DIY hydraulic wood splitter making
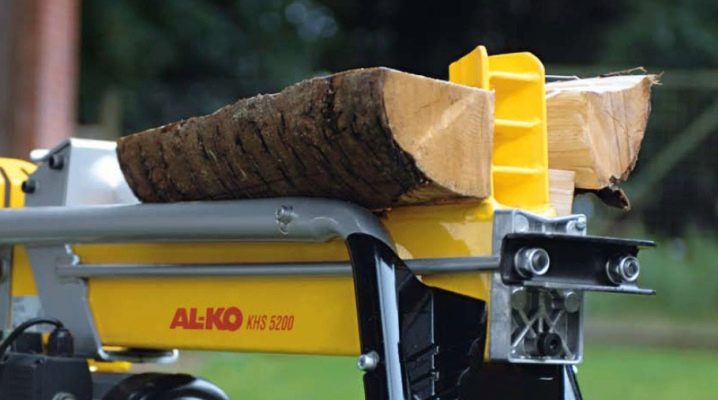
Chopping wood is an activity that requires significant physical effort. When the volumes are small, it is useful and even necessary to "wave" an ax in the fresh air.
Things are much more complicated if you need to chop a few cubic meters of wood every day. This requires a special tool to help split massive wood ingots. The hydraulic wood splitter is the very device that can effectively help in the preparation of firewood.
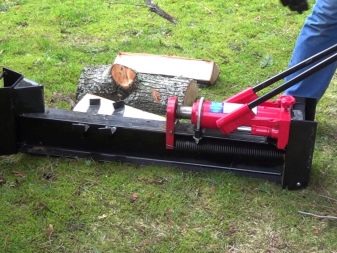
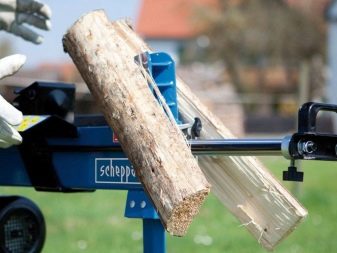
Design features and purpose
The reasons for the popularity of hydraulic wood splitters are quite compelling: in such units, a load of more than ten tons is accumulated over a certain amount of time. This technology makes it possible to prudently exploit the engine and mechanical components. The minimum amount of energy and fuel is spent, while the productivity of the work increases.
There are many factory hydraulic wood splitter on the market at a price of 10 to 300 thousand rubles, there is plenty to choose from. But you can make a hydraulic wood splitter with your own hands. This device consists of several standard units:
- base;
- a special emphasis on which the cylinder rests;
- cutters;
- hydraulic pressure generating device;
- container for oil;
- hoses;
- power point.
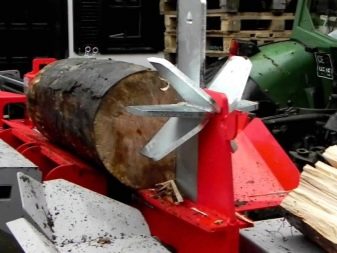
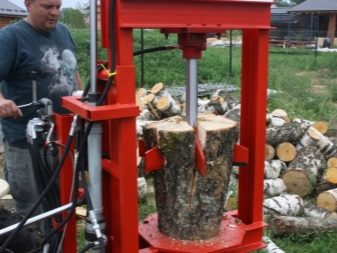
First of all, you should make a solid foundation, weld a solid frame from channels or corners of "eights", which will bear the main load during operation. The lower part of the bed is supplied with a jack (you can use a car jack). At the top, the installation of the connector should be planned: it is necessary to process workpieces of a wide variety of parameters.
Making a wood splitter requires practical plumbing skills. The work is not very difficult, but it is important to correctly fit all the nodes and parts. After assembly, several test runs should be carried out. It is necessary to own a tool and be able to handle metal, only then can you get a well-working machine.
