Enamel XB-785: characteristics, colors and rules of application
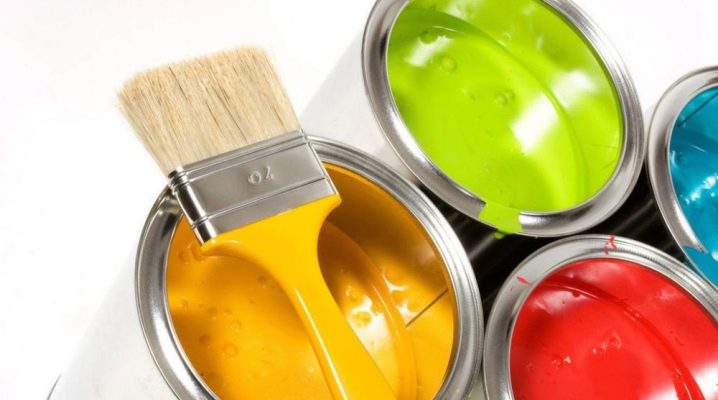
Very often used in construction and industrial production, metal parts and structures are exposed to various negative influences during operation. To protect them, you need a strong and stable coating: it can be provided by the "XB-785" enamel. These products allow you to make the base as durable as possible, such materials come in a variety of colors. It should be borne in mind that when using such coatings, it is necessary to remember certain application rules. After reading this article, you will find out all the basic information about these materials.
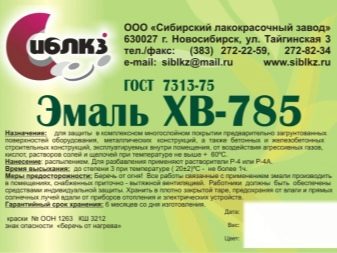
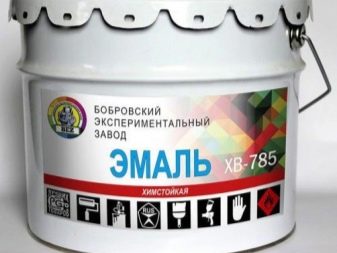
Distinctive material properties
Enamel brand "ХВ-785" is a paint and varnish product, the main component of which is polyvinyl chloride chlorinated resin. The composition also includes fillers, plasticizers, organic solvents that improve technical characteristics. The color of the product is directly related to the presence of various pigments. It can be white, gray, yellow, black, red-brown.
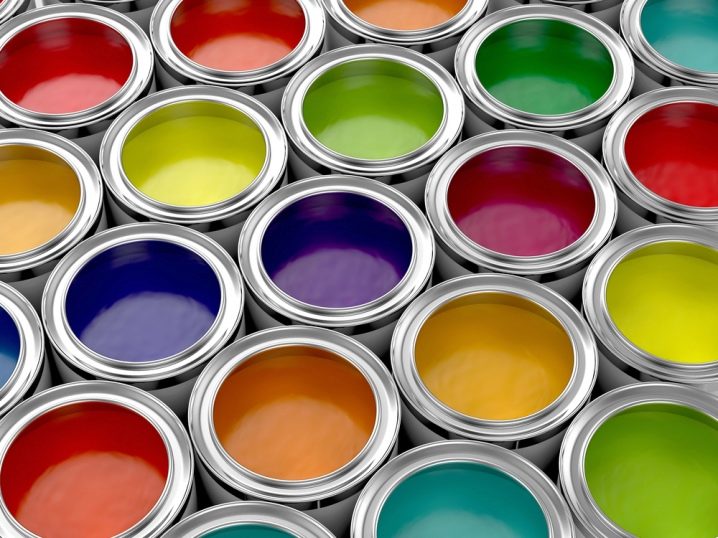
Material advantages:
- excellent anti-corrosion properties;
- resistance to salt and alkaline solutions, gases;
- hardness and wear resistance, increased resistance to mechanical stress;
- good adhesion to substrates;
- plasticity of the coating;
- extension of the service life of metal, concrete, reinforced concrete (due to strength and durability).
