Features of membrane compressors
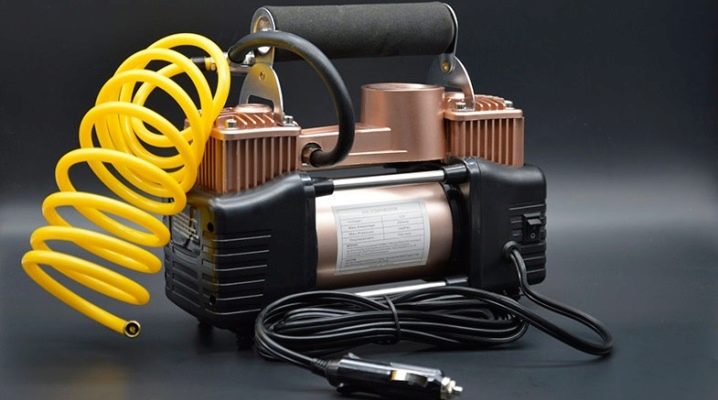
To choose a good diaphragm compressor, you need to be guided by the tasks for which you need it. In the article we will consider the principle of operation, areas of use and features of these devices.
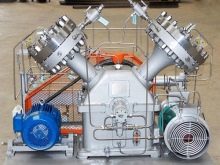
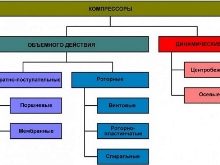
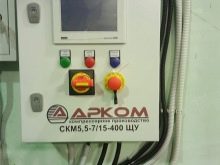
Device and principle of operation
Diaphragm compressors include modernized analogs of a piston unit. Their principle of operation is based on volumetric action. In this case, the working fluid is compressed by a metal membrane. The compressor consists of a diaphragm, crankshaft, pusher, intake and exhaust valves, housing. Inside there is a gas, hydraulic cavity, a distribution disc. The pneumatic unit circuit includes a shut-off valve, a membrane block, a heat exchanger, a drive crankcase, and an electric motor. In addition, it has a bypass and non-return valve, a throttle, a compensation pump.
The gas inside the compressor is compressed by means of a flexible, reciprocating diaphragm. It is driven by a pusher, which is attached to the crankshaft. It is fixed on the working chamber along the perimeter. Due to this, piston rings and sealing rings are not used in the diaphragm compressor. The inlet and outlet valves seal the separated suction cavities. Lobe valves are most commonly used in such devices.
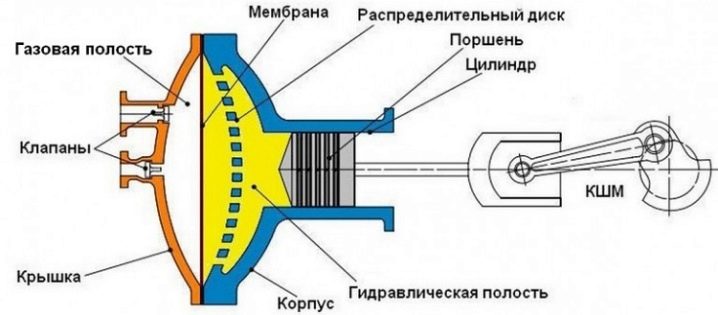
In addition to the membrane, only the inner surfaces of the working chamber are in contact with the gas in the compressor. As a result, diaphragm compressor systems are used for pumping toxic and explosive gases. During the retraction of the membrane, the volume of the compression chamber increases. The gas pressure drops. The inlet valve opens and the chamber is quickly filled with working gas.
The stem then pushes the membrane, which leads to a decrease in the volume of the compression chamber and an increase in gas pressure. The inlet valve closes, the outlet valve opens. Due to the high pressure, the working gas is supplied to the outlet. Then the diaphragm is pulled back, the outlet valve is closed and the entire working cycle is repeated. This principle ensures a constant flow of gas into the connected device. The membrane is driven by different mechanisms.
In addition to automation, the type of drive is mechanical, diaphragm-piston, magnetic, pneumatic.
