Foundation construction technology with a basement
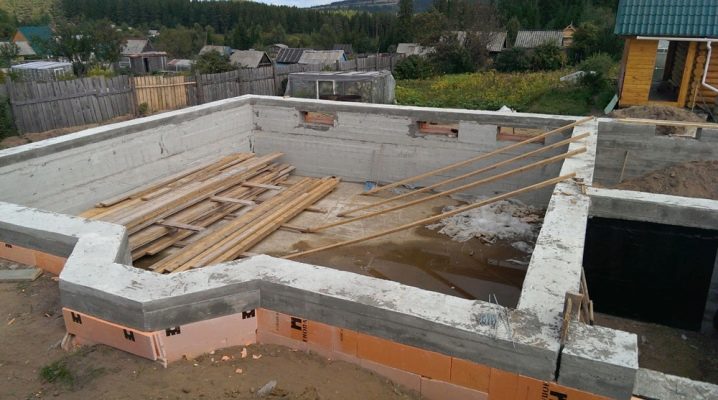
In some cases, home owners do not have enough of the premises that are located on the surface. The solution to this problem seems to be simple - by organizing the basement. But it is important to consider that each such case requires a modification of the foundation of the house.
Peculiarities
A foundation with a basement inevitably comes out more expensive and more complicated than a simple analogue. The volume of earthworks is increasing, and the consumption of construction materials is increasing. More attention will need to be paid to preventing water ingress and condensation. For your information: foundations designed for a basement, regardless of the properties of the soil and the severity of the building, are made recessed.
The calculations take into account the level of standing of soil water and the characteristics of the land in a particular place.
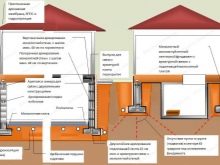
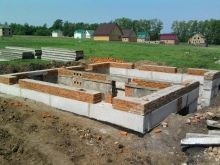
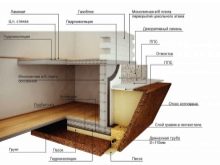
Views
Before you make a basement in the house, you need to figure out the type of foundation for it. Most often, the base is made of tape. The final choice is made after studying the mechanical and heaving properties of the soil.
Important: the tape can be not only monolithic, but also a team for execution.
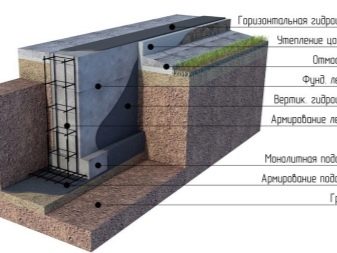
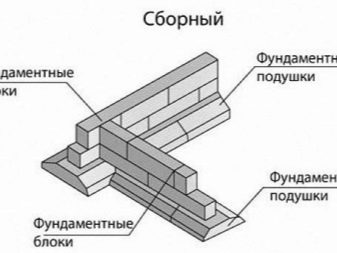
The use of ready-made blocks drastically saves time and allows you not to fear the poor quality of work. Monolithic ribbons are necessarily formed with formwork, and concrete must be poured into it strictly at one time.
In any case, the need for mortar and other materials is determined using special calculations. Be sure to mark the construction site to avoid problems. The pit under the tape is made as even as possible, and layers of crushed stone and sand are placed below, which will have to be thoroughly rammed. For formwork, it is allowed to use durable wooden boards with a thickness of at least 25 mm. It is customary to reinforce the tape with metal rods with a cross section of 1.2-1.6 cm.
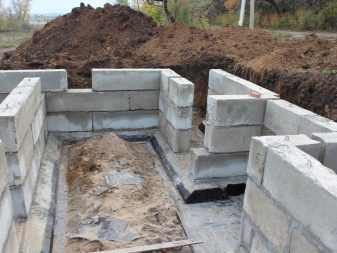
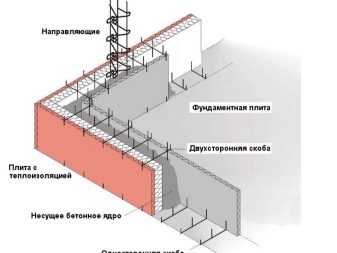
Avoid the exit of frame elements outside the foundation. Ideally, the ends should be recessed 30 mm or so. Particular attention is paid to strengthening the corners and the lowest points. Waterproofing of tapes is made with bitumen, roofing felt or more modern materials. The strip foundation can even be used to obtain a basement with a cellar.
