Features of transport plywood

It is important for organizers of any transportation to know the peculiarities of transport plywood. You will have to carefully examine automotive plywood for the floor, laminated mesh, moisture resistant plywood for the trailer, and other options. A separate topic is how to choose plywood for a gazelle, for a semi-trailer, for a truck, for a body.


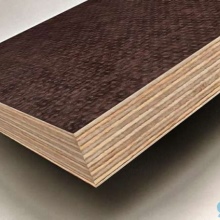
Characteristic
Before dealing with the types, use and choice of transport plywood, it is necessary to carefully study its general features. Undoubtedly, this material is close to that used for flooring, partitions and other similar applications. However, there are still noticeable differences. It differs from ordinary transport plywood by the presence of a moisture-resistant laminated layer.
Basically, such a product is placed on the floor in self-propelled vans and trailers. However, there are a number of other important areas of its use. Specific types are distinguished, first of all, by size (more precisely, by thickness). The doors and the floor are laid out from the inside with the plywood that matches the applied frame. The maximum permissible thickness is 27 mm.
In semi-trailers, products are usually used no more than 20 mm in thickness. Finally, passenger cars and river boats are sheathed in sheets with a maximum thickness of 1 cm.



Views
The best quality option for transport plywood is birch veneer. Its parts are held together using thermosetting compounds based on phenol-formaldehyde resins. Bakelite varnishes are also sometimes used. The second option guarantees excellent resistance to moisture and mechanical wear. Film faced mesh and smooth plywood with a thickness of 0.6 cm is quite widespread.
A typical solution like this:
- has a formaldehyde emission category not worse than E1;
- resistant to moisture;
- has a natural moisture content of 5 to 14%;
- has a specific gravity from 640 to 700 kg per 1 m3;
- processed from the ends;
- has a thickness difference of no more than 0.06 cm.


Sveza Titan hard-wearing plywood with anti-slip notch is popular. This grade of material is of high quality. Thanks to the non-slip surface and a special abrasive coating, both people and goods will be completely protected from possible problems. The outer coating includes corundum particles, which reliably protect against mechanical damage.
Sveza Titan has the highest slip resistance category that meets the highest requirements of DIN 51130.
The abrasion resistance of good transport plywood with mesh is at least 2600 Taber revolutions. The rolling resistance of the roller propellers of hand unloading carts and similar equipment exceeds 10,000 cycles. Determination of sustainability takes place according to the SFS 3939 standard.

Application
Floor plywood with a thickness of 24 or 27 mm is rarely used. Basically, it is needed to sheathe walls and doors. Theoretically, it is considered that the layer should correspond to the applied profile, however, such parameters fit perfectly into most options. Material with double-sided lamination is used for vertical surfaces. But mesh products are usually used for the floor of a semi-trailer or trailer.
Structures with a thickness of 1.5 to 2.1 cm are more common in semi-trailers, and not in full-fledged trailers. Plywood of this type is unable to withstand significant loads. The bottom part of a conventional passenger semitrailer can also be covered with mesh material.Plywood that is 2.1 cm thick is relatively expensive. For this reason, the main part of the craftsmen uses it precisely as a floor covering, the sides are trimmed with thinner materials at an affordable price.


Transportation of the lightest loads usually allows the use of a sheet with a thickness of 0.95 - 1.2 cm. Such designs are applicable even for boats and boats. They will help you cope with the workload of 2-5 people. In some cases, plywood with a thickness of 0.65 cm is used for the walls of vans. Such a product is even suitable for equipping isothermal vans and mobile refrigerators on wheels.
The load on the floor must be taken into account. This is not about the absolute loading of the transported goods, but about the load created by the actions of the loaders in the semitrailer. Normally, the floor is calculated for the value of such a load from 7100 to 9500 kg (in terms of one axle). However, a competent calculation is only possible when taking into account the existence of even heavier loaders.
In addition, in the actual use of plywood, one has to pay attention to the diameter of the wheel and its width.


