All about plywood

Plywood is a composite material made from natural wood. It consists of sheets formed by gluing 3 or more thin layers of wood. The material is characterized by exceptional strength and stability with changes in humidity levels, while it compares favorably with solid wood.


What it is?
Plywood is a multi-layer material obtained by gluing sheets of thin wood veneer. It is characterized by increased resistance to bending and mechanical deformation - this is achieved due to the special structure of the material. The veneer sheets used for the production of plywood are stacked on top of each other so that the direction of the fibers alternately changes. As a result, under any mechanical action, each sheet forms a deflection in its direction and, as a result, compensates for the deformation force of the remaining layers.
Plywood production is a laborious multi-stage process that requires careful selection of raw materials. At the initial stage, logs are hydrothermally treated. Under the influence of water and high temperature, the wood fibers acquire sufficient elasticity, then the bark is carefully removed in a special installation and peeling is performed.


A specialized machine dissolves the wood into thin veneers - technically, the process is similar to sharpening pencils. As a result, a thin long tape with a cut of 1-3 mm is formed from the log.
The veneer is cut into separate sheets in accordance with the parameters of the plywood. They dry well, then they are coated with glue, folded and cold pressed. The resulting blank is pressed again, already under high-temperature action - this contributes to the polymerization of the main adhesive components. For greater strength, the resulting slabs are additionally laid out in large piles, where they lie under their own weight for at least 20 hours.


Of course, plywood cannot replace wood, however, it has its advantages:
- affordable cost;
- ease;
- ease of installation;
- high thermal conductivity;
- soundproofing;
- resistance to mold, fungi and other pathogenic microflora.
However, plywood has its drawbacks:
- fear of moisture;
- low, in comparison with wood, operational parameters;
- in case of mechanical damage to the plywood, its delamination is possible.


Composition and properties
Not all types of wood have a set of necessary characteristics for the manufacture of plywood sheets. The most common are coniferous varieties and birch. And also plywood is oak or beech, less often it is made from poplar, ash, as well as linden, maple or exotic bamboo. Besides, combo panels can be found on sale - they are obtained from several types of wood.
- Birch. This plywood is 85-95% birch raw material, it is considered the strongest material from all the assortment offered in stores. The density of this material corresponds to 600-700 kg / m3. It is 20% stronger than its pine counterpart. It is distinguished by a homogeneous structure and aesthetic appearance. Resinousness is absent.

- Coniferous. Environmentally friendly plywood, conifers are used for the production of such material. Thanks to resins that repel fungi and mold, it is highly resistant to decay. Pine plywood is most often sold in Russia.

- Combined, the strongest types of plywood. Manufactured in such a way as to achieve high resistance to all types of external mechanical influences. Several different types of wood are used here. As a rule, the core is formed from birch or pine, and the outer part is made of hardwood with a decorative texture.
A separate type of plywood is OSB boards - they are made from pressed shavings and sawdust.

Plywood has a number of distinctive characteristics.
- Strength. Directly depends on the type of wood, as well as the characteristics of gluing. Usually ranges from 500-750 kg / m3.
- Environmental friendliness. The toxicity characteristics of plywood are determined by its emission class. For installation in residential premises, you need to buy only environmentally friendly materials with an emission class of E1 or less. All other varieties, to one degree or another, can be sources of formaldehyde and be harmful to health.
- Biological resistance. This is not to say that plywood is completely protected from mold and rot. However, its resistance to them is much higher than that of ordinary wood. This is due to the fact that plywood contains phenolic as well as urea resins, they act as fungicides. In any case, it is advisable to treat the surface with an antiseptic composition before use.
- Flammability. Plywood is classified as a product with high flammability - this should be borne in mind when using it.
When flame retardant impregnations are added to the adhesive composition, non-combustible varieties of wood material are obtained.


Plywood is often used to create outdoor fencing, with this method of use it is necessary to take into account its insulating characteristics.
- Moisture permeability. The material can absorb water, when moistened on one side, water will surely fall on the opposite side, and it can also transfer to adjacent construction materials. However, its permeability is capillary in nature.
- Thermal conductivity. This parameter directly depends on the density of the material, it is usually set in the range from 0.1 to 0.25 W / (m • K). The thermal conductivity of the most popular brands is close to that of natural wood.
- Water vapor permeability. The vapor permeability of sheets is almost 2.5-3 times lower than the similar parameter of wood and 5 times less than that of brickwork. That is why plywood is often bought for vapor barrier of internal walls.


