Construction and installation of formwork for strip foundations
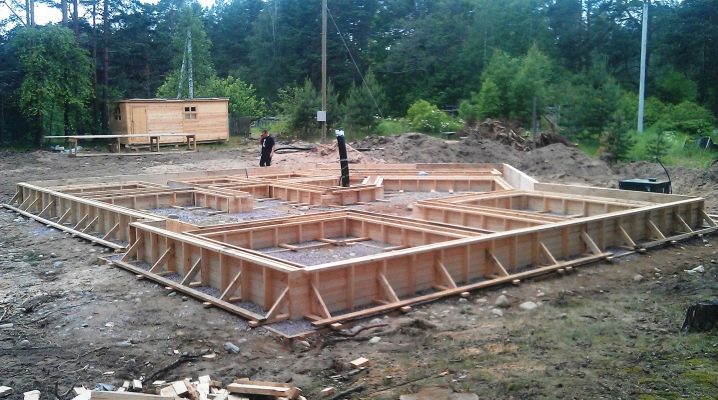
The construction of a private house is impossible without the construction of its main part - the foundation. Most often, for small one- and two-story houses, they choose the most inexpensive and easy-to-build strip base structure, the installation of which is impossible without formwork.
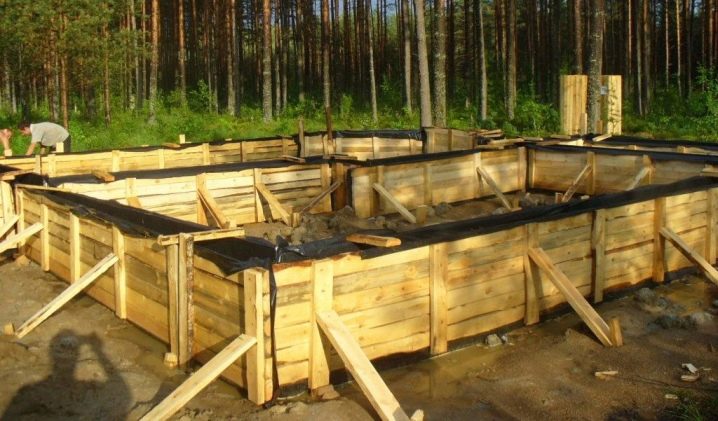
What is it for?
The formwork for the strip foundation is a support-shield structure that gives the liquid concrete solution the required shape. Its main task is to ensure the strength of the entire building.
A properly installed structure must meet the following requirements:
- keep the original shape;
- distribute the pressure of the solution over the entire base;
- be airtight and erect quickly.
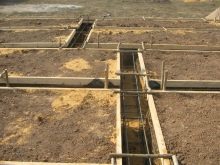
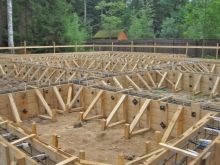
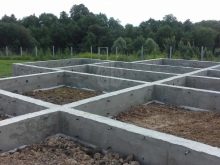
How does the structure work?
The mortar mold can be built from different materials. These include wood, metal, reinforced concrete and even expanded polystyrene. The formwork device made of each such material has its own advantages and disadvantages.
Wooden
This option is the most economical - it does not require special professional equipment. Such formwork can be made from edged boards or plywood sheets. The thickness of the board should vary from 19 to 50 mm, depending on the required strength of the board. However, it is quite difficult to install the tree in such a way that no cracks and gaps appear under the pressure of concrete, therefore this material requires additional fixation with auxiliary stops for reinforcement.
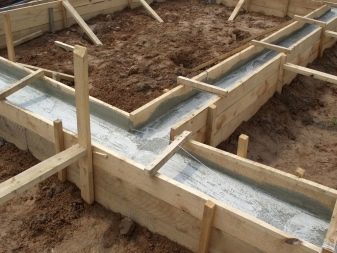
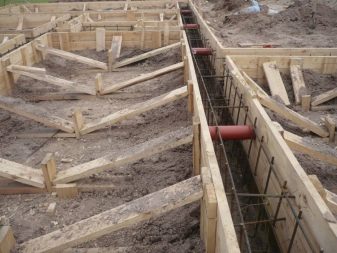
Metal
This design is a durable and reliable option that requires steel sheets up to 2 mm thick. There are certain advantages to this design. Firstly, due to the flexibility of steel sheets, complex elements can be erected, and they remain airtight, moreover, they have high waterproofing. Secondly, the metal is suitable not only for tape, but also for other types of formwork. And, finally, the part of the formwork protruding above the ground can be decorated in various ways.
