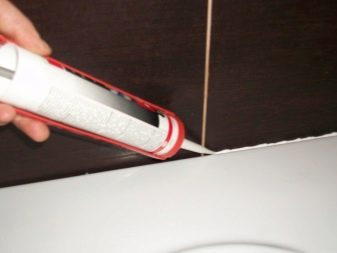
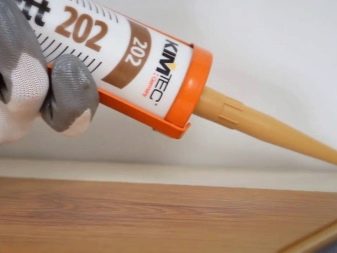
- Manufacturers of silicone sealants currently produce products with a variety of colors, which greatly simplifies the task of the buyer when choosing.
- Heat-resistant sealants containing sodium silicate are currently successfully replacing asbestos products from the market, which are recognized as carcinogens all over the world.
- The use of sealant makes it possible to increase the degree of protection against ignition of structures and structures. Often, sealants are used when installing ventilation ducts, arranging a warm floor, and installing door leaves.
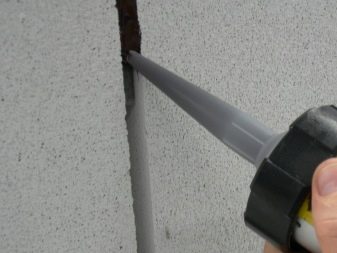
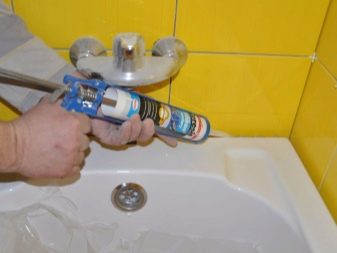
Negative properties.
- The overwhelming majority of high-temperature sealants contain iron oxide, therefore, upon contact with working surfaces during the polymerization process, they are able to paint them in a rusty brown color, which in certain conditions is undesirable and does not look quite aesthetically pleasing.
- The silicone, which is part of the sealant, does not allow paint to be applied to the sealing layer - it does not stick to it. This is not always convenient, for example, when repairing a car.
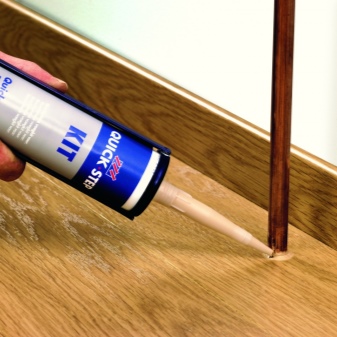
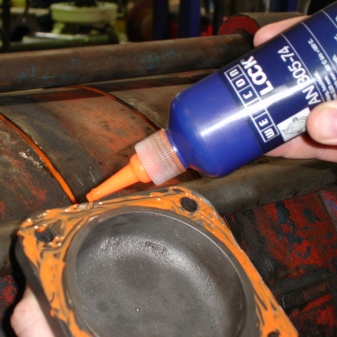
- The silicone-based sealant dries at a rate of approximately 2-3 millimeters per day. Thick seams may not solidify inside at all, since air access is important for the polymerization process.
- It is possible to work with heat-resistant sealants only at temperatures above zero, low temperatures during installation work will lead to disastrous consequences due to a violation of the polymer process technology.
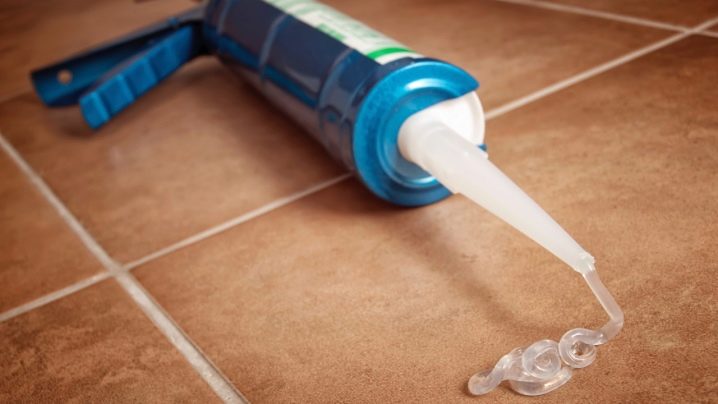
The use of heat-resistant sealants requires strict adherence to the instructions specified by the manufacturer, as well as adherence to all the nuances that you need to know and understand about this material in order to avoid annoying mistakes.
Views
In order to understand the world of heat-resistant sealants, the easiest way is to start from their main composition-forming component.
Silicone based sealants - a temperature-resistant product based on silicone rubber, which has the ability to polymerize in conditions from 2 to 40 degrees Celsius. Silicone sealants can be one- or two-component, and their chemical method of polymerization is acidic and neutral. They are used for construction, installation and highly specialized works. The operating temperature is on average 230-250 degrees, but the sealant can withstand a maximum load of 350 degrees for a short time.
