What is an I-beam and where is it used?

I-beam is a structural element with the shape of the letter "H" in cross section. Refers to an improved version of a simple brand. It is like two T-blocks, which are connected together oppositely and longitudinally, placing the shelves apart.
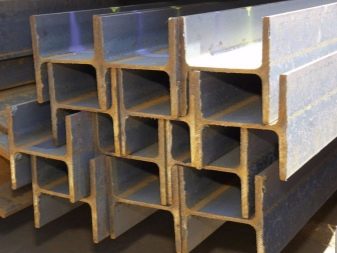
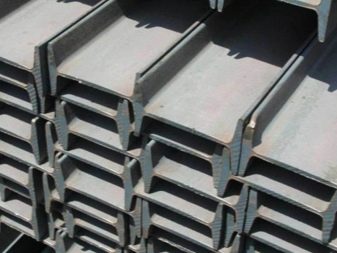
What it is?
The execution of the I-beam must be strictly parallel: the faces do not bend or intersect in an arbitrary shape. The characteristics of the I-beam are such that it differs from the channel, which looks like a shortened letter "P". Partly an I-beam with a thickened, and not thinner than the side flanges, wall can be obtained by folding two channel elements together with the main jumpers to each other. You can get an I-beam with equal success from two T-shaped elements.
According to GOST, an I-beam is made of steels with a low and medium carbon composition.
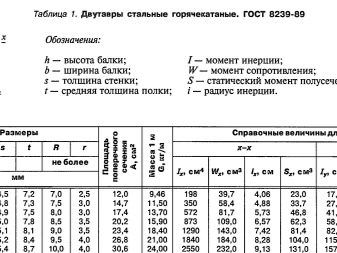
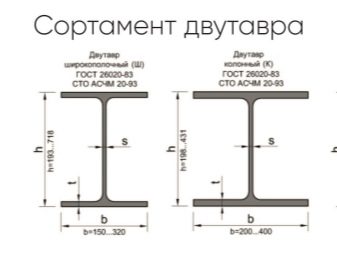
The same applies to alloying, which even hardens the steel: saturation of the alloy with alloying elements is carried out in a greater percentage by weight than carbon - there are steel grades from which channels are made, with 1-2% content of chromium, nickel, manganese and molybdenum. These impurities are the main impurities for tee and channel elements. But the presence of harmful impurities - phosphorus and sulfur, making steel more brittle, is regulated by special technical specifications and auxiliary requirements of GOST.
I-beams are especially taken into account, for the manufacture of which neither steel nor non-ferrous metal - wooden components are used.
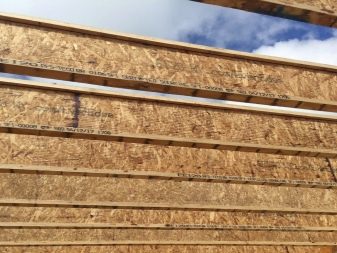
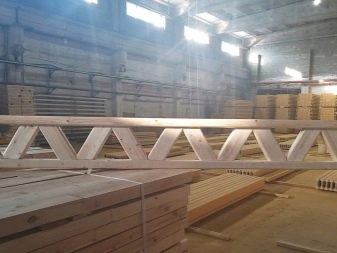
They are assemblies from sawdust and glue-based sawdust - the simplest composite, which, unlike natural wood, does not twist out upon further drying. They are not covered with cracks of the fibers, shrunk during drying and subsequently parted with the formation of voids. Fastening of such I-beams is carried out on segments of a perforated sheet, bent into a corner and made of medium-alloy steel. The advantage of a wooden I-beam is its relative lightness up to 10 times compared to steel, the disadvantage is its susceptibility to charring even when coated with impregnations that do not support an independent flame.
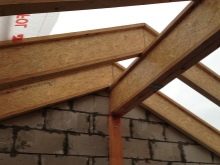
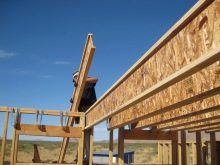
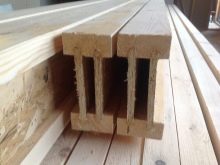
Varieties
The aluminum I-beam is a replacement for the steel one. It is unsuitable for creating load-bearing structures. Rather, it is suitable for the construction of auxiliary, for example, partitions in a large office space. The moment of resistance of steel, as well as strength, elasticity, is several times higher than that of aluminum. The high strength is due to the equally high density of the material: the thicker and heavier the element, the greater the load it will withstand.
