Selection and installation of chipboard on the floor
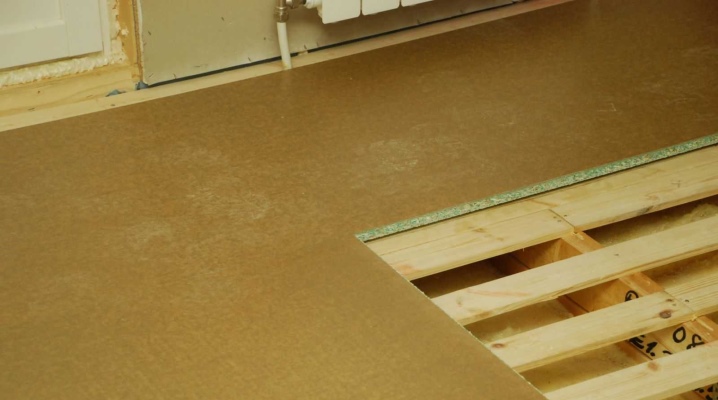
Selection and installation of chipboard for the floor Is a very relevant topic now. It is necessary to take into account the peculiarities of laying slabs under linoleum on logs, the standard thickness of the panels. But before you lay the sheets under the laminate with your own hands, you must also read the reviews and study the maximum of other nuances.
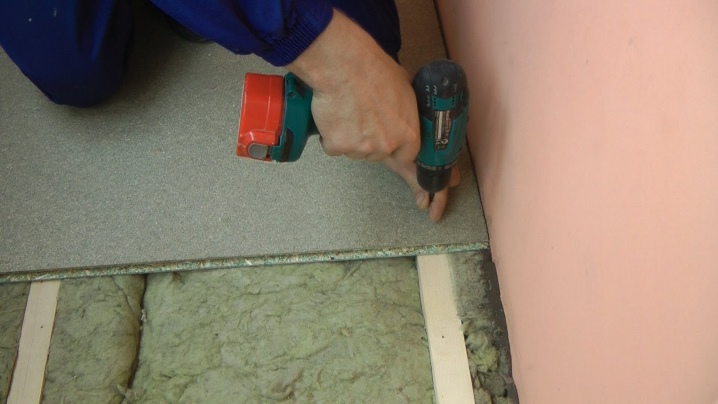
Peculiarities
The main specificity of laying chipboard on the floor is that this procedure is quite simple... Knowing the key points, you can complete all the work in a short time and without any problems. Chipboard is obtained by pressing processing of wood waste (with simultaneous heating). Most often sawdust and shavings fall under the press. To make the connection more effective, they also use a combination of specially formulated glue with resin.
The cost of the finished product is quite attractive. Therefore, floor slabs and panels are widely used in construction.

This solution is much more profitable than boardwalks, self-leveling floors and even more parquet. Manufacturers invariably mention the high technical qualities of such a coating. However, another point is also important - if necessary, the floor from particle boards can be easily decorated, it is simply used as a blank for linoleum, laminate, tiles and other materials.
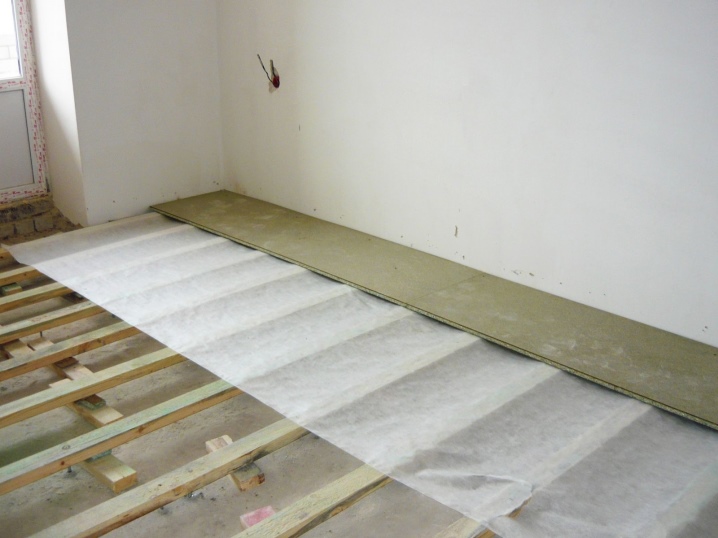
A flat surface is formed without much difficulty. The compressive strength is quite sufficient for the front floor covering in rooms where there will be no special loads. The product is invariably resistant to microorganisms, little susceptible to the formation of mold and other fungal foci. The adhesion quality is also at a decent level. It should be borne in mind that:
- the edges of particle boards are very fragile;
- with prolonged or very strong exposure to moisture, the structure will be broken;
- Particleboard is highly flammable.