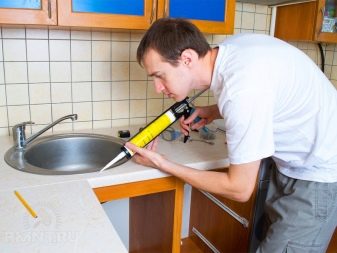
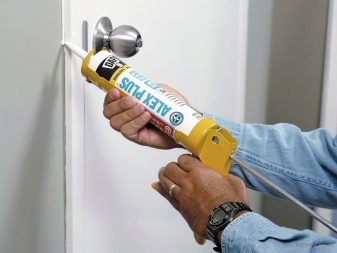
Used for:
- filling gaps in the chimney from the street side;
- tight fit of the roof to the chimney;
- chimney installation work;
- filling gaps in brickwork from the outside of the oven.
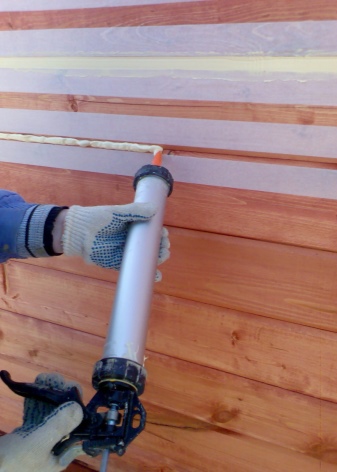
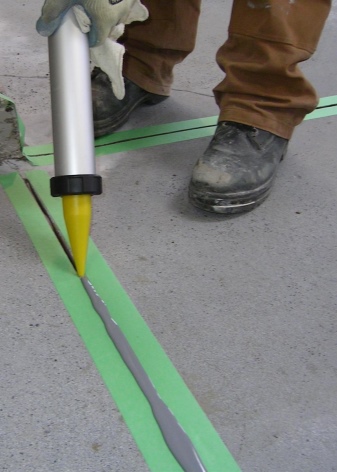
Pros:
- long service life, up to 15-20 years;
- the average operating temperature range is from minus 50 to plus 350 degrees;
- good adhesive properties, subject to the installation technology;
- easily applied to any curvature of the working surface without loss of elasticity.
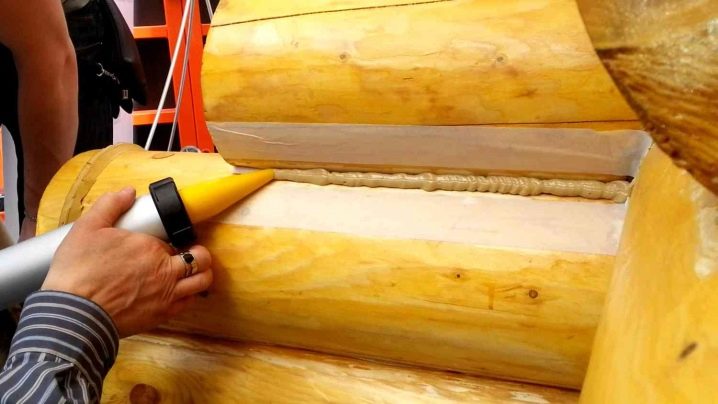
Minuses:
- poor adhesion to wet surfaces;
- does not retain paint and varnish coatings;
- when laying on an old layer of silicone sealant - poor adhesion of the new layer;
- corrodes metal and concrete.
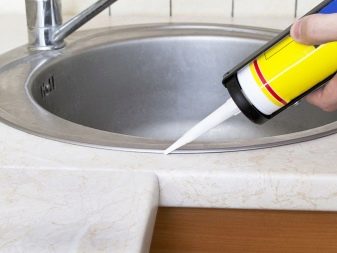

Before applying the sealant, the surface requires some preparation. - cleansing from oils, fats, dust, dirt, moisture.
In a thiokol-based sealant, the main component is the chemical thiokol or, as it is also called, polysulfide rubber. Available in two- or three-component formulations. The polymerization time can take up to several days. The composition prepared after mixing the components is suitable for operation for 2 hours. The operating temperature range is from minus 60 to plus 130 degrees.

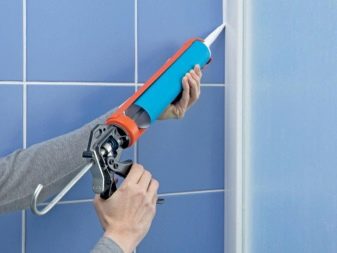
Are used:
- for sealing metal structures, for the repair of automotive systems, assemblies;
- for sealing fuel systems, taking into account oil-resistant and petrol-resistant qualities;
- due to its low gas permeability, the product is suitable for sealing gas boilers;
- for sealing structures operating under conditions of exposure to acids and alkalis;
- for sealing steam and water boilers.
