How to make a wind generator with your own hands?
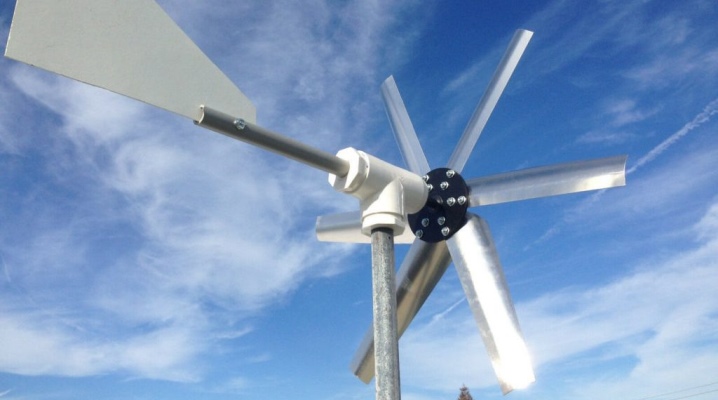
A wind generator for generating electricity is an irreplaceable source of electricity where there is not much sunlight, there are no rivers nearby, and there are no centralized power grids.
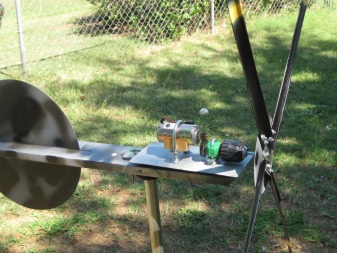
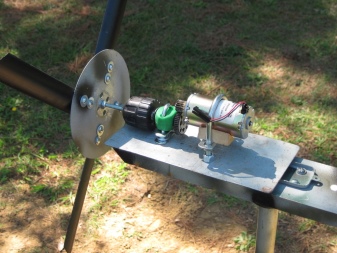
Design features
The principle of operation of a wind generator is the conversion of wind energy into electrical energy.
In other types of electric generators, the flow of water in the river, the force of oceanic tides and ebb tides are used as a source of mechanical (kinetic) energy.
In systems where heat energy is needed to generate electricity, they use:
- an engine running on gas, gasoline or diesel fuel;
- heat release from plates and blocks of a nuclear reactor, whose heat is used to convert water into steam - in a steam turbine;
- various types of fuel burned in a CHP plant, replacing heat, heat from a nuclear reactor.
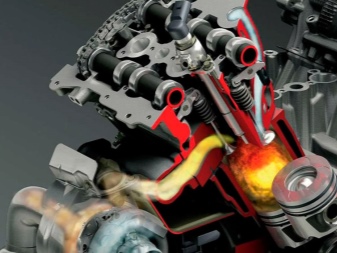
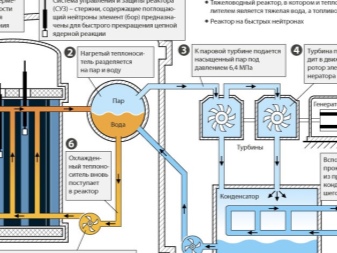
Solar panels stand apart, where light is used as a source of energy, and not heat or mechanical energy.
But back to the "wind turbines", whose operating principle is as follows. The force of the wind rotates the propeller, which drives the shaft of the motor generator. Together with the shaft, the rotor of the motor, on which permanent magnets are installed, rotates synchronously. The magnetic field, passing through the stator winding, induces an alternating current in it due to a change in the strength of the magnetic flux passing through the turns of the coils, from which the winding is assembled. An alternating electrical voltage is fed to an electronic circuit, where it is converted into direct voltage. Numerous devices and devices that need it work from direct current.
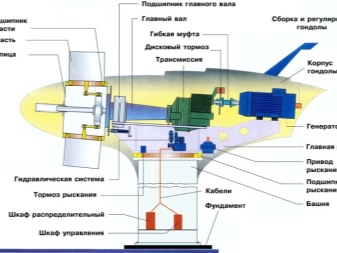
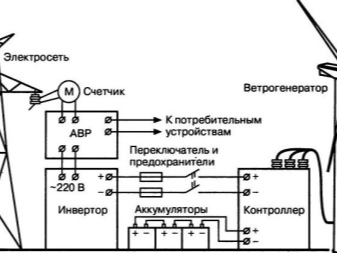
Anyone can make a generator for summer cottages or field conditions that generates alternating current with a voltage of 220 V. The more impressive the dimensions of the structure, the greater the efficiency of recoil will be received by a particular user. It is not a problem to make a generator that generates one or several kilowatts of electricity per hour. The electricity received from such an installation is capable of powering almost all electrical appliances in the house, including gardening equipment.
The wind generator is installed as high as possible - at the level of the roof ridge. There, the wind force reaches the maximum values indicated in the weather forecast.
