Description of the main pile driving methods
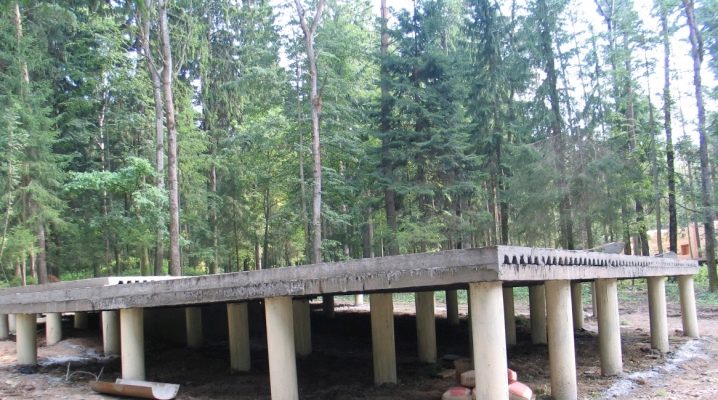
The construction of any capital building begins with the construction of the foundation. The appearance, performance, durability and safety of the structure depend on how correctly its type was chosen and the installation work was carried out. Today, pile foundations are increasingly used in the construction of objects for various purposes.
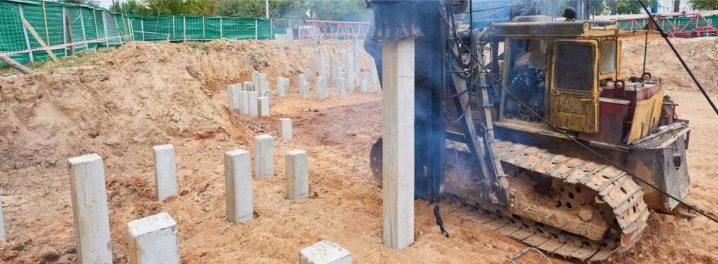
Peculiarities
Driven piles rest on solid soil layers, and therefore are characterized by high bearing capacity. Their use, in addition, prevents the deformation of dangerous soil layers, which, under other conditions, is fraught with uneven subsidence of the structure.
Pile driving is carried out in the following types of soil:
- loose sandy and medium-strength soils;
- fluid and plastic sandy loam;
- tough, fluid and soft-plastic clays and loams.
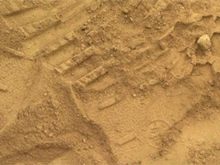
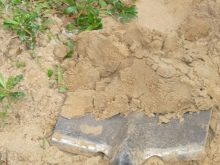
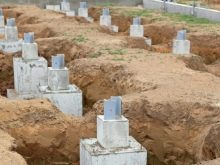
If the piles go beyond the soil by no more than 200 cm, then this technology can also be used on clay soils with a fluid consistency.
Different types of piles are used for driving. If we talk about the shape of the section, then these are:
- round (solid and hollow);
- T-shaped;
- square.
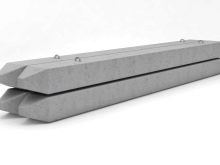
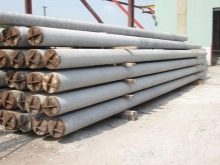
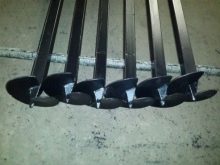
Depending on the material used, piles are distinguished:
- metal - suitable for the construction of large brick buildings, based on a wooden frame, as well as for the construction of frame houses;
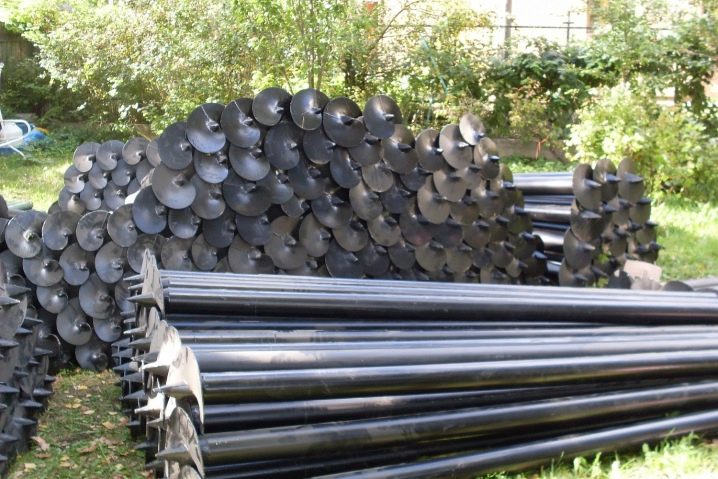
- reinforced concrete - used for monolithic industrial and multi-storey buildings, recommended for moving soils;
- wooden - suitable for private houses, summer cottages, small bridges, temporary buildings.