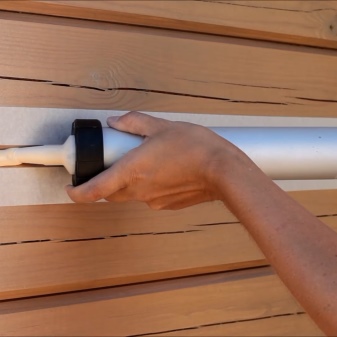
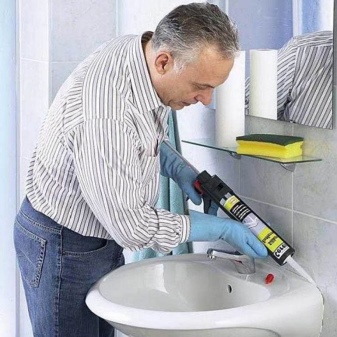
Pros:
- elasticity, strength of sealing seams;
- service life is up to 20 years;
- has excellent adhesion to metals, and is also suitable for stainless steel products.
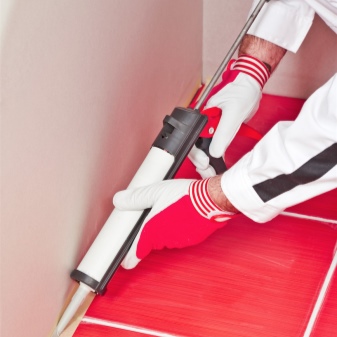
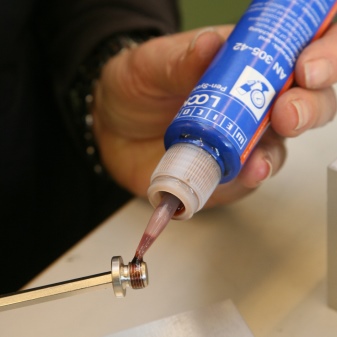
Minuses:
- after preparation, the composition must be used quickly, since it begins to polymerize after two hours;
- when exposed to the skin, the product has an irritating property, therefore, it is prohibited to work with it without the use of protective equipment.
Surfaces must be cleaned and degreased before use.
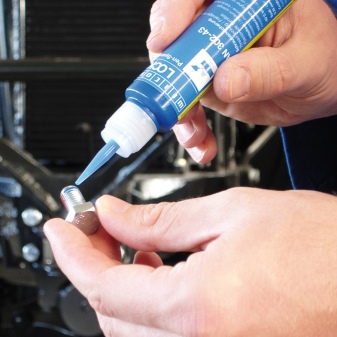
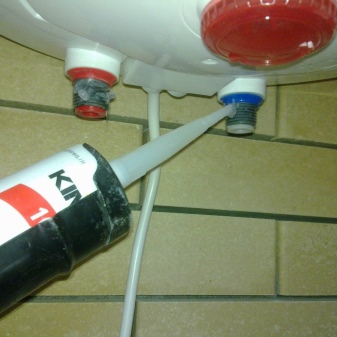
Bitumen based sealants the main component is bitumen, which, in combination with certain additives, forms a plastic polymerizable mass. The material has steam and moisture insulating qualities, is capable of operating at temperatures ranging from minus 50 to plus 150 degrees.
Are used:
- for fixing insulating materials to various types of surfaces;
- for sealing heating boilers and threaded connections in a humid environment;
- for sealing hot and cold water supply lines.
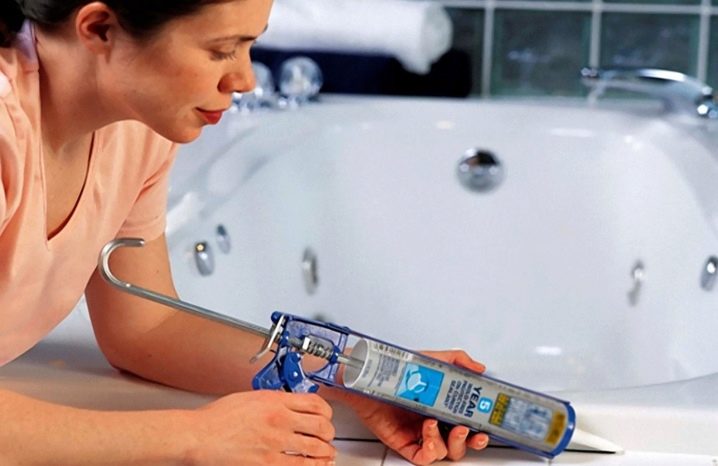
Pros:
- has good adhesive properties;
- plastic and durable, service life is up to 20 years;
- resistant to vibrations, but only in an environment where temperatures are above zero.