This solution allows you to preserve food and other perishable items, regardless of the availability of electricity, in any season of the year. Even if the refrigerator breaks, the cellar can help out. Moreover, just the tape base is best suited for this purpose. If the foundation is made using slab technology, you will either have to abandon the cellar altogether, or equip it outside the main house.
In any case, some kind of structure should be equipped above the cellars, this will improve ventilation and increase the drying efficiency.
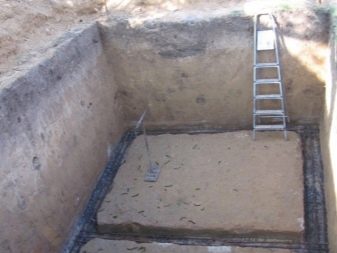
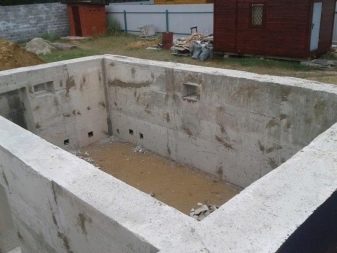
A simple basement (without a cellar) can also be built on a monolithic slab. This practice is best suited for difficult terrain, that is:
- heaving;
- subsiding;
- actively compressible and so on.
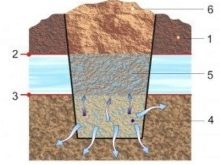
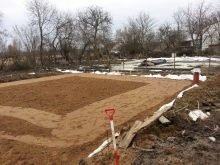
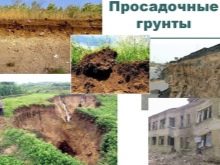
The classic slab scheme requires lowering the foundation deeper than the ground freezes. In the floating version, the mount is made 0.6-0.8 m below the surface of the earth, regardless of freezing. The pit will have to be dug 2 m more than the intended slab in all directions. Having reserved this place, it will be much easier to carry out foundation work. The bottom of the pit must be carefully tamped.
Having filled up the pillow, they begin to form a foundation, that is, a screed with a thickness of 4 cm. The actual concreting is carried out using sand concrete M300. Crushed stone needs to be watered with portions of this solution, and not all of them at once, this is the only way to get a kind of "crust". When the preliminary screed is formed, you can already do the waterproofing. For it, they mainly use roll materials on a bitumen basis.
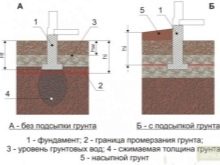
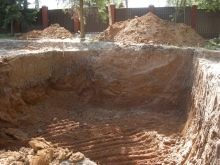
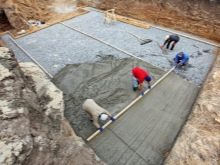
An alternative to the described solutions turns out to be a foundation for a basement made of FBS blocks. This design has three advantages:
- increases the usable area of the house;
- makes the building more stable;
- increases energy efficiency as the walls of the underfloor space are insulated.
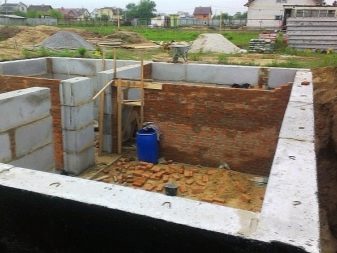
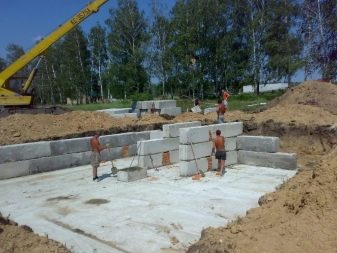
The foundation blocks differ and adapt to the size of the buildings. But according to experts, it is most convenient to use the largest products, and all others are best used as additional parts. The fact is that no calculations and careful preparations allow avoiding the occurrence of voids and shortages in length. FBS is distinguished by perfect safety for human health and the environment. This material will not accumulate fungal foci and will not be affected by microbial colonies.