Views
Plywood can be classified according to various criteria.
By the number of layers
Plywood can contain several sheets of veneer. The most widespread are lightweight three-layer products, they have a thickness of 3-4 mm. And also stronger products are presented in stores:
- 5 layers - 6 mm;
- 7 layers - about 9 mm;
- 9 layers - 12 mm;
- 11 layers - 15 mm;
- 13 layers - up to 18 mm;
- 15 layers - 21 mm;
- 17 layers - 24 mm;
- 19 layers - 27 mm;
- 21 layers - about 30 mm.


By moisture resistance
In the manufacture of plywood sheets, adhesives are used, so the material has a fairly high water resistance. There are several varieties.
- FC is a moisture resistant material. For gluing veneer, glue based on urea-formaldehyde resin is used. When buying, you need to pay attention to the emission class - it should be no more than E1, the harmfulness of such plates is minimal.
- FSF is a material of increased moisture resistance. Here the same glue is used, only with the addition of water-repellent components. This plywood is often used for exterior decoration.
- FSF-TV - varieties of flame retardant plywood with flame retardant additives.
- Laminated - this plywood is practically insensitive to the action of water.


By the degree of surface treatment
Depending on the method of surface treatment of the slabs, plywood is:
- unpolished;
- sanded on one side;
- sanded on both sides.
Sanding makes the surface smoother, ready for any finish.This is very convenient when performing renovation and finishing works, as well as when creating furniture modules. The surface of the panel can be additionally treated with a phenol-formaldehyde resin coating. This coating makes the surface harder and more resistant to wear. The surface of the slabs can be grooved, perforated, brushed, milled and fired.
Commercially available lumber is available in white, black, colored or varnished. Some boards are covered with plastic wrap.


For other characteristics
Plywood is classified according to its functional purpose.
- Aviation. To create such a sheet material, the thinnest veneer with a cross section of 0.4 mm is used. Only the highest quality wood is selected. This plywood is lightweight, yet has the highest strength and density. It is resistant to mechanical damage. Aviation plywood is in demand for aeromodelling and aircraft cladding. Usually, the material is made in small batches by order of military enterprises.
- Ship. As the name suggests, this material is used in the assembly of structures for floating facilities. The peculiarity of such plywood is the presence of a special impregnation, which greatly increases its moisture resistance. A special type of tropical wood is used for this material. Most of the ship plywood on the construction market is produced in America, as well as in Israel and the European Union. Domestic companies do not have the necessary raw materials for starting serial production.
- Furniture. This type of plywood has a very aesthetic appearance. Nevertheless, in terms of its physical and technical parameters, it is inferior to all other materials. Used exclusively to create kitchen furniture and bathroom cabinets.
- Formwork. This material is optimal for rough work, for example, for the design of the formwork before the rough pouring of concrete. A characteristic feature of such plywood is a laminated layer - this completely eliminates the soaking of the boards under the influence of water. And in addition, it provides the simplest possible tearing away from the hardened cement mortar.
- Construction. A very strong building material used for the installation of a flexible roof frame, wall and ceiling cladding. Construction sheets are expensive, so they have a narrow application.
- Transport. Beautiful dense materials that are relevant for the sheathing of wagons and trolleybuses. These sheets are distinguished by an anti-slip coating, they are characterized by maximum resistance to moisture and increased strength. The thickness of this plywood varies from 6.5 to 27 mm. Thickened is used for body cladding. Medium thickness products are optimal for the production of light vans.
- Decorative. This is probably the most unusual type of varnished plywood. It looks very beautiful, has an interesting texture and original color scheme. Suitable exclusively for renovation and finishing works.



Varieties and brands
There are several common grades of plywood.
- FSF - material glued with phenol-formaldehyde resin adhesive. It is durable and water resistant. Usually used in the construction industry.
- FC - here the veneered layers are glued with a carbamide compound. Such a material has a slightly lower hygrostability, but to a greater extent meets the requirements of environmental friendliness. It is relevant for interior cladding of structures and furniture production.
- FB - plywood glued with bakelite resins. They increase bending strength by 2-5 times, increase moisture resistance by 60-70%, and give exceptional surface density.
- FBS Is the most durable plywood made using alcohol-soluble bakelite resins. The material can withstand prolonged contact even with salt water, therefore, elements of the hull of floating craft are made from it.
- FBV - for gluing veneer sheets, water-soluble resins are used here, so it is 15% less moisture resistant than FBS.
- FBA - the only brand of 100% natural plywood without phenol. In it, veneer slabs are glued together with casein or albumin glue. Such material is absolutely safe for human life and health. Has a low moisture resistance.