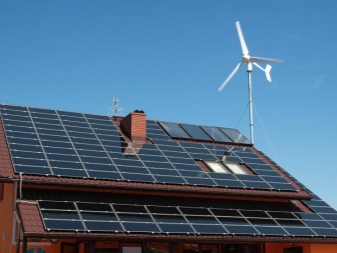
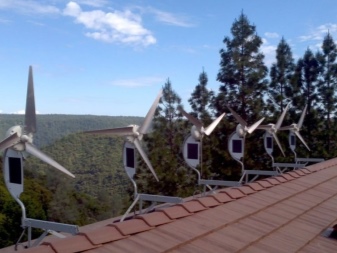
The installation vaguely resembles a weather vane with a propeller, thanks to which this structure turns where the wind blows. This is necessary in order to maximize the use of his strength, speed.
The horizontal propeller is rotated by a shank located at the rear of the unit. The vertical shank is not needed - its blades are located in such a way that the propeller itself will start almost half a turn, no matter which side the wind blows from.
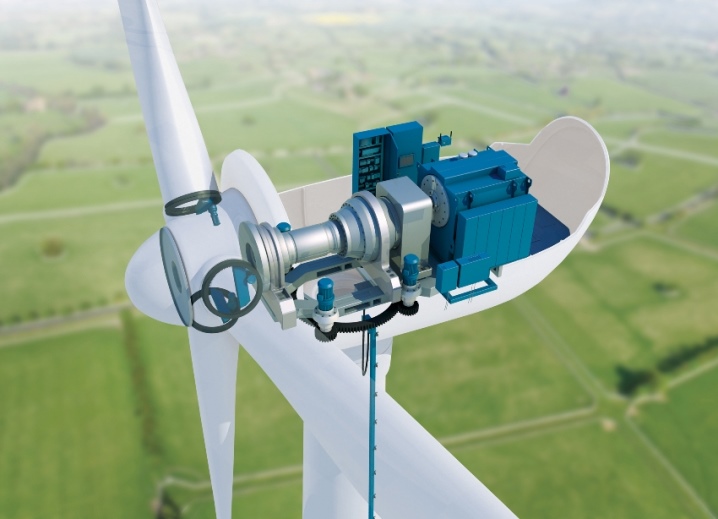
For a wind turbine to operate at maximum efficiency, a speed of 3000 rpm or more is required. For generators producing alternating current, this frequency corresponds to the value of 50 hertz, which is typical for domestic industrial power plants. After spinning a motor-generator weighing about 10 kg, it is not a problem to get 2 kW every hour.

What can be made of?
The main element of any model of a wind farm is a motor generator. It works like a motor - direct or alternating current makes the rotor (and with it the shaft) spin. Working the other way around - as a generator - is also possible.
Among the motors used as generators, there are brushed, brushless asynchronous and stepper motors. It is these three types of motors that are popular with amateurs who assemble wind turbines with their own hands.

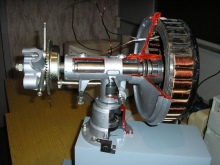
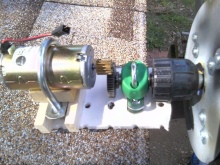
In a collector motor, the rotor windings (armatures) are located in a constant magnetic field of stator magnets. The constant voltage removed from the terminals of such a motor when its shaft with the armature is untwisted is transmitted from the current-carrying contacts of the armature through the brushes. The brushes themselves are the weak point of such an engine - they quickly deplete their resource. As a rule, such a generator is under constant load; when the armature moves, the brushes spark. Several days of continuous operation of such an installation can completely wear out the brushes, as a result of which the latter will need to be replaced.
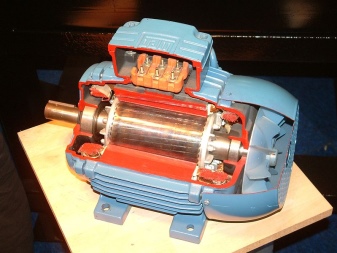
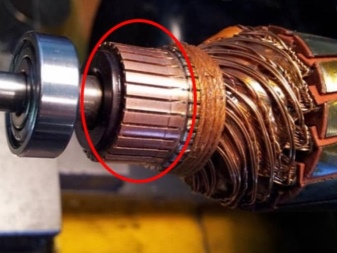
The use of brush motors as a generator with a constant active load is impractical.
The best option is the brushless engine. In it, a rotor with magnets rotates in the space between the stator windings. The windings themselves remain stationary, they do not need sliding contacts. Thanks to such a simple solution, the installation can operate for decades - it is important only once a season or every six months to lubricate the motor bearings, which are responsible for perfect, backlash-free rotation of the rotor. Popular solutions based on a brushless motor - asynchronous or stepper - are available to almost every home "DIYer".
