Fiberglass reinforcement for the foundation: features and installation rules
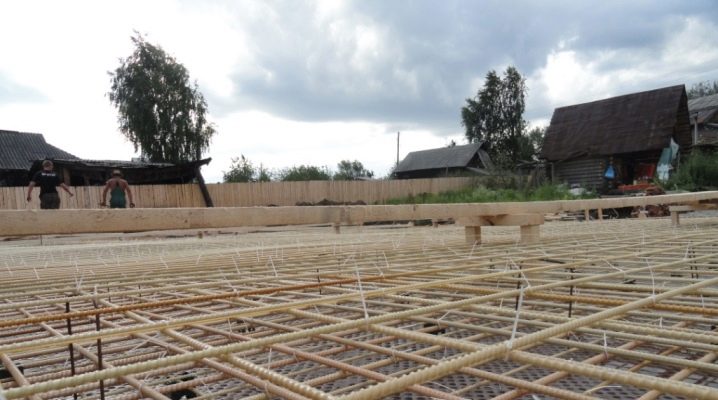
Every year, new materials appear on the construction market that differ from the old ones in any way. Fiberglass reinforcement is no exception. These products have a lot of advantages over the usual steel "skeletons".
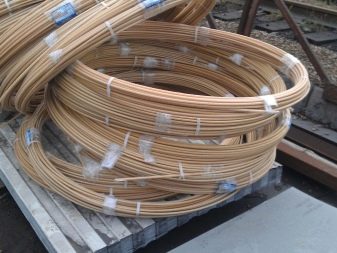
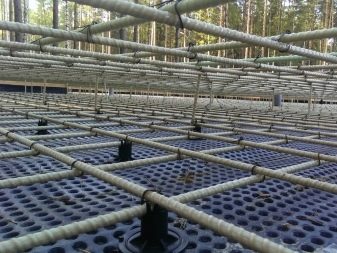
Specifications
Glass reinforcement appeared in the 1960s. Due to its high cost, it was used exclusively in the Far North, where metal structures were quickly corroded. Composite materials were used most often for the construction of bridge supports. Due to the rapid development of the chemical industry, the price of fiberglass reinforcement has dropped significantly. This made it possible to become an affordable product that manifests itself only on the good side in all building structures for various purposes.
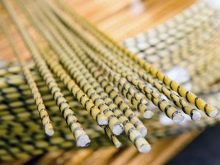
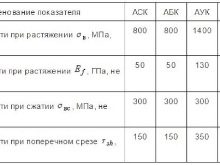
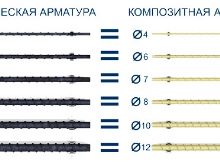
The wide popularity of glass reinforcement contributed to the development of GOST 31938-2012, where the requirements for the manufacture of fittings and the methods of their testing are indicated. In accordance with this state standard, composite fiberglass reinforcement is manufactured with a diameter of 0.4 to 3.2 cm. However, materials with a diameter of 0.6 are in great demand; 0.8 and 1 cm.
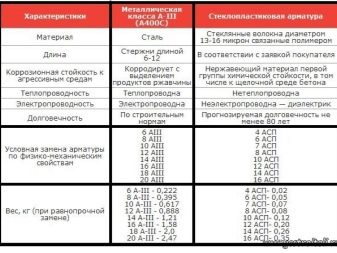
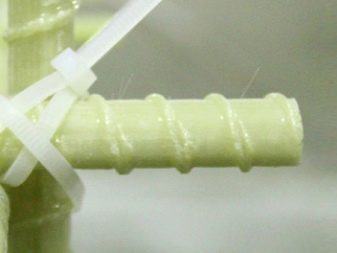
In the technical document, in addition to standards for the geometry and diameter of reinforcement, requirements for the outer surface of products are also indicated. On the surface of the reinforcement there should be no delamination, chips, dents and other defects.
Fiberglass material consists of high-strength rods of various diameters. They are made of composite material - fiberglass. They are mainly used in concrete structures, as well as for installation instead of iron reinforcement. Fiberglass is painted, decorated, covered with PVC films, and also lends itself to all types of mechanical processing. Depending on the reinforcing additive, glass composite, carbon composite and combined glass reinforcement are distinguished.