As for the disadvantages of FBS, it is worth remembering their high price. However, due to the lack of fittings, the fee for the construction of 1 cubic meter. m is still less than when using monolithic slabs. More serious is the fact that the joints cannot be sealed 100%. Bulk foundation options tolerate contact with groundwater and water-saturated soils much better. It is also important to remember that FBS are heavy, normal work with them without the help of truck cranes and trained installers is impossible.
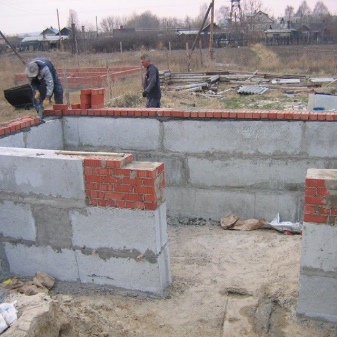
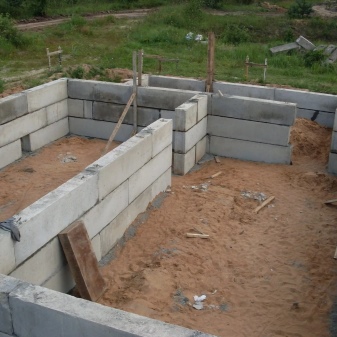
In some cases, basements are placed in a recess below the foot of the foundation. This is done if the basement was not originally equipped, but then it became necessary. This can only be done using tapes or piles. Going deeper under the slabs is categorically unacceptable. It may even end in the destruction of the entire house or other structure.
It is very difficult to prepare a recess for the basement below the foundation. Considerable amounts of soil will need to be taken out and the outsole will need to be reinforced. Additionally, you will need to make a sand backfill for future floors, pour concrete there, decorate walls, stretch wiring and install electrical appliances. According to statistics, building a basement in an already operated house will cost twice as much as building it simultaneously with a dwelling (and this is still a minimum estimate).
It is preliminarily recommended to assess how deep the moisture is in the soil; control is carried out by digging a hole on the hottest day of the year.
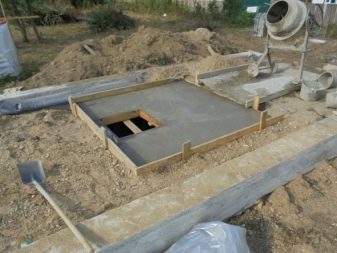

The markings for the future basement are adjusted for the thickness of the outer walls. Most cellars are made in 2x3x2 m format - more serious dimensions are not always needed. It will be necessary to disassemble the screed in accordance with the markings, and only then undertake earthworks. The walls must be covered with a two-layer waterproofing coating based on any roll material.
When concreting, it is permissible to use both removable and one-piece formwork.
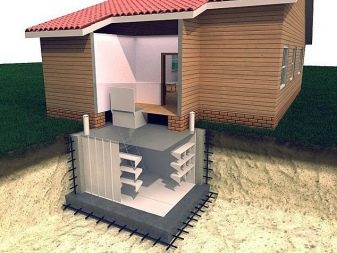
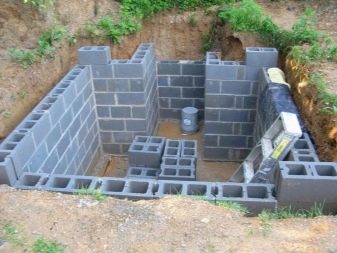
In actual construction practice, instead of a clean tape, slab or pile foundation, a composite foundation is often found. There are various schemes for how to do it:
- place a block structure on a monolithic pillow;
- instead of the grillage, tie the piles with a highly placed tape;
- put bricks or blocks in the intervals of the pillars;
- to make the support of the slab on piles (instead of the usual sandy flooring).