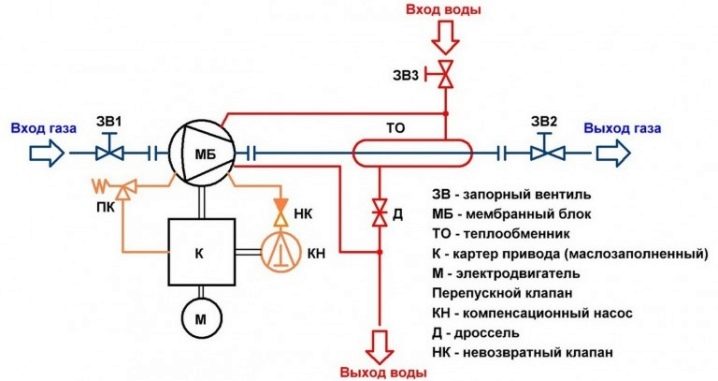
Specifications
Diaphragm compressor devices are unpretentious in operation and structurally simple. Membranes are key structural elements. They are made of rubber or other elastic raw materials, as well as metal. The inner cavity of the diaphragm is attached with an air outlet from the unit. The air flow is in one direction. The device has no dynamic seals in the compression zone.
It is capable of compressing gas up to 400 bar and more. A diaphragm rupture sensor is installed in it. It is practically silent, in most cases it is performed in one stage. Most often it has water cooling, less often air cooling.
Depending on the type, it can be supplied with an additional option.
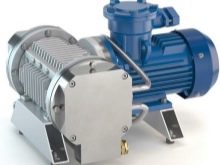
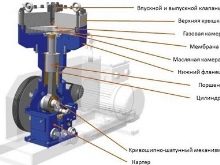
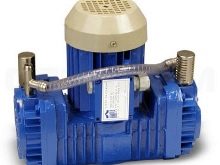
The models are equipped with a pressure and temperature switch of the gas stages, a remote control system. They can be integrated with a closed loop water cooling system on a chiller basis. Other modifications are equipped with separators or filtering devices for compressor suction. An equally useful option is an adsorption-type dehumidifier with a dew point of -20, -40, -55, -70 degrees.
The power of the models varies in the range of 3-18.5 kW, the productivity is from 5 to 240 Nm3 / h... The devices do an excellent job of compressing all types of gas without the risk of leaks. Based on the parameters of the device, the operating speed can be 250-720 rpm, the pressure ratio is 1: 20, they work from a voltage of 12 volts.
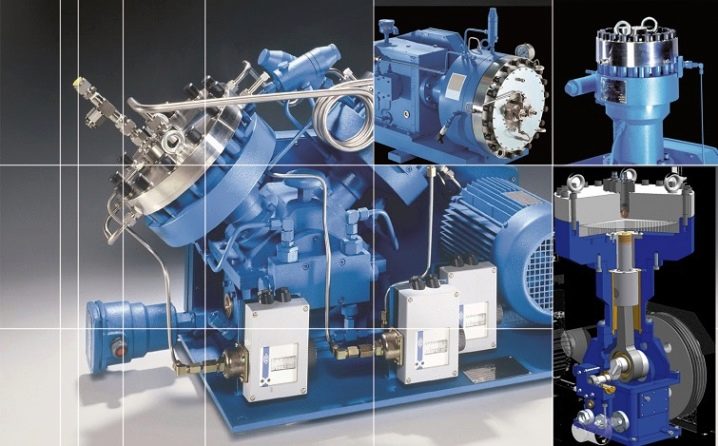
Comparison with reciprocating compressor
Diaphragm compressors are more popular than reciprocating counterparts. They are better in a number of characteristics.... The key one is ability of the diaphragm to keep oil out of the piston... These devices are cheaper than piston devices, they are common as amateur-type equipment. They pump viscous liquids worse. They are bought for intermittent use and small amount of work. Piston units are not capable of producing a perfectly clean compressed substance at the outlet.
To reduce friction, they use a lubricant that penetrates through the seal into the cylindrical working cavity. They have high performance and unpretentiousness. However, the performance of membrane models is significantly lower. In addition, the membrane wears out quickly. On average, it is enough for about 500-1000 hours of work.