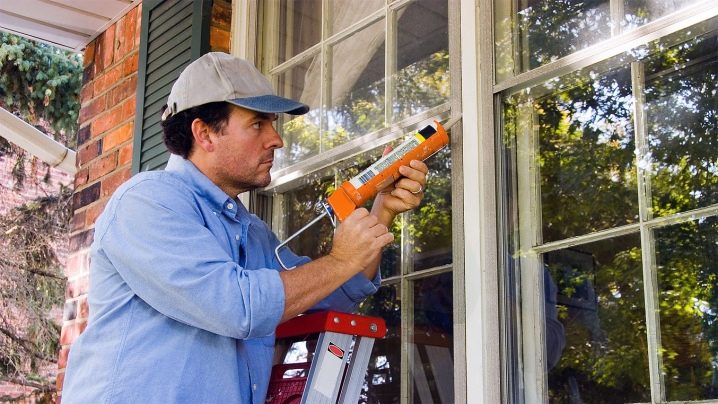
Minuses:
- does not adhere well to surfaces contaminated with oil;
- loses vibration resistance at negative temperatures;
- cannot be used at the joints of the abutment of the roof and the chimney, as the bitumen begins to melt;
- when on hand, it is very difficult to remove, therefore, requires the use of personal protective equipment;
- when a thick layer is applied, the polymerization process is very poor.
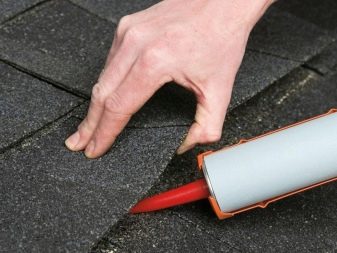
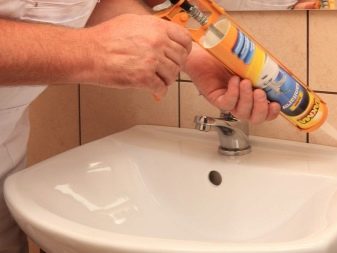
Work surfaces must be cleaned before use. When using sealant on porous surfaces, they must be primed first.
Sodium silicate sealants - The main component of this fire-resistant material is sodium silicate. The composition can be one- and two-component. Thanks to silicates, sealants are able to withstand operating temperatures from 1200 to 1500 degrees. They are usually used in ovens, but these refractory materials can be used wherever increased fire retardant performance is required. The process of application and polymerization should be carried out at positive temperatures up to 40 degrees.
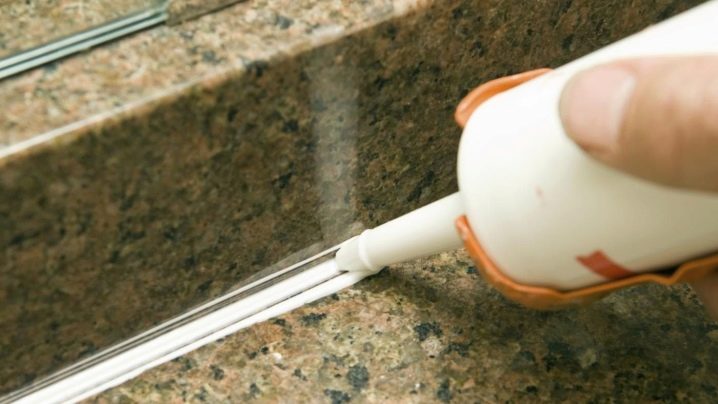
Are used:
- for sealing the connecting parts of chimneys;
- at the joints of the elements of the outer and inner contour of the furnace;
- for repairing the exhaust unit of the car;
- for sealing the joint of the cylinders of the fuel supply system of the engine;
- for sealing joints of powerful electric heating structures;
- to enhance the fire-fighting properties of certain structures.
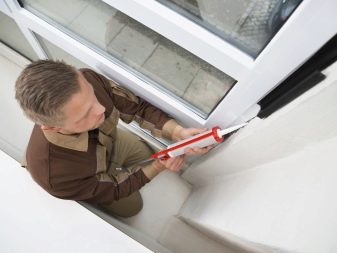
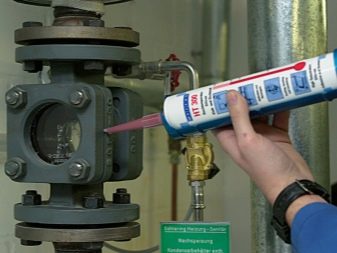
Pros:
- excellent refractory properties;
- the possibility of good adhesion to any building materials;
- well withstands exposure to open flames.
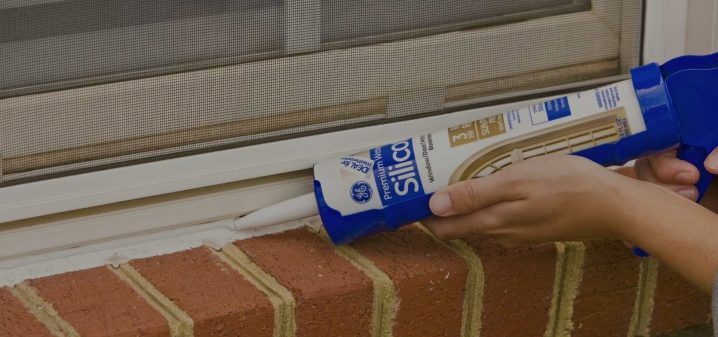
Minuses:
- the sealing seam is not elastic;
- unable to withstand vibration and deformation of the sealed surface;
- a narrow range of optimal temperatures for application - the best conditions are an ambient temperature of 20 degrees.