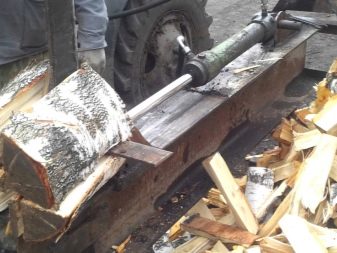
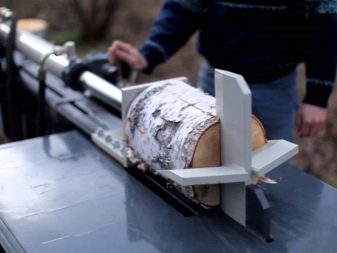
It is also recommended to consider the following when designing: if you put a powerful drive (for example, from a tractor), add a sufficiently voluminous engine (from 2 kW), then it will be necessary to mount a cutter with 4–6 blades.
A hydraulic log splitter can generate a significant energy impulse, it takes a certain amount of time, so the difference between a hydraulic log splitter and all the others is that it does not work very quickly. The technical fluid enters the stem, which, in turn, pushes the stop with the workpiece to the cutter. In this case, the effort is generated (by accumulation) more than ten tons.
The hydraulic wood splitter is safe from the point of view of work, and it is quite productive.
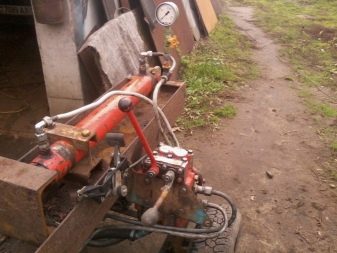
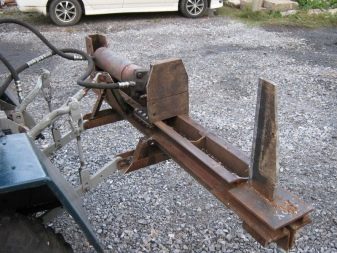
It is recommended to remember: damp wood is not suitable for interaction with a hydraulic splitter, the cleaver can get stuck in the material, it will be difficult to pull it out.
Before starting work, it is recommended to let the wooden ingots lie down. Usually they are placed under a canopy for 2-3 months in the warm season - this is quite enough for the wood to reach its condition. Excess moisture evaporates from them within 2-3 months, after which the material will be prepared for work.
A homemade hydraulic wood splitter is simple in design, you can do it yourself, it will be no worse than a factory one.As an example, we can say that a good unit that can work with ingots with a diameter of 30 cm costs from 30 thousand rubles. There are wood splitters on sale and from 40 thousand rubles, they can "cope" with material with a diameter of 40 cm.
Advantages of a hydraulic wood splitter:
- great productivity;
- a small amount of energy is consumed;
- safe to maintain.
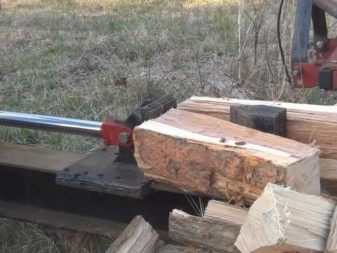
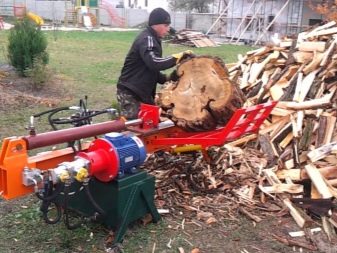
If we talk about the disadvantages:
- such a unit can be handled by a person who has practical experience;
- if there are excessive loads on the components of the device, then the technical fluid can flow out of the cylinder;
- you will have to "tinker" in the process of setting up and testing the device, but if everything is done correctly, it will last for many years;
- the speed of the reverse pusher of the mechanism is about 8 meters per second - one person can prepare half a ton of firewood in a couple of hours.
Spare parts for a hydraulic wood splitter are easy to find, the same applies to used engines, hydraulic units.
The hydraulic wood splitter does not have a return spring: it takes 0.56 seconds to switch it, which is a rather long period of time, during which the workpiece can split into several parts.
The engine of the wood splitter operates through a fluid coupling, so sometimes problems with loads arise, in such a forced mode a fair amount of fuel is consumed.