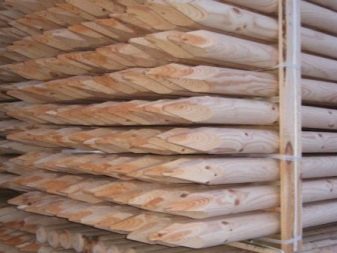
Monolithic and welded, depending on the manufacturing method.
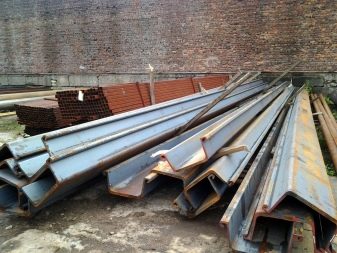
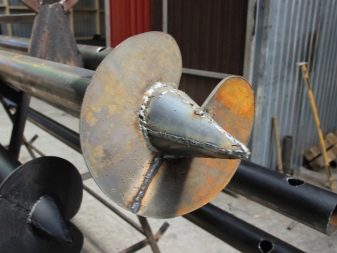
Selection criteria and features of wooden piles are determined in accordance with GOST 9463-88. There are regulations for other products.
Regardless of the type of pile, they must meet the following requirements:
- one element must withstand a heavy load;
- high crack resistance;
- resistance to high variable loads, the ability to function in difficult hydrogeological conditions.
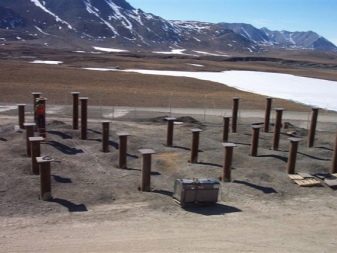
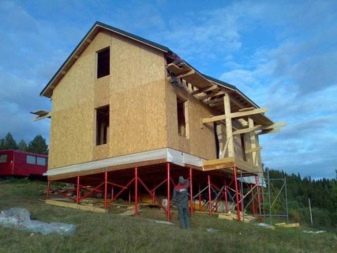
For pile driving, special equipment is used that exerts a static (constant indentation) or dynamic (impact) load on the elements. The work is preceded by geological exploration and driving of a test element. The last action allows you to see how accurate the theoretical assumptions about the nature of the soil are, to evaluate the behavior of the pile in the soil.
After driving the test element, a break is made for 3-10 days (the exact time depends on the type of soil), during which observation is continued.
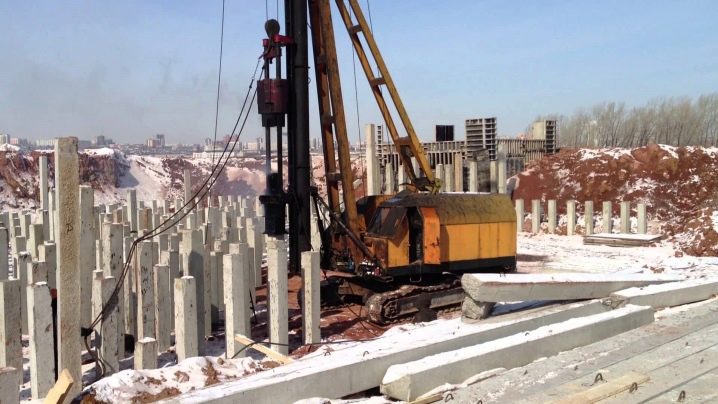
If the trial driving was successful, all the supports are installed, the foundation is organized, at the end of which the foundation is taken in. The latter involves the closure of the aboveground part of the base in order to protect it from negative environmental factors. The pick-up can be carried out using brickwork, boards, concrete mortar. The resulting plinth is then lined with a suitable material.