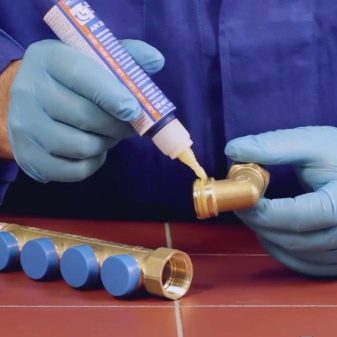
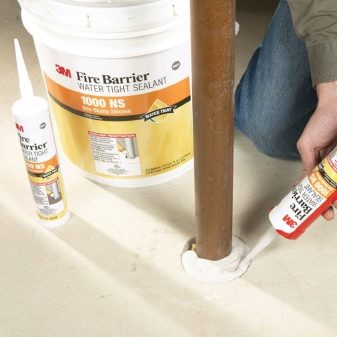
The surface to be treated must be clean and dry before applying the silicate sealant. Once dry, some brands of this sealant require a seam to be treated with a gas burner.
Colors
The color of the heat-resistant sealant can be important when it performs its function when sealing the seams of structures that carry an aesthetic load - a stove, fireplace, chimney. In other cases, this is not so important. The bulk of sealants, due to the content of iron oxides in them, has a brownish-red color. Sealing materials containing sodium silicate are usually gray or black in color. But they can be colored at your own discretion after the polymerization process is completed. Silicone sealants allow a wider range of colors and can be transparent, white or colored.
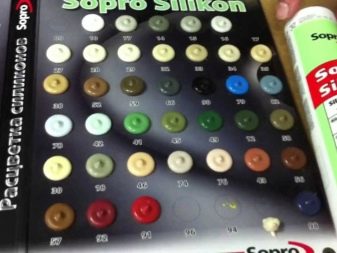
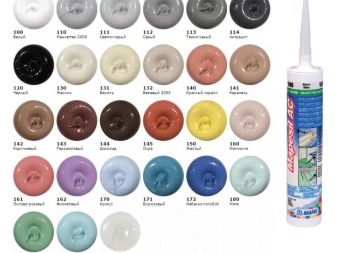
Scope of application
The range of application of heat-resistant sealants is quite wide. They are used by specialists to perform narrow-profile work and ordinary ordinary consumers for household needs. Sealants are often used in industrial areas.
Sealing materials are most in demandwith fire-resistant properties in the furnace sector. They are used to seal various elements of stoves, fireplaces, stove chimneys both indoors and on the roof, at the joints with roofing materials. Often, threaded and connecting elements of heating boilers installed in the steam room of a bath or sauna and made of metal or stainless steel are treated with sealants.
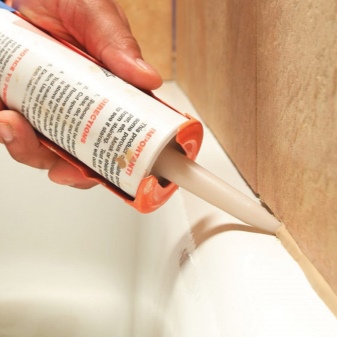
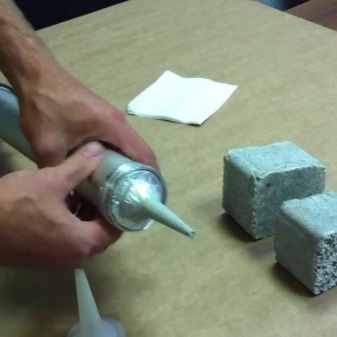
Sealing in the industrial sector covers a wide variety of applications, from industrial pipe connections to high-power electrical installations. Often, sealants are needed when installing various fire-resistant panels, surface-mounted printed circuit boards, hobs, and they are also used to seal joints, assemblies and other important technological systems.
Motorists have found use of heat-resistant sealing materials for the repair of an internal combustion engine, exhaust manifold, radiator repair, car stove and other components that are heated during vehicle operation.
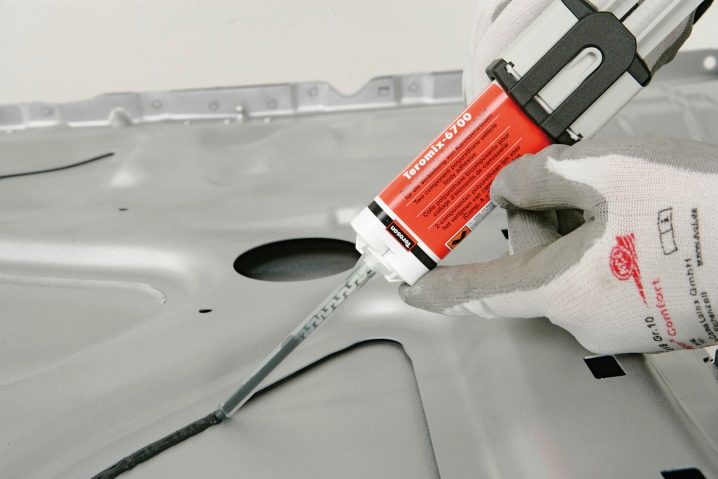
Consumption
Before proceeding with the work on sealing a particular surface, it is necessary to calculate how much sealant may be required for this. Experts believe that the minimum joint width should be at least 3 millimeters, and in the ideal case, the sealing joint should be within 6 millimeters. The seam depth should always be half its width. Ideally, the seam depth should be less than 3 millimeters. In addition to these parameters, you need to determine the length of the seam. It will depend on the size of the specific object where the sealing material will be laid. Knowing these parameters, we will be able to determine the amount of consumable sealant in running meters.