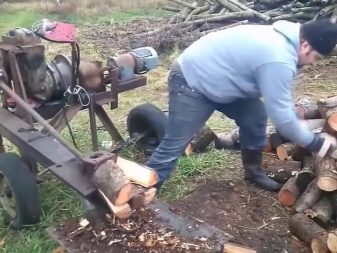
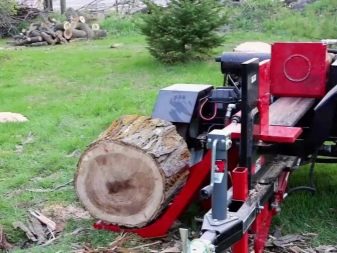
A mechanical clutch is attached to the flywheel, which is hydraulic (sometimes frictional). The lever itself is a clutch with a pusher, it provides the feed of the ingot to the cutter. The hydraulic wood splitting device is powerful enough to handle any workpiece.
In a hydraulic wood splitter, you can pre-fix the workpiece, which makes it possible to do all the manipulations in a safe mode and ensures a better work performance. The engine can be diesel or gasoline with power up to 6 kW.
The drive of the hydraulic wood splitter is of two types:
- vertical;
- horizontal.
Both units can be used very successfully, only free space is required for this. Wheels are sometimes attached to the frame, so the machine can be moved around the room. Instead of a cutter, you can use an X blade - this makes it possible to divide the workpiece into 4 parts.
The pig height is limited by the size of the frame; one worker can operate the hydraulic device. With a longitudinal arrangement, the stability of the device is reduced. The hydraulic system from the tractor may be suitable for working with a hydraulic pump.
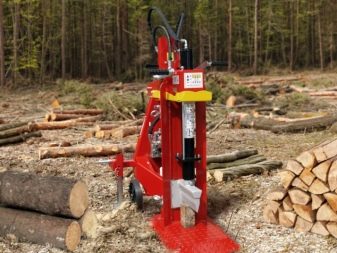
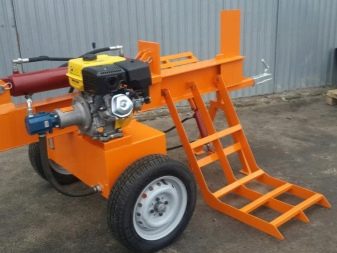
The working indicator is the pressure that is generated at the end of the workpiece.
It is usually calculated up to 200 bar. If recalculated, it will be approximately 65 to 95 kN. Such indicators are quite enough to split any workpiece with a diameter of half a meter. The working stroke of the piston is determined by a distance of 220-420 mm, while the drive is usually two-speed:
- direct movement - 3.5–8.5 cm per second;
- a return movement of 1.5–2 cm per second.
It is best to use petrol or diesel power units. They are easy to repair, they are more functional.
The base should be based on a massive flat surface (a reinforced concrete slab 20-50 cm thick is ideal). It is permissible to work only with such ingots that correspond to the power of this machine. During operation, it is required to do a preventive inspection of the unit. It is necessary to ensure that foreign objects - nails, fittings, screws - do not fall into the working area.
It is recommended to change the pulley often enough, which "remembers" the trajectory of rotation, after a while it starts to provoke excess vibration. It is necessary to regularly conduct test inspections and start-ups of equipment.
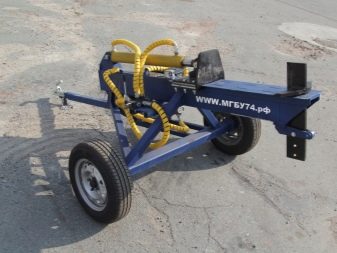
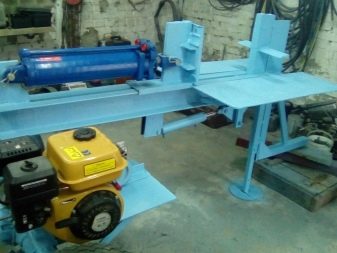
Tools and materials
To create a hydraulic log splitter you will need:
- power plant from 1.8 kW;
- a shaft with a fixed bearing (possibly even 3);
- pulley;
- cone;
- metal 5 mm thick;
- corners "4", pipes 40 mm.
You will need tools:
- hacksaw for metal and jigsaw;
- welding machine;
- "Bulgarian";
- tape measure and triangle ruler.
