Varieties and use of plywood for flooring

Knowing the types and order of use of plywood for the floor allows you to establish which type of material is better to choose. It is necessary to understand the thickness of the sheets and the specific types, with the features of moisture-resistant grooved film faced and other types of plywood. It is equally important to figure out exactly how to lay it. In this article, we will consider the types and uses of plywood for the floor.

Advantages and disadvantages
The unconditional advantage of the plywood floor is its affordable price. But it is important to carefully check whether the parquet plywood floor is really finished (if this is the option chosen). Many samples are delivered unfinished and the flooring has to be finished additionally. If the work is completed, the product will be more affordable than the cheapest hardwood boards. It is easy to use in place of traditional laminate flooring.
Installation of plywood elements on the floor takes very little time. All work is done with minimal effort in a matter of hours. The most difficult manipulation is grinding, laying, gluing (option - nailing), painting (other finishing options) of the floor. If the floor is quite large and the configuration is very complex, it will sometimes be necessary to work for 2 or 3 days.
However, the problem is only in painstaking, but not in complexity.


Plywood, which is important, differs in flexibility of use. It can be painted with a wide variety of paints. Or you can - abandon the usual boards and use squares or even a more intricate shape. And even if you don't like the result, you can always put on a new coating option. The maximum simplification of work is also possible - plywood blanks are simply ordered ready-made and asked to cut them exactly to size.
Plywood is sold almost everywhere, in any hardware store - it is not necessary to go to a large shopping center or a hypermarket of construction goods. The variety of its options is due to the thickness and grade of veneer. As a result, it is not so difficult to find a floor covering with ideal characteristics. A multi-layer device would itself be an advantage of the material. Thanks to this property, it is quite strong and serves for a long time.
Quality plywood is quite stable in almost any environment. It can be used regardless of the climate in a particular area. It is also safe in environmental and sanitary terms (except for some harmful impregnations). However, one must understand that even the best plywood is relatively weak. Frequent and prolonged walking, falling of various objects, installing and rearranging heavy cabinets are not about her.
Traditional planks and bamboo are much stronger.


Views
But both the disadvantages and advantages of plywood for the floor should be discussed more specifically, because it comes in a variety of types and designs. The most important gradation is given in GOST 1996. The following main categories of plywood sheet are indicated there:
- E - a special group that does not have any deformations;
- I - products with cracks and other violations no longer than 20 mm;
- II - cracking up to 20 cm in length, small wood inserts are allowed;
- III - a typical slab has a maximum of 9 defects (with a cross-section of up to 6 mm), a maximum of 10 wormholes per 1 m²;
- IV - the lowest quality material, sheets may contain wormholes up to 45 mm in diameter, defects along the edge by 4–5 mm in depth (in addition, full coverage of the surface with intergrown knots is allowed).
In theory, the choice between these varieties is unlimited. But experts believe that for subfloors, it is better to use a product of groups 2–4 (this will be more economical). But the front flooring is most correct to make from plywood of level I or even E. Of course, technical performance also plays an important role.
So, moisture-resistant plywood flooring can be used in the kitchen, to a lesser extent in the bathroom and toilet, when designing approaches to the pool.

The grooved type of material deserves special attention. During the manufacturing process, the raw material is pressed hot. This allows for a relatively high strength and ability to withstand significant loads. Sound and thermal insulation is also improved when compared to conventional options. The main advantages are as follows:
- ease of collection and dismantling of the flooring;
- precise connection with a tongue-and-groove lock;
- the ability to partially remove the flooring and replace the material, lay new communications without violating the overall integrity;
- no need to use complex devices and special tools.
But grooved plywood isn't the only option. The laminated variety is quite widespread. These are always multi-layer products, thanks to the addition of plastic, they do not absorb water at all. Therefore, rotting, swelling, the formation of mold - at least as long as the protective layer is intact - are completely excluded. The PVC layer, which is important, also increases the aesthetic properties of the floor covering.
It can be painted in the most intricate way without any problems.