It is impossible to manufacture welded structures to reinforce the floor without T-bar and channel elements.
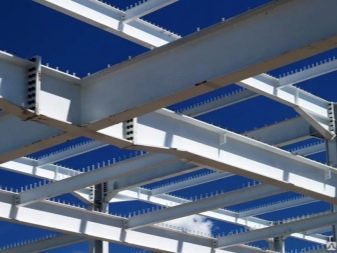
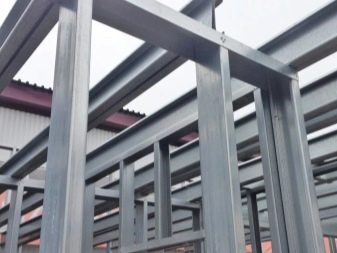
The section of the profile in the section of typical I-beams of a certain size is more than 10 cm2. The strength provided by such a quantity of steel distributed over this section according to the width of the shelves and the main headroom of the element is sufficient for a segment of several meters to withstand the weight of 10 people standing on this element without noticeable deflection.
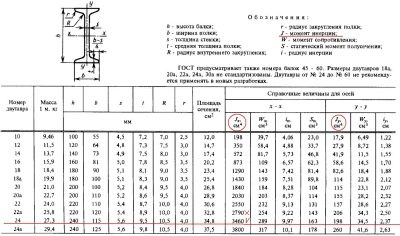
T-and I-beams, along with channel bars, are used to organize reinforced concrete floors, which are the basis of a strip-monolithic foundation, poured taking into account the load from some particularly heavy equipment. For example, pipe and bar bending machines, whose weight, in turn, reaches a ton or more, and the production (shock) load during the main work has an additional effect on such a foundation, need to strengthen the foundation slab not only with reinforcement, but also with a beam profile ...
I-beam steel is used in the construction of floors and bridges.
In contrast to Russian conditions - say, in the USA - wide-shelf I-beams are used.
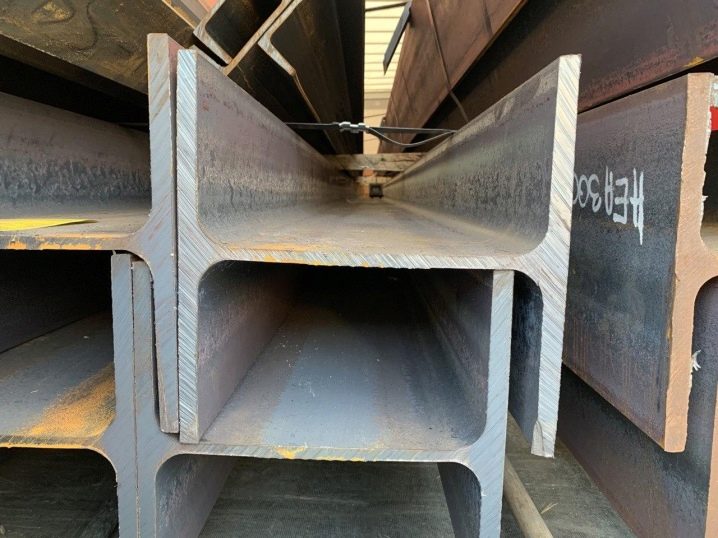
Beam normal
Normally fired beams are a standard parallel-equal-beam I-beam. Like a channel, it has a strict rectangular ends in cross section. In the longitudinal section, its landmarks - the longitudinal edges of the faces - are strictly rectilinear and parallel. Any specific characteristics (slope, rounding, bevel of the walls) are completely absent. The width of the shelves outside and inside, respectively, on each of both sides are equal along the entire length.
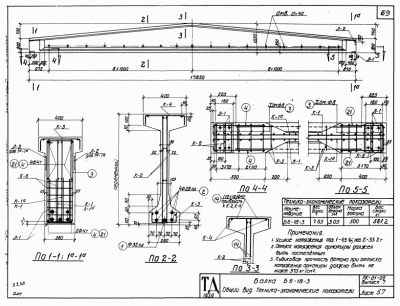
I-beams with a slope of internal flanges
The slope of the inner surfaces of the shelves in the "inclined" elements of the diesel fuel - conditional, does not affect the location and parallelism of the outer sides of the shelf edges.