Views
It is also worth considering that chipboard can belong to different classes. Default raw material parameters are strictly standardized. But deviations from the specified dimensions are still permissible, and this inevitably affects the properties of the finished product. Very small raw materials are unacceptable, because then the quality of the products will irreversibly deteriorate. It is worth considering that regardless of the type, the glue must be distributed over the surface very carefully, in order to avoid unpleasant consequences.
Some firms, due to the use of defective raw materials, overestimate the concentration of impregnations. The aldehyde based polymer really helps to provide better bonding between dissimilar chips.


However, such a product cannot be considered good quality. In good slabs, the proportion of composite is a maximum of 12%. The most responsible manufacturers use no more than 6% of polymer components.
According to specific consumer qualities, wood-based panels are divided into:
- equipped with grooves;
- not having grooves;
- not subjected to grinding;
- polished as carefully as possible;
- covered with laminating film;
- protected from water;
- veneered;
- laminated (coated with a paper sheet);
- characterized by increased resistance to fire.
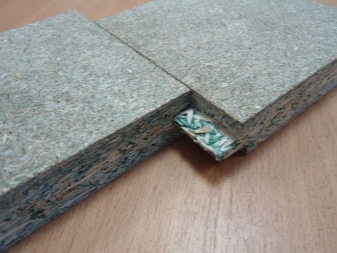



An important parameter of chipboard is also their density... Therefore, it is always necessary to clarify what the specific weight of a particular product will be. The first grade includes only panels without noticeable defects. In the presence of a limited number of defects, including deviations from the plane and chips of chipboard are referred to the second grade... If the slab does not have a grade, then this implies its roughest appearance.
Unpolished slabs are the cheapest, but in reality they can only be used in rough work. After sanding, the surface becomes much more beautiful and will even be suitable for decorative purposes. Additionally, veneer, thick paper or polymer-based films are used as coatings.


Laminated particle boards are the most resistant to negative influences and have the best performance parameters. In terms of decorative properties, they are also superior to other samples.
Only the highest quality layers are subjected to lamination, painted in a variety of colors.... Along with simple coloring, imitation of oak and mahogany is widely practiced, the formation of heterogeneous textures. After lamination, the plate is completely ready for use, all that is needed is to obtain a workpiece of the required geometry and size, work with the edges and mount the product. Moisture resistant sheet, intended for damp rooms, contains paraffin inclusions. Fire-resistant performance is the most expensive, and it is economically justified only with really high fire risks.


Dimensions (edit)
The thickness of the sheet directly affects its strength, and, of course, the ease of movement and installation. Minimum thickness the serial chipboard is now 0.8 cm. Maximum value theoretically it is not limited, however, for standard products it does not exceed 3.8 cm. As required, the number of layers within the formation and their size are increased, which makes it possible to achieve an increased total thickness. According to the current regulations, the error is limited to 0.3 mm, exactly the same approach is applied to laminated chipboard.

Geometrically, any slab is made in the form of a parallelepiped... The length of its surface ranges from 1.83 to 5.68 m (deviations even by 1 mm are unacceptable). The width of the product can be 1.22 - 2.5 m (with the same deviation level). The error of the products conforming to the standard is limited to 5 mm. The most commonly used sheet is:
- 2.75x1.83x0.015 m;
- 2.44x1.83x0.016 m;
- 2.62x1.83x0.016 m;
- 2.44x1.2x0.016 m.