To prevent oil from getting into the compressible substance, you need to constantly change the membranes. Regardless of the diaphragm mechanism, the compression is always effective.
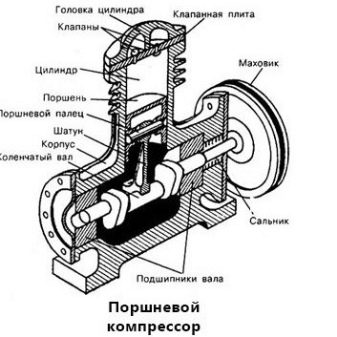
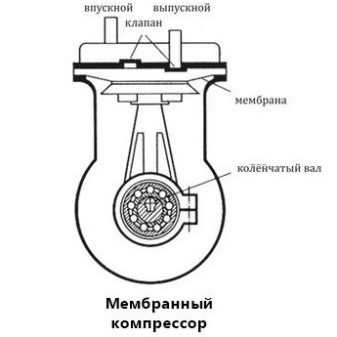
Gas leakage is excluded, outlet air is always clean. In this case, the required values are achieved not by several stages of devices, but by one or two. It is much more convenient. The advantage of the devices is their compactness. They can be installed in small laboratories and medical centers. They are capable of completely purifying the final product. Reliable and durable enough.
Equipped with an emergency shutdown mechanism that is triggered when there is a risk of membrane damage. Their maintenance is minimal. However, repairs are expensive. A significant advantage of the systems is the absence of the need for lubrication of the internal surfaces. In order to reduce vibration, they are equipped with rubber bearings.
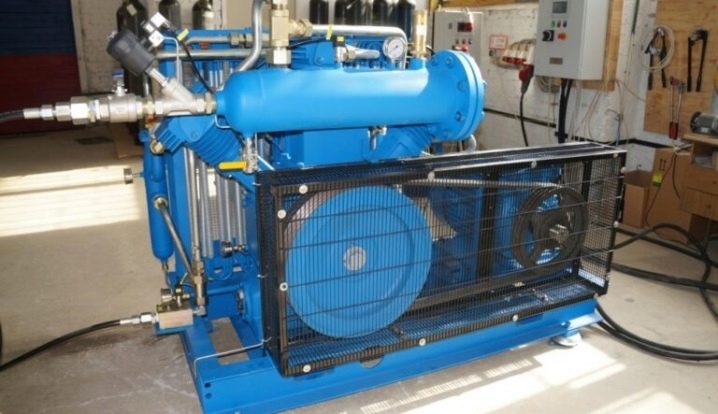
Popular manufacturers
The leading companies in Germany, USA, Italy, Switzerland are engaged in the production of membrane compressors. The official distributor of various suppliers of industrial equipment in our country is the company Intech GmbH.
- Diaphragm compressors are offered to domestic buyers by the trade mark "Kovint KSVD-M"... The brand's lineup includes 1- and 2-stage models designed for the compression of industrial gases from atmospheric pressure.
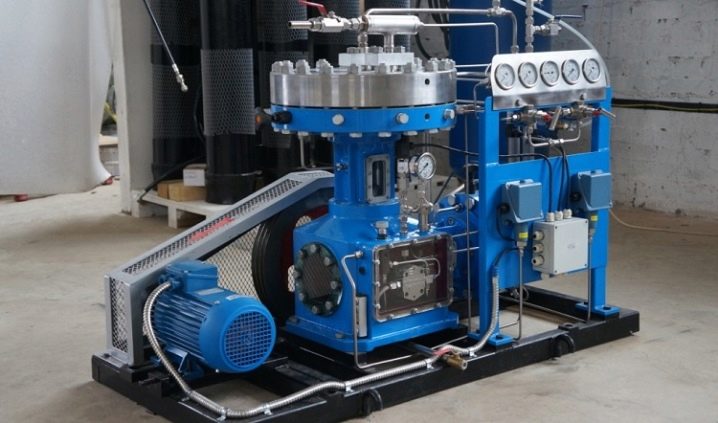
- One of the well-known manufacturers is the compressor company "Arkom", which produces high pressure compressor equipment without oil compression of gases.
