All about HDF panels
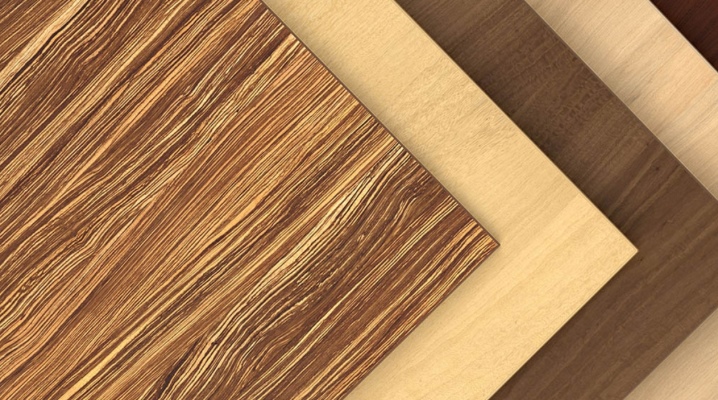
Today, finishing materials are presented in a huge assortment, while HDF panels are in special demand. They are highly efficient and easy to install. The material is widely used for the decoration of rooms, with the help of it you can create an original design.


Peculiarities
HDF panels are a popular facing material that is produced in the form of dense slabs. The abbreviation HDF originated from the English expression High Density Fiberboard, which means "high-density fiberboard" in Russian. The sheet panel has a standard size of 2070X695X3 mm, it is produced from the scraps of the array, which are cleaned, dried and crushed. After that, the mixture is formed and sent to pressing. The production of panels is completed by grinding and decorating (an image is applied to the front side of the material and varnished). The main advantages of HDF panels include:
- good resistance to various influences (when fat, boiling water, steam, water and dirt get on their surface, the decor continues to retain its original appearance);
- strength and durability - experiencing high loads, reliably serve up to 15 years;
- environmental friendliness - the material is produced only from natural raw materials and does not contain toxic substances in its composition;
- a huge selection of designs - the panels have different colors and decor, which allows them to be used to decorate any interior;
- ease of use - the material is easy to clean and does not require special care;
- quick installation - to install the plates, it is enough to cut them, after which they are fixed to the surface.


Besides, HDF panels have anti-corrosion properties. As for the shortcomings, there are practically none, except for the high cost. The price depends on many factors, it is usually increased by photo printing, which is made to order. When choosing this finishing material, you need to take into account the manufacturer's reviews, since on cheap panels, over time, the top layer of varnish turns yellow.


Comparison with other materials
HDF finishing boards are sometimes confused with MDF panels. Despite the fact that these 2 types of materials look similar in appearance, there is still a difference between them. High-density HDF has a thickness of no more than 3 mm, while MDF has an average density, it is produced with a thickness of up to 6 mm. Fiberboard is safe for health and moisture resistant. In the manufacture of MDF panels, various chemical additives are used, and they swell quickly when exposed to steam or water.
If we compare the decorative material with fiberboard, then it is in many ways superior to fiberboard, since it can withstand heavy loads. The finish made with HDF panels does not undergo deformation, which cannot be said about fiberboard, which can quickly break or crack.

Where are they used?
HDF wall panels have been very popular in recent years, since they not only have high performance properties, but also allow you to create an original design in the premises. Most often, this finishing material is often used in certain areas.
- Furniture manufacture. The panels can be used for the manufacture of hull structures.
- Decorating surfaces. The panels are suitable for wall cladding in the kitchen, they can be used for covering a kitchen apron, and for skinning.And also the material is used for lining the ceiling, the plates are installed on a pre-assembled crate. HDF with imitation film imitating expensive wood species is often installed on one wall in a living room or a combined kitchen with a dining room for zoning the space.
- Manufacturing of doors. The panels are applied to the frame to decorate the front surface. In addition, the material is often mounted externally on front doors.



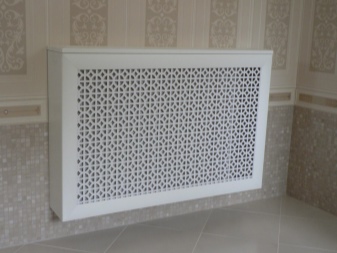
HDF panels are also in demand when laying floors, acting as a rough base. They can also be used to remove unevenness on other surfaces (ceilings and walls). Low weight and strength make the material indispensable for the interior decoration of various vehicles.