This is achieved using a variable thickness: the closer to the longitudinal edge on each side of the DFC, the smaller it is.
At the edges, within the last few millimeters of width, it turns into a smooth rounding, dropping to zero at the interface between steel and the surrounding such element, or adjacent to it - the environment (air, concrete, roofing felt, wood, etc.).
Pile
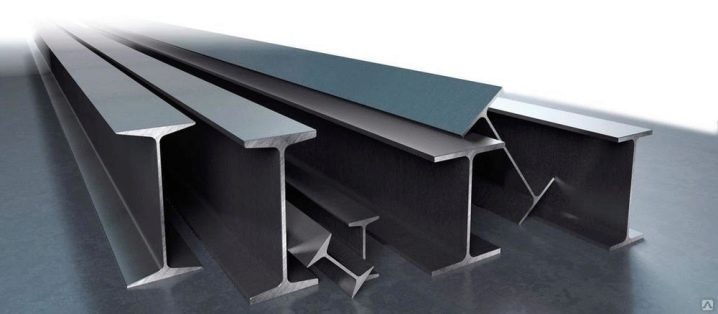
Column
Column I-beams, like a square professional pipe, have mounting ends. These are transverse flanges, with which the elements are fastened using anchors or studs welded to the reinforcement before pouring concrete. In the second case, the sections of the studs must be located strictly parallel and spaced apart from each other at the corners of these end flanges, as in the case of hammering in anchors.
The verticality of such a structure is set strictly according to the level gauge and the plumb line, and the concrete support, into which studs are installed or anchor bolts are drilled, is also verified strictly horizontally.
If errors are made during concreting, then it is advisable to perform a screed space (you can pour, with "gravity" of the hardening composition), or grind the installation sites of the column I-beams, periodically checking the installation site for horizontal alignment with a level gauge.
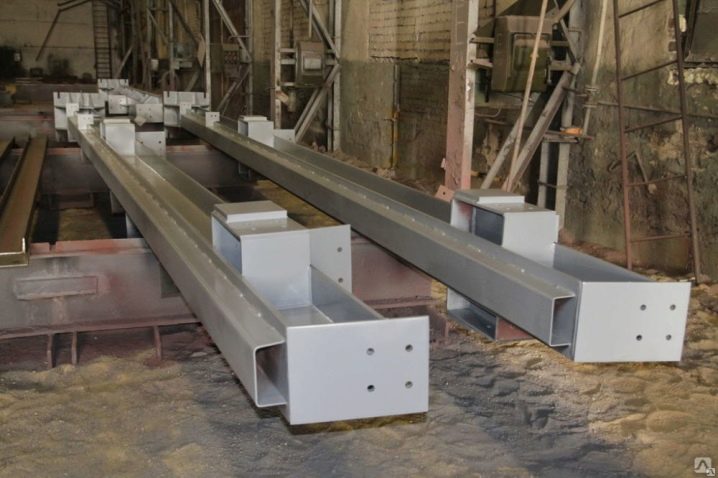
Pile
The pile I-beam by the principle of location, installation, preparation for installation of horizontal beam elements resembles a column one, but does not contain fastening horizontal ends. Like a professional pipe, channel, round pipe, solid circle and square, it is hammered with a copra. The lower end, entering the ground, is sharpened to a sharpened state to accelerate and facilitate driving into the ground, which reduces the serration and flattening of the opposite end of the element when the striker is working.
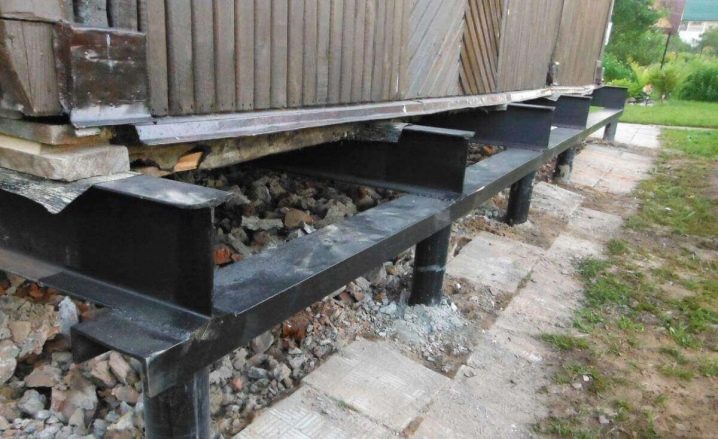
Other
Parallel-flank I-beams are manufactured, as previously noted, with a center of gravity with no offset. The rolling method of production is hot-rolled profiled steel, which has an overall structure of equal strength. The joints between such DFCs are welded or bolted, as on a monorail line.