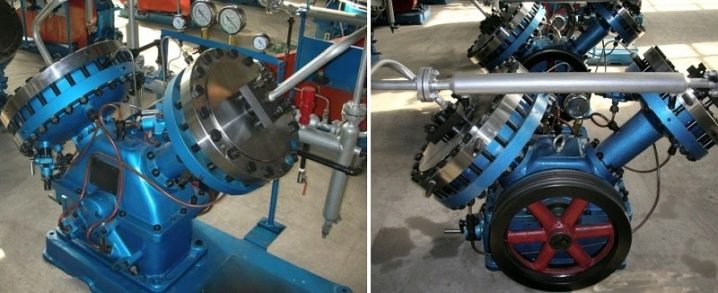
- AirMac supplies the market with products for industrial and home use. The models have good performance. They are reliable, stable in operation, and work due to the electromagnetic pulses of the membrane.
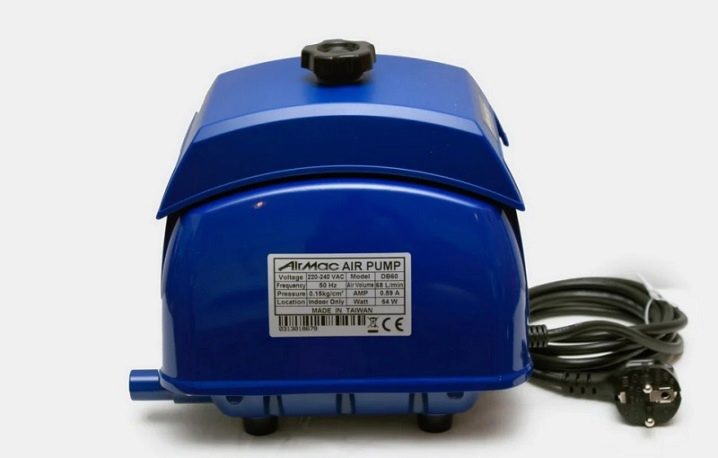
- HIBLOW (a registered brand of the Japanese company Techno Takatsuki Co., Ltd) produces high-tech professional equipment. The supplier's products are designed for consumers with different budget options.
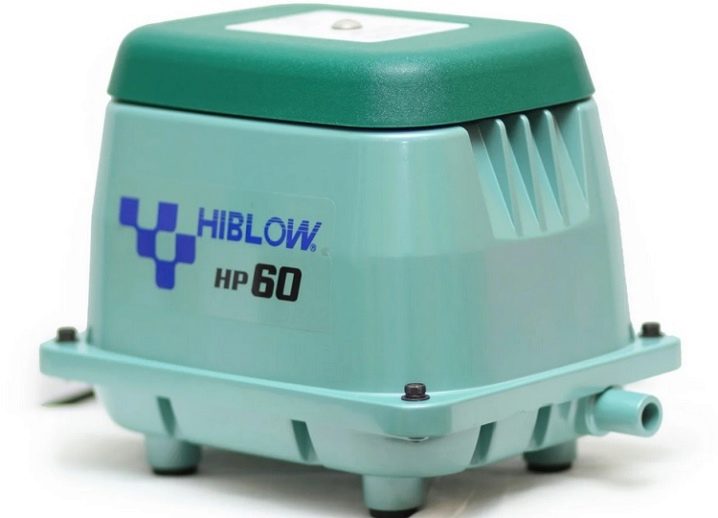
- Japanese brand SECOH is engaged in the production of universal membrane equipment that can be used in various fields. The membrane has wide temperature capabilities (from -10 to +40 degrees). The units are noiseless, inexpensive, equipped with a rupture protection for the main element.