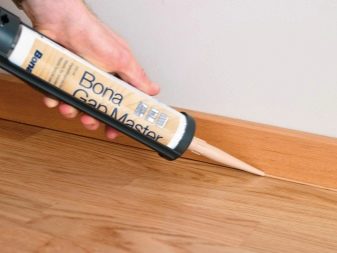
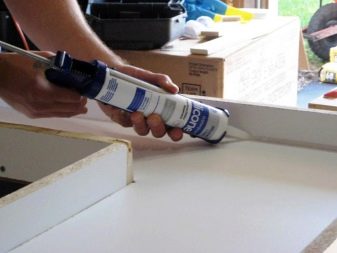
Manufacturers, in order to simplify this task for us, indicate on their products its volume and the number of running meters that this volume can cover. Many manufacturers on online sites for consumers place special calculators, with which you can determine the required number of units of their products for the given parameters of the coverage area. In addition, manufacturers have a special table, where, depending on the width and depth of the seam, it is indicated for what footage one package of one or another sealant is enough. For example, a cartridge with a volume of 310 milliliters can process 13 linear meters of the surface if the seam width is 6 millimeters and the depth is 4 millimeters. And if we take the seam width equal to 12 millimeters, then with the same seam depth equal to 4 millimeters, the cartridge will be enough for us only for 6 running meters.
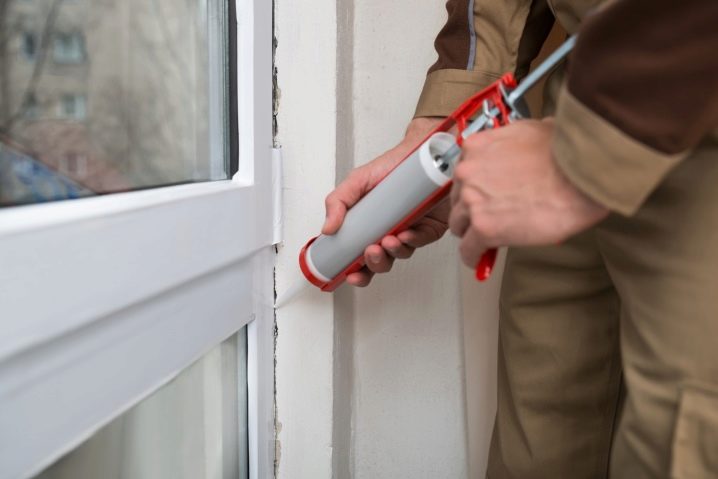
How to use?
Prepare the work surface before using the sealant. Most sealants adhere well to dry and free from dirt, grease and oil surfaces. If the material is porous, it must either be cleaned or sanded to a solid state, or well primed. It is recommended to first coat the surface of wood with varnish or paint, and after they dry, use a sealant. Metal, glass, ceramics are first degreased with alcohol-containing liquids or acetone. Polymers are best handled with alcohol only.
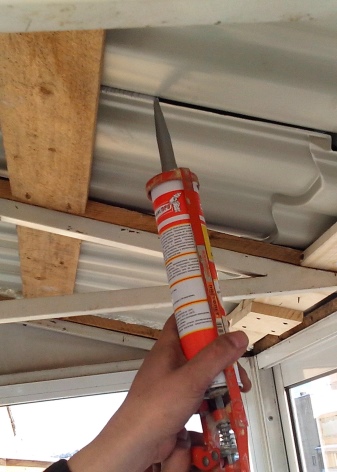
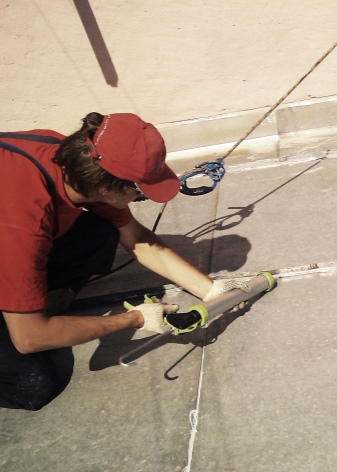
A sealing material is applied to the prepared surface. To do this, use a cartridge with a special nozzle or a special device in the form of a mounting gun. The sealant is applied to the joint so that the joint is completely closed with a sealing compound. There are special devices that help to align the seam, making it uniform and aesthetically pleasing. Sometimes the sealing compound is applied with a rubber spatula, the width of which is chosen depending on the object being processed.
