Building a foundation: step-by-step instructions for making your own hands
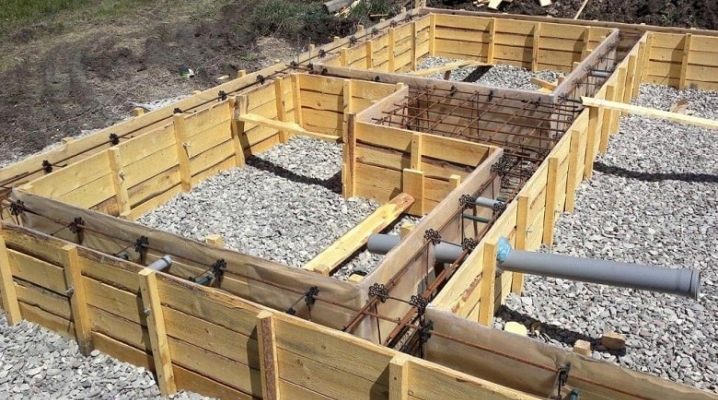
The construction of any house, bathhouse or even just a barn always begins with the preparation of the foundation. But it is quite difficult to make it, there are many potential problems that every builder, be it a professional or an amateur, is obliged to eliminate. To begin with, it is worthwhile to understand what the base for the house actually represents.
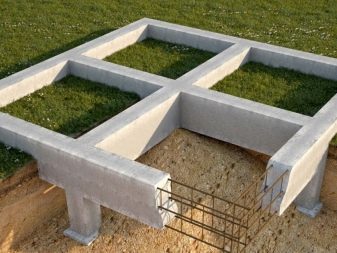
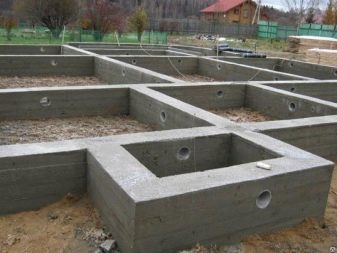
What it is?
The foundation is an underground, much less often the underwater part of any structure, which transmits static and dynamic stresses to the soil foundation. Correct design implies such a transfer of impulses in which it is impossible to exceed the shrinkage rates and accelerate the destruction of the house.
There are a number of techniques by which this effect is achieved:
- dispersal of the acting forces over a large territory;
- removal of soil to a solid mass;
- overcoming the loose layer in some places by means of piles;
- increasing the strength of the surface array.
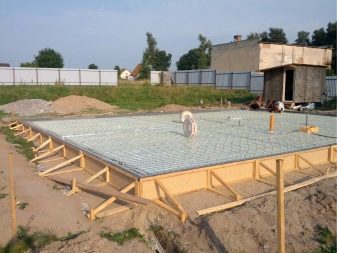
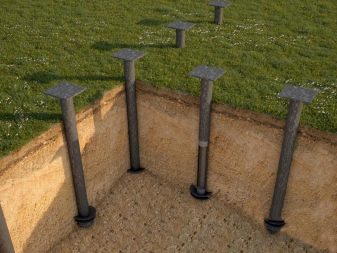
The easiest option is to build on completely rocky ground, there is no shrinkage, or it is too small. It is much more difficult to create and design foundations where the soil is characterized by increased compressibility. Even worse for architects and developers of areas with changing soil properties.
The type of substrate also determines the preferred options for the foundation for the house. The contact space is calculated based on the generated load and the predicted response from the ground.
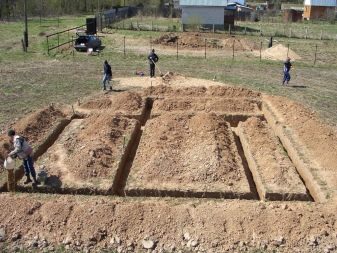
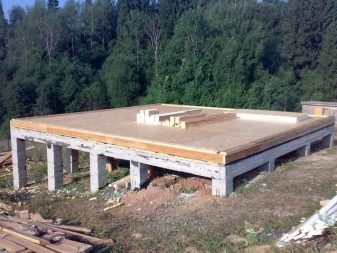
Varieties
In residential low-rise construction, a much smaller range of foundations is used than in the industrial sector. That is why it is possible and necessary to study each type as closely as possible in order to prevent errors from occurring. Along with strips and slabs of monolithic execution, glass-type bases were also in wide demand. The name is not accidental - the point structure takes over the excess load, then this force is distributed exactly where the pressure can be very high. Under large buildings of small height, it is the "glasses" that are mounted in many cases.
Important: do not take the name of this foundation literally. Geometrically, it most of all resembles steps in the form of trapezoids, the tops of which are narrower in comparison with the base.
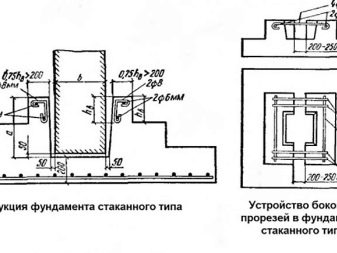
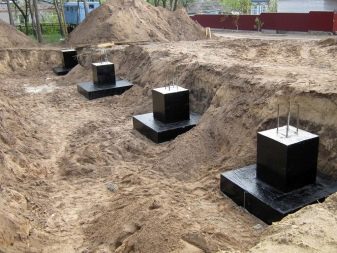
It should be noted that glasses should not stand under low-rise buildings in principle.
It is preferable to put them under:
- bridges thrown over water bodies;
- crossings and crossings over rail tracks;
- underground garages, parking lots;
- single-storey warehouses, sports, entertainment and trade establishments;
- workshops and ancillary facilities at energy enterprises.
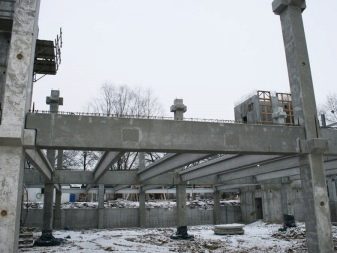
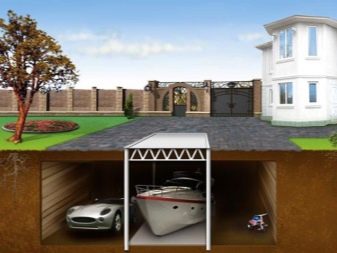
Glass foundations are formed strictly within the framework of the terms of reference and GOSTs, there can be no independent initiative here in principle. Determination of soil and material properties, drawing up a picture of geological layers is carried out through rigorous testing. For each specific case, design institutes develop special series of glass foundations, the features of which are fixed as strictly as possible.
The key building blocks are:
- the slab, which plays the role of a support, is installed on a cushion of sand and crushed stone that occupies the bottom of the pit;
- Column;
- podkolonnik, it just looks like a glass most of all;
- a concrete pillar holding the support beams under the walls.