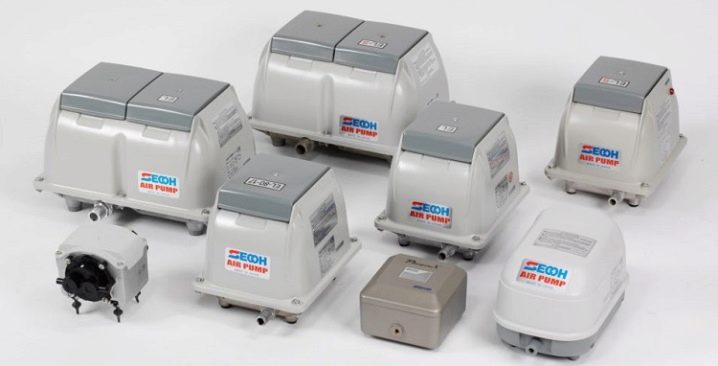
- "Thomas" Is a leading manufacturer of membrane systems that can be used in a wide variety of applications. The brand's products are simple, comfortable, quiet in operation. They have a low vibration level.
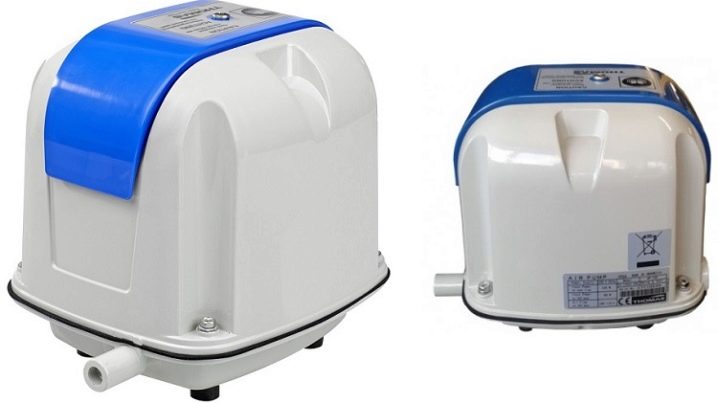
Applications
Diaphragm compressors have a wide range of uses... For example, they are bought for inflating passenger car tires. With their help, the carburetor is blown through, air is pumped.They are used to clean the water of an aquarium (aquarium version), a pond. They are used to aerate water. Moreover, they can work without shutdown for a long time. They are needed to aerate the septic tank, with their help they carry out small volumes of painting. They are used for research purposes. They are physiotherapy equipment. They have found application in the nuclear, oil and chemical industries. Compressors are used to test and calibrate critical systems. For example, these include elements of anti-missile systems that cannot be tested in any other way.
These devices are actively used in pharmacology and food industry.... They are used in electric and gas stations. With their help, the polluted environment is cleaned, using for sampling gas samples. They analyze atmospheric conditions, determine the carbon content in tunnels on the highway. Freon is processed and used in pilot installations. Diaphragm compressors are used in syngas applications. Today they are used in fuel cells as well as to capture greenhouse gases. The type of application is determined by the type of membrane. For example, models with metal elements are used to handle highly corrosive and radioactive gases.
Teflon diaphragm counterparts have proven their worth in sampling in LNG plants. They are used when taking samples of the polluted environment.
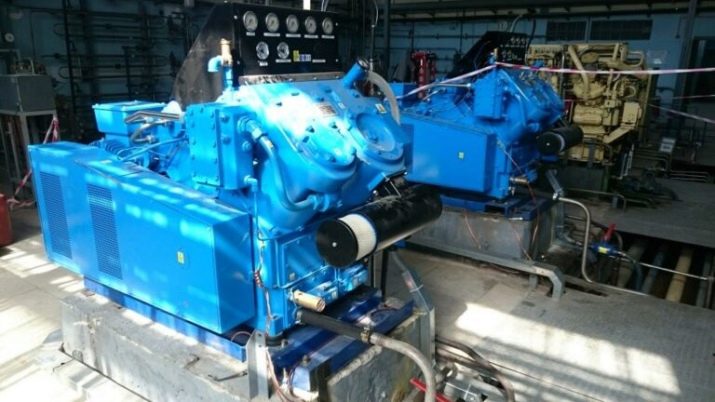
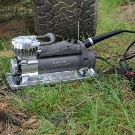
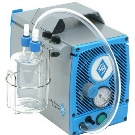
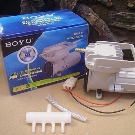
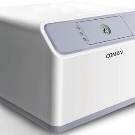
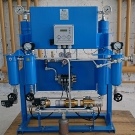
The comment was sent successfully.