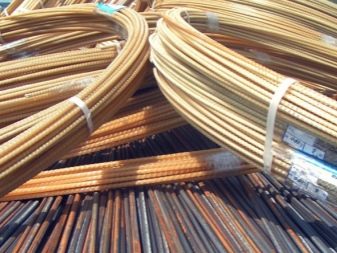
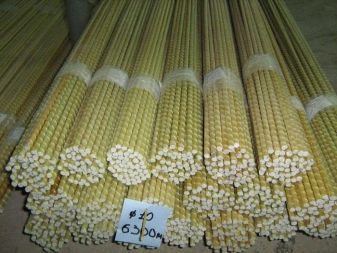
When choosing glass reinforcement for installation of the foundation of a structure, it is necessary to take into account such technical characteristics as:
- the upper temperature limit for the use of glass reinforcement is more than + 60 ° C;
- Ultimate tensile strength is the ratio of the applied power to the sectional area of the part. Fiberglass reinforcement has an ultimate strength of 900 MPa, and carbon composite - 1400 MPa;
- tensile elasticity for carbon composite materials is 3 times higher than for glass composite materials;
- ultimate strength during compression for any type of glass reinforcement should be above 300 MPa;
- the ultimate strength of the cross-section for glass reinforcement should be at least 150 MPa, and for carbon composite - at least 350 MPa.
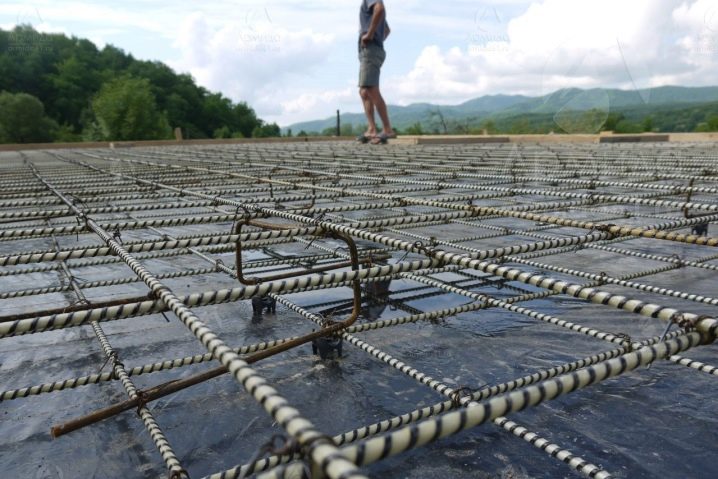
Advantages and disadvantages
The advantages of using composite polymer products are as follows:
- easy transportation due to the possibility of winding the material into coils;
- small costs during construction with your own hands, since materials can be picked up from the workshop on your own vehicle;
- small size allows you to do without a huge number of workers and trucks;
- resistance to corrosion. Fiberglass is not afraid of moisture or aggressive environments;
- lack of heat-conducting properties, since concrete structures must be covered with a layer of insulation for high thermal insulation - in order to avoid heat loss. For this reason, the poor heat conductivity of the composite has practically no effect on the quality of the structure;
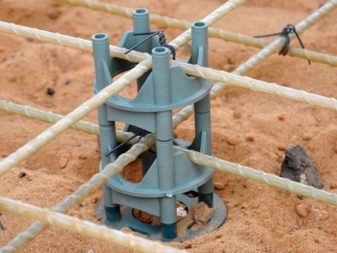
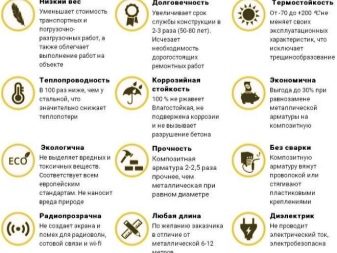
- dielectric properties ensure electrical safety;
- light weight allows you to reduce the cost of transportation and loading and loading processes, and also simplifies the strengthening of the foundation;
- high service life ensures the durability of the structure up to 3 times, which is equal to 50–80 years. In this case, there is no need to carry out expensive repair work;
- resistance to temperature extremes. Glass reinforcement withstands the temperature range from -70 to +200 degrees, so cracks will not appear on the surface of the product over time;
- environmental friendliness. Fiberglass reinforcement is completely safe in terms of toxicity. It complies with all European standards, and also does not harm the environment;
- radio transparency - no screen and no interference for radio waves, mobile communications and the Internet.