The main advantage of the pile foundation is, of course, the possibility of erecting buildings of medium and large size on hazardous soils prone to crumbling and plasticity. One element can withstand a load of 1.5 tons. This, in turn, allows you to reduce the number of piles, and, at the same time, to reduce the cost estimate. The costs of the pile foundation will be lower compared to the costs of organizing a strip or monolithic analogue.
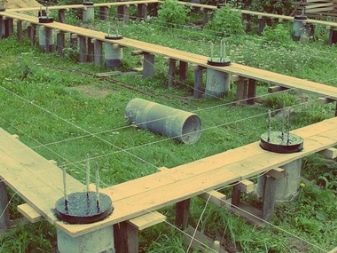
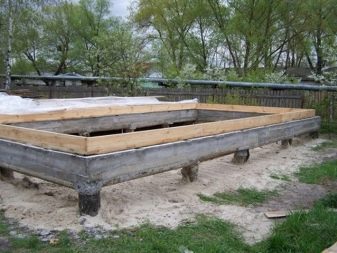
It is important that the elements are immersed in the soil below the level of its freezing, otherwise they will be pushed out in winter. To partially prevent this, as well as to reduce the force of pressure on the elements, a waterproofing layer in the form of 2 layers of roofing material allows.
Besides the obvious, the pile driving method has the following advantages:
- nearby buildings do not experience dynamic loads;
- the possibility of building on relief soils, soils with a significant slope;
- preservation of the general appearance of the landscape;
- high speed of foundation construction, no need to wait for the foundation to gain strength;
- suitable for all types of buildings;
- makes almost any site suitable for construction.
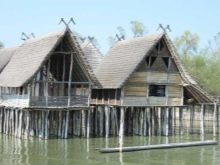
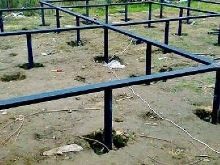
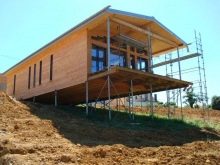
The ways
A feature of the pile driving technology is the need to pre-drill wells of the required depth. The next step is to organize the pile shaft. This stage can be carried out, depending on the type of soil, in one of three ways:
- dry - made without fixing the walls of the support;
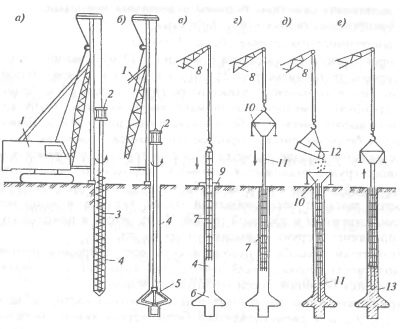
- using clay, which avoids well sloughing;
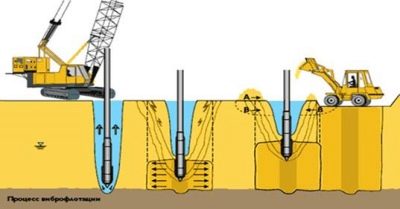
- using casing to fix the supports.
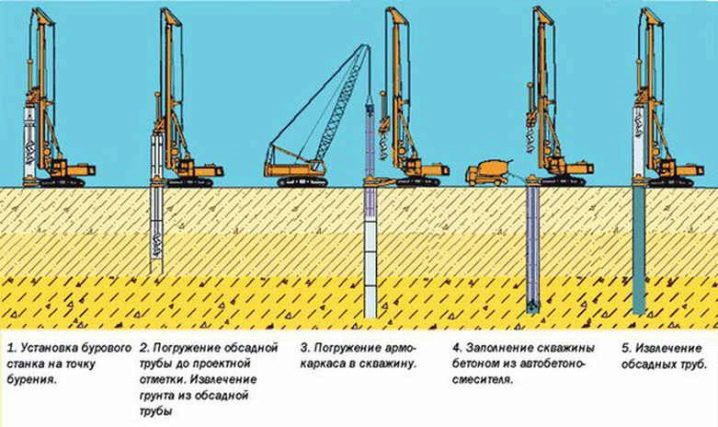
In addition, the driving process itself can be done in different ways:
- through a blow;
- by vibration method;
- by indentation;
- screwing method;
- with the use of leader wells for supports.