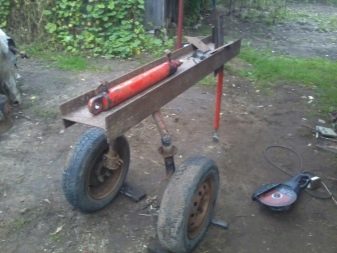
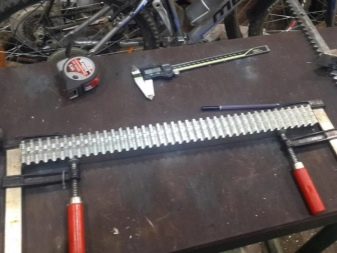
During the working process, it is necessary to observe safety precautions. The energy of impact on the wood mass, which is spent per second, is quite significant, the speed of the chips flying is comparable to the speed of shrapnel.
At the beginning of work, it is imperative to check all fasteners, cables, joints, pulley. The torch must be free of corrosion and must be sharp.
The employee should be dressed in loose-fitting overalls, his hair removed, he should be wearing:
- special gloves;
- good work shoes.
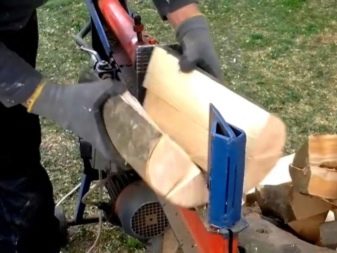
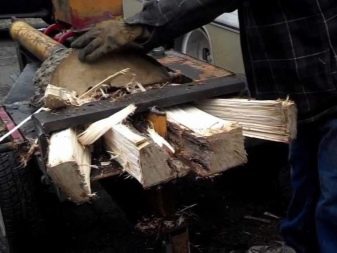
Manufacturing instructions
Before you start working, you should collect the drawings, they are on the World Wide Web. The assembly scheme for the unit should be carefully worked out, there can be no trifles in this matter.
You can do the job of creating a hydraulic wood splitter in the garage. Used hydraulic system is taken from an excavator or tractor. Productivity depends on the volume of the workpiece and what kind of split the log will be, the effort spent on splitting also plays an important role:
- 220 mm - 2 tf;
- straight layer - 2.8 tf;
- 240 mm - 2.5 tf;
- 320 mm into 4 parts - 4 tf;
- 320 mm for 8 - parts 5 tf;
- 420 mm in 8 parts - 6 tf.
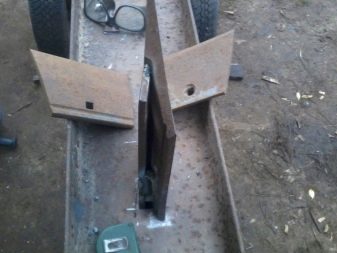
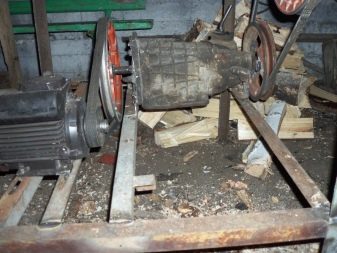
The force of the hydraulic pump depends on the feed rate (4.4 mm on average). After the basic parameters have been calculated, you should attend to such a topic as the search for the engine. The power plant should be selected with a margin of more than 20%. You should also choose fittings that should be reliable enough:
- tubes and hoses;
- tap;
- gate valves.
The cleaver is a very important element and must be properly sharpened at a 45 degree angle. A cleaver is made of hardened metal to avoid unnecessary deformation. The cutters must also be hard. The log first "meets" the vertical cutter, it is sharpened on a straight wedge (with observance of symmetry). The cutter, located in the horizontal plane, is mounted in the background, at a distance of 20 mm, it "rests" on the upper oblique wedge.
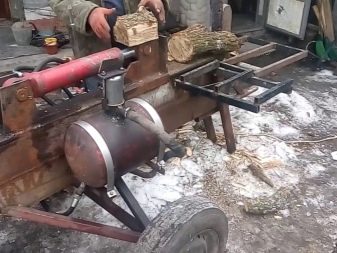
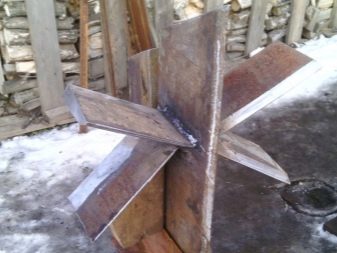
The rectangular cutter is mounted at the bottom, its height is 4 mm, the tool protrudes no more than 3 mm. Such installation will make it possible to work with wood blanks of increased complexity. The corners are sharpened like this:
- vertical cutter for soft woods - 18 degrees (3 cutter sizes);
- for dense tree species (including birch) - 16 degrees (3.7 knife thickness);
- horizontal cutters - 17 degrees;
- the lancing device has a tilt angle of no more than 25 degrees (minimum level 22 degrees, cutter size 2.5).