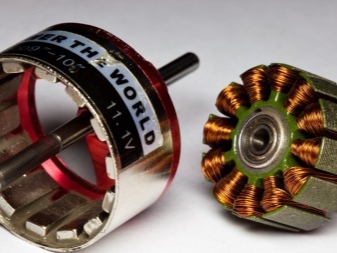
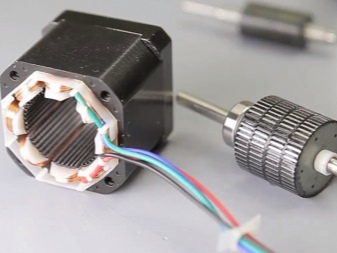
An asynchronous motor is used in power tools - for example, in a grinding machine. The stepper can be found in a wide variety of devices - from a motor-wheel of a bicycle to a mechanical drive of a printer or a disk drive.
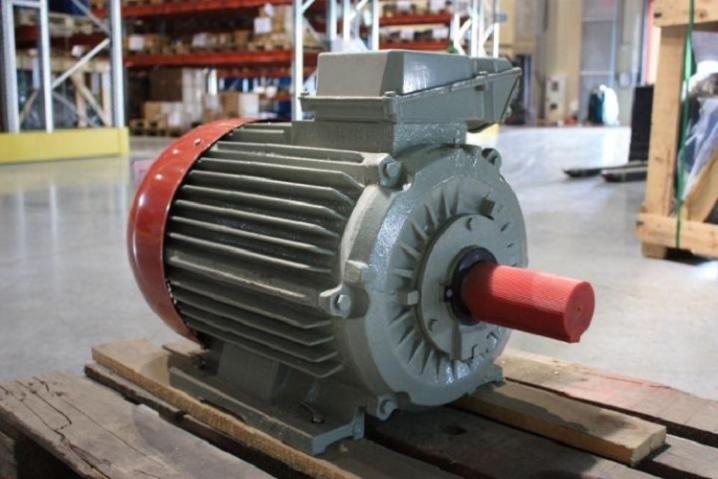
The variable brush motor used in rotary hammers, grinders, screwdrivers, jigsaws, and electric planers stands apart. Their disadvantage is the need to remove the brushes and the rotor bore for neodymium magnets. As a result, only the stator winding remains from the active windings - the rotor winding is completely removed.
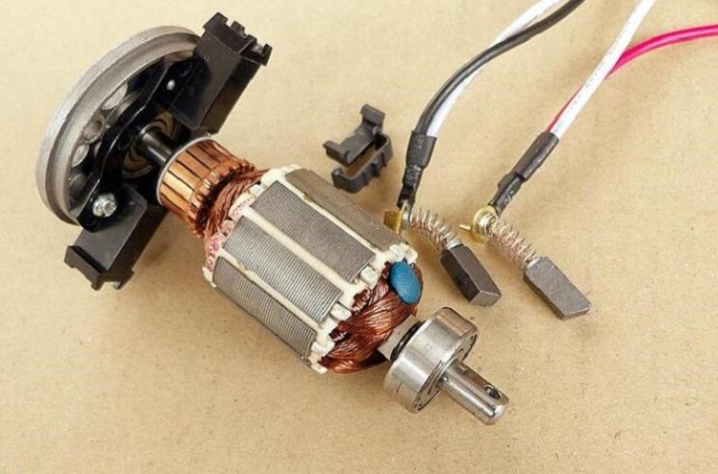
A wind turbine propeller can be made from plastic sewer pipes, PET bottles and similar recyclable materials. The lighter and stronger it is, the less wind force will be required to unwind it.
A wind generator made from a fan will require a rotor bore for neodymium magnets. The design of the household fan motor is not designed to receive electric current by spinning the rotor. A computer cooler (chip cooler) - a fan of the system unit of a PC or laptop - falls under the same alteration.
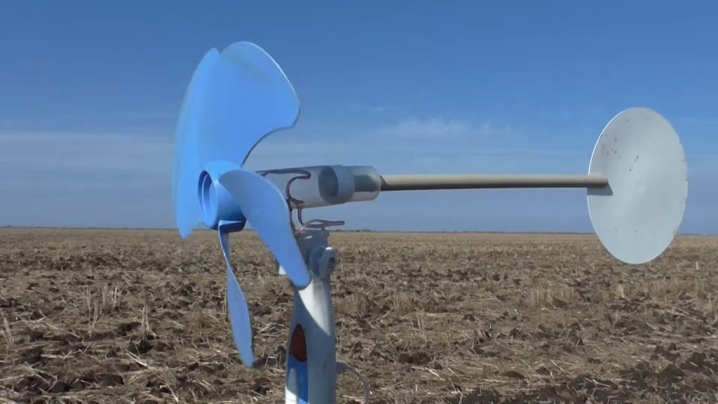
A tractor or car generator uses an additional field winding, which is powered by the battery of the machine itself. In order for the generator to produce, for example, an alternating current of 135 amperes with a voltage of 15 volts, the rotor excitation winding after turning on the ignition consumes a direct current of 3 amperes with a voltage of 12.6-14 V. The main source of energy for the generator is still the crankshaft of an internal combustion engine operating on gasoline, diesel or methane / propane. A tractor or car generator will require the removal of the field winding and the installation of neodymium magnets instead.
