We make machines from plywood with our own hands

Making plywood looms with your own hands is not as difficult as it seems. It is imperative only to study the basic drawings of homemade CNC machines. A skillful approach allows you to make wood lathes with your own hands and other homemade products of various profiles.

Peculiarities
Experienced specialists have known for a long time that home-made plywood CNCs in some cases are not inferior to full-fledged factory-made metal counterparts. Such structures are used, of course, only where there are no significant mechanical stresses, strong vibrations, heating and the need to remove heat with water. The technical qualities of plywood machines may well be at a decent level. At the same time, the cost of such equipment is sparing.
Attention: such systems are intended for private use only. The plywood machine is not useful as a full-fledged production workplace. Before doing it, you need to soberly assess your abilities and knowledge in the field of carpentry art. In the absence of special skills and ability to work with power tools, you will have to forget about the independent manufacture of machine tools.
In addition, you will have to carefully select the main structural material.



Design
On machines, even the least critical, should not be allowed sheets with a thickness of less than 0.6 cm. In any case, this applies to the supporting and bearing parts of the assembly. Sometimes an exception is made for casings and other lightweight parts. However, even then it is necessary to carefully weigh the pros and cons in order to give a correct assessment of the selected details. Mistakes in their selection can be fatal.
Some experts believe that a sheet with a thickness of 1 to 1.2 cm is sufficient for individual machines, for example, when it comes to a cutting table. Other experts proceed from the fact that parts of a large thickness are always needed, even for minor sections of the structure. There is also an opinion that bulky parts glued from medium-thick plywood are more effective in dampening harmful vibrations during occasional vibration. But true masters always give preference to considerations of reliability and safety. That is why they try to make the most of plywood sheets with a thickness of 19 mm or more, despite the severity and significant prices.



But you should not focus on only one thickness. It is imperative to take into account the type of original wood. Coniferous wood is lighter and softer, it is used mainly for minor nodes. Hardwood veneer is more expensive, and yet it is used more often. But the differences in the chemical composition of adhesives and the level of resistance to moisture practically do not play a role; in most cases, plywood of the FC grade is quite enough.
What's more important is the veneer category. An increase in the number of knots threatens cracking and delamination. Experienced professionals try to take sheets of the second grade and higher. You shouldn't try to buy very cheap unpolished material. It is almost impossible to bring it to the required parameters in artisanal conditions.
Fully sanded workpieces are also easier to glue.

A 4-in-1 plywood machine can be considered as an optimal handicraft model. This design implies the use of a 54x32x88 cm box and a 65x98 cm table. Plywood for these parts is 10 and 18 mm thick, respectively. The section of the disc grinding unit will normally be 18 cm. To work on wood, a different apparatus is needed, the types differ sharply, namely:
- sawing on the basis of a hand-held circular saw;
- jigsaw;
- using a drill;
- universal model, suitable for hanging various attachments.



Homemade options
It is quite possible to make a decent lathe on the basis of plywood. For work, you will need, in addition to the material itself, the following elements:
- glue;
- circular saw and miter saw;
- pencil or marker, ruler (for marks);
- fixing clamps;
- bearings, paint, screws, screwdriver;
- metal plate, electric motor and pulley;
- a number of other details.


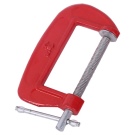



To form the base of the machine, plywood with a thickness of 1.2 cm is used. After cutting and gluing the blanks, the edges are butted, and the grooves are used to install the racks. The headstock is also made of plywood, it is necessary to drill a hole in it for the bearing. Some nuts and washers can be glue-mounted. The width of the platform and the guide part must match, and a well-made platform with clamps moves freely in two planes.
The manufacture of tailstock and headstock is no different. They both require special protection. You need to mount the power drive on a board connected to the base with a hinge. To make a spindle, you need to weld two nuts in a washer, and then make "teeth" in the nut. The machine must be painted.


Of course, you can also make a drilling machine from plywood. Since it is usually designed for relatively small workpieces, plywood sheets 1 cm thick can be used. All parts must be fitted as tightly as possible so that there are no visually noticeable breaks. Important: sheet material does not tolerate rough mechanical stress, so joining parts on nails and self-tapping screws would be a bad idea, only spikes and grooves can be used, and sometimes PVA glue for maximum hardening.
If you plan to drill other plywood blanks using a plywood machine, you need to provide a place for lining another sheet. Otherwise, the processed products may crack and even split. The coloring of the drilling machines is not very justified. They are exposed to very intense vibration, thermal and mechanical stress. But the application of a primer is very useful, especially in workshops without heating.
It is also possible to assemble CNC milling or woodworking machines. The path of the machining part (as in other types) is calculated along three axes. If there is not enough space in the workshop, versatile stands can be used to accommodate a wide range of tools. Typically, the working area is 60x90 cm with a vertical stroke of 25 cm.
But if you do a little less, then no problems usually arise.


There are two main schemes for the device of any home-made plywood looms. In one version, the table moves, and the portal remains stationary, in the second, the roles change. The first method simplifies the design, but is suitable only for very small work tables. Therefore, in practice, the approach with the movement of the portal and the stationary table is much more often used. But even in the second scheme, there may be particular variants.
First of all, they relate to the use of a single central drive or two lateral drives. The 2-drive version is suitable for relatively bulky structures. It minimizes the risk of the portal skewing relative to the guides. Moreover, the entire assembly has excellent rigidity. The size of the processed area is determined by the tasks to be solved.
The larger the machine, the more expensive it comes out, and besides, it is easier to correct mistakes on small models.



It is often believed that the geometry of the portal, the proportions of the distance between the axes and the working guides, the gaps between the bearings can be calculated only taking into account the strength of materials and precise mechanics. This is largely true, but the basic points are available even to non-specialists, namely:
- reducing the clearance above the table increases the rigidity of the structure;
- the axles should also be made stiffer and not too long;
- if possible, widen the gap between the guides along the X axis to reduce abnormal twisting;
- the center of gravity of the portal must correspond to the point where the cutter is located and at the same time be between the bearings of the Y axis (because of this, the vertical struts are often bent backward);
- it is required to use only ball screw drive screws, which give the smallest backlash;
- the screw must be equipped with a pair of independent bearings and connected to the motor through a flexible coupling (then a balance of simplicity and quality is achieved)
- assembly of all key parts can be carried out on box spikes (this is much more aesthetically pleasing than nuts bulging in all directions).

How to do it yourself?
There is no particular need to look for ready-made drawings. You can build on the schemes of metal machines. Anyway, each such product is unique and is optimized for specific tasks, for the personal needs of the owners. However, it is necessary to pay attention to the exemplary photographs. Plywood machines can only be done properly with a quality power tool. If sheets up to 1 cm thick are sawn by a jigsaw, then thicker ones are usually processed with a circular or circular saw. However, advanced jigsaws can also cope with cutting plywood sheets up to 2 cm thick.
A hand cutter will help to select the grooves and holes. Move the tools smoothly to minimize chipping. The same is achieved using plain tape. After final assembly, all surfaces and faces need to be sanded. As a soil, you can use a mixture of water and PVA in equal proportions.



You can learn how to make a belt sander out of plywood with your own hands from the video below.
The comment was sent successfully.