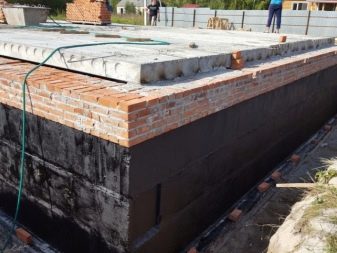

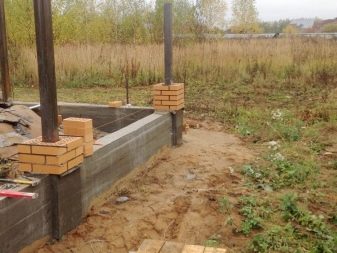
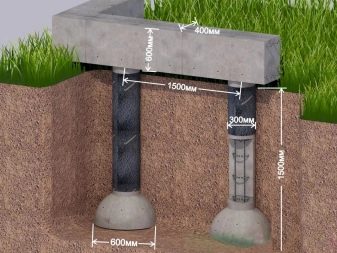
The formation of a layer of monolithic reinforced concrete around the perimeter of the foundation, made of piece parts, allows you to guarantee the reliability of the structure and unite its various parts. The combination of tape and pillars makes it possible to strengthen the support of the tape base. For soft soils or for soil prone to heaving, this is the best option. Ultimately, it will even turn out to build a heavy house on an area with rapid horizontal movement of the ground. The load generated will be evenly distributed, including in difficult cases such as building on slopes.
Important: the combination of different types of foundations under one structure must be approved by professionals.
Attempts to collect information on your own are unlikely to allow you to make the right decision. And in the best case, this will result in an unnecessary delay in construction, excessive earthwork and other additional costs. Some miscalculations can completely reduce the life of the house and even lead to its premature destruction. If the characteristics of the combined blocks do not match, cracks sometimes appear between them.
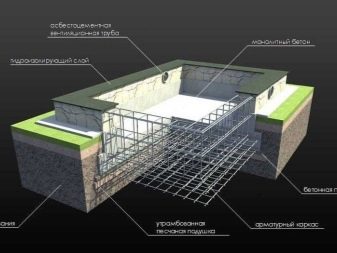
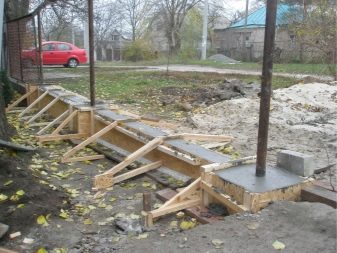
A columnar foundation under a private house attracts the attention of developers with its minimal cost, ease and lack of special requirements for the experience of builders. The strongest and most stable pillars are structures based on monolithic reinforced concrete. Only they should be used where soil swelling is aggravated by high-standing groundwater. It is usually customary to put pillars in the corners, at the intersections of walls with each other and with piers.
Additional reinforcement is made if the gap when placing the supports according to the basic rule turns out to be more than 3 m.When building a heavy house, it is required to bring the supports closer together, but you should not put them closer than 1 m to each other, this will only create unnecessary costs without adequate return on strength. A grillage and tape with a slight deepening can be used as a transverse beam that dampens the likely uneven shrinkage.
Construction in such formats and the use of foundation blocks does not exhaust the possibilities of making a base for a house with a basement. We also need to think about the pile foundation, which in a number of situations turns out to be an ideal choice for developers. This solution is recommended if the soil only weakens as it moves deeper, instead of the expected hardening.
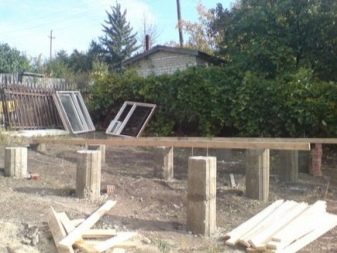
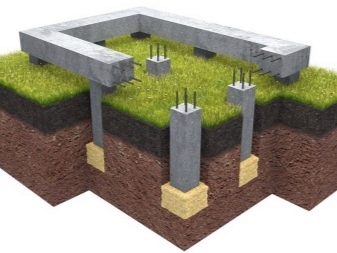
It is impractical to dig a pit tens of meters under a private house, but it is more accurate to use piles. They are actively used on soft soils:
- rich in humus and peat;
- loess-like;
- quicksand;
- plastic loams.
