How is plywood made?

Plywood, without exaggeration, can be considered one of the most popular and demanded materials all over the world. Its huge advantage is that it can be perfectly processed even without complex factory equipment. - almost any skillful owner can work with it. You should be aware of the features of the product and the methods of its production.

Peculiarities
Out of inexperience, many people think that plywood is a kind of uniform standard of material, but in fact it can be different depending on the method of production and useful purpose. This material is classified according to the type of processing.
- FC... Such sheets are able to withstand moisture. The plywood layers are held together by urea adhesives. The use of sheets is very wide: from underlays for flooring in high traffic areas to wall cladding inside buildings, the production of furniture and boxes.
- FSF... A kind of material with even higher moisture resistance, which is achieved thanks to the phenol formaldehyde adhesive. FSF is a more reliable and durable product that is suitable even for roofing work.
- FBS. Such plywood is made by impregnating wood with a special resin that can dissolve in alcohol. Such processing contributes not only to improving the moisture-resistant properties of the sheet, but also immunity to temperature extremes. FBS cannot be called incombustible, but it resists fire better than the above-described "relatives".
- FBA... An excellent choice for those who care about the ecology of the environment: the production uses safe glue on albumin and casein. Natural materials, however, create a noticeable disadvantage: such plywood is afraid of moisture.
- BV... In all respects, it is similar to FBS, but somewhat inferior to it in terms of moisture resistance.
- FOF... The same FSF, but pasted over on the outside with very thick paper, which is impregnated with resin.


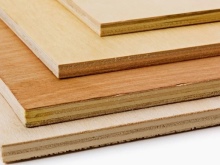
And also plywood sheets are classified according to the presence of defects on the veneer from which the material is made. For this, Roman numerals from I to IV are used, where I grade is the best and with the minimum number of defects, and grade IV allows continuous coverage with flaws, provided that the edge relief does not exceed 5 mm. At the same time, for facing work and in order to save money, many manufacturers make one side noticeably better and more even than the other. In this case, the grade is indicated with a fractional number, for example, 2/4, where one side is grade II, and the other has flaws.

The main types of pressing equipment
Although plywood processing does not require a large amount of sophisticated equipment (and therefore the material is widely used by craftsmen at home), the production of such sheets is technologically much more complicated. The process uses a large number of different tools:
- calibration machines and cleaning of wood raw materials, various trimming units, and sometimes special baths, if the wood must first be softened;


- automatic machines for peeling, used for cutting wood into veneer;


- special knives, including the guillotine type, due to which the veneer tape is cut into fragments of the required length according to the size of the future sheet, and today's machines can not only cut, but also independently stack such pieces;

- tunnel dryer - it is necessary for the wood veneer to dry correctly, without deforming during the drying process;


- glue production unit, which in most modern modifications not only kneads the adhesive, but also applies it to the veneer surface;

- gluing machines - the veneer is aligned according to the dimensions and shape of the future sheet, the layers are sequentially coated with glue and superimposed on each other;

- pressing machines - in most industries, hot and cold presses are used separately;

- fitting equipment - allows you to remove the excess, so that the almost finished sheet is fully consistent with the declared length and width;

- various equipment for possible post-processing - used only if some unusual sheet is required, for example, perforated or special color.

Manufacturing process
Plywood production technology consists of many successive steps that can be mastered by the efforts of a relatively small enterprise. Let's take a closer look at how rounded and relatively thin logs turn into flat sheets of a fairly large size.

Materials (edit)
Plywood raw materials are far from the last importance in the question of how high-quality the sheet will turn out. Each type of wood used has its own performance characteristics, so different materials are made from different woods.
Plywood is made from both hardwood and softwood, some types of wood are used most often.


Birch
Perhaps, the optimal solution for the production of plywood sheets - It is not for nothing that many manufacturers are praised for their birch products. Such wood is very dense and durable; even a thin veneer does not break or crack in it.
Thanks to these properties, the resulting plywood board cracks much less during any processing, it can be cut and drilled without the risk of spoiling.