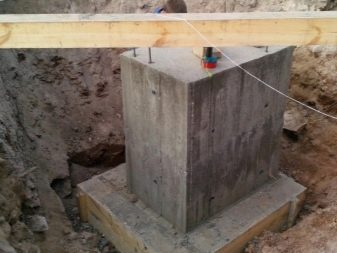
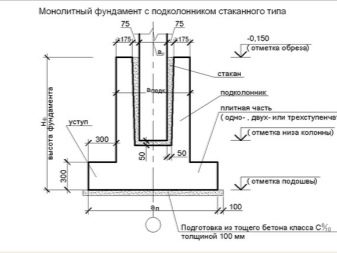
A heavy reinforced "glass" is made point-like, and therefore the load on the ground is minimal. The speed of work impresses even those familiar with construction. Moreover, the need for special machines when lifting heavy parts does not negatively affect the turnaround time. Low contact with the ground minimizes water absorption. The glass is very good under buildings of considerable size, but under a private house it does not justify itself.
A glass foundation cannot be made if the surface is not properly cleaned to a perfectly even state. It is forbidden to lay a slab above 1 m. During the work, the geometry is constantly monitored using levels and levels. After delivery to the construction site, the glasses are cleaned of any debris; they are lifted and installed using a crane. You need to work slowly, carefully checking the positions of the marks.
The thread mesh will help tie the individual elements together. The extracted soil cannot be taken out, it will be useful for backfilling the excavation to the top of the mounted block. Next, they put the support beams on the glasses themselves or on the posts.
The use of wedges under the columns of industrial buildings is strictly mandatory. In private and individual construction, the "floating" type of foundation has a certain value.
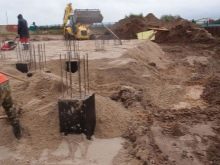
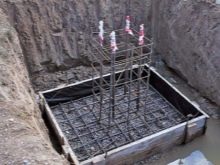
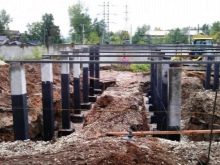
Of course, no liquid should be in or around it. On the contrary, the structure being created is a rigid, reinforced concrete slab located under the entire volume of the future house. "Swimming" is reduced to the adaptation of the support to the arising loads. This solution almost does not change under the action of ground movements, unlike metal pipes (piles), they are not deformed by the forces of cold heaving. In most cases, slabs 25-30 cm thick are used, under which there is a layer of sand and gravel of comparable dimensions.
A serious problem with any floating base is the significant consumption of building materials. It is impossible to fill the slab where the territory has at least a slope different from the measurement error. And even in the most favorable cases, it is not possible to organize a basement or basement room. Requirements for communications are becoming more stringent, their wiring and planning are becoming a filigree art. Moreover, if errors with the infrastructure are made, the complexity and cost of correcting them is unacceptably high.
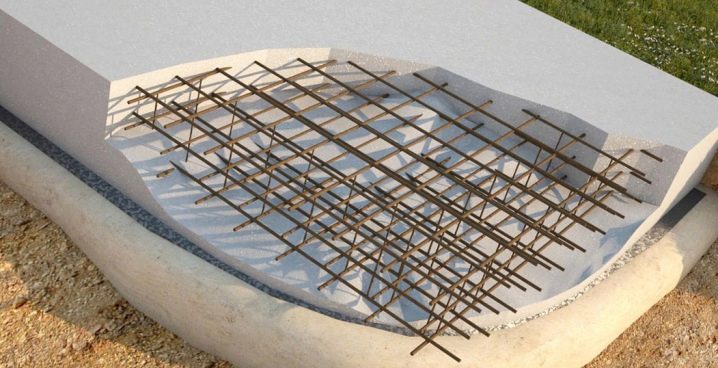
Materials (edit)
Much when choosing the type of foundation and its optimal organization depends on the type of building materials used at the top. For example, a brick wall is heavier than a comparable (or even slightly large) wooden structure, so you will need to create a strong, stable base under it. A building with a deep laying of a support is recognized by most specialists as the most reliable and stable, but the complexity of preparing such an element makes it acceptable only for a large brick house.
In addition to concrete strips, three types of piles are often installed:
- bored;
- screw;
- clogged.
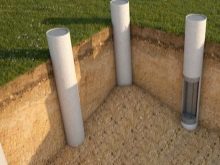
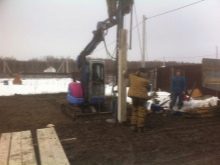
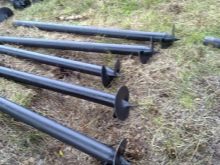
Even without special geological and geophysical studies, it is obvious that the properties of the soil in different places are not the same. Its composition and mechanical parameters directly affect the choice of the optimal and acceptable type of material.
It is also worth taking into account the freezing zone, the characteristics of the aboveground structure, the climate, groundwater, the funds available to the developer.
- reinforced concrete;
- asbestos pipes;
- metal constructions.
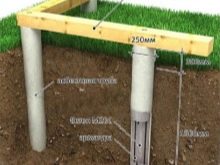
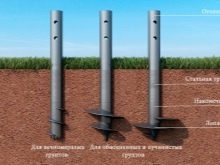
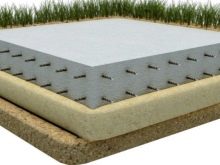
But wood, even especially durable and processed in accordance with all the rules of protection, cannot be recognized as a completely effective solution. In most cases, independent developers choose reinforced concrete because this material is versatile and suitable for all known types of soils.It can be prepared using cement, sand of various fractions, crushed stone and reinforcing rods. The installation of steel strips is done in the formwork, after their connection, mortar is poured inside.
Changing the proportions of its components, consistency and adding special additives, you can flexibly adjust the properties of the finished casting.
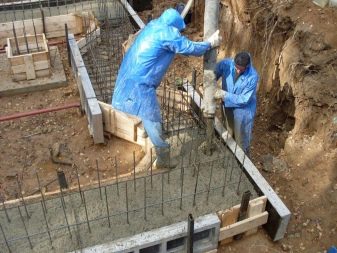
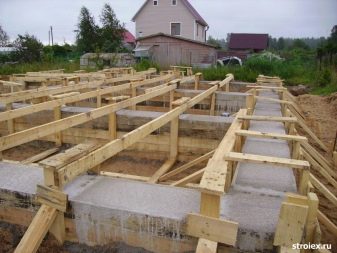
When erecting a building on solid soil, composed of stone rocks, natural stone and light grades of rubble concrete can be used for laying the foundation. The same materials are recommended for use on most soils that are not heaving in winter. But it should be noted that adherence to the work methodology becomes critical. The irregularity of the contours of natural stones makes it difficult for them to densely and homogenously lay out. It is very difficult to correct the discovered deficiencies; for this, it is almost always necessary to call in lifting equipment.