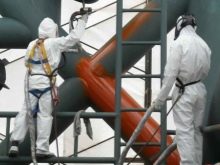
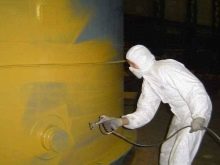
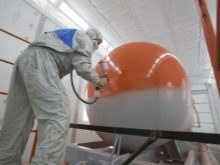
The enamel is acid-resistant, so the material protects surfaces in direct contact with various aggressive substances already during their use. At the same time, it allows you to get a smooth and beautiful coating.
For multilayer surfaces, used in outdoor conditions, usually used red-brown or black perchlorovinyl enamel "XB-785" in combination with varnish "XB-784". It is always applied to pre-primed substrates, including wooden ones. This composition is able to suspend destructive effects at temperatures not exceeding +60 degrees. Light shades of paint are more suitable for interior coatings, dark ones for exterior use.
This enamel is used in various fields. It is used in construction, in the arrangement of production workshops, to give strength to containers for chemical mixtures, to increase the service life of industrial and automotive equipment.
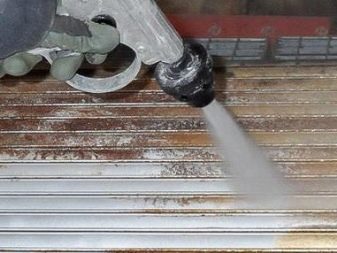
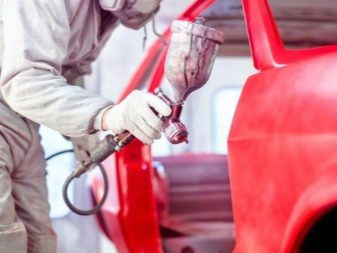
Preparation for staining
The process of staining with this material has its own characteristics. They must be taken into account when carrying out finishing work.
First, the surface is prepared:
- the metal is cleaned of dust particles, dirt, corrosion, old paint, grease and oil stains;
- the previous paint and varnish coating is removed with a scraper, rust - by using sandblasting, cord brushes (you can sand the material by hand - with abrasive agents, you can use a rust converter);
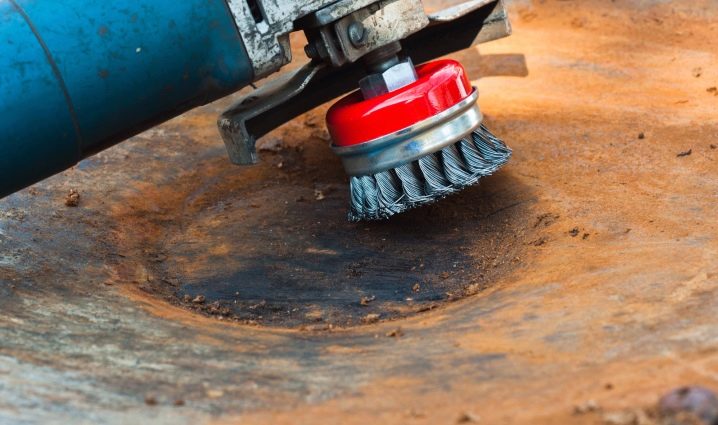
- it is important to thoroughly remove dust;
- degreasing is carried out using white spirit, solvent "R-4" or "R-5";
- on a dry surface, one or two layers of primers of the “XC-068”, “XC-010” or “FL-03K” brand are applied (depending on wear); it is easier and faster to do this using a pneumatic or airless method.