Low-alloy I-beams do not have the highest strength - the same steel grade St3, St4 or similar is used for their manufacture.
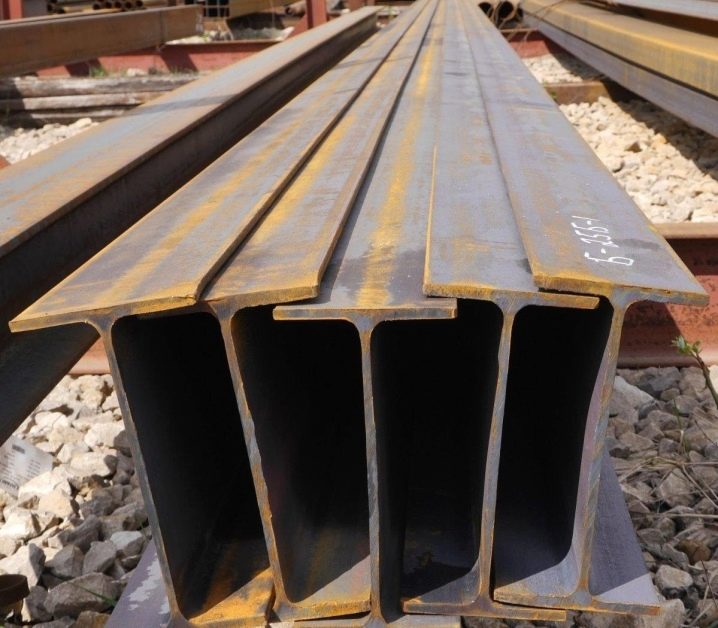
In terms of material, in addition to wood-composite, steel and aluminum, there are often mono-composite (homogeneous composite, for example, from solid MDF-building material), as well as plastic I-beams. And if a homogeneous composite - a composite-one-piece (two) tee - can be used to build full-fledged auxiliary supporting structures, then a plastic I-beam rather resembles a double-sided furniture edge that can be pressed between metal slats. The role of a plastic I-beam, especially a small one, in imparting the final strength to a specific product is noticeably reduced.
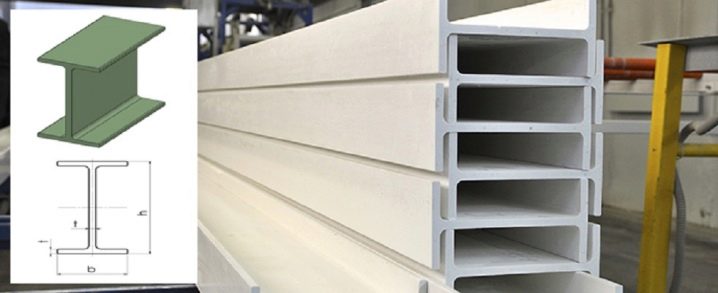
Classification
The I-beam, in addition to the form factor - the cross-section and the length of the forming profile, as well as the type and variety of material, is classified by size. The standard size, which has specific indicators of the material used in the manufacture of each such unit, has important characteristics: the thickness of the walls and shelves, their width and length of the segment. So, the I-beam-20 has a 20-cm width of the main bulkhead wall connecting these shelves. Diesel fuel height from 25 cm is widely demanded in construction.
The thickness of the wall and shelves of the steel DTE can be up to 12 mm, depending on the specific requirements for the safety factor created using the wall / ceiling.