Among the disadvantages of this design, in addition to the complexity of the arrangement and the high cost of materials, it is worth noting the high thermal conductivity and significant specific gravity, as well as the laboriousness of its repair (argon welding will be required).
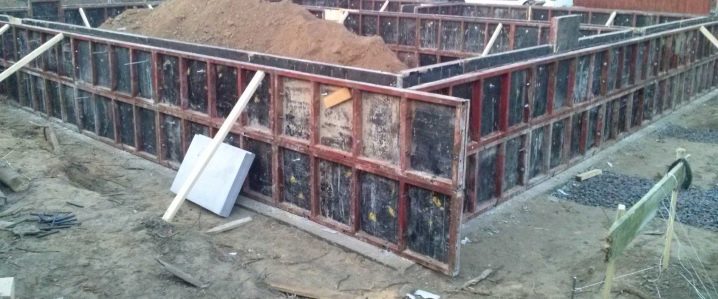
Reinforced concrete
The most expensive and heavy construction is the reinforced concrete formwork. It is necessary to additionally purchase or rent professional equipment and fasteners. Nevertheless, this material is not so rare due to its strength and service life, as well as the ability to save on the consumption of concrete mortar.
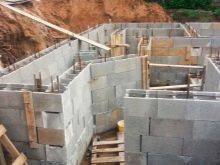
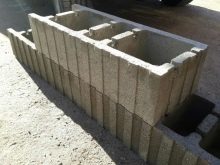
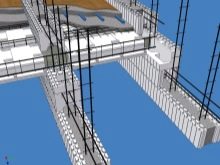
From EPS (extruded polystyrene foam)
The material is also from a high price category, but it is gaining more and more popularity due to a variety of shapes and sizes, low weight and high thermal and waterproofing properties. It is easy to install it with your own hands, and even a beginner can handle such work.
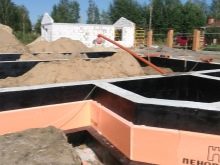
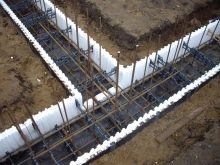
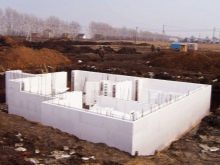
There is also an option for erecting formwork from sheet corrugated slate. However, this option is difficult to insulate and strengthen properly, so it is used quite rarely and only if there is no other material at hand.And the use of expensive plastic shields, which are removed and transferred to a new site, is justified only if it is planned to build at least a dozen different foundations.
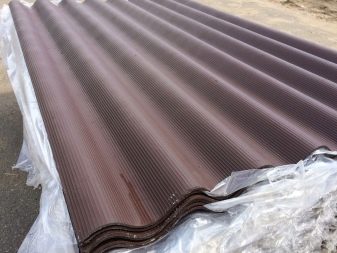
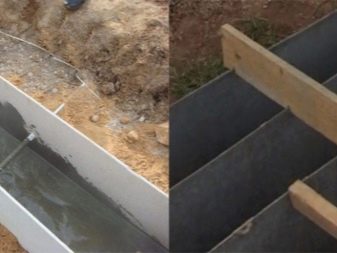
The design of a small-panel formwork is quite standard for any material and consists of several basic elements:
- shields of a certain weight and size;
- additional clamps (struts, spacers);
- fasteners (trusses, locks, contractions);
- various ladders, crossbars and struts.

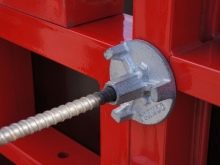
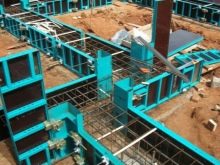
For large-sized formwork erected during the construction of heavy multi-storey structures, in addition to the above, the following additional elements are required:
- struts on a jack to level the shields;
- scaffolds where workers will stand;
- bolts for screed shields;
- various frames, struts and braces - for the stability of a heavy structure in an upright position.