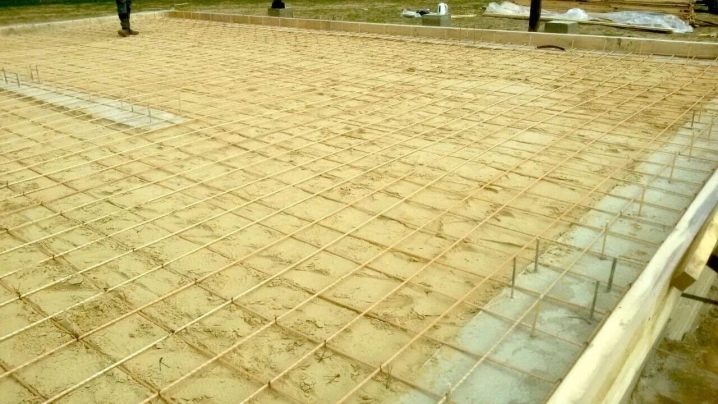
The use of a composite material has the following disadvantages:
- does not lend itself to bending, so you need to make diagrams for the manufacturer;
- it is impossible to use welding. For composite reinforcement, knitting is used;
- instability to temperature extremes. At a temperature of +600 degrees, steel loses its useful properties, and composite materials lose their bearing capacity even earlier.
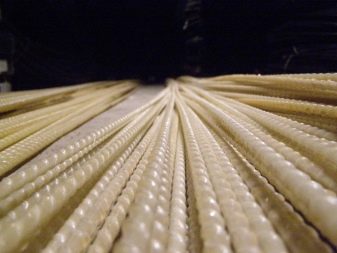
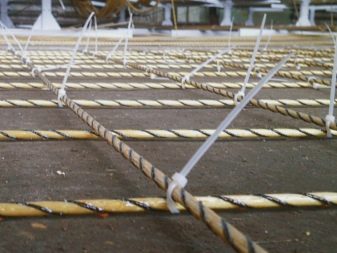
When comparing steel and fiberglass reinforcement, the latter will have more advantages, namely:
- resistance to corrosion, because they are not afraid of either acids or alkalis;
- low thermal conductivity, since glass reinforcement is made from polymer products. As a result, during the construction of foundations, there is no need for cold bridges;
- in comparison with steel reinforcement, fiberglass does not conduct electric current and does not form radio interference;
- iron products weigh up to 10 times more than fiberglass;
- the pricing policy for the two types of fittings practically does not differ, but it is much more convenient to use - fiberglass. On average, fiberglass products are 30% more expensive than metal ones, but manufacturers assure that the diameter of steel reinforcement is larger than that of fiberglass. For example, metal fittings with a diameter of 0.8 cm and a length of 1 meter cost 10 rubles, and fiberglass - 16 rubles. But at the same time, the diameter of fiberglass reinforcement can be taken not 0.8 cm, but 0.6 cm, but the price for 0.6 cm will be 10 rubles. And this means that when buying, you will get almost the same cost as when purchasing metal fittings;
- installation of fiberglass reinforcement usually does without seams, since they are produced in the form of rods up to 150 meters. When using iron reinforcement, the joints are considered the most unstable areas. And the use of fiberglass materials in the construction of foundations there are no unstable areas in the reinforcing base;
- another of the most important advantages of fiberglass is that the buyer can purchase the amount of material strictly according to need;
- transportation of fiberglass products is much easier than metal ones. Bars and coils with fiberglass reinforcement fit even in a passenger car;
- the thermal expansion parameter of fiberglass is practically the same as that of concrete, therefore, when reinforcing the foundation and concrete structures, various defects are not formed.