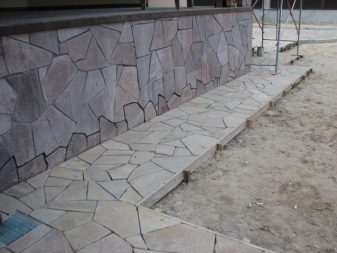
Therefore, simple concrete is much more often chosen (even without reinforcing reinforcing inserts). As a binder, in addition to cement, sometimes polymers of a special composition and a combination of silica with lime are used for the production of concrete. But the last type, which makes it possible to make silicate concrete, shows itself very poorly where the soil is abundantly saturated with moisture or prone to freezing to a great depth.
Instead of pouring it yourself, it is allowed to install ready-made blocks, but this is a less accurate and reliable method. Industrial semi-finished products are needed for pole and strip foundations.
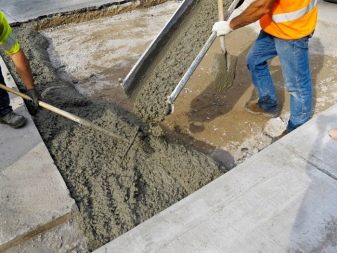
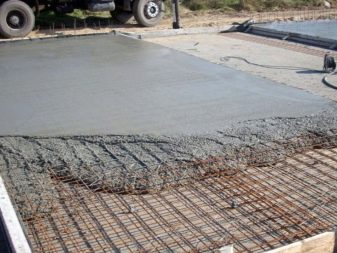
Of course, great attention should be paid to the sand. In addition to being a part of the concrete solution, it is "marked" in one more role - the underlying cushion. It is recommended to create such pads if the rocks below are loose and by themselves will not tolerate the created load. Both cases, when sand is used in the construction of the foundation, require mainly its quarry variety with a large fraction. As reinforcement, special rods are used, the geometry of which is designed for ideal adhesion to the concrete mass.
The tree is used in the form of supports, in formwork structures. The cheapness and availability of this material do not allow, unfortunately, to ignore its main problem, that is, a short period of operation. When choosing a natural stone, one should carefully understand not only its characteristics and cost, but also transportation costs. Quarry stone is cheaper and more practical than granite or sandstone, it can be obtained without excessive costs. Expanded clay is traditionally used to insulate foundations, but it makes sense to think about other, more modern and practical insulating materials.
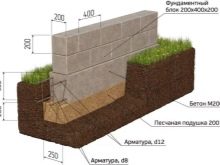
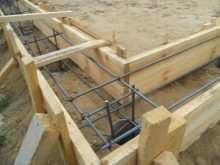

Peculiarities
The construction of a particular foundation depends to a very large extent on the type to which it belongs. For low-rise private buildings, the whole range of classical foundations and their combinations are characteristic. Plates are invariably cast only inside the formwork; they cannot be used on a steep slope and on subsiding ground. The assembly of pillars from concrete racks and glasses does not exhaust all possible options; it is quite possible to pour the solution into a tubular or shield formwork. Such formwork is distinguished by an especially wide lower part, but its bearing capacity is less than that of piles.
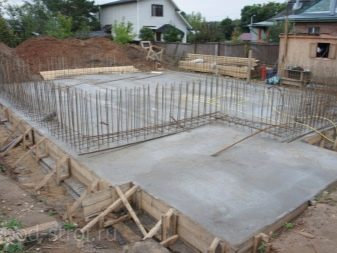
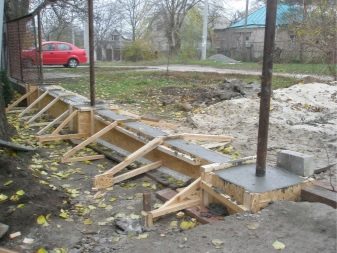
The strip base can be assembled from FBS foundation blocks, laid out of rubble, decorated with bricks, or poured into the formwork.
If the soil is prone to heaving, the tape requires:
- drainage works;
- backfilling of nonmetallic materials;
- thermal protection of the most problematic parts of the structure.
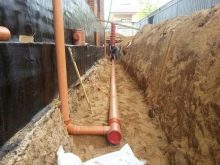
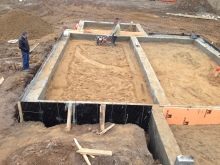
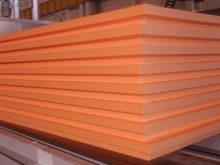
As for piles, each of their subspecies has specificity. So, the bored execution manifests itself well in areas with difficult terrain or with weak soil. But at the same time, the lack of waterproofing makes it impossible to use such supports with an average and high level of soil water.The screw supports have no technological limitations, however, it is recommended to use them only under wooden buildings.
All pile and pillar foundations are supposed to be equipped with a grillage, it can be made in various ways, but in any case it is intended to become a support for the walls and increase spatial rigidity. Under the stairs located in the house, emergency power generators, stoves, capital fireplaces, and so on, it is required to organize autonomous foundations.
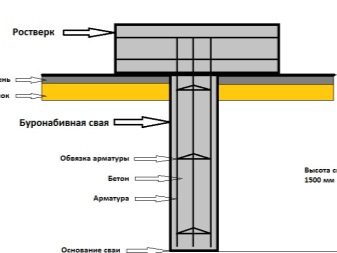
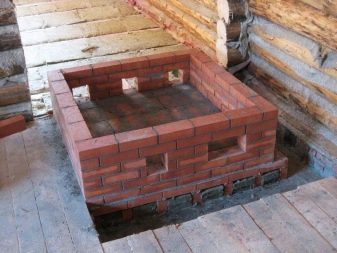
When an extension is being constructed, it is advisable to give preference to pile and pole solutions. Whether these or some other types of foundations are chosen, it is very important to leave a technological gap between the primary and secondary foundations.
For your information: roofing block rafter systems must also be autonomous. The pillar system is attractive for its exceptional simplicity and the ability to carry out almost all work without help. The post is supposed to be poured in one go.
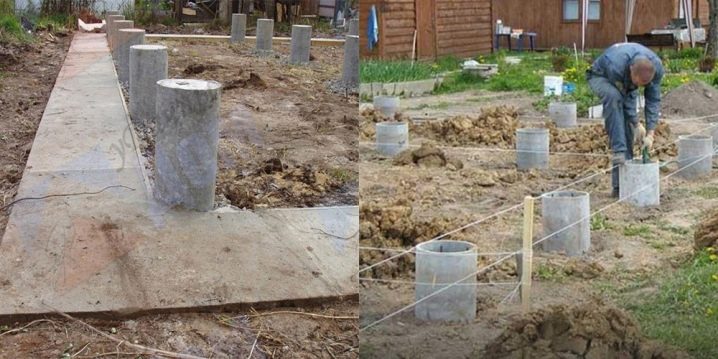
The constituent structures of the foundation assembled from the pillars are:
- slabs 0.3 m thick;
- reinforced concrete racks;
- reinforcing vertical frame;
- grillage from various materials.
With all the advantages, the pillar option will not cope with the load from heavy walls. It will work poorly on wet soil, on soil prone to subsidence and sliding. This approach is not recommended where steep slopes are present. But heaving is not too dangerous, a typical set of measures to prevent it is quite enough.
Pillars are better than piles in the sense that they allow for additional formwork and waterproofing after construction is completed.