A separate topic is the use of transport plywood in a gazelle and other small minibuses. You can even make a laminated floor with your own hands, without resorting to professionals. A simple laminated product is better than a specialized one (designed specifically for cars) already due to a much more affordable price. Also this coverage:
- allows you to get excellent strength and wear resistance;
- cut into exact dimensions without problems;
- flexible enough (which is important when wall cladding);
- does not swell and does not suffer in any other way from moisture;
- not prone to delamination;
- relatively resistant to fire.


In addition to plywood, you will need:
- frame slats;
- composition for corrosion protection;
- mastic for plywood materials;
- metal fasteners;
- aluminum corners on the threshold;
- strip in the form of the letter T (for joints).


First of all, a slatted crate is created. Already on it and screw the flooring. Thick plywood strips can serve as a replacement for the slats. The frame can be attached by making holes in the body. These places are certainly treated with a composition that inhibits metal corrosion. Next, the slats are fixed to the floor, the wheel arches can be closed with a frame, although this is not necessary.
Plywood preparation is greatly facilitated by using a pattern. It is carefully transferred onto sheets. Shaped cuts are usually made with a small-toothed file. Usually the sheets are fastened using self-tapping screws. But for the greatest reliability, aluminum blind rivets can be used.
A homemade floor for a truck body can be mounted on small hinges and self-tapping screws. Some people choose sheets with a thickness of 0.5 cm for a truck (for a cargo van), where it is planned only to walk, but not to roll any heavy carts.


Exactly the same material will fit in the trunk of a passenger car. In this case, the workpieces are usually cut with an electric jigsaw.
It is also recommended to take:
- for floors - plywood F / W;
- on the front wall - F / F grade with a thickness of 2.4 - 2.7 cm;
- for wall cladding - smooth plywood F / F 0.65 cm thick.
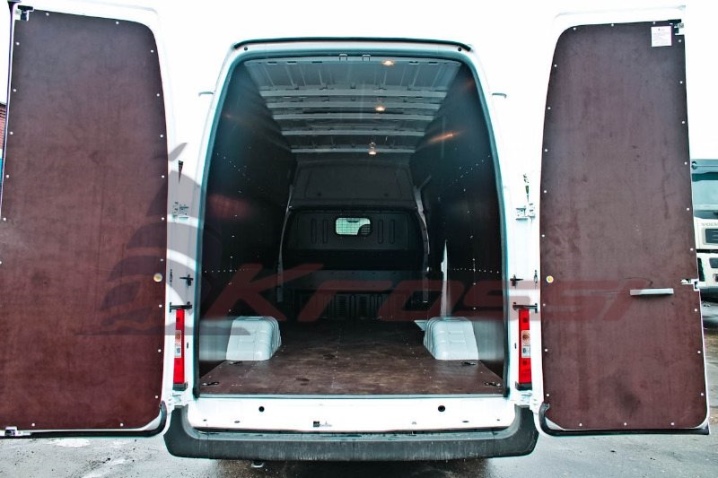
Choice
Picking up automotive plywood is not as difficult as it sounds. In most cases, bodies are formed from FSF. Birch specimens are preferred; coniferous blanks are occasionally used. Additional lamination is carried out for situations where special water resistance and an attractive appearance are needed. It must also be understood that laminate may not withstand constant walking and handling, so it is better for walls than for floors.
In an extreme case, a FSF is placed on the floor with the grid up. The dimensions of the plywood are matched to the dimensions of the vehicle. The most common choice is 4/4. But at the same time in constantly exposed places it is preferable. It is important - according to GOST 3916.1-96, predominantly sheets are produced with a thickness:
- 3;
- 4;
- 6,5;
- 9;
- 12;
- 15;
- 18;
- 21;
- 24;
- 27;
- 30 mm.

For information on how to sheathe the cargo compartment with plywood, see the next video.
The comment was sent successfully.