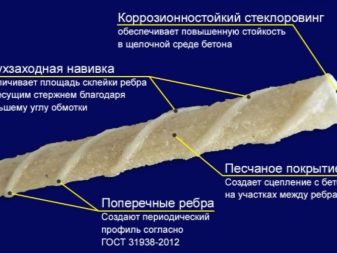
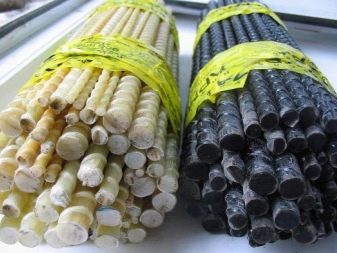
According to experts, fiberglass-type reinforcement really has the above positive and negative sides. However, its main task is to strengthen the foundation, and due to the low level of strength of the material, this is very difficult to achieve.
For this reason, most buyers prefer conventional fittings. Many also wonder how this material can be strengthened if it cannot be welded and twisted. Some builders use plastic bottles in order to reduce the price of foundations. As a result, such structures have not been destroyed for many decades. Most engineers have found the use of fiberglass reinforcement very effective, since it can significantly speed up the construction of any structure, which also reduces material costs.
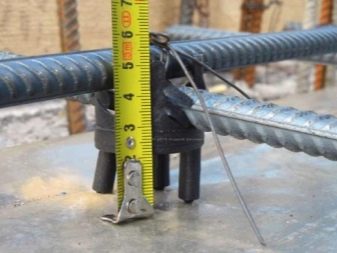
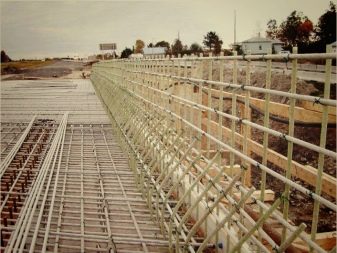
Scope of application
Fiberglass reinforcement has become widely used in the field of industrial construction, and in the construction of private houses has just begun to be introduced.
During the construction of cottage objects, composite materials are required for bank protection and reinforcement of the following elements:
- fences of concrete structures. But they are not used in supporting structures and floors;
- most types of foundations. The process of reinforcing tape-type foundations using fiberglass can do without the calculated part, since the product is light and resistant to harmful factors. But nevertheless, it must be used extremely carefully, especially for large building structures and foundations on heaving, subsiding soils and in soils with an increased content of groundwater;
- aerated concrete and foam concrete;
- roads with increased exposure to medium environmental factors;
- masonry. Antifreeze and other components are added to masonry mortars that impair the reliability of steel materials. Plastic composite reinforcement is not afraid of any additives.
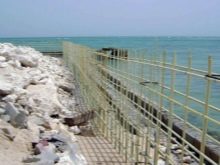
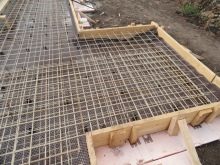
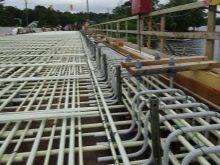
But when reinforcing masonry, the issue of using fiberglass reinforcement is controversial. Professionals say that when laying aerated concrete walls, glass reinforcement with a diameter of more than 0.6 cm should be used, and the corners should be reinforced with steel material. The result is a combination of two types of materials.
The use of glass reinforcement is justified only in the case when toughened requirements are imposed on resistance with regard to the effects of corrosion, thermal conductivity and conductive properties of reinforcing products.
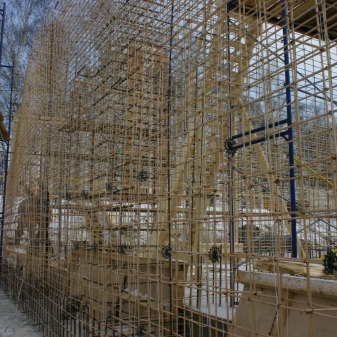
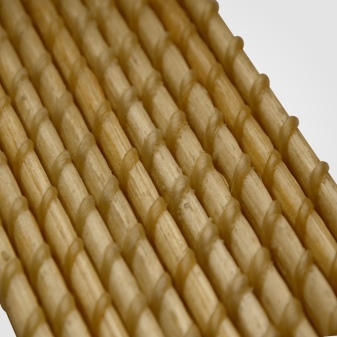
Reinforcement technology
When reinforcing various types of foundations, reinforcement rods with a diameter of 0.8 cm are used.