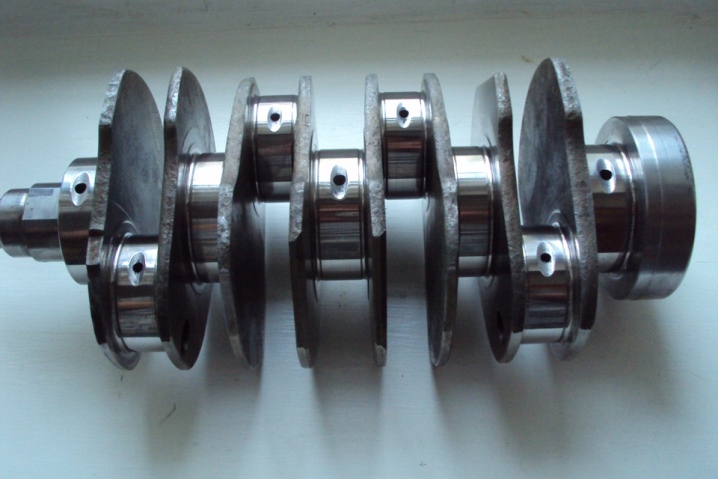
What is required?
The most common option is to use a washing machine engine for a homemade generator. If the old "washing machine" is not available, you can find such an engine at the junk shops in the household market, in the nearest service center for household appliances or a specialized store. It is not a problem to order such an engine from China.
Basically, a brushless asynchronous motor is used in washing machines.
Both new and used ones will work for a long time. 200 watts of power can be easily converted to kilowatts or more.
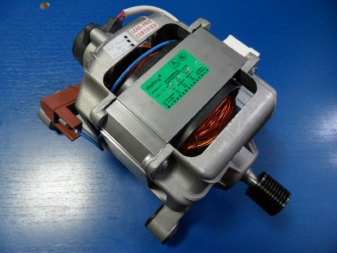
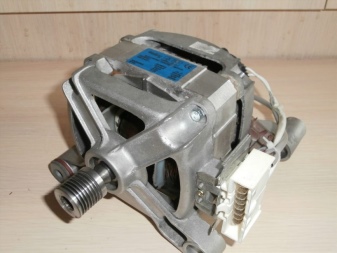
Materials (edit)
To assemble the generator, in addition to the motor, you need:
- neodymium magnets in sizes 20, 10 and 5 mm (32 in total);
- rectifier diodes or a diode bridge with a current of tens of amperes (observe the rule of a two-fold power reserve);
- epoxy adhesive;
- cold welding;
- sandpaper;
- tin from the side of a tin can.
Magnets are ordered online from China.
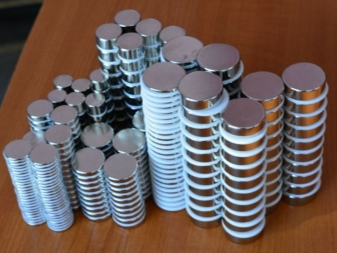
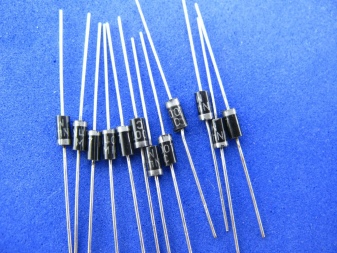
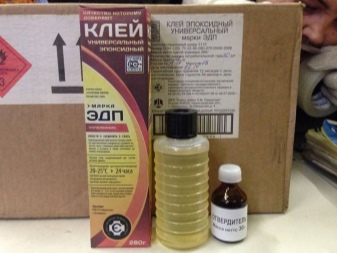
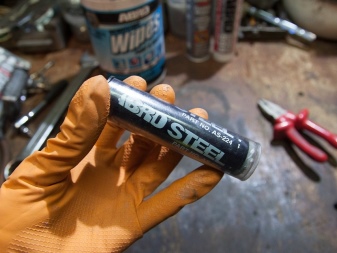
Instruments
The following tools will speed up the manufacturing process:
- lathe;
- scissors;
- screwdriver with nozzles;
- pliers.
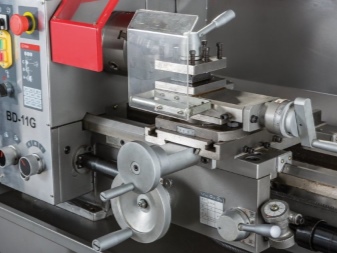
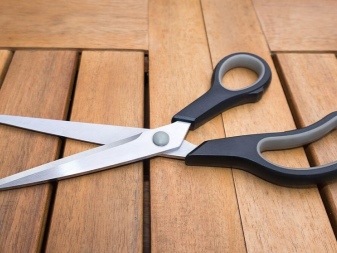
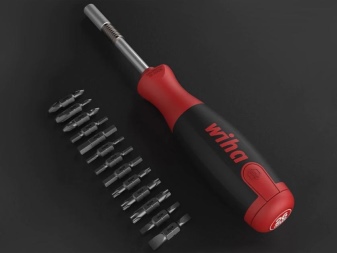

In the absence of a lathe, contact a friend who knows how to work on such a lathe.
