Overview of fiberboard panels

All people who want to decorate their home beautifully need to know what it is - fiberboard panels. It is imperative to find out how the choice of moisture-resistant decorative panels with a pattern for tiles and bricks, other types, is carried out. It is equally important to consider the features of specific types and installation recommendations.


What it is?
A conversation about fiberboard panels should start with the fact that this is an important type of sheet building material. To obtain it, wood waste is processed. The processing procedure involves exposure to the press while hot. Fiberboard cannot be considered a very new material - the production of such structures began almost 2 centuries ago. Production using modern "wet" technology has been going on without any significant changes for over 50 years.
The wood pulp will first have to be washed. The standard work sequence involves first removing impurities, which can be done mechanically. A separator helps to remove metal debris.
The chips are crushed into small fibers. In the mass prepared in this way, polymers, paraffin and specially selected resins with an adhesive effect are placed. The advantage of the "wet" method is that the substance will contain fewer harmful components.


Varieties
The main gradation of sheet chipboards is the degree of their rigidity. The softened version, due to its low density and porous structure, is very light, almost does not allow heat to pass through. The usual thickness varies from 0.8 to 2.5 cm. The density in different versions ranges from 150 to 350 kg per 1 m3. In appearance, it is not difficult to recognize such a material - its edges are tousled; panels of increased softness are not resistant to moisture.
Especially soft slabs are used mainly in construction. They act as a good semblance of gypsum boards and bend perfectly. This material is relatively cheap and therefore popular with consumers. The transport of the softened fiberboard is not a problem.
It is used both for decoration and for laying under flooring.



A semi-rigid slab is not that flexible. Its mass is usually 850 kg per 1 m3. The layer thickness is usually 0.6 or 1.2 cm. Such designs are widely used to obtain the back walls of furniture. Of course, they can be placed under the front floor covering, as well as used for assembling boxes, transport boxes.
For rigid fiberboard, the density, depending on the brand, can be from 800 to 1000 kg per 1 m3. The thickness of the slabs is relatively small, no more than 6 mm. Mostly they are bought to make panel doors. Furniture production also uses this material, but only as the back walls of some cabinets. Along with glossy and matte specimens, there are also modifications that reproduce the look of natural wood (this is a particularly decorative type).
Particularly hard (or, as experts say, super-hard) fiberboard formation has a density of at least 950 kg per 1 m3. Simple pressing does not allow achieving such an indicator. Pectol must be added to the working mixture. The most rigid panels are used to assemble doors, arches and interior partitions. Loose slabs can make an excellent floor covering; and due to their dielectric properties, they are appreciated in the assembly of electrical panels.


Laminated fiber board is highly appreciated by furniture makers. A layer of synthetic resins is located on top of the main array of fibers.It is able to reproduce a natural wood surface. And also there are options painted in a certain (for example, white) color. Additionally, gradation is distinguished by types:
- sheet;
- tiled;
- finished under the lining.
The tiled panel is small. It is sold in a format of at least 30x30 and no more than 100x100 cm. Thorn grooves are cut at the ends. These units can be ceiling-mounted, floor-standing or wall-mounted. The imitation of the lining is also mounted using tenon grooves; it is a moderately moisture resistant construction, which is installed in a short time and almost does not warp, unlike natural wood.


Quite often there are options:
- under a brick;
- under the tiles;
- under the stone.
In many cases, perforated fiberboard is used. It is an economical option when compared to other types of perforated slabs. In most cases, the surface is painted in light colors, which dramatically increases its attractiveness. The product will look original even in a private house.
As for sandwich panels, they have been produced in our country since 1974; many pieces are made with a pattern, and this immediately increases their attractiveness.



There are other classifications:
- a plate with an unrefined surface;
- slab with unfinished face layer;
- plate with an improved face layer;
- product finished on both sides;
- blocks smooth on one or both sides;
- cladding products;
- painted products;
- laminated products;
- 5 levels of plates according to the intensity of the emission of formaldehyde to the outside.



The choice of appearance depends entirely on the preferences of the owners. So, imitation of brickwork is most appropriate in the style of a loft or in an urban room. Accent design is often practiced, bringing variety to the atmosphere. It is impossible to see a special visual difference with the natural brick of the product. At the same time, the structure turns out to be noticeably lighter and is assembled without dirty, wet processes.
Panels that reproduce the appearance of a stone look colorful. This is a completely natural solution that only a few people can afford - so why give up at least its external semblance. "Stone" slabs harmoniously fit into a variety of design trends. They will definitely create a feeling of comfort, harmony and indestructible stability. One cannot ignore the fact that complex installation work will not be required.
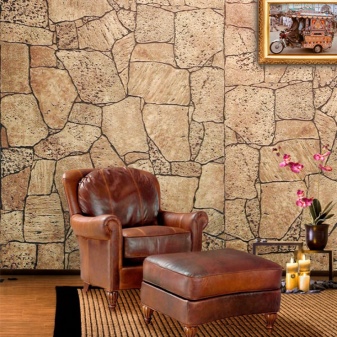

A true classic, however, is the use of wood imitation. In the budget class, this is achieved by applying a polyvinyl chloride film. Such coverage and protection will provide, and will convey the appearance of the rocks. It is less profitable economically, but more practical is the use of veneer. It, in general, cannot be distinguished from "real" wood.
Panels that reproduce the appearance of tiles are relevant in the decoration of kitchen areas. Sometimes even an apron is formed from them. Installing such products is easy. To cleanse, simply use damp cloths.


Installation tips
The wall panel can be exposed in different ways. It is often believed that the easiest way to place it is with glue. But a prerequisite is the perfect leveling of the surface. Only if this requirement is met, the work will take place quickly, and its result will last for a long time. Sometimes the elimination of all interfering defects takes a very long time.
Of course, before gluing the panels, it is necessary to remove not only all the old material, but also grease stains, dusty and dirty places. The substrate is primed twice, allowing time to dry. Otherwise, adhesion is not ensured.
When this is done, you can cut the blocks themselves to the size of the wall.


The back surfaces of the panels are lubricated with glue and glued to the designated place. The glue mixture can be applied either pointwise or in a zigzag manner. Maximum attention should be paid to the edges. Since the panels are heavy, proper operation can only be ensured with the assistance of assistants.Marking is done using a level and a plumb line.
Installation with nails and self-tapping screws is also widespread. The second type of fastener is preferable.


Important: the use of hardware does not mean that you can refuse to level the substrates. Fastening to brick, concrete walls is done with dowels. Screwing fasteners into the stone "neat" means an increased risk of tearing out.
The use of lathing helps to compensate for the unevenness of the walls without unnecessary finishing. The frame will also help cover the wiring and other communications. Insulation can also be put there. The useful space in the room, however, will be taken away - and this can hardly be considered a plus. The panels themselves are fixed to the lattice with nails or self-tapping screws.


How to choose?
Buying fiberboard for the bathroom or for the purpose of decorating an apron for the kitchen will bring much more joy if you apply laminated solutions. They are much more resistant to water ingress. It is equally important to carefully study the technological parameters of structures and find out if there are quality certificates. In the materials, information on the passage of sanitary control must be noted. This is especially important for the decoration of the living room, bathroom and kitchen.
Any products with increased formaldehyde emission should not be used in residential premises. The presence of mechanical defects, bubbles is unacceptable. And also it is impossible to allow the presence of oil stains, paraffin. The packaging should be provided with a label that is as descriptive as possible. For the ceiling, you need to choose the lightest possible, and for furniture - the most durable modifications.


For information on how to trim fiberboard exactly, see the next video.
The comment was sent successfully.