When designing and creating a drawing, first of all, the functionality of a home-made machine is determined. For household chores, a vertical hydraulic wood splitter is sufficient. The productivity of such machines is small, but they are small in size and easy to use. Then you should think about the drive: the gasoline engine is mobile, but the electric engine is cleaner, less loud.
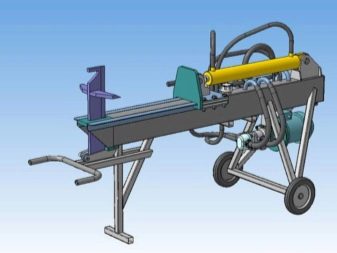
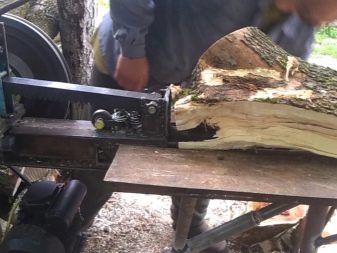
Next, it is important to attend to the topic of creating a mechanical jack - it will be needed to move massive workpieces. The jack is mounted on a cross member, which is made with the letter T, it is attached to the bottom of the frame. The tool can be made in this form of a wedge device. This block also contains a centering unit, it sets the vertical movement of the axis of the facing split. To do this, a mark is made along the axis of the workpiece - a hole through which the wedge device will enter the workpiece at an angle of 90 degrees with respect to the lower block. The device will split the workpiece with minimal energy consumption. At the same time, the quality of the cleavage increases, the energy costs decrease, and hence the fuel consumption.
A car jack can be used for a horizontal hydraulic drive device. When installing it, it is important to connect the hoses correctly. In this case, the device is mounted on a wheel frame. When rocking, the handle from the jack acts on the end of the workpiece. The opposite end enters the material and cuts it.
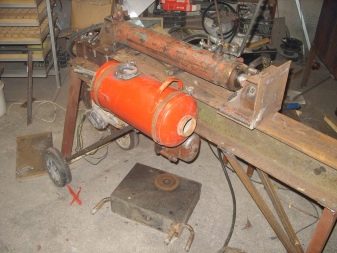
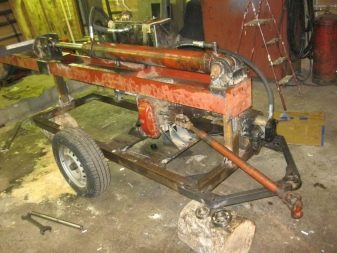
If the pressure decreases in the hydraulic system of the jack, return devices in the form of a spring (on both sides) return it to its original position. If you use a different knife, X format, the productivity can be increased by 100%. By adding an additional pumping unit, the speed of work will increase by another 50 percent. The pump unit has the following components:
- hydraulic cylinder;
- container for oil;
- pump NSh 34 or NSh 52.
Thus, a choice will need to be made. The hydraulic log splitter is more bulky. The vertical hydraulic log splitter is larger, but it also has more power. You will also need to decide which model is preferable - more often they use a design when the cutter is in a stationary position, and the workpiece is fed to it. Sometimes another principle is used, when the torch "enters" the workpiece.
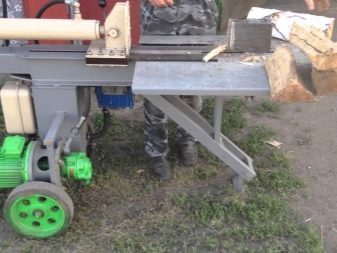
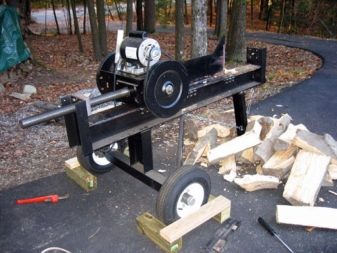
For information on how to make a hydraulic wood splitter with your own hands, see the next video.
The comment was sent successfully.