Alder
If the material is planned to be used outdoors, and it will inevitably be exposed to regular exposure to a large amount of moisture and temperature extremes, then alder veneer, which perfectly resists drying out, will come in handy. Such raw materials do not deform, regardless of any weather conditions. At the same time, alder wood is quite expensive, so you can hardly find plywood made of it in its pure form.
It is present as an additive to plywood made from cheaper wood species.

Linden
Such wood is good because it is found quite often even in those regions where there are no dense forests, while linden veneer in its properties is similar to the varieties described above.
It is relatively easy to cut a linden log into veneer - the sheets are smooth and neat, they do not crack or bend.

Conifers
Among conifers the most common pine and spruce are considered the most suitable for the production of plywood sheets, although fir, cedar and larch are also sometimes used. If we talk about the quality of wood, then coniferous varieties are usually criticized: in logs, annual rings differ inhomogeneity, therefore the veneer often cracks and peels unevenly, which is especially the "sin" of pine. This structure of plywood predictably makes it less durable, but the product is still attractive in cases where a heavy load is not expected on the structure. This plywood weighs much less and is easier to transport.
In addition, coniferous trunks are naturally impregnated with various resins that repel pests and prevent mold.

Each type of wood has both advantages and disadvantages. To solve the problem, many modern manufacturers make a single sheet of several types of wood, alternating layers of veneer.
Gluing
A full-cycle enterprise rarely buys veneer just to glue it - processing starts with logs. First of all, such raw materials are cleaned from bark and cut off knots on a special automated line. After that, the trunk is cut into fragments that are convenient for subsequent veneering.
During the delivery process, the wood may acquire an uneven moisture content, and the veneer will be cut unevenly. To avoid the problem, pieces of wood are soaked in baths with water, to which substances that improve the useful properties of wood are added. After that, the pieces are sent to a peeling machine, where the veneer is removed from their surface with sharp blades.


In most cases, veneer is either strip or sheets. In this form, it is cut into fragments that are convenient for the formation of products of the planned size. The cut veneer passes through a special conveyor, where it is blown with hot air and acquires a moisture level of no more than 4–6%. After that, most often manually, the veneer is sorted according to the size of the pieces.
Then proceed directly to gluing. The adhesive is applied only to the layer that will be inside the thickness of the sheet, its "facing" is applied from above, without being smeared with glue. Depending on what thickness of the product is required, the manufacturer can add more outer layers, but at the same time the one that will be the core in the next stage is always coated with glue.
To further compact the material, it is pressed... The pressing method depends on the type of glue used: it is either 6 hours at a stable temperature (cold press), or rapid compression with heat and high pressure (hot press). Lamination and sanding complete the production process.


Manufacturers in Russia
Plywood remains a worthy competitor to plastic panels, and at the same time enjoys wide consumer demand. Many characteristics of the material directly depend on the good faith of the manufacturer. For example, plywood from Asian countries is not very popular in the Russian markets, since it is of low quality.
The process of making the product is relatively simple, and Russia is exactly the country where there is no shortage of mainly raw materials in the form of wood, therefore we actively produce plywood ourselves. So that the reader understands whose product it is worth paying special attention to, we will single out several of the most popular factories.
- Syktyvkar Plywood Factory. The Komi Republic is one of the most striking examples of the Russian region with a huge amount of forests, therefore it is not surprising that high-quality plywood is made here. This manufacturer has its own segment of goods, from which he prefers not to get out, namely: large-format plywood sheets, which are actively purchased by furniture manufacturers.
The plant understands that not only large factories will work with their products, therefore part of the plywood is deliberately laminated.

- OGK Sveza. The group includes 6 companies that together are able to provide the consumer with the widest range of various wood products, and even in different regions of our vast country.
In the model series of plywood, you can pick up sheets for any needs, but craftsmen especially highly value Sveza birch plywood.

- GC "United Panel Group"... Another association of companies engaged in the massive supply of wood products to the market. Due to the scale of production, it can offer the buyer a choice of a huge number of different sheet options: among the standards there are 27 formats and 3 dozen solutions in thickness.
As in the case of the previous manufacturer, the main specialization of the company is sheets made of birch veneer, but the film faced plywood of this brand is also highly valued.

You can watch a video overview of the plywood production process below.
The comment was sent successfully.