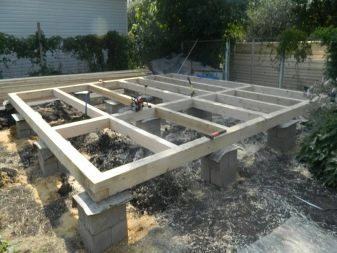
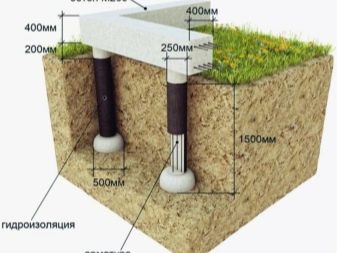
Private developers appreciate shallow strip foundations. It is much more difficult to equip them than any pillars. For reinforcement, frames are used, the mating points of which are reinforced with anchors. To make the outer concrete layer last longer, spacers and side rings are used.
Additional cover is provided by:
- waterproofing layer;
- insulation materials on the outer edge;
- blind area (preventing swelling);
- non-metallic materials (for the same purpose);
- backfilling of trench sinuses (so that the tape does not pull out to the surface).
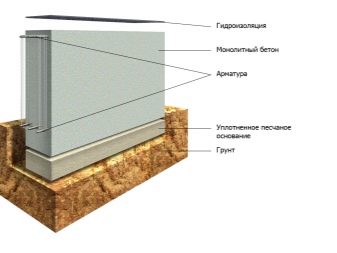
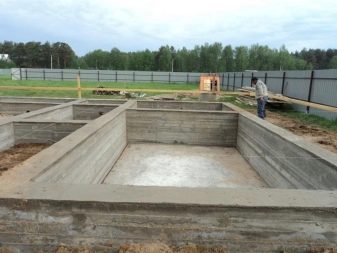
It is necessary to deepen the tape only in the presence of basement floors. In any case, it is not applicable to subsiding and wet soils. If construction is carried out on a slope, stepped concreting often helps, but even this does not allow you to confidently mount heavy walls. The undoubted advantage of the tape is the convenience of working with the points of entry of engineering communications and the absence of prohibitions on the height of the house. The floors can be built on the ground, it is also permissible to install floors on beams. In the most difficult cases where tape, posts and piles are ineffective, it is recommended to use slabs.
It should be noted that even this very reliable technology has objective limits. If the soil has low resistance, the slab base may sag. Under the influence of the heaving forces arising on the overhanging slope, the block can move to the side. The floating slab has an identical perimeter thickness and requires a significant consumption of building materials.
The ribbed option allows you to reduce the thickness of the central area; there are also solutions with built-in underfloor heating and with a blank for the cellar.
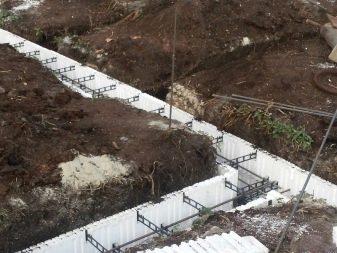
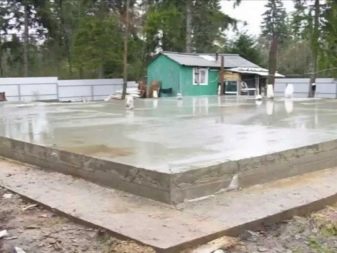
Regardless of the option used, all foundations must have air vents. The underground continuously accumulates moisture that evaporates from the ground. Water vapor is very dangerous for any building structure, for any finishing material. Increased attention should be paid to wooden buildings and all kinds of houses in areas where radon accumulation is likely. The lack of freezing of the soil makes moisture seep into the underground even in winter.
If you do not take care of air vents, water will collect and freeze on various parts of the foundation, on the back of the floors of the first floors. SNiP stipulates that even in ideal cases, the total area of the ventilation ducts should be at least 0.25% of the basement or technical subfloor space. And when work is carried out in areas with an increased level of radon concentration, this figure is increased by 2-3 times. Additionally, it is worth considering that equip airflows less than 0.05 sq. m just makes no sense. Their limiting value is 0.85 sq. m, since if this size is exceeded, the structure will have to be carefully reinforced.
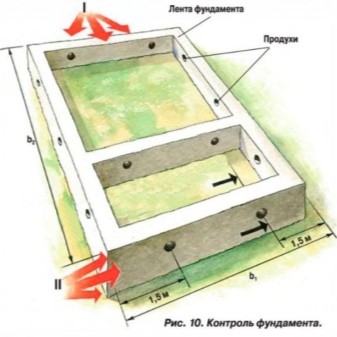
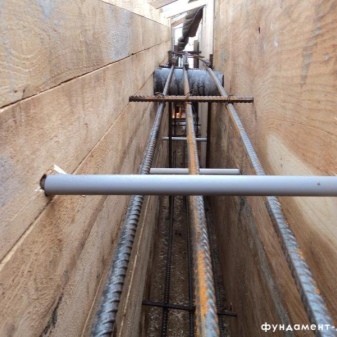
What form to make the air is - the owners of the houses decide themselves. Most often, a rectangle is chosen, this configuration is not only simple, but also the most aesthetic in appearance. But the location of the holes on the outside should be uniform in area. It is possible to exclude the formation of "bags" without ventilation if the air vents are not removed from the corners by more than 90 cm (measurements are taken along the inner edges). The most effective solution is symmetric placement of an even number of holes.
How high to put the air vents is determined in accordance with the height of the first floor above the ground. But their lower point should not be closer to the ground than 20-30 cm. If you do not follow this rule, you can run into the bay of the underground in the spring and autumn months.
Important: when the house is equipped with internal load-bearing walls, air vents should be made for each underground space. If the calculations indicate an unnecessarily large number of holes, which can weaken the structure of the foundation, this problem must be circumvented by increasing the size of the individual channel.
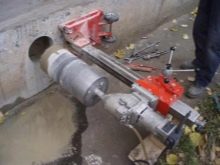
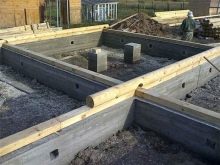
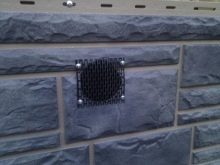
In addition to ventilation, the rational arrangement of the foundation also implies backfilling. Houses of permanent residence, heated year-round, do not allow freezing of the underlying soils. Therefore, under such buildings, it is allowed to use any type of dumping, even from clay. Projects in which it is planned to carry out overlapping on beams, it is recommended to fill it up from the inside with clay as the cheapest material. The sand will have to be used under floating floors in the form of a layer of at least 100 mm.
Significant volumes of construction work make it quite justified to backfill with soil from the building spot, taken out of the trenches. Only the upper part can be covered with sand to fill the foundation. In areas with a high standing groundwater, crushed stone is used. If the aquifer is relatively deep, it is allowed to save money using sand.
For your information - the organization of external clay locks described in the building codes of outdated editions is now prohibited.