After application, the sealant must be given a certain time to cure. Therefore, the treated object must not be used until the end of the polymerization period.
Manufacturers
Heat-resistant sealants in Russia can be purchased from both domestic and foreign production. According to analysts, Russian manufacturers have tended to oust foreign suppliers in recent years.
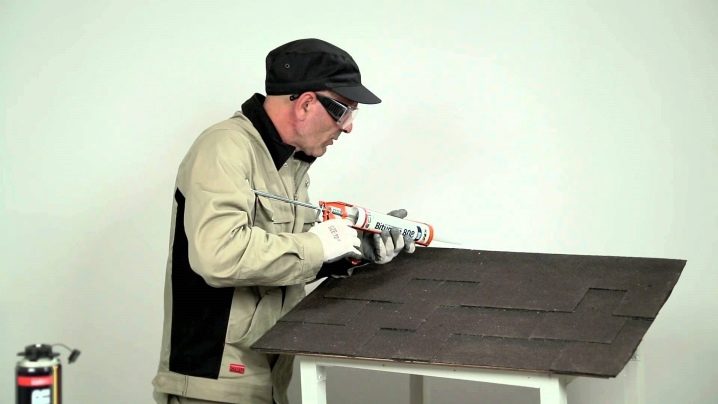
The largest manufacturers of sealants in our country, producing products according to their own developments or foreign technologies, include the following companies:
- Lipetsk company Fenzi - the company produces sealants and adhesives using Italian technology. As an example, one-component sealant "Butilver" can be cited, which operates at temperatures ranging from +120 to + 150 degrees.
- Bashkir company "Moment" produces sealants according to the technology of the German brand Henkel. The products are packaged conveniently for professional and household use. The product called "Moment Herment" is produced on the basis of silicates, the operating parameters for heating reach +315 degrees.
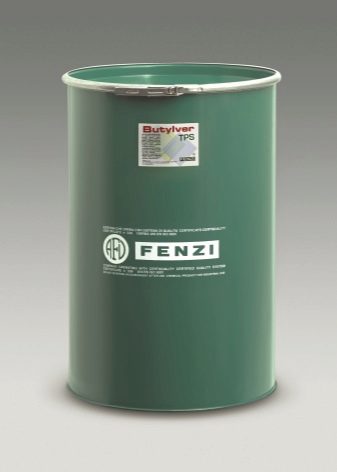
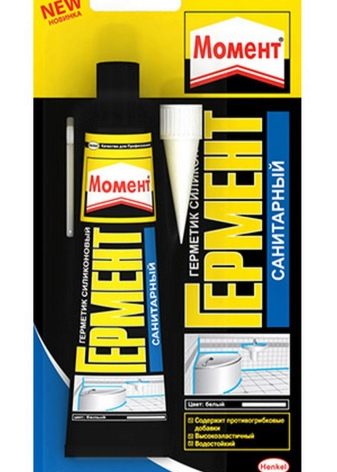
- Vladimir research and production company "Adhesive" develops and manufactures adhesives, sealants, elastomeric coatings. An example of this is the one-component sealant "Advaflex", which works in the temperature range up to + 90 degrees.
- Nizhny Novgorod company "Germast" - the manufacturer develops and produces sealants for various purposes. The Vikar sealant is designed for a wide range of applications, it is produced in the form of a 310 ml cartridge and can withstand temperatures up to +140 degrees.
- Moscow company "Sazi" - the largest enterprise that specializes in the production of sealing products. The range includes all types of sealants, from household and ending with highly specialized.
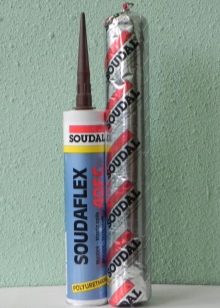
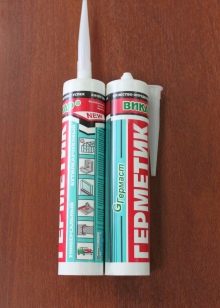
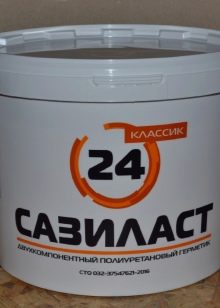
- Trademark Hobby... The company "Hermetic-Trade" is its distributor in Russia and sells a line of sealants on the Russian market, among which, as an example, we can single out the heat-resistant silicate sealing product "Hobby 1250c" used for fireplaces, stoves and chimneys. The composition of the sealant is capable of working at temperatures up to +1250 degrees.
- Trademark Abro industrials - under this trademark, an American company began to produce in Russia high-quality temperature-resistant sealants in small packaging for use in the installation and construction industry and automotive repairs.