Schemes and drawings
The generator as a device generates alternating current, which must be converted into direct current, brought to the required voltage value. If a motor-generator produces, say, 40 volts, then this is unlikely to be a suitable value for most consumer electronics using 5 or 12 volts DC or 127/220 volts AC.
The schematic of the entire installation, proven by time and millions of users, includes a rectifier, controller, battery and inverter. A car battery with a capacity of 55-300 ampere-hours is used as a buffer storage of stored energy. Its operating voltage is 10.9-14.4 V with a cyclic charge (full charge-discharge cycle) and 12.6-13.65 with a buffer (portioned, dosed, when you need to recharge a partially discharged battery).

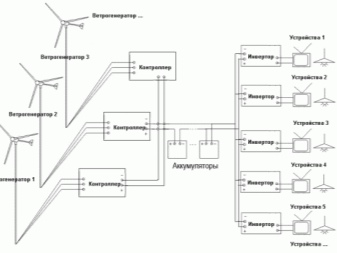
The controller converts, for example, the same 40 volts into 15. Its efficiency in volt-amperage ranges from 80-95% - excluding losses on the rectifier.
The three-phase generator has the greatest efficiency. - its output is 50% more than that of a single-phase one, it does not vibrate during operation (vibration loosens the structure, making it short-lived).
The coils in the winding of each of the phases alternate with each other and are connected in series - like the poles of the magnets, one of the sides facing the coils.
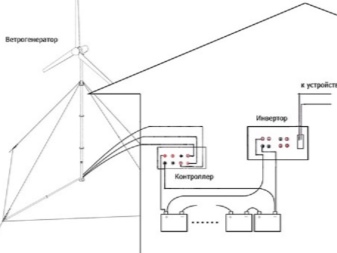
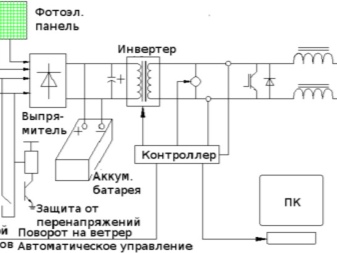
The task of the inverter is to convert a constant voltage of about 12 volts taken from the battery into an alternating voltage of about 220.
Modern household appliances and electronics are capable of operating from 110 volts (American standard for household networks) up to 250 - it is not recommended to give more to network appliances and devices. All converters are impulse, in comparison with linear ones, their heat losses are much less.
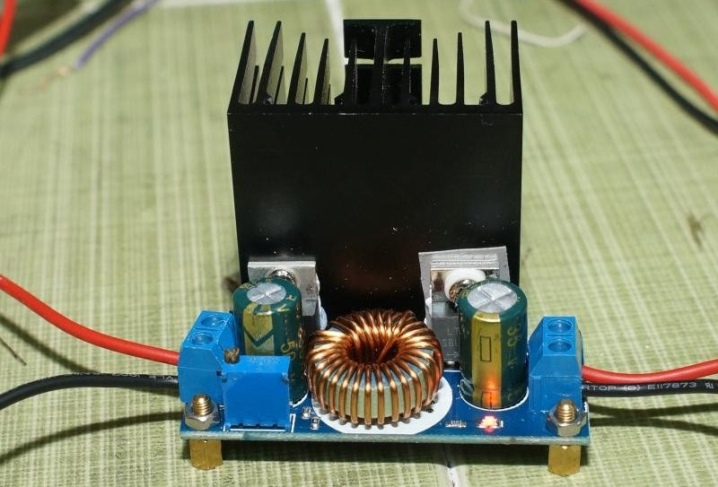
Manufacturing steps
To modify the design of the induction motor, do the following.
- Disassemble the motor and take out the rotor.
- Remove the plates from the rotor armature. Trim them to a depth of 2 mm.
- Make grooves up to 5 mm deep - for magnets.
- Mark a strip of tinplate for the magnets. They should be equally spaced from each other - this will prevent unnecessary loss of power of the installation.
- Attach them to this strip of tin with superglue. Fix the strip with magnets on the anchor.
- Fill the space between the magnets with cold welding or epoxy glue.
- Remove burrs and unevenness on the rotor with sandpaper.
- Check - and replace if necessary - motor bearings and bolts.