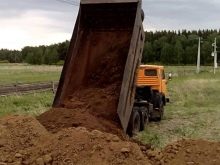
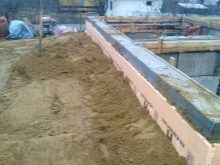
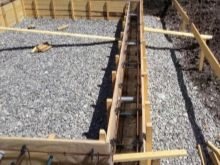
Compaction of the backfilled soil is obligatory every 0.2 m. The presence of large stones (over 0.25 m in size) in the backfill is unacceptable. Drainage, if necessary, is formed in the form of longitudinal channels connected to a single circuit, standing along the entire perimeter of the building. It is necessary to cover the foundation with non-metallic materials at different depths. So, with occasional heating of the house, 0.2 m of sand is enough next to the inner walls.
If there is no heating, and the soil can freeze by 100 cm, it is required to form a 200 mm sinus, saturated with inert materials. But when the freezing depth reaches 2 m, you will have to put 50 cm of a protective layer.
Important: it is customary to count this backfill depth from the planning marks, most often from the blind area. It cannot exceed ¾ of the groove of the soles of the tapes. Only when forming overlaps along the logs is it allowed not to compact the filled materials, in all other cases this is extremely important.
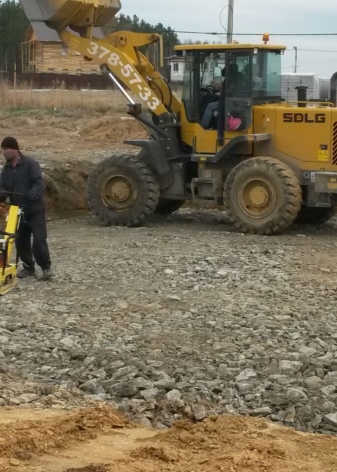
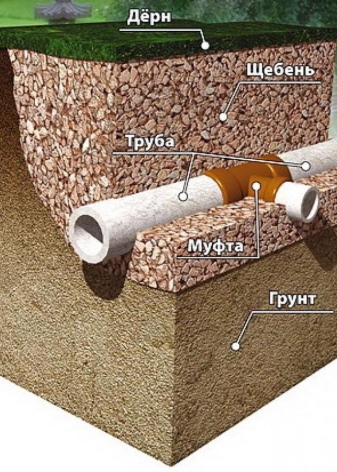
Under the screed, it is always necessary to compact the backfill to a level of 0.95 m. Finish the rammer, whether in manual or mechanized mode, after leaving a mark on the ground.Watering sand, loam and sandy loam is impractical, this can lead to excessive saturation of soil horizons with water. Heavy soil can be moistened to no more than 23%, and light sandy loam to a maximum of 14%. In any case, it is unacceptable to mount the screed before the soil is completely dry.
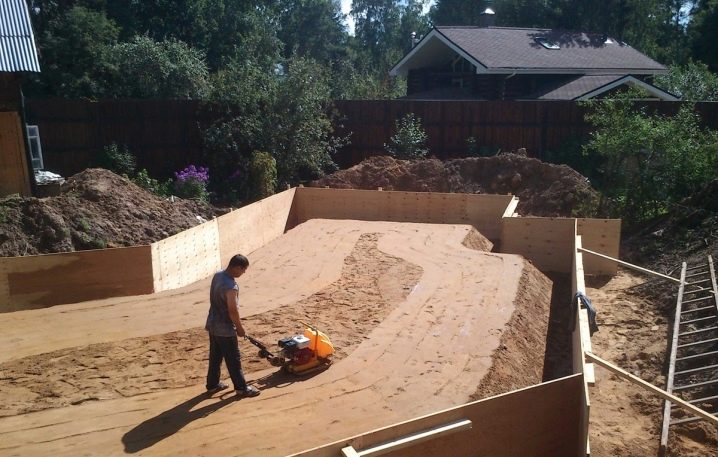
The concrete must be used under all monolithic foundations.
Her role is threefold:
- reducing the height of protective layers;
- exclusion of cement laitance breakthrough into the lower layers;
- covering the waterproofing of the foundation sole.
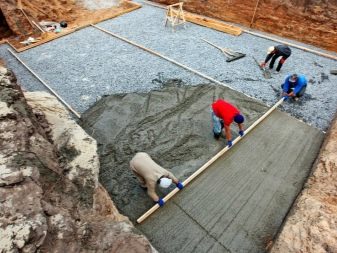
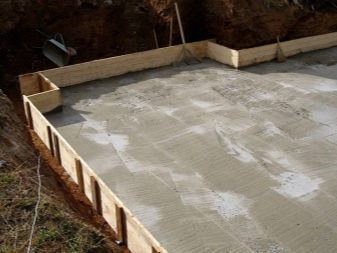
The soil along the outer edges of the foundation is not protected by anything from the cold. This means that it will swell, and not uniformly throughout the volume, and there will be a force that pulls the concrete base up. There are three main options for solving this problem, one of which is just backfilling. You can also insulate the blind area by forming a tape 0.6-1.2 m wide around the entire house. Another way is to create a slip-crush insulation.
Its essence is that rigidly dense extruded polystyrene foam is attached to the outer walls. Further, the base, fixed in the ground, is covered with a couple of layers of polyethylene. Sheets PSB-25 are mounted, they must be placed strictly vertically and tightly pressed against the wall. Sand powder will be able to hold these sheets, so additional fastening is not required. The heaving forces invariably crush the polystyrene, but its rise along the smoothed film layer does not damage the key level of thermal protection.
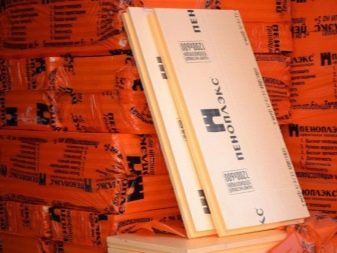
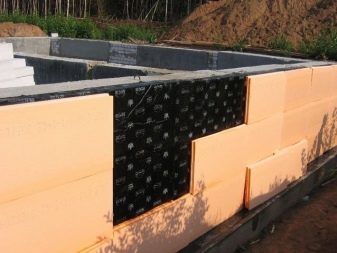
Returning to the sole under the foundation, it is worth noting that most often it is twice the width of the base itself. In order to support the sole throughout its entire length, the so-called footing is equipped (the other functions of which have already been discussed). In industrialized countries, this support structure is prescribed by all building standards and technology codes. Double rechecking of all distances between landmarks placed by surveyors helps to eliminate errors. Only then are all the alignment lines shown with cords.
Crushed stone concrete allows you to save on construction work. The thickness of the layer to be created cannot be less than 200 mm. But the problem may be related to the low rigidity of the formed substrate. Therefore, it makes no sense to fill up crushed stone under the foundations of serious, responsible buildings. But under the household blocks, sheds, such a decision fully justifies itself.