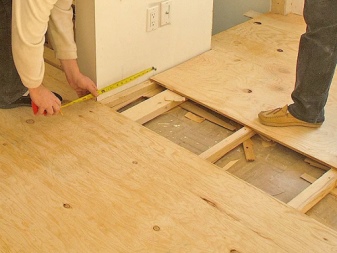
It is very easy to imitate even elite woods without extra expense. It should be borne in mind that some types of film faced plywood are not covered with plastic, but with a paper sheath. There is not much difference in aesthetics. Due to the impregnation of the outer layer with specially selected resins, it provides good resistance to moisture and effective suppression of bacterial colonies.
Extruded plywood can already be considered a real classic. Strictly speaking, it should not be singled out in a special form, since pressure treatment is practiced in any plywood production. It should not be confused with the following materials:
- Fiberboard;
- Chipboard;
- OSB;
- Particleboard.


Stamps
FBA
This type of plywood is produced by gluing the veneer with a special albuminocasein mixture. From an environmental point of view, FBA is an impeccable product, but it cannot be used everywhere. To maximize the use of such plywood is hampered by its insufficient moisture resistance.
You can only meet such material in dry rooms.

FSF
Such a brand means sizing with a resinous composition based on phenol-formaldehyde. Such processing guarantees excellent performance properties. The material will be mechanically strong and practically wear-free. The moisture resistance is quite high. FSF is used in the construction industry, industry, and is often purchased for roofing work.
However, the intense release of formaldehyde is extremely hazardous to health, therefore, FSF should be used only in non-residential buildings.


FC
This option involves joining veneer using a carbamide compound. This technology is much better suited for various indoor environments. Plywood with urea glue is very durable. The level of safety is sufficient for use in furniture, so it is also suitable for the floor.
However, the danger of excessive moisture must be taken into account.


FB
In this case, the veneer is saturated with bakelite-based varnish. This solution dramatically increases the resistance to water ingress. The FB slab can be safely used even in tropical and subtropical regions.The thickness of the workpiece is usually small, since insulation is not provided. FB is also suitable for floors in laboratories, kitchens, workshops and other places where exposure to aggressive substances is likely.

BS
In this case, treatment with a bakelite-based composition is also used, but not with varnish, but with glue. This veneer is sometimes called aviation veneer, since it was previously used in the production of aircraft and river, sea vessels. This material is very durable and perfectly tolerates contact with moisture. Harmful fungi do not grow in it.
It is not difficult to bend the BS veneer in an arbitrary way.
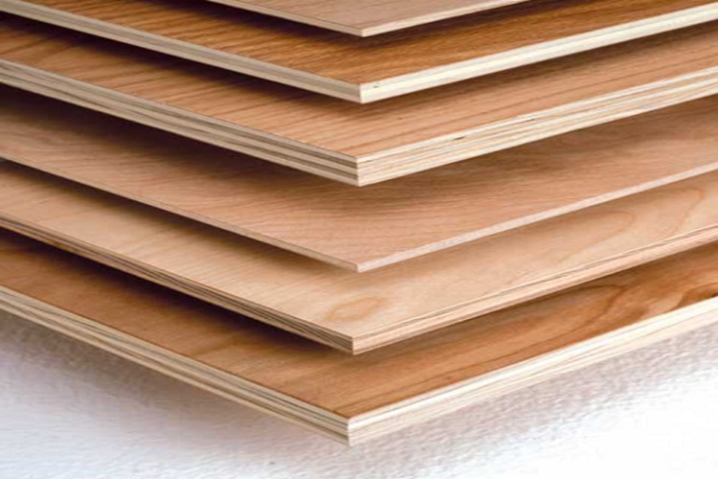
BV
This type of plywood is glued with a water-soluble bakelite solution. Plates obtained in this way are not sufficiently resistant to water. But their strength is at a decent level. Bakelite plywood of any type must comply with GOST 11539-2014... There are no specific restrictions on the size, so it is necessary to cover this topic in more detail.
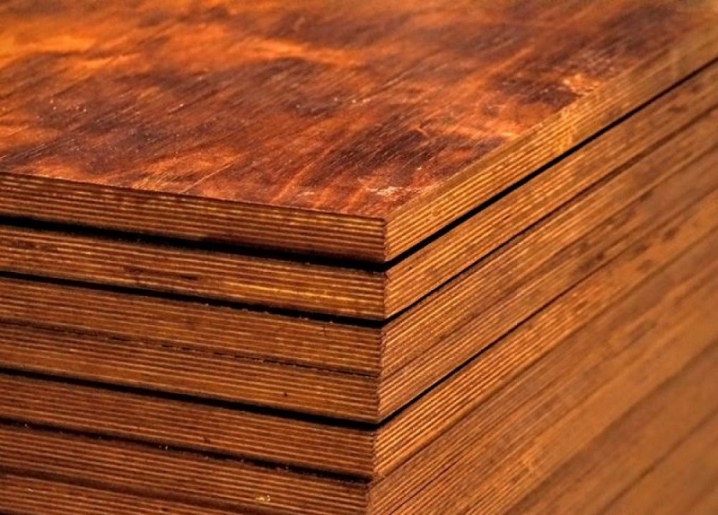
Dimensions (edit)
The optimum plywood thickness should be selected individually. When making a sub-floor, it is recommended to use a material not thinner than 12 mm. In this case, the front finishing can be successfully performed with 10 mm products. Laying in two layers is allowed, but it must be clearly understood whether such a step is needed. Thick plywood (up to 25 mm) is preferable for workshops, factory halls, shopping centers and cinemas, and other places with a high floor load.
The smallest number of layers in plywood for flooring is 3 layers. Sheets with a thickness of 12 mm are made from 9 layers. The 16 mm product consists of 11 glued layers. It is not recommended to lay plywood less than 3 mm thick on the floor. For parquet with a thickness of 16 mm, a substrate with a layer of 1 cm should be used, for a thicker one (from 17 to 20 mm), a support of 1.2 cm is needed, and when using large-sized parquet, you will have to lay sheets no thinner than 1.5 cm.
Laying on logs implies the use of even thicker plywood - at least 18 mm. In the practice of domestic manufacturers, 2 types of plates are widespread: standard and enlarged formats. Typical design is a square sheet with an edge of 1525 mm. Rectangular products have a size of 2440x1525 mm.