Styling
Tools and materials
To calculate the need for material when laying with your own hands, you will have to make very simple calculations. First of all, determine the exact area of the room.
Then the area of a separate sheet is calculated. Determining the required number of sheets will allow, of course, a banal division. But you will definitely have to take into account the indents from the walls, connecting seams.

Having calculated the required amount of chipboard, you need to prepare:
- bars (they are used to get lag);
- laser or hydraulic level;
- construction tape;
- screwdriver;
- high-quality hammer drill;
- electric jigsaw;
- dowel-nails;
- wood screws.




Mounting
Chipboard allows you to cope with even the most uneven floors... However, leveling the surface will have to be carried out as carefully as possible. The subfloor is laid on logs on top of a concrete base. The gaps between these lags are 30-40 cm (if you have to use sheets up to 16 mm thick). When using a sheet with a thickness of 22 mm, the gap is increased to 40-60 cm.
Important: you will have to leave a gap of about 2 cm near the walls. If the floor is uneven, the gaps are filled with slag or sand. When working on the ground floor, the gaps are saturated with foam or related polystyrene foam. But even before installing the lags, it will be necessary to lay out a layer of a vapor barrier on the concrete floor.

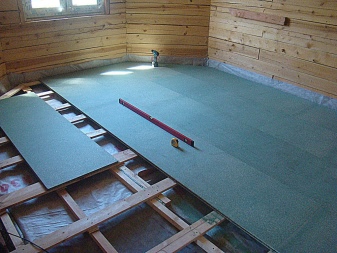
The building level helps to verify the horizontal plane of the base.
Covering with paper or building plastic helps to avoid the squeak of the exploited floor. Installation is carried out starting from the most distant wall. Immediately after laying out the first panel, you must immediately fasten it to the substrate with pre-prepared self-tapping screws. First of all, you have to "nail" the middle of the block. Further, the installation step will be approximately 0.2 m, the caps of the self-tapping screws are recommended to be "sunk" by 1 mm or more.
Immediately after this, you can lay a new slab. It is pressed firmly against the previous panel. In order to exclude damage to the material, it is advisable to use the supplied fitting bars. The seams must be done strictly on the logs. When arranging floors in narrow corridors, the frame is placed at an angle of 90 degrees to the direction of travel.

Vertical irregularities are easily eliminated: they need to be sanded and cleaned from dust and dirt. After that, the surface finish is finished (unless it is decided to stay on the chipboard coating).
It is quite possible to apply this material not only for laminate or parquet, making a floating floor in an apartment is also easy. Normally, a layer of steam protection is formed on top of the concrete. But on the wooden flooring it is most correct to lay out glassine.
The next stage of work is adding filler... Slag and dry expanded clay are ideal in this role. The layer of this backfill must be made as even as possible. A paper or a construction membrane is placed over the filler. At the wall from which the installation will proceed, you will have to lay wedges.

The very process of installing chipboards involves gluing them together. From the edge of the panel to any wall, exactly 1 cm should remain. It is important to know other subtleties, how to put the chipboard on a pure concrete base. If it is perfectly flat and free of horizontal drops, you can do without using lags. It is enough to cover small irregularities with a thin screed, which will settle for at least 3-4 weeks.
As soon as the substrate reaches the required strength, it must be cleaned, accumulated dust and dirt removed. A construction vacuum cleaner will ideally help in this matter.