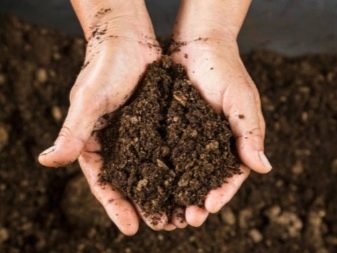
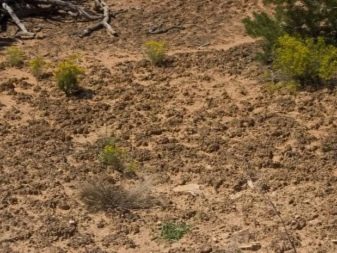
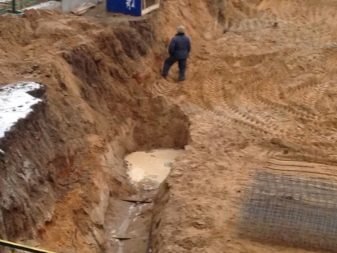
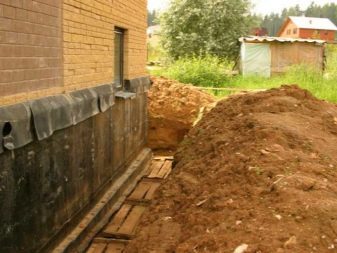
But in very dense soil, pile structures are also useful. They reduce labor intensity and the need for foundation concreting. Now there are many types of piles and modes of their application. In order to avoid unnecessary problems, it is best to consult with specialists. Without any consultation, it is clear, however, that the wood should be left as a last resort. Even with a solid treatment with protective agents, it serves too little.
Large steel products cannot be assembled without cranes.
In any case, you will have to spend money on a thorough anti-corrosion treatment. It is worth considering the increased metal costs. Reinforced concrete structures are considered the best choice. They can be made on the construction site itself, if there is a suitable tool and minimal skills. Having made reinforced concrete piles in accordance with all the rules, you can expect that they will last at least 100 years.
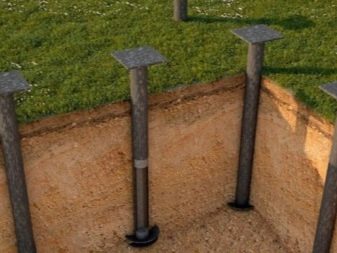
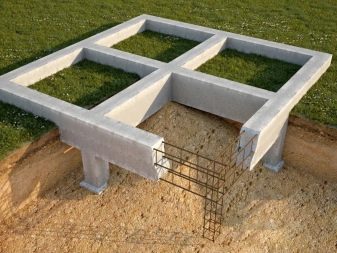
How to build with your own hands?
The construction technology according to step-by-step instructions after digging a pit is as follows:
- filling the pillow from gravel and sand;
- spillage of cement screed;
- protection against water;
- forming the basis for the foundation;
- drainage preparation (with closely lying groundwater);
- overlapping the basement with additional waterproofing.
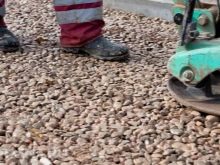
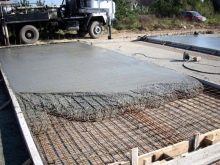
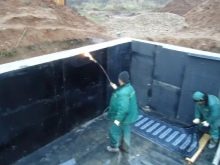
The good thing about independent work is that it helps you save money on the salaries of professionals. But first you have to calculate everything thoroughly.If some kind of work can be done manually and with the help of special equipment, it is better to prefer the mechanized option. The expense of paying for equipment or helping craftsmen will soon be justified by a significant improvement in quality. It is advisable to perform any work with cement pouring in one working day, otherwise the strength properties will be unsatisfactory.
Important: a foundation with a basement cannot be built without large-scale earthworks. Therefore, the order of freight transport for the removal of the seized soil is necessary in any case.
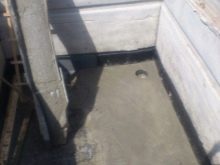
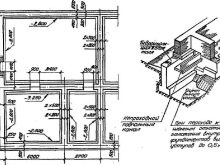
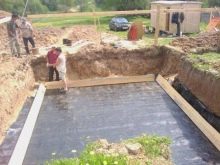
After the excavator completes its work, the bottom and walls of the pit will need to be compacted by ramming. It is imperative to calculate the walls and floor in the basement, only then it will be of high quality inside and out. Those who build such structures without calculations find themselves in a losing position.
