Types of drying chambers for wood and advice on their choice
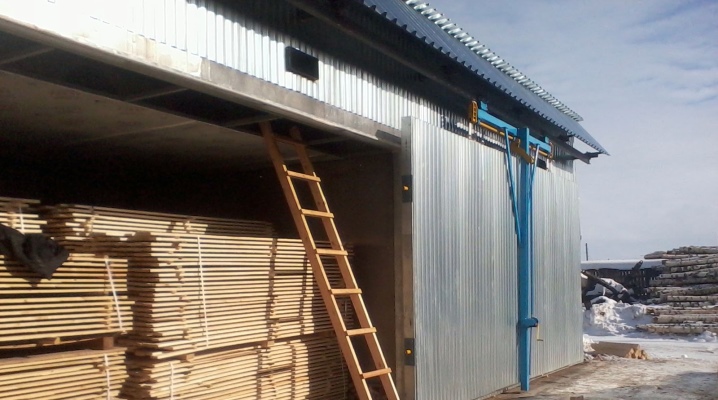
Drying chambers for wood are a device that is actively used in the field of industrial activities. It is a piece of equipment that turns out to be an indispensable tool for lumber during the production phase. For boards made by industrial enterprises, there are certain criteria that the material must meet.
Description and purpose
It is very difficult to make wood of really high quality and suitable for further use, while observing all the necessary stages of production. In this process, drying chambers are a necessary element, because first of all, the raw material must be dried, and only then proceed to the subsequent processing process.


The uniqueness of the equipment lies in the fact that it is used for drying any kind of material, from the simplest varieties of trees to exotic ones.
The technology of drying chambers allows this process to be carried out without allowing wood defects, which is very important in the production of sawn timber.
There are different types of equipment, each of which is designed for a specific type of work. However, most dryers are versatile, which is a significant advantage in their use.

Classification
There are several criteria for classifying the drying process: by the way of removing moisture, by the way of air circulation and by the type of drying agent.
By the way of moisture removal
There are a number of types of drying chambers.
- The most common type of drying chamber is convective. It has a simple operating principle. To remove moisture from the wood, hot air is blown over it, which is most often heated with the help of electric heaters. Fans are used to form a jet that will have the necessary strength and direction. They are usually powerful, and more than ten fixtures can be used in production at the same time. The convection dryer has the important advantage of steaming the wood, which minimizes the stress inside the material.

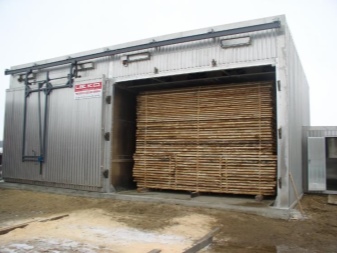
- Condensing. Condensation drying equipment for wood has a special feature - moisture from the timber is released and condensed on specially designed structural elements. After that, it accumulates in the discharge channels and leaves the chamber. Air, meanwhile, cyclically blows the material. Freon is used to charge the cooler. The temperature that is kept inside the dryer is only 450 and the drying time is significantly increased. The best option for a condensation dryer is a device that is equipped with a humidification function. This allows you to reduce the stress that appears in the upper layers of the dried timber.


- Aerodynamic. Aerodynamic chambers are structurally simple. They represent a metal box where fans are installed, thanks to which the air inside the chamber heats up. As soon as the humidity reaches the desired level, the fans stop working.A significant disadvantage of this type of chambers is that the wood is dried unevenly: the upper layers dry out, while the inner ones remain moist. This increases the tension inside the wood. When trying to dry the material, they tend to crack. This is a clear disadvantage of this type of drying.


- Infrared. Such a dryer differs in that there is no need for the chamber itself and any other enclosed space in principle. To remove moisture, infrared cassettes are used, which are placed between layers of dried sawn timber. Radiation evaporates moisture from the wood. Drying in the warm season can be carried out in an open space, protected from rain. However, this type of drying is quite difficult compared to others due to the length of the preparation phase.