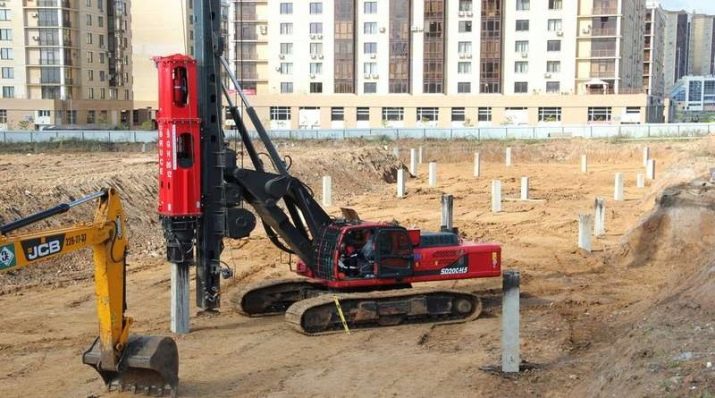
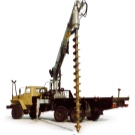
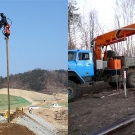
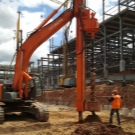
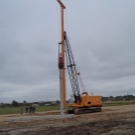
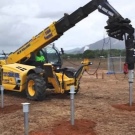
Sometimes several methods are applied at once on the same foundation. Let's take a closer look at each of them.
Driving piles involves the use of a pile driver or other special equipment (for example, an excavator), on which a hydraulic hammer (or a diesel or pneumatic hammer) is hung for driving. Diesel hammer is a simple but effective hammer. It operates regardless of the availability of energy sources, has a high performance, weather resistance.
This technology is considered one of the most affordable, since it is not associated with increased financial costs, it can be used on any type of soil.
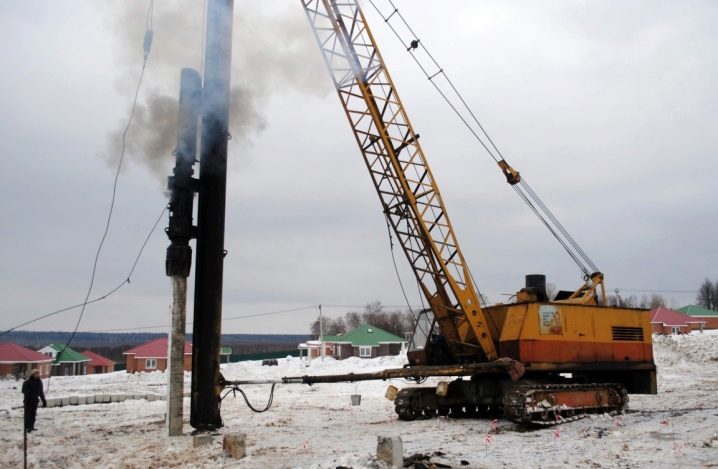
The essence of the hammer-in method is based on the impact energy. With each blow to the head, the element goes deeper into the ground until its tip rests on a solid base.
Vibration driving involves a reduction in friction between the lateral surface of the supports and the borehole walls, so the method requires less stress. During vibration immersion, the displaced soil should be compacted around the pile, since this is directly related to the strength of the future foundation. It is carried out with the use of submersibles, hammers and special installations that provide vibration and deformation of the soil under the tips of the piles and in the area of their side walls.
The vibratory pile driver in this technique is effective on moisture-saturated soils. For dry and dense soils, spring-type vibratory hammers are more suitable.
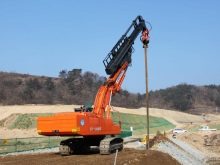
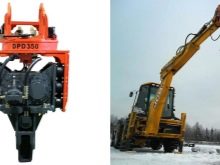
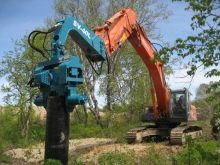
The indentation technology is one of the quietest. It is carried out due to a certain load on the piles, which is why they literally "fall through" into the ground. The load comes from vibrators and a hydraulic jack, it is important that the piles are also pressed under the influence of their own weight.