Species overview
Sheets are available on the market in several varieties. Polished slabs are often used in finishing works; their smooth surface, if desired, can be coated with transparent varnish or painted. From such panels, perforated panels are made in workshops and a base for flooring. Sanded HDF panels are also used in the production of cabinet furniture, they are used for making the bottoms of drawers and walls of nightstands, cabinets.
Decorative panels, on the surface of which several layers of colored varnish are applied, are also in great demand. They are also produced with a natural wood imitation. Surface cladding with such material gives the interior an exquisite look.
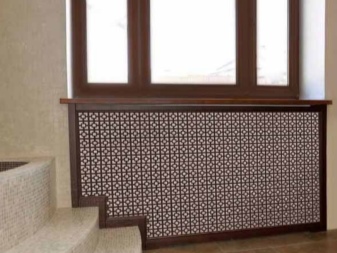

HDF panels, made on the basis of wood with a laminated coating, deserve special attention. They are well suited for decorating interior doors and decorating furniture, kitchen apron. The rusticated surface of the slabs looks especially beautiful. The panels can be used to cover the walls in the living room and bedroom.



Design options
Wood fiber panels are available in a variety of decors, while models with photo prints and patterns are appreciated. The application of images is carried out by means of ultraviolet printing; it can have several types of designs.
- Monochrome option. For the panel, colors are selected and applied that correspond to the interior of the room (a two-color range is allowed). Usually, dark shades are used for the background, and light shades are used for the images.

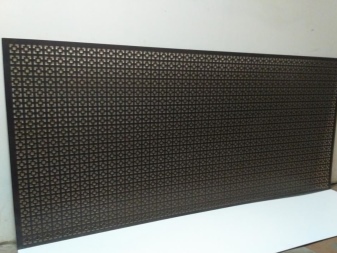
- Full color design. The drawing is made rich, multi-colored, which gives the slabs a special look.

- With 3D effect. The panels are characterized by a three-dimensional pattern. Landscapes and fruits are usually depicted on their surface. For the best effect, HDF is covered with several layers of varnish.

Laminated boards are also often found on sale, they are covered with a synthetic film that imitates a natural solid wood. They are characterized by strength and moisture resistance, therefore they are well suited for wall cladding in the kitchen, bathroom and toilet.

Installation rules
HDF panels are a versatile finishing material with which you can independently transform the interior of the premises. In order for the decorative finish to fit perfectly into the style of the room, when choosing plates, you need to take into account their color and texture. Installation of HDF panels is simple, so everyone can handle it.
The installation of the material is carried out in the same way as the installation of other finishing boards. They can be attached to the base by gluing or fixing to the crate with self-tapping screws.
It is worth noting that the last installation option is usually used when creating boxes (for masking communications) or for decorating walls that have a large unevenness. To properly fix the sheet material on the surface, you should adhere to some rules.


Installation on glue
Before starting finishing work, you need to prepare a tool: a drill with a milling cutter, a plumb line, a pencil, a meter, a grinder, a level and a screwdriver. Then the workplace should be prepared. For this, furniture is removed, the walls are cleaned of dust, dirt, old finishes and treated with a primer. In order to properly cut the panels, they are measured against the wall, then measurements are taken, places for switches and sockets are marked. Cutting the panels must be done carefully, as the material can crumble. The holes for the sockets are cut with a cutter.
The adhesive is evenly applied to the material from the wrong side, it is important to ensure that no cavities form, they can impair adhesion. The edging profile is attached to the base with self-tapping screws, the panel is fitted under it. The decorative material must be pressed tightly to the wall until it attaches to it, the protruding glue residues are picked up with a mallet.
To ensure a secure fit, it is recommended to additionally install the corner and connecting profile. All joints are treated with a sealant. During installation work, one should not forget about checking for irregularities, since it is easy to eliminate defects during the installation process, and after its completion it is problematic.


Installation with self-tapping screws
This method is considered simple and fast. Preparation and cutting of slabs is carried out in the same way as when installing the material on glue. The only difference is that in this case, holes are first drilled in the wall, then dowels are hammered into them and the panels are screwed on. The places where the dowels are driven in must exactly coincide with the places intended for screwing in the screws.
Many craftsmen, instead of ordinary self-tapping screws, use special dowels, called "quick installation". For installation in finishing panels, holes are drilled and fasteners are hammered. To hide the caps of the screws, special plugs are used. They need to be planted on a sealant. The installation is completed with the fastening of the edging strip, it will provide strong fixation and protection of the joints from moisture and dirt.

Installation on a crate
This method is usually used when the walls are too uneven or there is a need to hide communications under the finishing. The lathing is made from both profiles and wooden battens. This type of installation does not require preliminary preparation of the base, that is, the old cladding can be left. Measurements and cutting of material are carried out in the same way as in the above installation methods.
The slats should be prepared before starting the cladding. They are covered with linseed oil and dried. This is necessary to improve the performance of the wood. The slats are fixed on self-tapping screws, a distance of 400-450 mm is made between them. They should be positioned vertically and horizontally. The installation is completed by processing the joints with a sealant, this will provide the cladding with better strength.

The following video tells about HDF panels.
The comment was sent successfully.