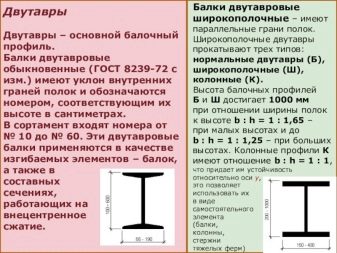
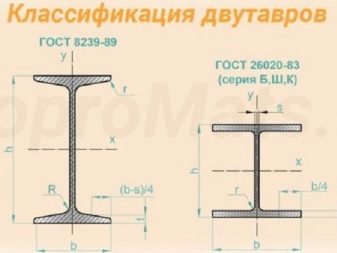
In addition to the width in centimeters, there is also a specific marking that emphasizes the same width in millimeters: 150, 200, 250, 320, 350, 400 and so on. The height of such an I-beam corresponds to standard sizes 15, 20, 25, 32, 35 and 40.
A complex icon, for example, 26B2, indicates the following features. So, the profile element B1 differs from the profile B2 in the height, thickness of the shelf and the wall with the same width of the shelves. A product with a marker 26 B1 has a height of 258 mm with a crossbar thickness of 5.8 mm and a shelf width of 12 cm.A product 26B2 differs by a height of 261 mm with a wall thickness of 6 mm and a shelf width of the same 12 cm.
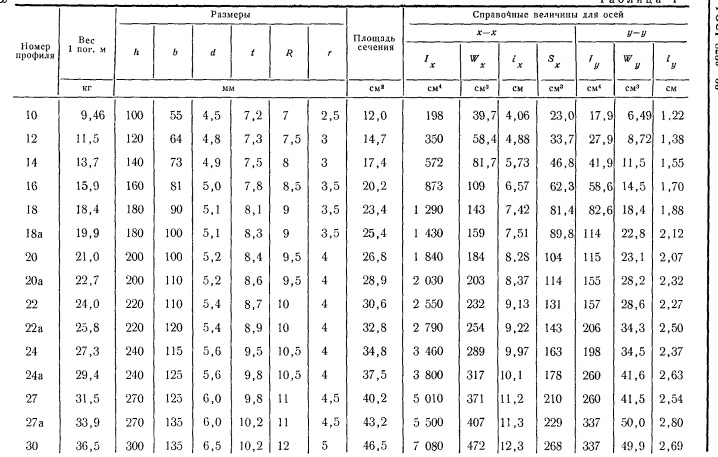
The principle of such designations is described in GOST R57837-2017.
Parameters, for example, beams 30B3, are as follows. Section height - 30.5 cm, width - 15.1 cm, lintel thickness - 0.8 cm, shelf thickness - 11.5 mm, radius of curvature - 1.3 cm.Products of brand 26SH1 have a wall height of 251 mm, width shelves 180, and shelves 1 cm thick, wall thickness 0.7 cm.
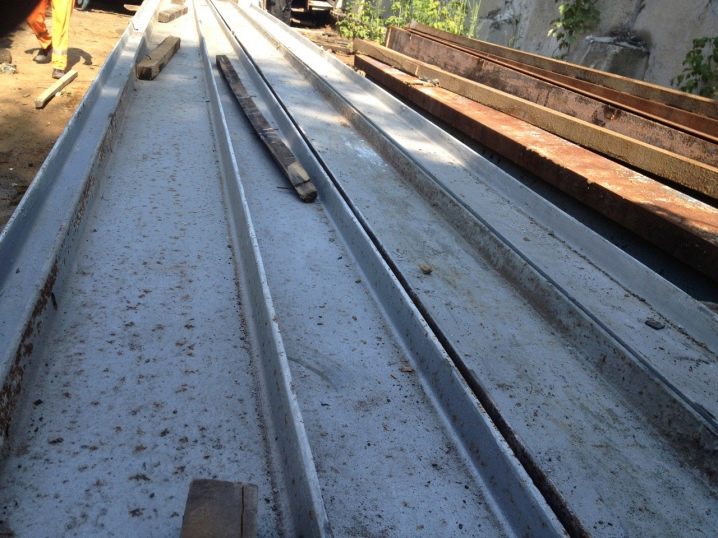
Selection criteria
The calculation of the safety factor is carried out in accordance with the cross-sectional area, the length of the beam, the distance for the span between the beam elements. If a structural component is selected for operation in the mode of severe frosts and long winters, then it is more expedient to use not the St3 alloy, but its more frost-resistant analogue, for example, 09G2S. The same steel is used in the construction of, for example, polar earth stations. It will also find wide application in the creation of habitable colonies on Mars and the Moon, since the 09G2S composition is considered one of the candidates for use in medical and space cryonics.