The process involves several cycles of deepening and subsequent extraction of the support until its tip stalls and reaches the design depth. Suitable for most types of soils, including those with deep dense layers. This method is not suitable for piles driven to a depth of more than 6 m. Due to the size of the equipment used, an area of at least 500 square meters is required for its placement. In addition, this is a rather expensive way of organizing a pile foundation.
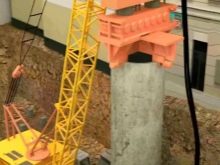
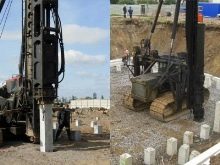
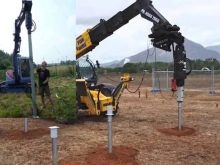
Screwing technology involves the use of metal or reinforced concrete (RC) piles, which, in addition to the tip, have blades. The latter are necessary for immersion, screwing the supports into the ground.This method is used on flooded and fragile soils, is widely used in urban construction, since it does not create noise and vibrations, does not deform the soil layers of neighboring objects.
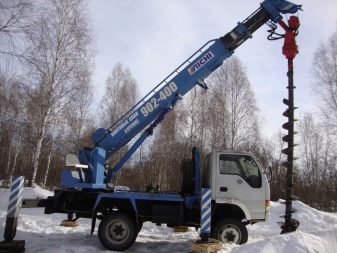
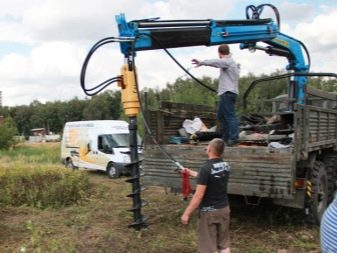
The quietest safe for the landscape is considered to be the method of sinking the supports. It is suitable for rocky soils, soils in the permafrost zone, soils with solid (up to 20%) inclusions.
The essence of the drilling method is that a hole (leader hole) is made in the soil, the diameter of which is less than the diameter of the pile. The height of the resulting borehole corresponds to the height of the pile without the tip. After that, a support is driven into the well.
A variation of the submersible method is the drilling run. In this case, the diameter of the well is slightly larger than the diameter of the piles, therefore, after the latter is immersed, the free space between the walls of the hole and the walls of the support is filled with a cement-sand or soil mixture.
Well drilling is carried out using pile drivers equipped not with pile hammers, but with rotary rotators. The latter ensure a strictly vertical direction of drilling, which is a key indicator of the quality of drilling.
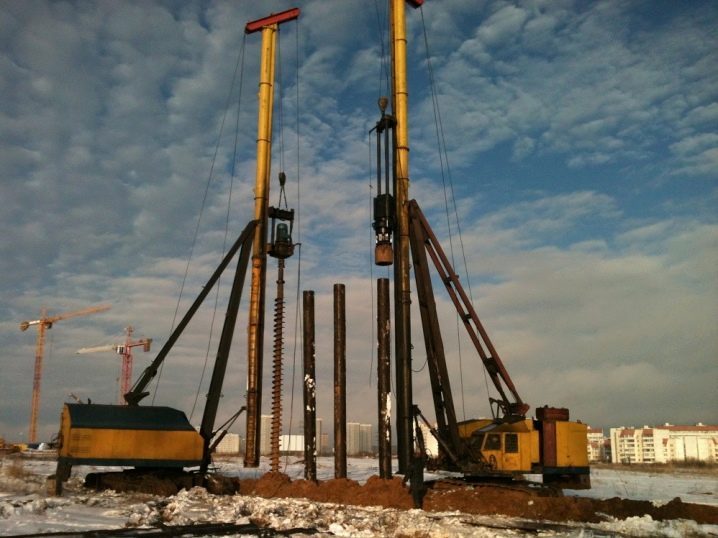
This method is costly as it requires the involvement of special equipment. However, on some types of soil, as well as in densely built-up conditions, it remains almost the only one.
How to choose?