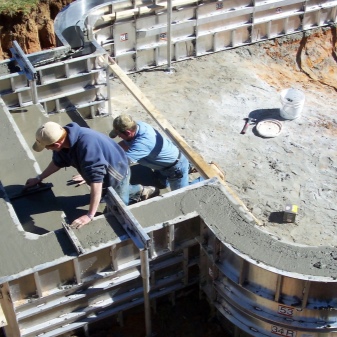
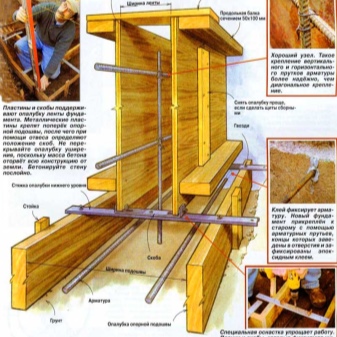
There are also climbing formworks used for tall towers and pipes, as well as girder and beam-panel options, various complex structures for the construction of tunnels and long horizontal structures.
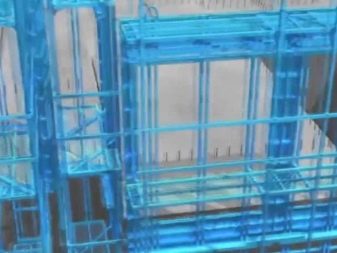
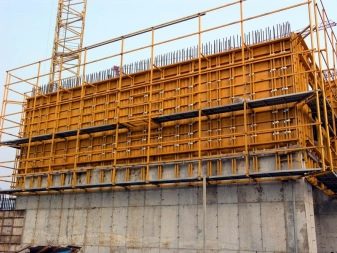
Depending on the design features, the formwork is also divided into several types.
- Removable. In this case, the boards are dismantled after the mortar has solidified.
- Non-removable. Shields remain part of the foundation and perform additional functions. For example, polystyrene foam blocks insulate concrete.
- Combined. This option is made of two materials, one of which is removed at the end of the work, and the second remains.
- Sliding. By raising the boards vertically, the basement wall is mounted.
- Collapsible and portable. It is applied by professional construction crews. Such formwork made of metal or plastic sheets can be used up to several dozen times.
- Inventory. Consists of plywood sheets on a metal frame.
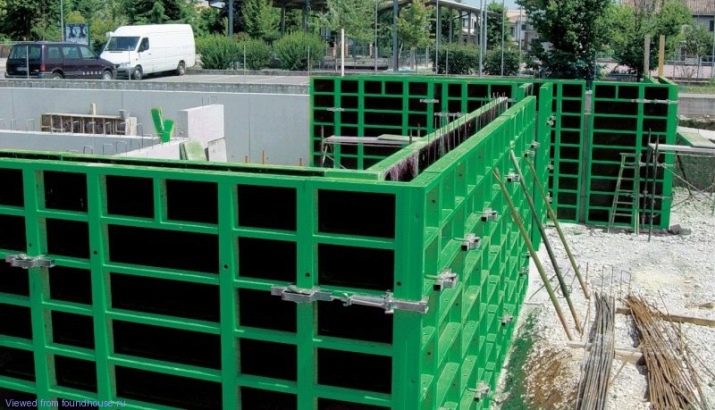
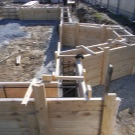
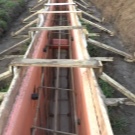
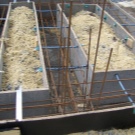
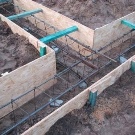
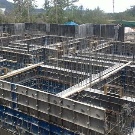
Manufacturing
In order to calculate and install the formwork with your own hands, it is necessary, first of all, to draw up a diagram of the future foundation. Based on the resulting drawing, you can calculate the entire amount of material that will be required for the installation of the structure. For example, if standard edged boards of a certain length and width will be used, then it is necessary to divide the perimeter of the future base by their length, and the height of the base by their width. The obtained values are multiplied among themselves, and the number of cubic meters of material required for work is obtained. The costs of fasteners and reinforcement are added to the cost of all boards.