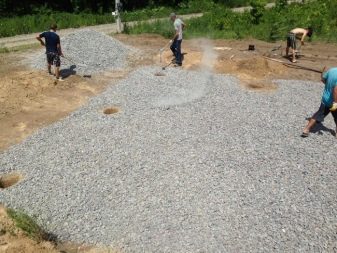
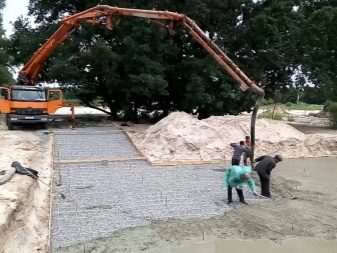
The concrete preparation layer is widely used under slabs and belts. In addition to the increased bearing capacity, this is also due to the convenience of organizing these types of foundations on rigid underlying surfaces. This advantage is especially important in the winter months, when the characteristics of the soil deteriorate sharply.
According to standard rules, preliminary concreting is performed strictly with mortars from M-350 and higher.
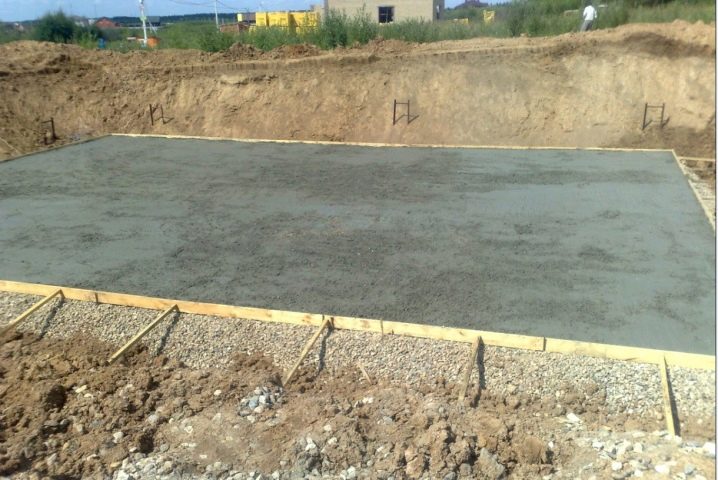
How to choose?
No matter how carefully the footing and drainage are made, if the type of the main foundation is chosen incorrectly, all these works and structures will turn out to be almost useless. When the construction site is built up of easily moving wet clay or dusty sand prone to deep freezing, you should not choose a strip foundation. As soon as spring comes, frosty heaving will be replaced by sinking. This will inevitably lead to cracks and even faults. Worst of all, even an immediate repair in accordance with all the rules with the use of adequate tools and materials will already be powerless.
But if there are no such problems with soils, the tape has a clear advantage - accelerated installation even without the help of professionals. Therefore, it is she who is recommended to be considered primarily for a residential building, courtyard buildings and baths.A monolithic strip foundation made of concrete can work up to 150 years, and at the same time everyone can mount it, even without spending money on renting powerful construction machines. The tape is very expensive and cannot be mounted during the colder months.
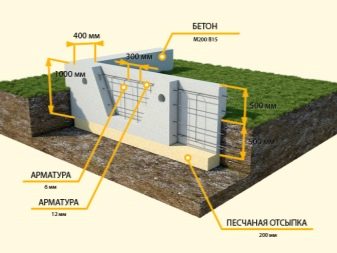
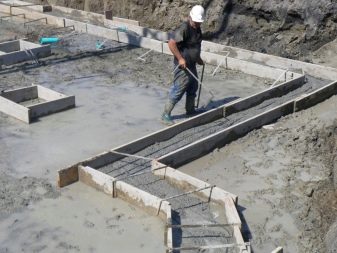
Problematic soils, which are encountered quite often, especially in areas of new development, are easy to "defeat" using the slab. The speed of its installation at the same level of preparation is the same as that of the strip base. Slab substrates are confidently poured in 1-2 months on their own. More precisely, pouring is faster, but it takes a lot of time for the mixture to harden. During the ascent and descent, the structures on the slab move uniformly, and this eliminates the risk of their destruction.
The monolithic structure can be mounted both on the surface and with some deepening; the benefits are canceled out by the significantly increased costs.
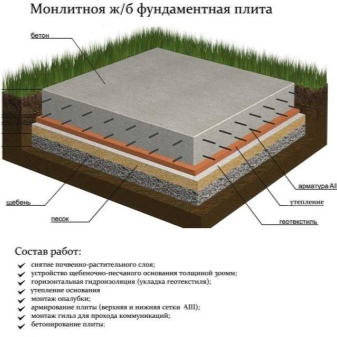
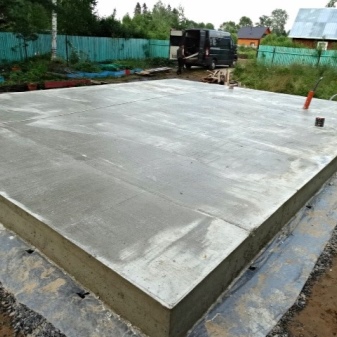
The solution to the problem of complex soil is also possible due to piles. Their bored type is mounted exclusively with the help of special equipment, and it is very diverse - you will need concrete pumping systems, and forklifts, and boring devices. If you plan to equip a clay castle around the pile supports, you will have to supply it with special pumps. Of course, the use of a whole fleet of machines and the involvement of several professionals significantly increases the cost of construction work.
If the goal is to reduce costs and labor intensity, screw designs can be used.
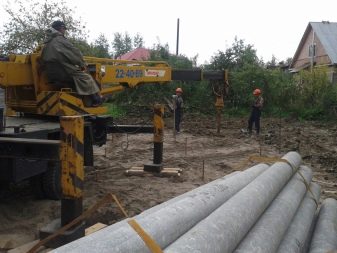
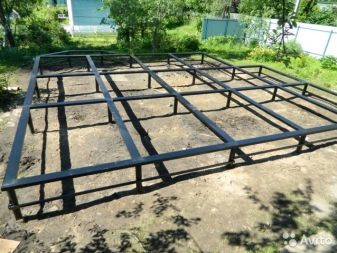
Calculations
The foundation drawing is prepared only after all the necessary calculations, calculations of linear and strength parameters have been completed. The detail images are written separately, the general scales are from 1: 100 to 1: 400. To transfer the scheme to the terrain was easier, use the axial markings. It is imperative to note in the documentation the gap from the extreme to the center axes. Another essential element of any well-thought-out scheme is the coordinate grid.
During the calculations, parameters are calculated such as:
- the degree of penetration into the soil;
- section geometry;
- width of the belt supports;
- diameter and internal thickness of piles.
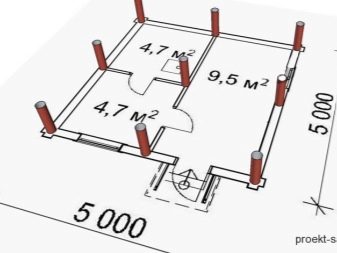
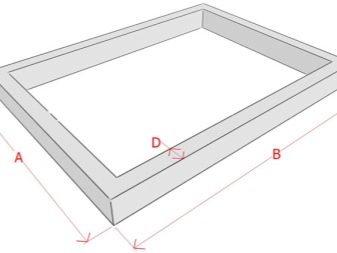
What is important, based on the results of well-conducted calculations, it becomes clear which types and brands of building materials should be applied in a particular case. Experienced developers always lay down a certain reserve for all indicators related to strength and sustainability. Even if it is not used immediately, it will at least help correct errors, offset the effects of increased loads over time, and postpone critical wear and tear of the structure.