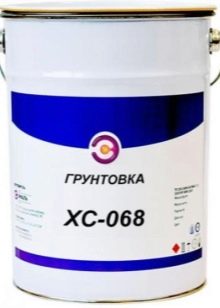
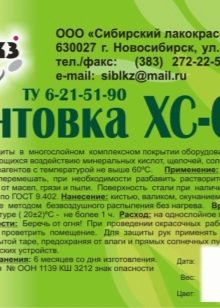
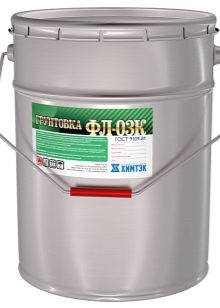
Then you will need to dilute the paint to working condition (using the "R-4A" solvent). The viscosity of the mixture is checked using a VZ-246 viscometer, it should be 16-22 s.It is not recommended to dilute the enamel with acetone or toluene, since these substances are not part of the material. Otherwise, there is a danger that the solution will curdle.
Mixing is best done with a construction mixer, it will provide the necessary homogeneity. No more than 20% of the solvent is added to the total volume of the enamel. If the proportions are different, the coating may peel off during further use.
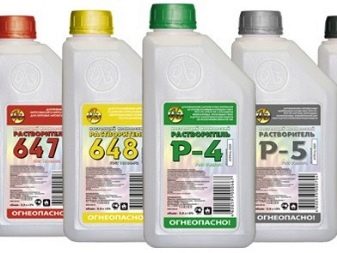
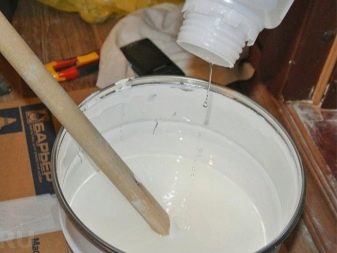
How to apply correctly?
There are certain painting rules that are important to follow. Considering the following requirements, you can achieve high strength of the coating and avoid some mistakes that can negatively affect the result:
- Much depends on the temperature regime. Application is carried out at +30 degrees and below, humidity does not exceed 80%.
- For maximum strength, one layer of enamel is not enough. Professionals recommend doing multiple layers. Each previous one must dry, after which the next one is superimposed. It takes about an hour to dry.
- Rollers and brushes are used in difficult places, automatic spraying - for large surface areas. This will greatly facilitate the workflow and save time.
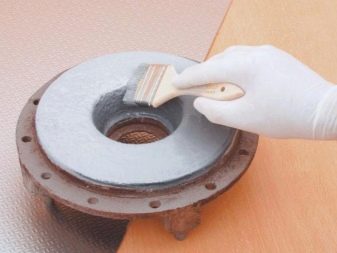
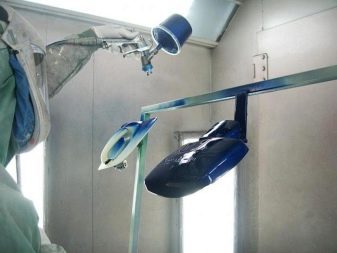
- To clean the instruments, use the same thinners that are required for the preparation of the solution.
- When working, you need to focus on the standard thickness of the coatings. Primer layer - from 15 to 20 microns, enamel - from 20 to 30 microns (each layer).
- Varnish "ХВ-784" is used to treat surfaces painted in any color - except for those on which black enamel is applied. The layer thickness should not exceed 20 µm.
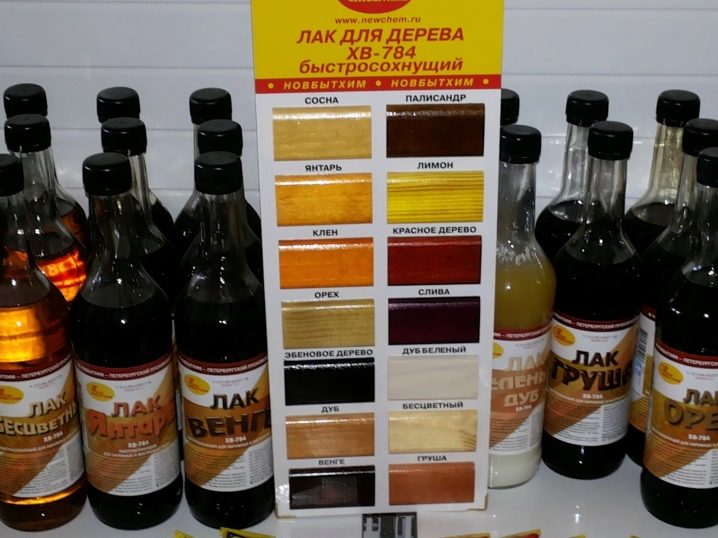
Absolute drying of the coloring composition occurs after 24 hours. It is noteworthy that the consumption per 1 m2 is 120-150 g per layer, you can save a lot. Consumption depends on the structure of the surface, the degree of its porosity, the total area.