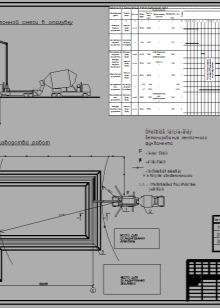
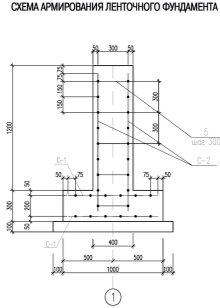
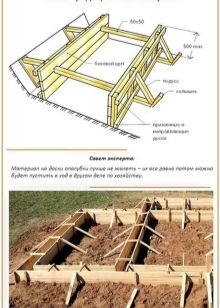
But it is not enough to calculate everything - it is necessary to correctly assemble the entire structure in such a way that not a single shield falls, and the concrete does not flow out of it.
This process is quite laborious and is carried out in several stages (for example, panel formwork).
- Preparation of tools and materials. After the calculations, they buy wood, fasteners and all the missing tools. They check their quality and readiness for work.
- Excavation. The site on which the work is planned is cleared of debris and vegetation, the topsoil is removed and leveled. The dimensions of the future foundation are transferred to the finished site with the help of ropes and stakes and a trench is dug along them. Its depth depends on the type of foundation: for the buried version, a trench is needed deeper than the level of freezing of the soil, for the shallow one - about 50 cm, and for the non-buried one - a few centimeters are enough to simply mark the boundaries. The trench itself should be 8-12 cm wider than the future concrete tape, and its bottom should be compacted and even. A "pillow" of sand and gravel up to 40 cm thick is made at the bottom of the recess.
- Formwork manufacturing. The panel formwork for the strip type of foundation should slightly exceed the height of the future strip, and the length of one of its elements is carried out in the range from 1.2 to 3 m. The panels should not bend under the pressure of concrete and let it pass at the joints.
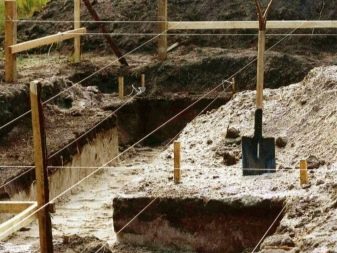
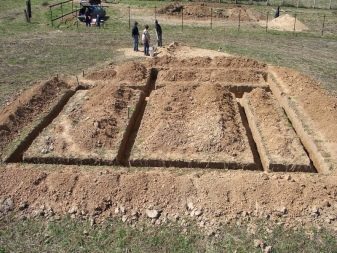

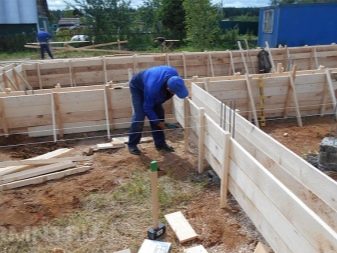
First, the material is cut into boards of equal length. Then they are attached with the help of beams, which are hammered into them from the side of the foundation. The same bars are attached at a distance of 20 cm from the side edges of the shield and every meter. Several bars are made longer at the bottom and their ends are sharpened so that you can stick the structure into the ground.
Instead of nails, you can make shields with self-tapping screws - this will be even stronger and do not need to be bent. Instead of boards, you can use sheets of OSB or plywood reinforced with metal corners on a timber frame. According to this algorithm, all other shields are made until the required number of elements is collected.
