How to replace epoxy resin?
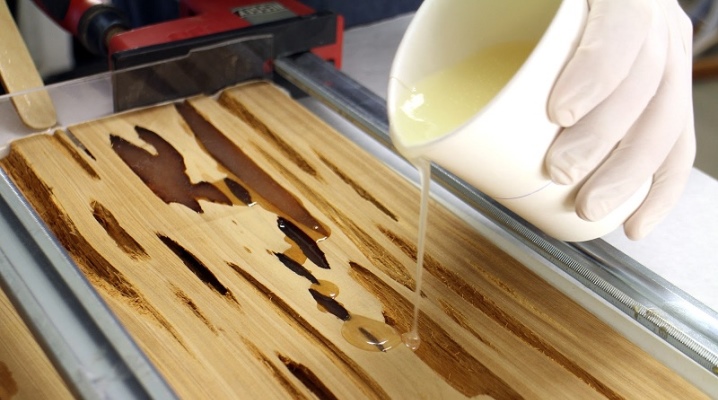
What can replace epoxy resin is useful for all art lovers to know. This material is widely used in various types of carpentry, needlework, and decorative items. What analogues exist for filling and crafts, how to find a cheap alternative to epoxy at home - you should learn about all this in more detail.



Major replacement factors
There are many factors to consider when choosing a material to replace epoxy with. Not every material is suitable for pouring or creating a strong connection. The main difficulty in finding an alternative is that the epoxy resin in its original form is an oligomeric compound. In order to provide it with a transition to a polymerized state, a hardener is required that starts the necessary chemical processes. The final state of the material largely depends on the proportion of these ingredients: whether it becomes rigid or will have an elastic consistency and properties close to rubber.
It is necessary to look for a replacement for epoxy in cases where the master has manifestations of an allergic reaction to this oligomer. In addition, resin is not suitable for delicate work involving precise and complex shapes. It will be difficult to achieve accuracy here. Do not use epoxy compounds when repairing food products, as well as those intended for contact with children (toys, dishes).
Sometimes the search for a replacement has purely everyday reasons: the lack of nearby construction stores, insufficient funds - in this case, it is easier to find an option available to any master without additional searches and investments.


When choosing an alternative to epoxy, it is important to consider a number of requirements that a chemical compound must have.
- Possibility of polymerization with a transition to a new state of aggregation. Not only oligomeric compositions have such properties.
- Resistant to wear and tear. The replacement must be able to withstand mechanical and other stresses while remaining durable.
- Chemical resistance. After polymerization, the material should not react with acidic and alkaline media, change its characteristics under their influence. Moreover, in acetone or other esters, it should dissolve without giving a precipitate.
- High moisture resistance. Impermeability to water and other liquids is a great advantage of epoxy.
- Lack of hazardous vapors when working with the material. The composition should not contain compounds that require special conditions for working with them.
- High mechanical strength. When creating a glue line, the material must withstand significant tensile forces.
- No shrinkage and deformation. It is important that the material retains the specified geometric parameters.
All these characteristics already have epoxy resin. When looking for a replacement, sometimes you have to compromise in order to obtain results similar to the action of a universal material.
But in general, with due diligence, it is still possible to find an alternative solution.



Analogs
Finding a cheap analogue of epoxy for creativity, for pouring countertops or making interior items is unlikely to work. At home, substances that have the ability to polymerize, are distinguished by a transparent structure and strength are a good alternative. For needlework, jewelry making, the flexibility of the substitute to grinding, polishing, and other processing can also be of great importance. When forming large products - a table, a lamp - more attention should be paid to the speed of its hardening and the homogeneity of the material. Sometimes the similarity still turns out to be noticeably worse than the classic epoxy resin, but there are also examples of a successful search for an alternative.


Cyanoacrylate adhesives
These are the compositions "Titan", "Moment", well-known to art lovers, as well as superglues with instant polymerization upon contact with air. Among the obvious advantages of such adhesives are:
- transparency of the seam after polymerization;
- high bond strength;
- a variety of choices - there are heat-resistant compounds;
- moisture resistance.
There are also disadvantages. Despite the strength under static loads, cyanoacrylate types of glue are not very resistant to mechanical damage and impact. They have a limited shelf life, and the chemical compounds themselves are toxic and can cause allergic reactions.
In addition, it will not work to connect fluoroplastic or polyethylene with their help - only ordinary plastics or metal.