The drawing should show what type of footing is used and how it is organized. Demonstration of the points of entry of engineering systems and a description of their technical capabilities are no less significant.
The sections should show:
- outer contours of the support blocks;
- blind area (for external walls);
- means of protection against water;
- the size of the ledges, if the foundation or its parts are mounted non-uniformly in height.
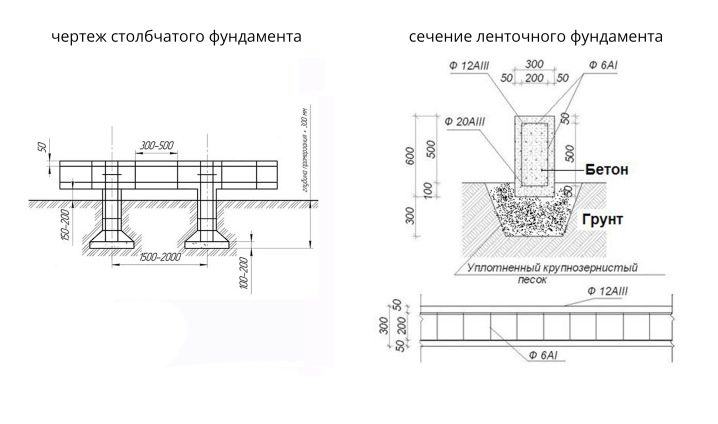
The strip bases are drawn with the indication of the levels, it is possible to increase the visibility of such marks by applying marks with a turn to the side of a specific section. For the zero mark on any foundation scheme, take the plane of the floors of the first floor. Additionally, they demonstrate the surface of the soil, the line of the base of the foundation and cuts. The point of the ribbon section on the main plan is marked with broken strokes and arrows showing the direction. To perform the sections, the scales are selected 1: 20, 1: 25 and 1: 50.
Professional builders, preparing drawings, add to them a general specification of all parts under the zero mark, a table of loads, assembly plans for prefabricated supports and a list of additional notes. Piles are placed under the outer walls along the entire perimeter, and the inner load-bearing walls are placed on supports. The gap from one support to another, in whatever direction the reading is taken, can be a maximum of 3 m.
If you plan to create a grillage, a separate scheme of such a design is created. Together with it, specifications or explanatory notes on the materials are prepared.
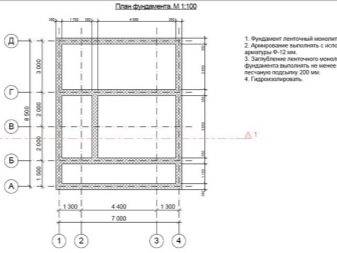
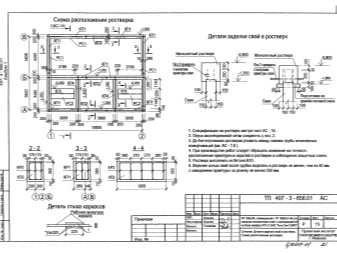
The height of the foundation increases if it is planned to form a basement. Accurate information about its value can be gleaned from building codes and regulations. In any case, the base should rise by 100 mm above the calculated level of the maximum predicted snow mass. The tapes, even in places where there is no or very little snow, should have a height of 0.3 m. The distance to the sewer is reflected in the transverse street profile, it is coordinated with the placement of other underground infrastructure.
To lay communications as correctly as possible, one should not forget about considerations of convenience when laying out, examining and repairing networks. It is also recommended to take into account the need to protect adjacent pipelines, to distance cables from each other. Another consideration is maintaining the safety of foundations and underground facilities, ensuring the tightness of water supply networks.
Pressure pipelines should be located 5 m from the base of the house, and non-pressure ones - at least 3 m.If it is necessary to cross the water supply and sewerage routes, the drainage channel should be located lower.
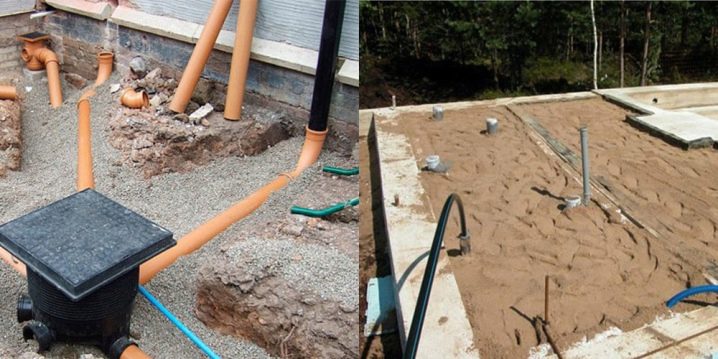
Construction stages
The construction of a private house with your own hands at the stage of foundation work breaks down, in turn, into a number of phases.
First of all, the type of suitable technology is found out, in which they start from:
- the general condition of the soil;
- freezing lines;
- standing height of ground fluids.
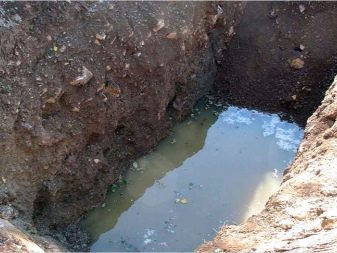
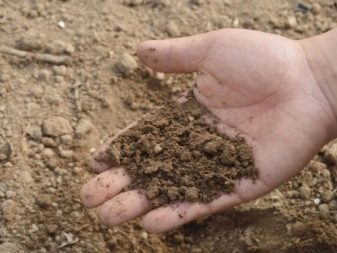
During the work, special reference books are used, but it is much more correct to do a full-fledged geological study. Regardless of the technical nuances, any step-by-step instruction provides for the installation of waterproofing and water drainage. Monolithic foundations are placed by pouring concrete mortar into the formwork.
The tapes are created by digging trenches, while their production is divided into the following stages:
- cleaning and compaction of the bottom of the pit;
- erection of a sand or gravel cushion;
- laying of hydraulic protection;
- checking the verticality of the walls;
- placement of reinforcing cages and filling the formwork with concrete;
- removal of formwork and external waterproofing.