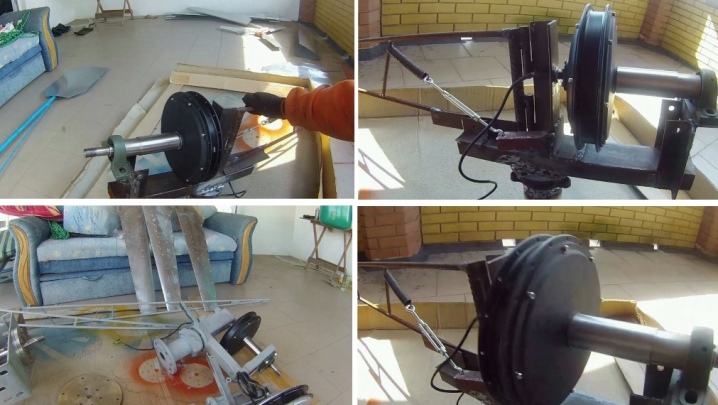
Assemble the motor generator. The device is ready for further installation. To check the device, clamp its shaft in a drill or screwdriver chuck and accelerate to 1000 rpm.
A voltage at the ends of the winding from 110 volts can be considered suitable.
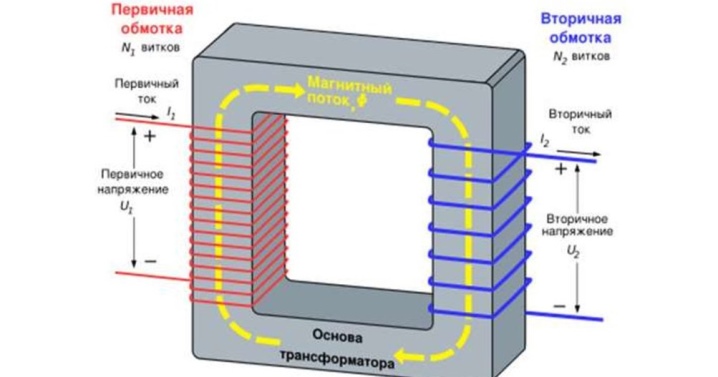
At a lower value, the error lies in the uneven alternation of magnets at any point of the armature rotation circle.
To assemble the wind turbine, do the following.
- Cut out identical pieces from a PVC pipe with a diameter of 11-16 cm, corresponding in length to the future blades.
- On each segment, draw an arbitrary line and retreat from it on both sides by 22 mm. Accordingly, the width of one blade will reach 44 mm. Repeat this action for the opposite end of the line segment.
- Straight connect the extreme points on one side of the center line.
- Draw on the other side the outlines of the future blade.
- Cut out the resulting blade and round off its free end by sharpening. Repeat the above steps for the rest of the blades.
- Attach the blades to the hub using a bushing adapter. Bolts with nuts and spring washers are suitable as fasteners. The width of each blade along its entire length ranges from 44 to 88 mm.
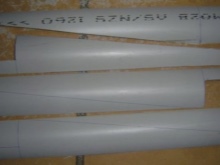
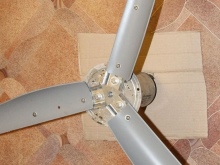
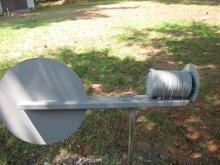
This is enough for the wind to spin the impeller at a speed of 3 m / s. The resulting structure must be balanced - correct balancing will prevent the formation of blind spots that slow down the generator when the propeller rotates.
A motor-generator with an installed impeller can be placed in a protective sleeve that protects it from atmospheric precipitation. Staying dry in all weather conditions, protected from rain and snow, the generator will last for years. To assemble the guard, do the following:
- in a pipe with a diameter of 7.5 cm, cut a longitudinal groove 2 cm wide;
- cut the back end of the cut pipe at a 45 degree angle;
- place the motor generator with the propeller in this tube and fix it to it.
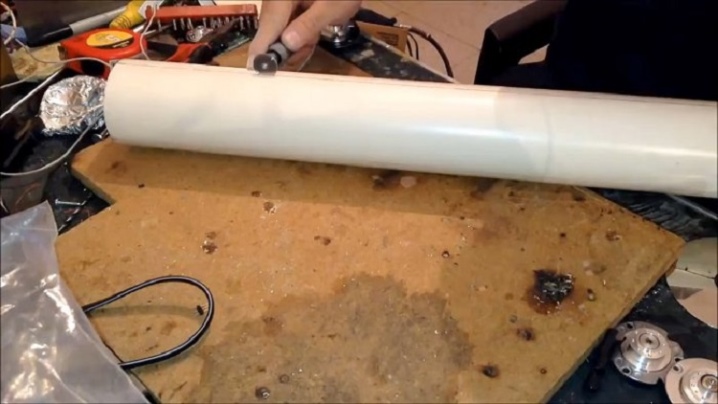
Free rotation of the motor will require a ball-bearing swivel joint, similar to that found in a domestic fan. It can turn endlessly to either side.