The choice of one or another method of pile driving is primarily determined by the characteristics of the soil. So, percussion equipment is unacceptable to be used in soils with solid impregnations (stone, crushed stone, gravel). The clogging method will not work even if the construction site is located close to the operated facilities, main pipelines. In short, where noises and vibrations are prohibited.
The vibratory immersion method is optimal for water-saturated and sandy soils, but it is not available when it comes to dense and inactive, especially rocky soils.
An important selection criterion is the consumption of piles and, accordingly, the cost of work. As a rule, for premises of regular use, one has to choose between reinforced concrete and screw piles. The bearing capacity of reinforced concrete supports is higher, but they are installed with the same pitch as the screw ones. That is, it will not be possible to reduce their number.
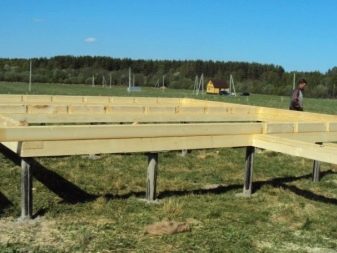
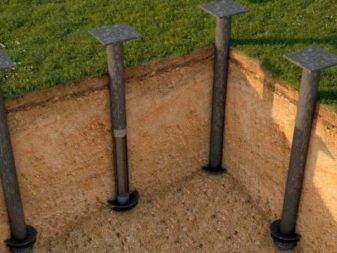
For the construction of a large object, including a country cottage, you should choose reinforced concrete supports. For baths, sheds and outbuildings, temporary objects, the purchase of reinforced concrete piles is irrational, you can also purchase screw analogs. However, the latter are not recommended for use on highly acidic soils, since the service life of the piles will be short.
But for soils with significant differences in height or on watered soils, it is better to use screw piles. Reinforced concrete (even when using compound modifications) in this case tend to fail, which does not happen with screw counterparts due to their wider base. In addition, the latter can be extended to the required length - until the base rests against strong layers.
If we compare the complexity of the methods, then all piles installed by the driven method require less installation time. As a rule, for this, you only need to deliver special equipment to the site, which moves along it on a caterpillar track. For a shift, such installations are capable of driving up to 40 piles, that is, creating a whole foundation in most cases.
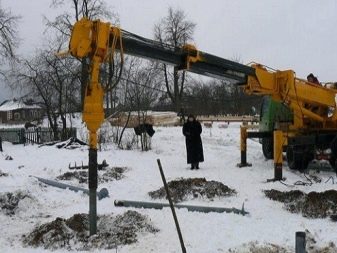

An important point - when choosing an indentation technology, it is important to evaluate the size of the area and the equipment used for pressure on the supports.
The introduction of screw piles into the ground implies the use of electromechanical equipment or a hole drills, with the help of which a gearbox is installed in the mounting hole, and it ensures the screwing of the supports. If access to the construction site is difficult or for other reasons it is not possible to use special equipment, manual installation of piles is possible.The process will turn out to be long and laborious.
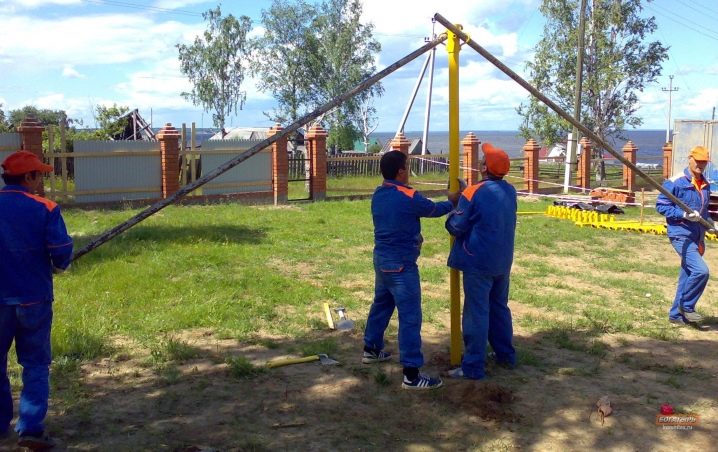
Advice
Regardless of the selected technology and size, the purpose of the building, diagrams must be drawn up, which reflect the bearing load of the supports, the depth of their burial, step, diameter, and so on.