The calculations take into account:
- Does the wall reinforcement fit into the foundation;
- whether the backfill soil is brought to the top of the wall;
- how the floor is supported;
- whether the engineering and geological conditions during construction are difficult;
- what coefficients are valid in a given area.
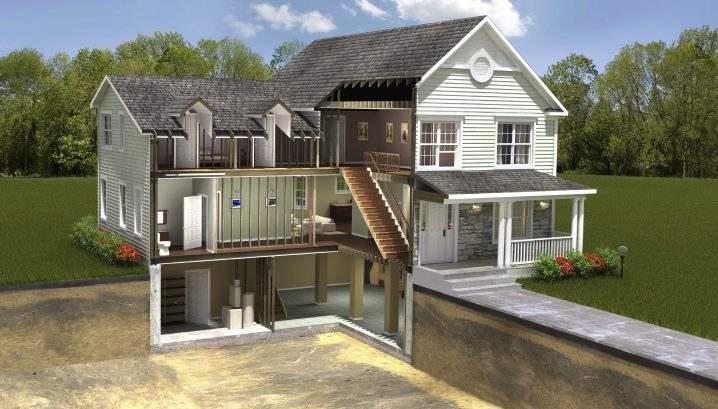
In most cases, the basement is used not only for storing blanks for the winter. And this means that in addition to the installation of walls and floors, they will also have to be properly insulated. This is especially important when additional living or working space is being organized. Backfilling can only be done with materials that are not prone to heaving. In any warm basement, basements are insulated; for this purpose, materials with a zero level of water absorption are used, which retain their characteristics even when moistened.
Extrusion foams are most commonly recommended. Slabs are insulated by laying out the material on the supporting parts between the logs. The insulation layer is preceded by a protection against getting wet. A vapor barrier is formed above the insulation, which will prevent it from being exposed to water vapor contained in the air. The material of this barrier is placed with a roll run of at least 10 cm.
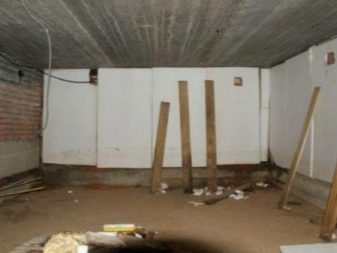
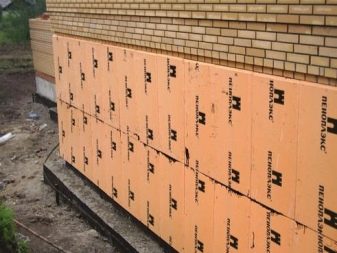
Even the warmest basement of a house may not cope with the task at hand. The fact is that after pouring the tape, its reinforcement must certainly be done. Only this approach guarantees normal mechanical strength. The cracks that appear must be immediately saturated with a solution and tightened with metal strips.
This technique almost always stops further destruction of the material.
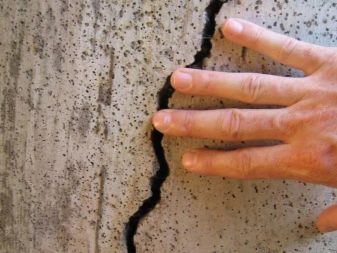
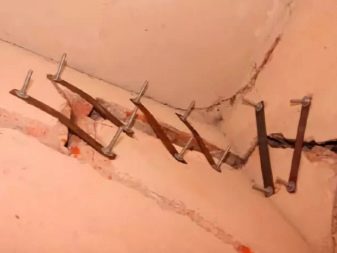
Advice
When building a foundation under a suburban private house, it is advisable to form a single foundation for the entire building. If in one part there is a basement, and in the other, for example, a tape, it will simply begin to sag in the air. Soon enough, such a structure will break. The optimal concrete wall for a home basement has a thickness of 0.4-0.5 m. There is no particular need to build a lintel in the basement.
How to build a foundation for a house with a basement, see below.
The comment was sent successfully.