When doing DIY installation, you should adhere to the following sequence:
- when installing the formwork, its parts are wrapped in parchment paper so that they can be used several times;
- using a horizontal level, markings are made on the details of the formwork, to which the concrete solution will be poured. This is necessary for even distribution of the concrete composition along the entire perimeter of the foundation;
- elements of glass reinforcement for strengthening all types of foundations are covered with a mixture with a thickness of more than 5 cm. For this, you can also use bricks, which should be laid on the bottom of the structure;
- several rows of fiberglass reinforcement are placed on a row of bricks. Solid rods with no joints should be used. To calculate the required length of the rod, you must first measure the length of each side of the future foundation. Based on these values, you can unwind or cut the rods of the required length;
- after laying the longitudinal row of rods, they proceed to strengthening the transverse jumpers with plastic clamps;
- the upper part of the frame is made, which exactly repeats the lower part. The size of one cell is about 15 cm. Both levels are fixed with vertical bridges;
- after knitting of the reinforcing cage, the process of pouring the concrete composition begins. Experts recommend using concrete grade M400.
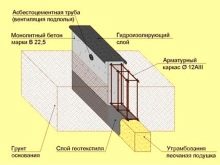
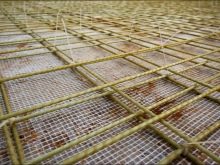
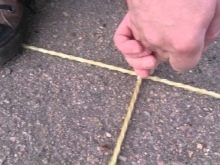
Competent calculation of fiberglass-type reinforcement will avoid unnecessary costs and additional problems due to the lack of reinforcing bars and purchase the required amount of products.The calculation for foundations of strip and slab types consists in determining the length and number of rods, based on the area of the foundation and the step of the reinforcing mesh. It is necessary to take into account that the slab must have two reinforcing belts: lower and upper, which are fixed with vertical rods along the entire perimeter of the slab. The process of reinforcing a columnar foundation is different. Ribbed reinforcement is strengthened vertically, and smooth reinforcement horizontally. The frame requires 3-4 rods, their length is equal to the height of the post. For pillars of large diameter, more rods will be needed, and more than 4 horizontal rods are needed for one pillar.
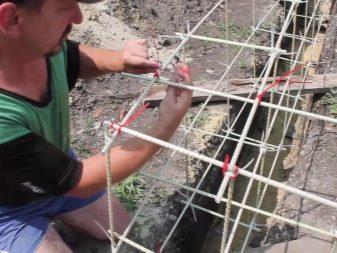
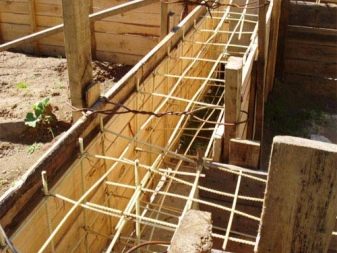
To calculate the optimal volume of concrete solution, you need to know the perimeter of the foundation, which is multiplied by its width and depth values. When pouring the mixture, it must be remembered that it is necessary to compact the solution in order to avoid the appearance of air bubbles.
The concrete mortar hardens for about 3 weeks. At this time, it is necessary to protect the surface of the poured foundation with polyethylene from moisture. In sunny weather, it is recommended to spray the surface with water.
Most professionals say that when laying gas and foam blocks, the corners should be reinforced with metal fittings. Such a combination will give building structures even greater strength, stability and reliability. There are often disputes about the need to knit glass reinforcement with plastic clamps. It should be knitted to strengthen the reinforcing cage before pouring the concrete mixture until the composition is completely dry. After the surface hardens, it does not matter whether the frame is connected or not.

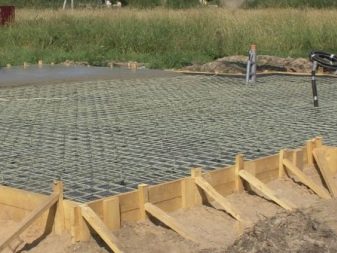
In the video below you can see a review of fiberglass reinforcement for the foundation.
The comment was sent successfully.