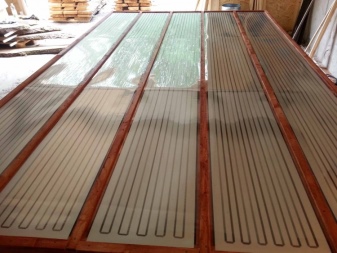
- Microwave. Drying is carried out in the same way as the process in a microwave oven, only the size of the products is significantly different. Such a drying chamber evenly frees the wood from moisture, delicately processing the material, while the speed of this process is quite high. Nevertheless, both the equipment itself and its component parts are of high cost. There is another disadvantage - you can load a small amount of lumber at a time, which suggests that the choice of such a chamber cannot be called a profitable decision. A much less expensive mini-dryer can also cope with small volumes.
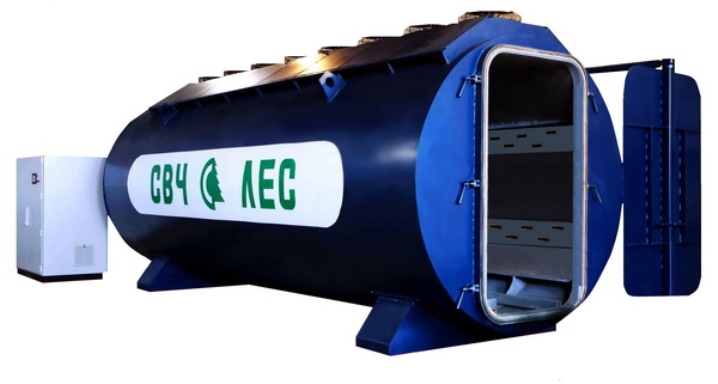
- Vacuum. The vacuum chamber is of a sealed design. The drying pressure is quite low. Drying is carried out at a low temperature, which is up to 65 degrees. The vacuum drying process is faster than other types of cameras. However, the complexity of the design of the vacuum chamber is worth noting. When the impact on the material is soft, the probability of cracking does not disappear, as with any other type of drying. The press-vacuum drying chamber deserves special attention (the vacuum in it is achieved thanks to the pump). The material is pressed to the bottom of the structure, which causes pressing. This method is a relatively new technology that helps to achieve high-quality production of materials with a minimum of defects and rejects.


By the way of air circulation
Air circulation is very important during material preparation. It can be natural and coercive.
- With natural circulation the movement is carried out due to the difference between the density of cold and already heated in the air chamber. Cooled air, being heavier, rushes downward, while hot air rushes upward. Due to the natural course of air circulation in the drying chamber, its vertical direction is folded.

- Forced circulation - artificial air circulation, which is maintained thanks to powerful fans installed inside the drying chamber.

By type of drying agent
Air chambers, in which drying takes place with the help of moist air. For heating the air chambers, in turn, there are also different methods.
Heater heating, that is, a process using heat exchange devices. It includes:
- steam and water, in which steam or water can act as a heat carrier;

- electrical, carried out by converting electrical energy into heat;

- boron and fire heating methods, similar to each other - in both types, the flue gas acts as a heat carrier, but with boron heating, the gas flows through a brick heater - a hog, and when heating - through a metal air heater.

Airless heating. It includes aerodynamic and condensation dryers, as well as heat-generating dryers.Here, the drying agent is heated using a fan heater as an external heating device.


In addition to air devices, there are also gas dryers, where flue gas is mixed with air. There are also chambers that work with superheated steam. Not to be confused with steam dryers, which are heated using steam heaters.

It is also worth considering the division of drying chambers into batch and continuous equipment. The former are suitable for drying small batches of lumber, while the latter are suitable for a constant flow of drying large batches.


The official classification of drying chambers for wood is regulated by GOST, which includes a detailed list of all existing types of equipment.
What are the modes?
The drying mode affects the duration of this process and the combination of qualities that the finished material will have. Rational mode is the conditions under which drying takes the shortest time. However, at the same time, all the criteria that high-quality sawn timber must meet are preserved. Typically, drying modes are divided into two types.
- High temperature, which takes place at temperatures above one hundred degrees. The mode ensures that there are no defects on the dried material, but slightly reduces its strength.
- Low temperaturepassing at temperatures below one hundred degrees. Provides different modes depending on whether the wood is coniferous or deciduous.


Nuances of choice
What should you pay attention to in the first place when planning to purchase a drying chamber? There are basic criteria for high-quality equipment: the chamber must perform its main function well, that is, it must dry wood with high quality, assume low costs, and also ensure the environmental friendliness of the process being produced. In addition to the general requirements for the equipment, it is worth carefully planning everything related to the purchase of a drying chamber in order to make the right choice.
- Analyze the volume to be dried over a specified period of time.

- Assess the presence of wood waste in production - they may be useful in the future when heating equipment.

- Think about the likelihood of natural drying of the material outdoors.

- Take care of a visual diagram that will demonstrate the location of the drying chambers.

Drying technology
The least costly option, which will also ensure the quality of the lumber, is a natural type of drying. However, natural drying has one major drawback. For in order to significantly reduce the moisture content of wood, it takes a long time to stay in the open air. Therefore, the chamber type of drying is much more popular in modern industry. It differs from natural drying in that you can independently regulate the process, which, moreover, is much faster. Moreover, the percentage of moisture after it is lower. The disadvantage of chamber drying is that after it, minor defects can be found on the materials. But this unimportant factor does not affect the fact that the chamber method is the most popular and effective. Standard drying technology consists of the following steps:
- calculation of materials that will be dried in one batch;
- the stage of heating the wood, followed by the evaporation of moisture as a result of heating - the actual drying;
- cooling, which normalizes the state of the material;
- repeating the heating and cooling steps.




The comment was sent successfully.