Security
Working with enamel requires basic safety precautions. The products are subject to fire, explosive, there is a percentage of toxicity (due to the presence of solvents), therefore, painting should not be carried out near a source of open fire. It is dangerous to inhale the vapors of the solution, and even more so - the ingress of its particles on the skin and mucous membranes of the mouth.
To protect yourself from unpleasant health problems, you need to adhere to important guidelines:
- The area in which the painting is carried out must be well ventilated.
- It is necessary to use special means (overalls, rubber gloves, respirators to protect against dust and gas during outdoor work, a gas mask - when applying the solution in closed rooms).
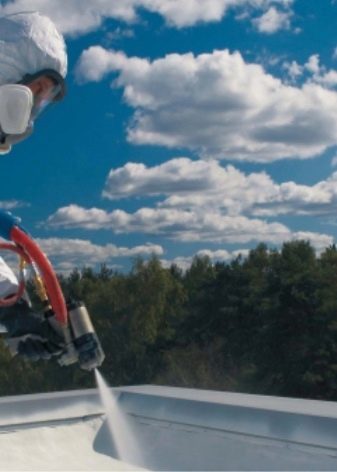
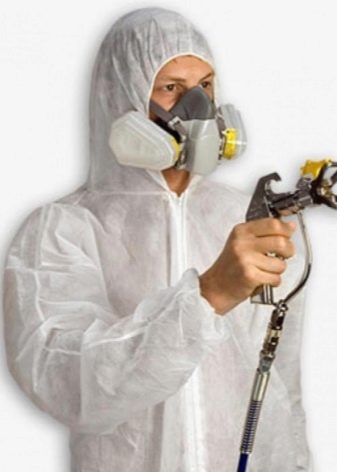
- You must have fire extinguishing devices with you, you must use safe tools.
- Smoking is prohibited in the workplace.
In case of fire, it is recommended to use a fire extinguisher, asbestos blanket, felt mat, foam and water spray devices. Packing is carried out in plastic or metal containers (weight - 10, 20, 25, 50 or 60 kg). The guaranteed shelf life is 6 months (with a tightly closed lid, away from direct sunlight).
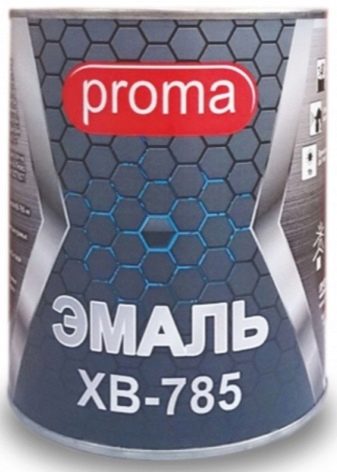
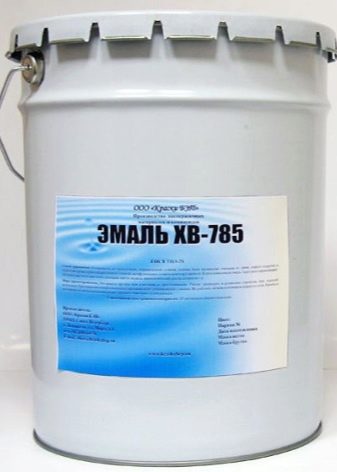
This product has a state quality certificate and is manufactured in accordance with existing standards (according to GOST 7313-75). This determines its high quality and required performance properties.
The problems that may arise when using paints and varnishes are described in detail in the following video.
The comment was sent successfully.