Large-format slabs sometimes reach a length of 3660 mm. Typical FC dimensions (in centimeters):
- 152.5x152.5;
- 127x152.5;
- 122x152.5.
FSF is most often cut into plates and sheets:
- 150x300;
- 122x244;
- 125.2x305;
- 125x250 cm.

How to choose?
To figure out which plywood is best for your home, you need to pay attention to the following points:
- type of coverage and features of the room;
- safety requirements (the safest material is selected for the nursery);
- study certificates from manufacturers;
- buy a product of the FC grade in the rooms of permanent residence;
- focus on moisture content (in high-quality veneer no more than 15%);
- select the level of strength according to your needs;
- remember that large format slabs are more difficult to mount;
- number all copies in the stack.
If the floor covering is slightly deformed, 6 mm thick material can be dispensed with. It is possible to cope with the differences in this way, but the relief will still show through. Good leveling is achieved with plywood with a thickness of 9 to 15 mm. If logs are already laid out, you will have to take into account their width.
And of course, the thickest and strongest plywood is placed under the wardrobe or sofa.
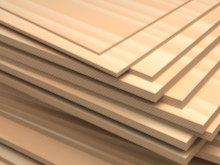


How to lay?
To use floor plywood correctly, it is laid out and carefully adjusted. At the same time, we must not forget about the gaps separating the different parts. They try to lay the sheets on top of the screed with some shift. It is very bad if all four seams are in one place. Having prepared and numbered the plates, you need to start work immediately.
It is quite possible to put plywood on the sub-floor under the linoleum. The material itself is recommended to be treated with an antiseptic. The rough base is cleaned and dried. All rotten areas are removed and replaced. With a significant change in geometry compared to the norm, you will have to change the entire rough base.
It is recommended to choose such sheets so that they fill the entire space as completely as possible.... Narrow segments are only suitable for the initial segments in a row, located at the walls themselves and subject to light stress. Before cutting the sheets, it is advisable to draw up a diagram. Important: the same approach should be used when laying plywood under a parquet board.
The sawn workpieces are carefully checked so that there are no chips.



Beautiful examples
This is what one of the options for a high-quality plywood floor looks like. Multi-colored "boards" with an original pattern look very good.

And this is plywood flooring. The combination of dark brown squares and light wood trim is delightful.

But plywood parquet can look like this.

You can find out how to properly lay the plywood on the glue with your own hands below.
The comment was sent successfully.