Silicate glue
It is sometimes compared to plexiglass, because after the polymerization is completed, the mixture actually acquires strength and transparency. Among the advantages of silicate glue are:
- extremely low toxicity;
- versatility;
- fire resistance;
- ease of preparation.
The disadvantage is the limited scope of application: for metal, ceramics, glass, plastic, textiles and wood. You can increase the properties of the composition by adding additional ingredients to it. For example, a mixture of crushed glass and asbestos gives the silicate adhesive improved chemical resistance. When mixed with milk casein, it acquires moisture resistance.
When combined with asbestos and quartz sand, it can become resistant to alkaline and acidic influences.

"Liquid glass"
A mixture actively used in various types of creativity. It has many advantages:
- hypoallergenic;
- high drying speed;
- smoothness and gloss of the finished surface.
There are also disadvantages. For example, a limited list of materials to which "liquid glass" has good adhesion. In addition, it is imperative to comply with rather complex application technology requirements.
Since "water glass" is sodium silicate, it exhibits the best characteristics when applied to glass. In this case, the surface is first coated with a thin layer of the composition. After 24 hours, it will be quite sticky - to eliminate this effect, wipe it with regular alcohol. Then you can apply a second layer. The finished coating will no longer stick, it will provide good polymerization and long-lasting gloss.

UV Gel Polish
The hardening of this composition occurs almost instantly when properly treated with ultraviolet light. In that gels and varnishes for manicure are superior to epoxy, with which they are related to a resin-based base. But such compositions have rather low strength characteristics. When struck or other mechanical stress, they quickly lose their decorative effect, become covered with cracks and chips.
The advantages of the gel polish include the ease in eliminating defects. Correction with removal of bubbles or restoration of coverage will be fairly easy to do at home. Gel polish is good for pouring molded products with small thickness - jewelry, decor items. A UV lamp and a few minutes are enough for polymerization.
Only finishing compositions are suitable for creativity - the base ones stick even after the use of a catalyst.


Polyester compounds
They also have the appearance of a resin that, after pouring, quickly gains strength and hardness. This option has many advantages, including short curing times. Hardeners are included during production.
The disadvantages of polyesters include a limited scope and the possible occurrence of allergic reactions.

BF adhesives
They are most often sold not under the usual brand name, but in the form of compositions under the Moment brand and the like. The connection takes place according to certain rules. It is imperative to dry the first layer - the primer, then apply the second, hold it for 4-5 minutes, and then press the parts to be glued with force. The reliability and strength of fixation depends on this factor.
The material has quite a few drawbacks. BF glue has a pungent smell, it is better to work with it in a respirator. The adhesive properties are also limited. Compounds of this type are poorly suited for working with glass and polished metal.
With the hot method of application, these disadvantages are somewhat leveled.

How to replace the hardener?
When working with epoxy, experienced craftsmen try to prepare an additional bottle of hardener in advance, especially if the proportions of the mixture differ from the standard ones. The reason is simple: this component comes in small quantities and runs out quickly. If this happens directly in the course of work, you can find an alternative to a ready-made catalyst among the improvised funds available at home. The simplest options are:
- orthophosphoric acid;
- ammonia (ammonia alcohol);
- benzoyl peroxide.
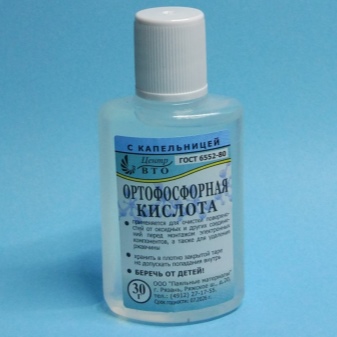

Each of these chemical compounds has the ability to accelerate the curing of the epoxy. Moreover, craftsmen easily cope with the task using ordinary dry fuel, adding it in 10% of the volume of the total mass of the substance. The polymerization will take quite a long time - about 24 hours. And you can also take advantage of the achievements of the paint and varnish industry. For example, a hardener for car enamels from the nearest store or compositions "Etal 45M", "Telalit 410".


The most effective substitute for catalysts supplied with epoxy resin are substances from the group of aliphatic polyamines - PEPA, DETA. On average, their consumption is about 10%. If the original hardener supplied with the oligomer is small, but it is available, you can dilute it with 1% ethyl alcohol.
Absolutely not suitable as catalysts for epoxy acids - nitric, hydrochloric, sulfuric. They give black foam, the material turns out to be unsuitable for use in the future.

For information on how to replace epoxy, see the next video.
Very interesting article.
The comment was sent successfully.