So that the cable, with the help of which the currents induced in the stator winding are removed, does not wind up or twist, the connection in the hinge must be sliding, but providing a reliable, stable electrical contact of the motor-generator with further located functional units of the circuit.
The best contact will be provided by gold-plated terminals taken from any old technology.
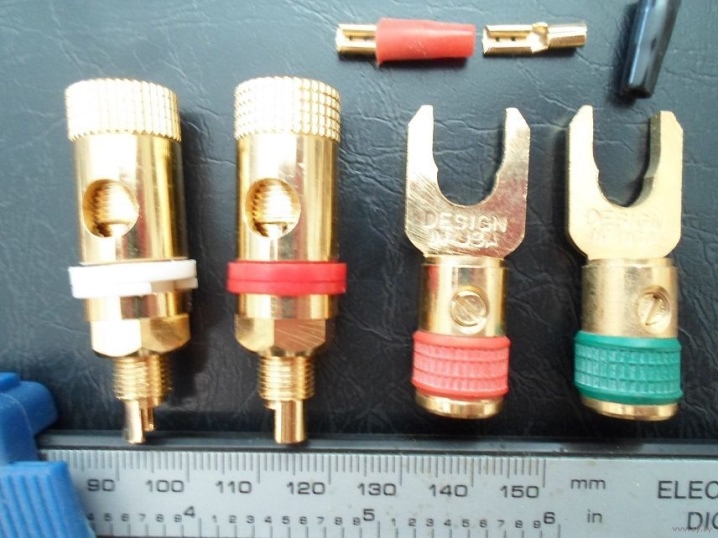
The use of a brush-graphite contact is unjustified - graphite has an electrical resistance an order of magnitude higher than that of aluminum and steel, and the power of the installation will noticeably decrease. The hinge is installed on a base made of a piece of a shaped pipe. After assembly, they check whether the resulting swivel mechanism is jammed, does not spin and whether the cable is frayed.
Providing a sliding contact and free rotation of the installation in the direction of the wind, a shank, made, for example, of a plastic water pipe and a piece of sheet plastic or aluminum, is attached to the additional outer casing of the motor.
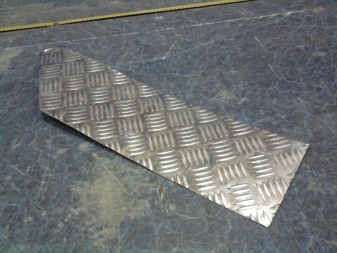
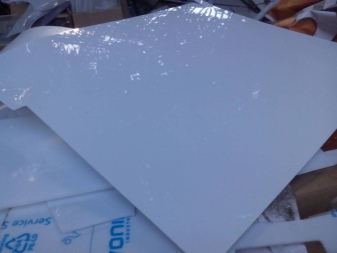
A round or profile pipe is used as a support, one end of which is concreted in the ground - not less than a meter. So that the support does not lurch over time from the hurricane, it is supplemented with three or six stretch marks, converging in the center at the same angle and directed in different directions.
After completing the assembly of the motor-generator part, a diode rectifier is mounted next to the motor, if necessary. The current losses in the wires can be significantly reduced by using a step-up transformer located near the generator set - as in lines that transmit industrial electricity over long distances.
The charge controller, battery and inverter are included further according to the diagram. The wind turbine is fully assembled and ready to go.
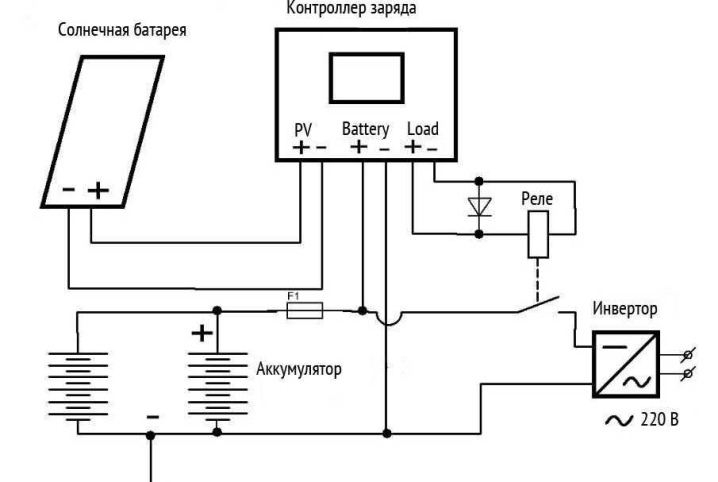
Recommendations
A home-made windmill for a private house generates a constant or alternating voltage of several tens of volts, which is an increased danger to a person. Live contacts and wires must be reliably insulated - rainwater is an acidified environment that conducts electric current well.
Work on a lathe or grinder is carried out in protective goggles and gloves. It is forbidden to assemble the circuit when the wind turbine is running.