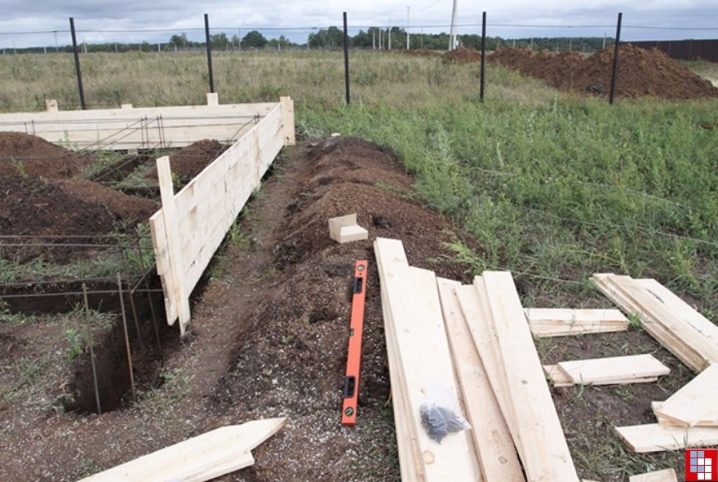
- Mounting. The very process of assembling the entire formwork begins with fixing the shields inside the trench by driving pointed beams into it. They need to be driven in until the bottom edge of the shield touches the ground. If such pointed bars are not made, then you will have to fix an additional base from the bar at the bottom of the trench and attach the shields to it.
With the help of a level, the shield is set in an even horizontal, for which it is knocked out with the blows of a hammer from the right sides. The vertical of the shield is also leveled. The following elements are mounted according to the marking of the first so that they all stand in the same plane.
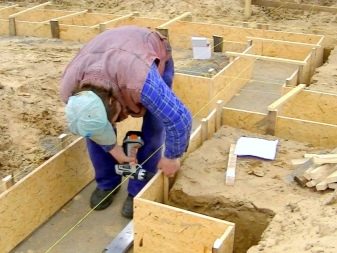
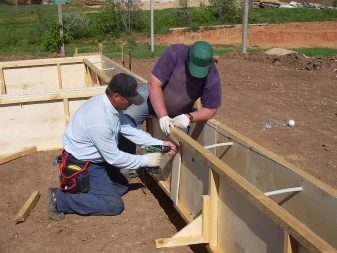
- Strengthening the structure. Before pouring the mortar into the formwork, it is necessary to fix all installed and verified elements into a single system both from the outside and from the inside. Through each meter, special supports are installed from the outside, and both sides of the structure are supported in the corners. If the formwork is more than two meters high, then the braces are installed in two rows.
In order for the opposite shields to be at a fixed distance, metal studs with threads from 8 to 12 mm thick are mounted on washers and nuts. Such pins in length should exceed the thickness of the future concrete tape by 10 centimeters - they are placed in two rows at a distance of 13-17 cm from the edges. Holes are drilled in the shields, a piece of plastic pipe is inserted and a hairpin is put through it, after which the nuts on both sides of it are tightened with a wrench. Upon completion of the strengthening of the structure, you can lay waterproofing, reinforcing ligature in it and pour the solution into it.


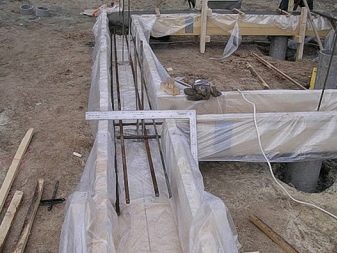
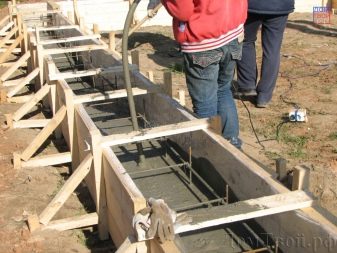
- Dismantling of the formwork. You can remove wooden panels only after the concrete has hardened enough - it depends on weather conditions and can take from 2 to 15 days. When the solution has reached at least half the strength, there is no need for additional retention.
First of all, all corner braces are unfastened, external supports and stakes are removed. Then you can start dismantling the shields. The nuts screwed over the studs are removed, the metal pins are removed, and the plastic tube itself remains in place. Shields with fastenings on nails are more difficult to remove than on self-tapping screws.
After the entire tree has been removed, it is necessary to carefully inspect the entire foundation strip for excess concrete or voids and eliminate them, and then leave it until it hardens and shrinks completely.