The parameters of the I-beam should be with such values that these elements do not bend even under the influence of furniture, equipment and people who are in rooms on any of the floors of a particular building.
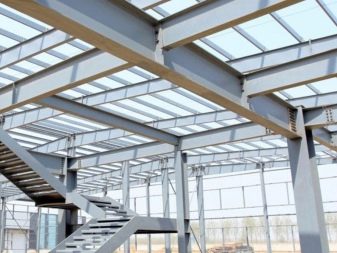
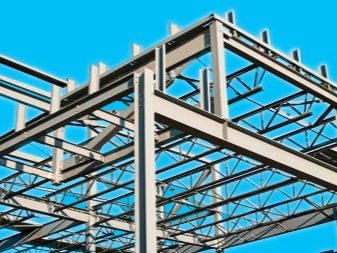
The construction of low and multi-storey buildings takes into account the total load on such a house or industrial building. For industrial construction, whose tasks include ensuring the operability of conveyors located on different floors, I-beams of the largest sizes and with the maximum wall thickness are used. Similar ones are used for the construction of bridges, which are used by heavy and multi-tonnage transport in the amount of up to thousands of cars / wagons per day.
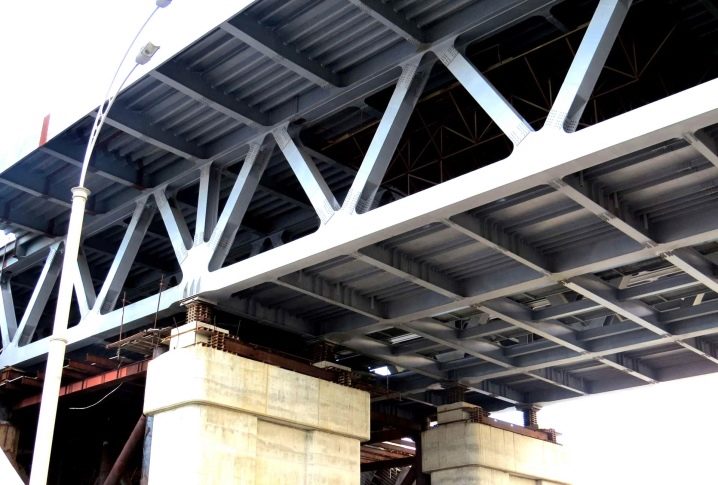
Application area
As noted earlier, an I-beam is an indispensable element in the construction of bridges, multi-storey buildings and underground garages, subway lines, bomb shelters and other structures. It complements the channel and simple T-bar - and it, in turn, complements the fittings. The connections of such structures are carried out mainly on piles and bolts. The diameter of the latter is selected taking into account the load reserve: if you use too small bolts, they will break, and the structure will fold.It is impractical to use riveted joints - they are more suitable for sheet sheathing, which plays an auxiliary role, and does not perform the function of the main supporting structure.
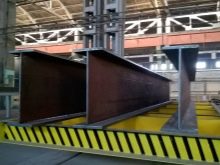
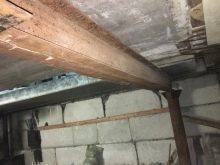
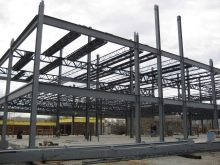
Cold rolled and special steel grades as well as finished I-beams are used in auxiliary construction, for example, when demarcating indoor areas. Here, it is advisable to use beam structures rolled to a perfectly smooth mirror state, which can replace reinforced concrete columns inside the room. A typical example is museums and banking halls, where a crowd of dozens of visitors gathers. But such a solution is often replaced by lightweight frame-plasterboard partitions, where each workplace of an employee and a place for a client is a single compartment.
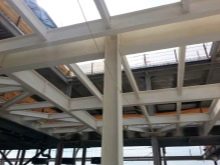
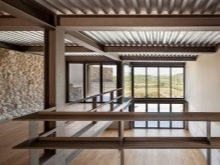
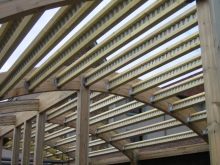
The comment was sent successfully.