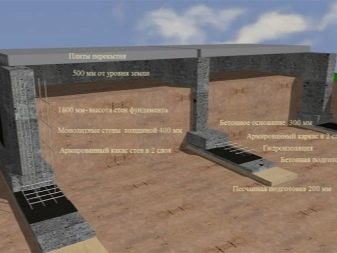
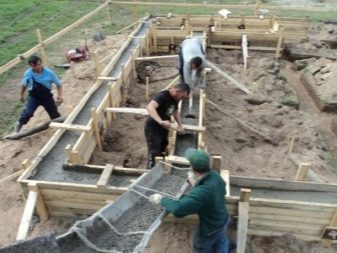
You will have to build a columnar foundation differently. The soil is taken to a depth of 100 to 300 mm, removing the bumps, filling the pits with soil. Horizontal lines are checked with building levels. The pillars are placed at the intersection points of the walls, these outline are used for digging holes and installing formwork. Then comes the turn of laying vertical reinforcement and pouring concrete into the formwork.
The pillars that have gained mechanical strength are covered with strapping. If small houses and outbuildings are being built, support pillars made of wood can be used. But it needs preparation through the use of antiseptic mixtures.
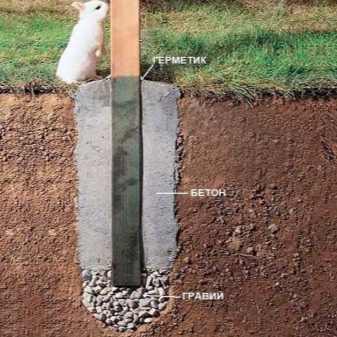
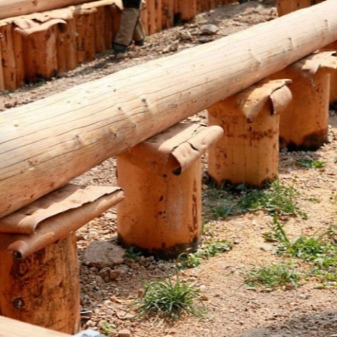
The formation of monolithic foundations also has its own characteristics. The first step in the work is a site carefully prepared and cleaned of dirt. It is possible to determine whether equipment is needed for work by the amount of construction work. It is correct to make a foundation pit of the same depth as the line for laying the foundation. The base of the trenches is supposed to be compacted, covered with sand and tamped, achieving the elimination of the slightest voids. A thin layer of concrete is poured over the sand mass, into which reinforcement is introduced and waterproofing is applied. On dry days, the surface is doused with water, and when precipitation falls, it is covered.
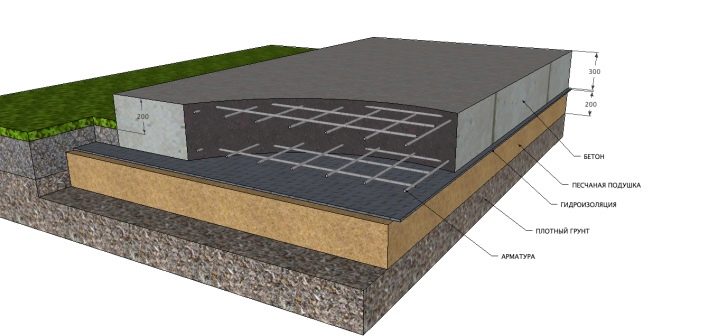
Pile foundations are of various types; residential buildings in areas with difficult terrain should be placed on screw piles. The diameter is calculated from the generated load. Stakes are driven in the selected places, the basting is used to obtain indentations. Screw supports are screwed in using pipe pieces or a specialized tool.
It is imperative to check whether the above-ground fragments of the piles coincide with each other, if necessary, the excess metal or concrete is cut off.
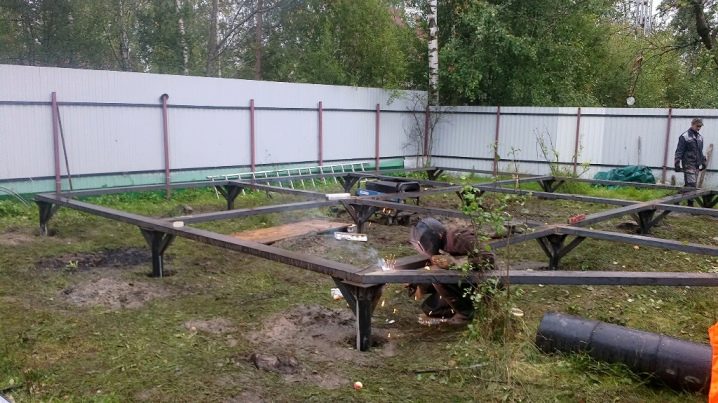
Tips & Tricks
It is recommended to make a strip foundation from concrete compositions of category B22.5. To get them, take 1 part of M-200 cement, 2 parts of coarse sand and 2.5 parts of gravel. Steel rods with a cross section of 0.8-1.2 cm should be used as reinforcement for it. The installation of a shallow tape is recommended for the construction of one-story houses on stable soils. A prerequisite for success is the location of the support above the freezing line of the earth.
To align all lines, you need to use a laser level; special attention is paid to checking the corners, the deviation in them is even worse than in the geometry of straight sections of the walls. A foundation with a width of less than 250 mm cannot be made under the bath and utility block; on heaving soils (muddy) and on sandy mass the minimum value is 500 mm. If a full-fledged house is being built on one floor, these parameters are 400 and 800 mm. The embedded part is designed to connect the blocks for the foundation to each other, but stairs, wall panels, and floor structures can also be attached to it. Any type of commercially available rolled metal can be used as embedded parts.
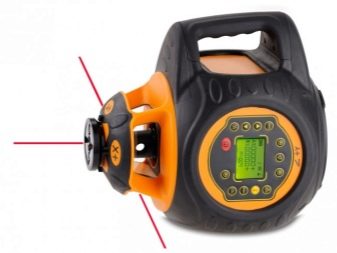
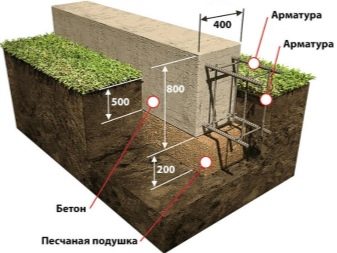
There are special technological methods that allow you to build a foundation on a site with a high water level. First of all, you should construct a drainage system, which alone allows you to avoid damage to building structures, their subsidence. Piles or precast concrete also protect from water, but they are very expensive and difficult to use. Particular attention should be paid to the base and the nuances of its execution. A reinforced concrete wall is optimally combined with piles, and a continuation of the outer surface of the foundation itself with a tape.
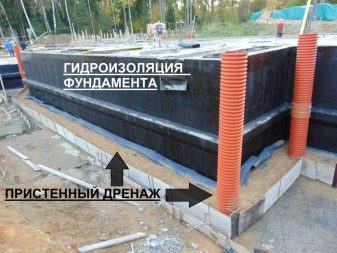
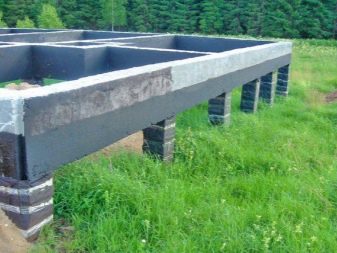
For the technology of creating a slab foundation from concrete, see the following video.
The comment was sent successfully.