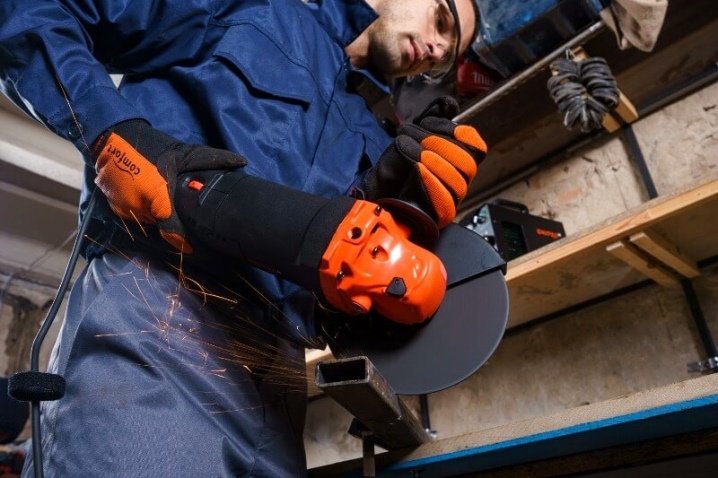
Wind energy is fickle. The best solution would be a low-speed generator with more than a dozen magnets and coils. The more coils, the thicker the winding wire should be. Too thin a section due to a total resistance of tens of ohms will reduce the useful power of the generator by several times. For a serious load - for example, from an electric stove or a washing machine - at 220 volts, a current of up to 10 A.
The design of a homemade generator - unless a converted engine is used for generating electricity - must be perfectly flat and symmetrical. Before installing the coils and magnets, the "spinner" itself must be centered. It doesn't matter what is used - a discarded CD or a homemade miniature copy of a windmill, the slightest imbalance is already unacceptable.
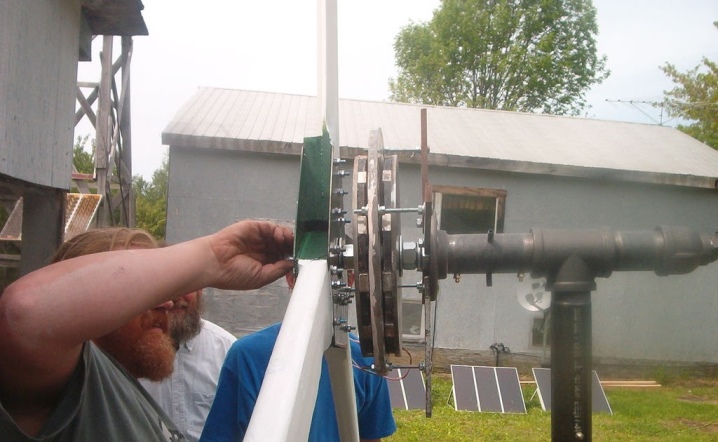
Try to achieve minimal noise - ideally, it should be absent. If your installation, which is not lubricated in the place of the bearings, is complained about because of the constant squeaking and knocking when rotating, such a complaint can lead to problems with the law, especially at night. The rest of the reasons to claim you as the owner of a wind turbine are insignificant - wind turbines are completely legal, since the owner of this device does not produce electricity with it on an industrial scale, as is done in Europe and America.
The installation should not be too high - above the pillars along which power lines pass. In every city, summer cottage or rural settlement, there is a restriction on the height of the structures being built.
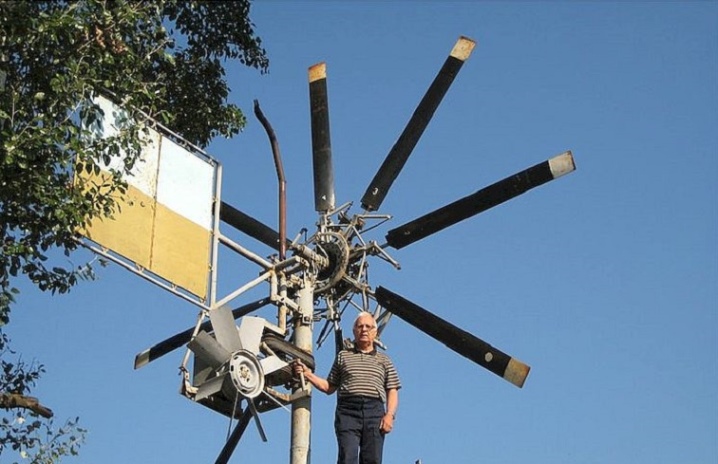
For example, supplying a 40-meter tower for a cellular base station requires a series of approvals and checks from government regulatory agencies. The same applies to wind turbines.
Correctly and extremely responsibly approaching the solution of the problem with electricity with the help of a wind generator, the consumer will get rid of downtime associated with power outages. It is always better to work ahead of the curve - within the framework of the law - than to wait for years on what the authorities promise.
How to make a wind generator with your own hands, see below.
The comment was sent successfully.