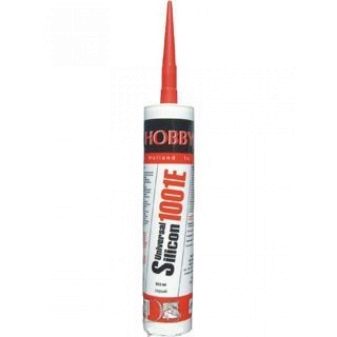
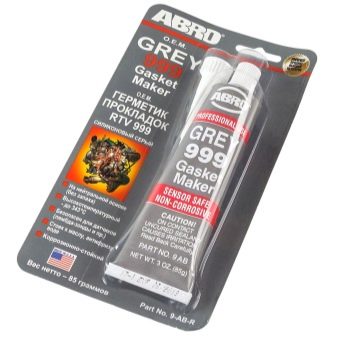
- Trademark Hilti manufactures sealants that are used for joints and seams of structures exposed to high temperatures. The most popular brands are P-301S, СР-606 - the sealing joints of these products withstand deformation well and can be painted on.
- Trademark Penosil belongs to the Estonian company Krimelte. This brand specializes in the production of polyurethane foams, various types of adhesives, sealants and other polymer products. The company's products are quite popular in Russia and are used for professional and domestic needs. An example of a fire-resistant sealant is Penosil Premium Sealant + 1500c - the product is used to seal the seams of chimneys, chimneys, fireplaces, boilers, stoves. It can withstand temperature loads up to +1500 degrees.
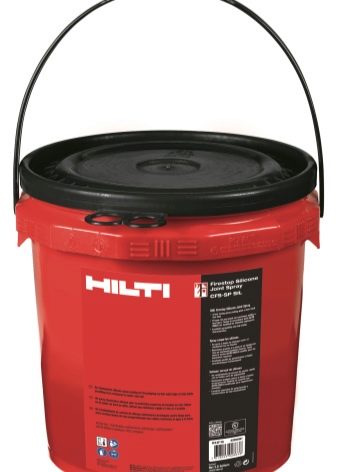
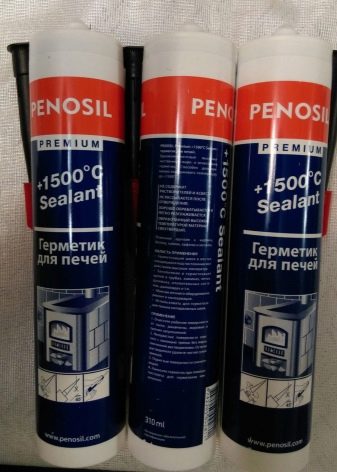
In fact, there are quite a few domestic and foreign brands that produce heat-resistant sealants, and here we have presented only a small part of them.
Tips & Tricks
Experienced specialists, when using a high-temperature sealant in the area of an open flame, advise paying attention when choosing a product grade to a direct indication of its refractory properties. After applying the sealing material, it needs some time for polymerization - each package has an instruction with such data. The sealing period must be strictly observed before proceeding to the subsequent stages of work. In the case when the work must be carried out in conditions of negative temperatures, the sealant must be selected with the properties of work in these temperature ranges and the possibility of adhesion to wet and frozen surfaces. If the sealed joint is located on a structure that has a certain amount of mobility, choose compounds that have high elasticity after polymerization.
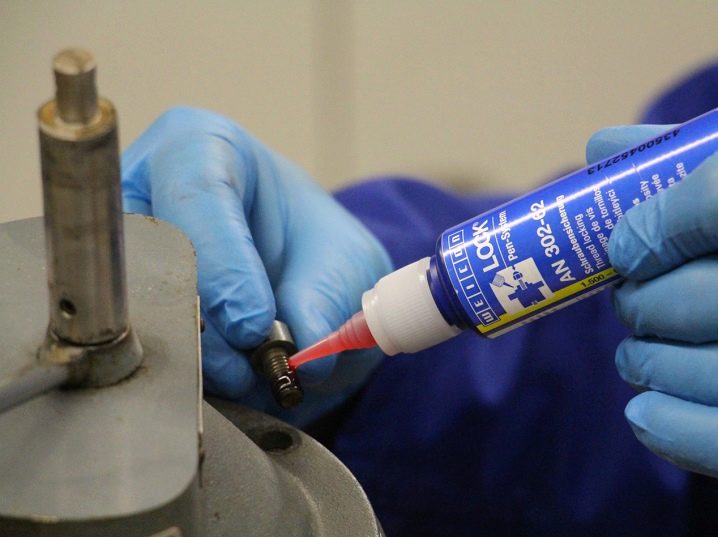
Some household sealants can work in humid environmentsbut that doesn't mean they'll be persistent underwater. Professionals recommend using highly specialized materials that are used in the field of shipbuilding for such purposes. And the last thing - when working with sealants, take care of personal protective equipment for your hands. If the sealant gets on the skin, it must be washed off immediately with water, since after a while it will be quite problematic to do this.

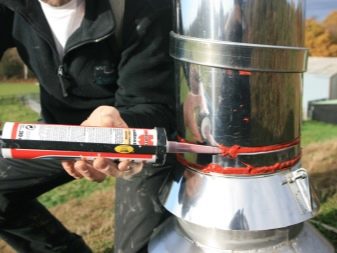
For the features and scope of heat-resistant sealant, see the following video.
The comment was sent successfully.