The grade classification of the material depends on the quality of the surface. Wood is a material with a heterogeneous structure, cracks or rot are found on it - during peeling, all these flaws pass to the veneer. The GOST contains a list of all possible shortcomings. All varieties have their own possible flaws and their volume. Some deviations are allowed.
Elite grade E:
- there should be no noticeable defects on the surface;
- on coniferous materials, the presence of single knots is allowed;
- for hardwood there may be minor structural changes in veneer.

Grade 1:
- knots / knot holes;
- single closed cracks of small size;
- pale sprout;
- natural change in shade;
- slight veneer gaps in the inner layers;
- end defects.

Grade 2:
- knots / wormholes;
- single cracks;
- germinate;
- resin pockets;
- overlapping veneer of the outer layer;
- dents;
- scratches;
- oozing glue.

Grade 3: for this variety the same defects are typical as for variety 2, but in slightly larger quantities.
Grade 4: for this plywood, most of the restrictions have been removed. This is a technical material, low requirements are imposed on it to maintain mechanical characteristics. These types of plywood are mainly used for creativity - modeling and burning.


Dimensions (edit)
Plywood can be produced in various sizes, conventionally they are divided into standard and non-standard. The former are regulated by GOST 3916.1-96, the latter are produced in limited quantities on order for large industries. As a rule, sheets are made rectangular, less often they are in the form of a square. Depending on the dimensions, plywood can be small-format and large-format.
The most common sizes of small-format slabs include:
- 1220x1220 mm;
- 1525x1220 mm;
- 1525x1525 mm.
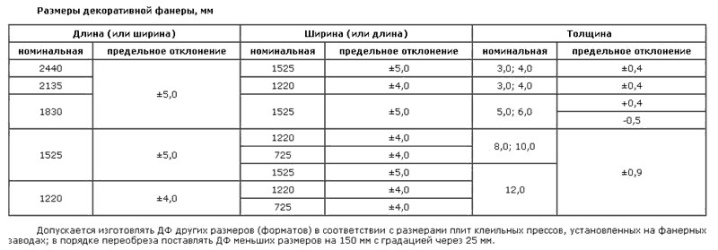
You can work with such sheets alone, without helpers. However, when fixed to the surface, a large number of layers are noticeable. That is why, in some cases, the optimal solution would be to use large sheets.
Large format products are manufactured in several sizes:
- 1830x1525 mm;
- 3050x1525 mm
- 3000x1500 mm;
- 2500x1250 mm;
- 2440x1220 mm.
As for the thickness, here you can find material in sizes from 1 to 40 mm. Some manufacturers make thicker models. The most popular are plates with a thickness of 6-27 mm.


Selection Tips
A high quality product can only be identified with close inspection. The look of plywood can tell a lot about the performance of a product. Be sure to look at the edge of the sheet, check if the layers are carefully glued. See what color the slice is. For example, the alternation of colored stripes indicates a combination of deciduous and coniferous varieties. The light one indicates the use of deciduous veneer, and the dark one - for coniferous wood.
Many unscrupulous manufacturers sometimes try to cheat consumers. - they glue only the outer surface of the panel with high-quality veneer. In this case, the operating parameters practically do not change, only the appearance of the plywood is improved. Such material can only be used for finishing cladding. But for the assembly of furniture and other serious tasks, it is unsuitable.


Common wood defects include:
- pinned or falling out knots;
- cracks;
- sharp shading transitions;
- scratches;
- dents;
- bulges;
- delamination of fibers;
- Wood "patches";
- the presence of rot;
- glue on the edge.
A large number of defects indicate that the manufacturer saved on raw materials, violated the standards for storage and transportation of products, or neglected the standards of the technological process. Such plywood will be short-lived.


Application
When using plywood sheets, it is necessary to keep in mind some of the subtleties of its application. Placing flat parts in mutually perpendicular planes, you can achieve the highest strength of the product. The main thing is to correctly redistribute the load on the surface and ensure the fixing of the mount. It is with great difficulty that the nails enter the plywood; they do not hold at the end at all. They are used only as dowels - they are driven into pre-drilled holes. This solution is used under shear loads, since they have little resistance to pulling out.
Screws and self-tapping screws resist pulling out well. However, pre-drilling is usually required to install them. Keep in mind that veneer tears and surface chips often occur during this operation.


To get a clean, even cut without spoiling the material, you can only use fine-toothed saws or laser cutting. For grinding, a belt sander is used, movements are performed along the edge.
Plywood is one of the varieties of furniture and construction material made from wood waste. You should not expect that by purchasing plywood, you will receive a versatile raw material that allows you to create a strong and beautiful structure that is not inferior in density to the Lebanese cedar. But if you use plywood in strict accordance with the manufacturer's recommendations, then this material will serve you for several decades.

In the next video, you will find additional information about the grades of plywood according to GOST.
The comment was sent successfully.