The cut of the sheets is made as carefully as possible in order to reduce the waste of material. Important: no matter what type of floor is created from particle boards, it is necessary to treat them with linseed oil or antiseptic. This is the only way to ensure the required performance.
The base is, of course, carefully marked out before installation. Precisely according to the markings, the concrete must be drilled. Dowels are inserted into the holes made for more efficient fastening. The sheets are laid out in such a way that a gap of 1.5 cm remains exactly. You will have to work with lags a little differently.
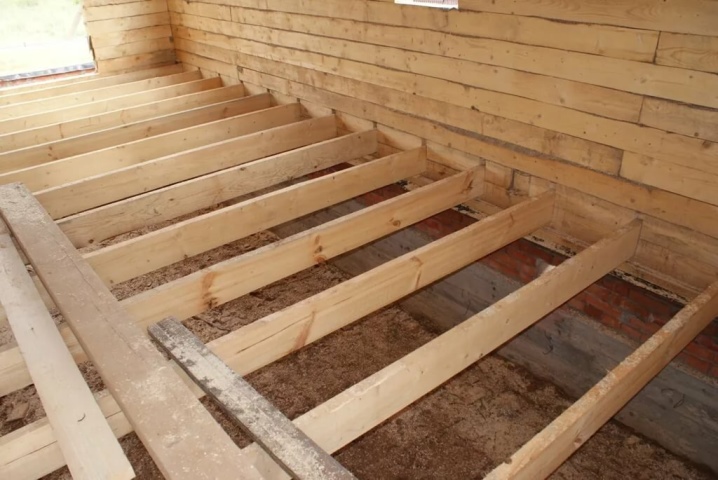
Chipboard is more fragile than plywood, or even more so wood. That's why lags bring closer together... But it is quite possible to refuse the arrangement of the screed. Since the use of logs does not guarantee complete uniformity in level, sometimes you have to put small pieces of plywood or wood under them. Otherwise, the support surface does not come out sufficiently.
The next step is to lay out the insulation in the gaps of the sheathing. The lags are attached to the floor with anchors. It is recommended to use mineral wool from heaters. It must be fitted tightly in order to exclude the slightest voids. The remaining cracks are sealed using polyurethane foam. A hydraulic barrier is created on top of the insulation - foil and oilcloth are optimal for this purpose.


Recommendation: if you apply penofol, it will not only retain moisture, but also improve heat retention. The very installation of chipboard is made by nailing the plates with nails.
Sometimes chipboard is used even in warm floors. Then it will have to make channels in it for the pipeline. In the rack and pinion version, the pipes are laid on top, and strips of aluminum are placed in the grooves, where the heating system circuit is then inserted.

Finishing
After the final fixing of the material, be sure to you will have to close up the gaps around the perimeter of the slabs. Only the protection of the ends can guarantee the optimum reliability of the coating. Before covering the seams and joints, it is necessary to thoroughly clean and dry them with a construction hairdryer. Later problem spots are coated with polyvinyl acetate glue... As soon as it dries, a layer of silicone is applied on top (in rare cases, it is replaced with a typical construction sealant).
No special clearance required... Where it is really needed, it is enough to simply adhere to the “tongue-and-groove” system installed at the factory. When using chipboard, paraffin grouting is required.
It is quite possible to get by using a regular home candle. Chipboard can only be putty after cleaning and degreasing.

Potholes and cracks are repaired in advance. The putty is used only at an air temperature of at least 7 degrees. With multi-layer filling, it is necessary to achieve drying of each level and only then process the surface again. Having finished drying final layer, grind the screed and remove dust from it. Primer carried out several times from both sides, this is the only way to achieve reliable protection.

In wet rooms, the choice is obvious - you need a primer containing an antiseptic. In dry rooms, there is more choice, the main thing is that the primer and putty are combined. In any case, specific compositions for wood surfaces should be used. You will have to work with a wide steel spatula. Acrylic and latex mixtures are usually applied in a layer not thicker than 3 mm, in other cases, the manufacturer's instructions should be followed.

Review overview
It is worth noting that the chipboard floor has quite a few opponents. Common grades of this material are extremely unstable to moisture penetration.... The swelling is literally catastrophic. Damp products suddenly lose their ability to carry stress. Some believe that it is more correct to glue such material, and not to nail it - because due to mechanical instability, poorly distributed load can destroy the panels.

However, complaints about chipboard subsidence are usually associated with a violation of technology. Either the distance between the lags is too great, or they are moving themselves. It is recommended to use linoleum as a front layer over chipboard. But tiling is not the best idea. In any case, it is better to weigh the pros and cons in advance, to clarify the nuances of the work performed.
How to properly install the chipboard, see below.
The comment was sent successfully.