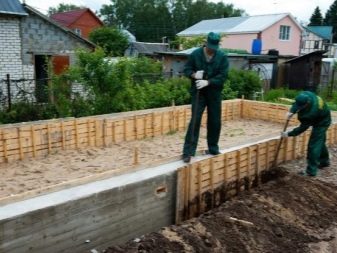
Advice
Although the independent production of removable wooden formwork for a concrete foundation strip is the best option in terms of price and quality, such a structure is not the cheapest purchase at all stages of construction, since with a large foundation depth, the material consumption for it is very high. There is an opportunity to save some money, not pouring the entire foundation at once, but in parts.
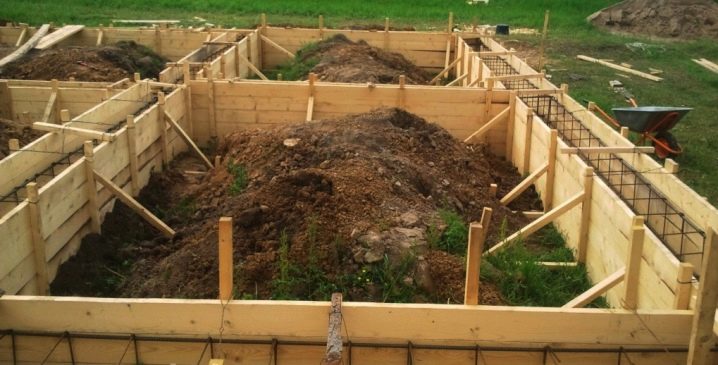
Fill with layers
With a foundation depth greater than 1.5 meters, the pouring can be divided into 2 or even 3 stages. A low formwork is placed at the bottom of the trench, and concrete is poured to the maximum possible height. After a few hours (6-8 - depending on the weather), it is necessary to remove the top layer of the solution, in which the cement milk that has risen up will prevail.The surface of the concrete must be rough - this will improve adhesion to the next layer. After a few days, the formwork is removed and placed higher, after which the whole procedure is repeated.
When pouring the second and third layers, the formwork should slightly grab the already solidified layer along the upper edge. Since in this way there are no breaks in the foundation in length, this will not affect its strength in any way.
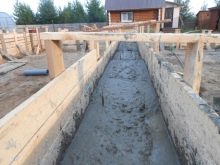
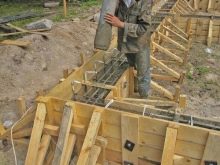
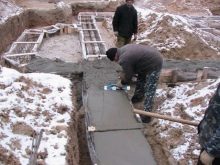
Vertical fill
With this method, the foundation is divided into several parts, the joints of which are separated by a certain distance. In one of the parts, a formwork section with closed ends is installed, and the reinforcement rods must extend beyond the side plugs. After the concrete hardens and the formwork is removed, the next section of the tie will be tied to such reinforcing protrusions. The formwork is disassembled and installed on the next section, which at one end adjoins the finished part of the foundation. At the junction with semi-hardened concrete, the side plug is not needed on the formwork.
Another way to save money is to reuse the timber from the removable formwork for household needs. So that it is not saturated with cement mortar and does not turn into an indestructible monolith, the inner side of such a formwork can be covered with dense polyethylene. This formwork also makes the surface of the foundation tape almost mirror-like.
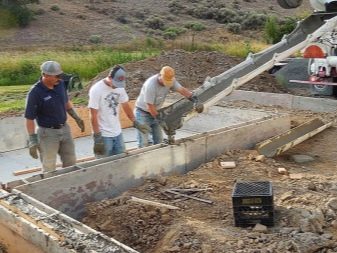
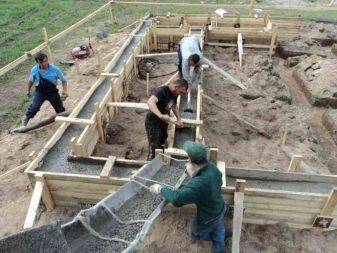
In order to avoid mistakes during the first experience in the manufacture and installation of formwork on our own, it is necessary to choose suitable materials and fix all the elements well.
A properly erected structure will create a solid foundation that will last for many decades.
For information on how to make a formwork for a strip foundation, see the next video.
The comment was sent successfully.