If the building provides for heavy structures, for example, stoves, fireplaces, then they need their own mini-foundation. It is not associated with the main base and must be built according to its own calculations.
When driving a pile with your own hands, it should be remembered that it must be installed below the level of freezing of the soil and pass through all the weak layers. This is the only way to achieve the strength and reliability of the pile-type foundation.
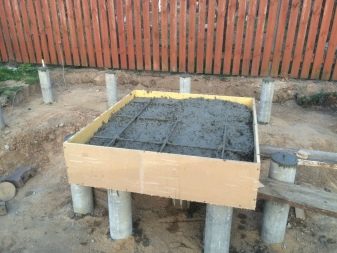
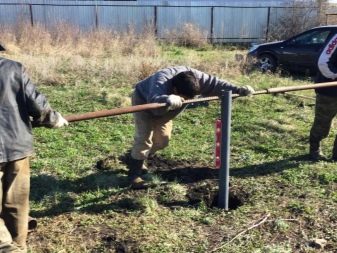
If it is necessary to drive a support into an overly dense soil to a great depth, the erosion technology can be used. To do this, water is pumped into the well along the pile under pressure. It serves to soften the soil and reduce friction between it and the pile walls.
Piles are driven, as already mentioned, to solid ground, the depth of which corresponds to the design documentation. In doing so, it is important to make sure that the element has reached solid layers, and not rested, for example, against a stone. Otherwise, the skewing of the pile cannot be avoided during the operation of the house, which affects the geometry of the structure as a whole.
It is better to submerge or drive piles in the warm season, after the upper layers of the soil have thawed. If it is not possible to carry out work before frost, then it can be carried out in a regular mode, provided that the soil is frozen to a depth of no more than a meter.
If freezing is more significant, you can use a special device - "steam needle". It represents a tube on which it has a hole - hot steam comes out of it. The tube is lowered into the well, helping to defrost the soil. For frozen soils, the drilling run method with preliminary drilling of leader wells is also suitable.
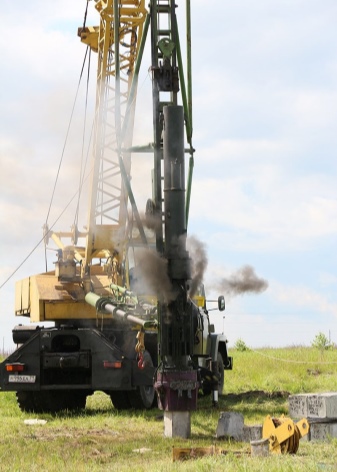
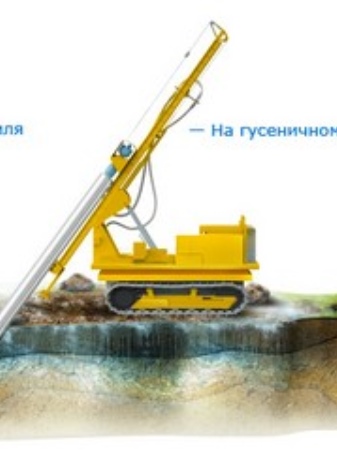
Attempts to drive piles into frozen soil in other ways, at best, will lead to loosening as the soil thaws, at worst - to deformations.
A hand hammer can be used to drive small diameter piles to shallow depths. For larger construction, an electric or hydraulic hammer is used. Their cost is high, but they can be rented when it comes to private housing construction.
When using the drilling method, you should first take care of the removal of the soil extracted during the drilling process. Otherwise, the construction level will rise by an average of 0.5 m.
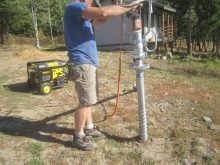
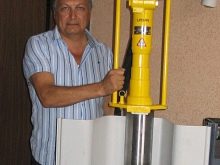
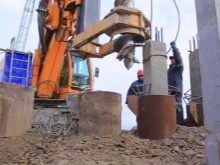
Well depth is of strategic importance in leader drilling. It should be half a meter shorter than the support. Otherwise, it will not be possible to ensure the retention of the pile with soil.
For vibration driving, indentation and pile driving, see the next video.
The comment was sent successfully.