All About Drill Chucks

Without a chuck, the drill will not adhere well to the design of the tool and perform the task at hand. This element differs in design and characteristics, and in order to choose it correctly, you will need to understand both one and the other.

What is it needed for?
The drill chuck is an important part that is responsible for the reliable fastening of the equipment. Its design is designed to hold the drill tightly without releasing it even at high torque. The chuck can be used to rotate a screwdriver or any other device.

A keyed item assumes that an optional component is being used for replacement. The key is made in a T-shape, it is located next to the chuck. When turned, moves the gear, which causes the collar to rotate around the lock, which is responsible for opening or closing.

Occasionally, in chuck design, the user turns the sleeve at the end of the drill to open and close the lock cams. Such a fastener holds the working tool better, it is easy to tighten it by hand with less force.
On some locks in the design of the chuck, the number of cams reaches six, and the more there are, the tighter the drill sits in its place. Of these, 4 are needed to hold the square bit. If the tool is used for household tasks, then the cams are 3 and they are self-centering.

Specifications
A user who frequently uses a drill should know and understand the chuck sizes on the market. Besides the fact that they differ in shank diameter, some require an adapter or adapter to be purchased separately.

The maximum shank diameter shows how wide the clamping tabs are.
In this case, these are:
- 0.6 cm;
- 0.635 cm;
- 0.65 cm;
- 0.1 cm;
- 0.13 cm;
- 0.16 cm.
The first sizes are rare, the rest are much more common. Based on the power and size of the drill, the manufacturer selects the best available shank diameter. If this is a small tool, the power of which is only 300 W, it makes no sense to put a cartridge at 0.16 cm on it.If the user cannot clamp the necessary nozzle with the existing cartridge, because the dimensions do not match, then it becomes necessary to choose another larger diameter.
It is worth taking into account the minimum permissible value of the shank diameter, which can be 0.5, 0.8, 1, 1.5, 2, 3 millimeters. It should be noted that the value of 0.5 mm is found on cartridges with a maximum value of 6.5 mm, and so on - in ascending order.
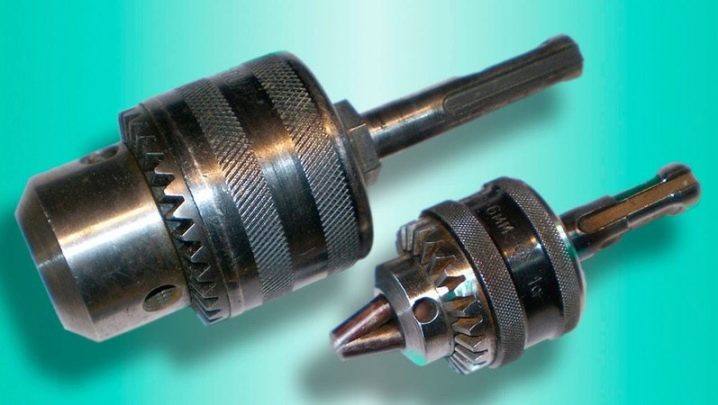
Of the other characteristics that must be paid attention to when choosing a suitable cartridge is the seat. It can be of two types: threaded and tapered.
Modern manufacturers prefer to use the first option in the design of the tool, the second is used on those drills where the maximum shank diameter is 16 mm.
The threaded connection plays an equally important role. It can be:
- metric;
- inch (1 * 4, 3 * 8, 5 * 8, 1 * 2).

The most popular sizes are 3 * 8 and 1 * 2. They are used on shank diameters of 0.10 and 0.13 cm.
There is only one type of metric thread - M12, it is used for cartridges with a shank diameter of 0.1, 0.13, 0.16 cm.

For cartridges, from the characteristics, you can also distinguish a seat, which is designated as:
- AT 12;
- B16;
- B18.
In this case, the numbers are the diameter, which is written in millimeters.
The honing head also plays an important role, the design of which depends on the length and diameter of the hole.
They are for holes:
- short;
- medium;
- deep;
- deaf.

Last but not least is the shaft, which can be stationary or flexible. The first is located in the drill body, the second is screwed in, there is a flexible hose in its design, it allows you to use the tool in hard-to-reach places.
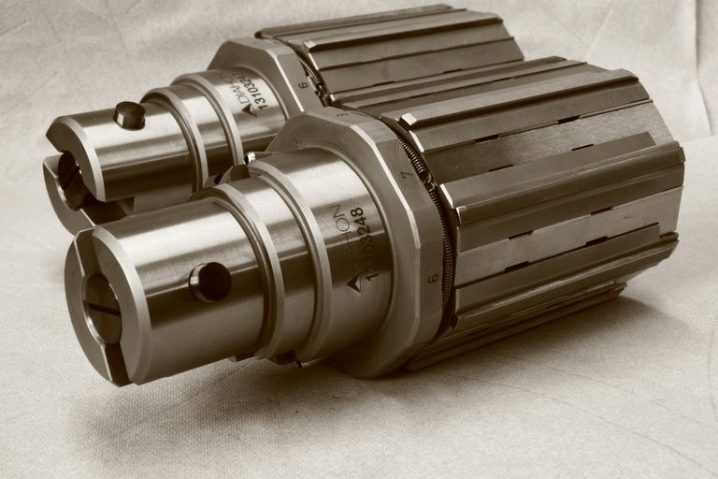
Design features
The device of the chuck is based on the use of a cam or collet mechanism in its design. Thanks to the element on the tool, nozzles of different shapes and diameters can be easily clamped.
The cartridge consists of several parts:
- cylindrical body;
- sleeve rotating on the outside;
- 3 clamping lugs.
The last element plays a very important role in the design of the cartridge, therefore it is made of high quality and high strength steel. All petals are of the same size and shape, when the sleeve rotates, they close, fixing the used nozzle.
Such a mechanism is simply irreplaceable when using round drills, since it prevents them from turning inside the chuck.




Views
There are several types of collet chucks with jaws inside:
- quick-clamping;
- key (gear-crown);
- mini-cartridges.


Quick-clamping devices are used without an additional key, which is their main advantage. The user has the opportunity to change the chuck quickly and without additional tools. The clamping is done automatically, which allows you to significantly reduce the time for changing the nozzle.
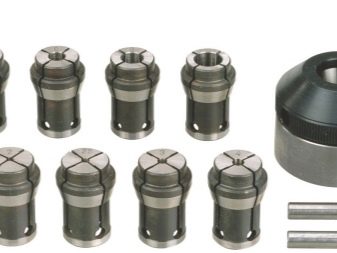

The disadvantage of the chuck is instability with prolonged use. Over time, the mechanism loosens and can no longer provide the required level of fastening, as a result of which the round shanks rotate.
More experienced craftsmen prefer key cartridges because they are more reliable and must be tightened by hand. However, it is not difficult to lose the key during operation.
Mini-chucks, which are installed on a small drill or drilling machine, are no less in demand today. Most often, jewelers use small cartridges.
These main types have subspecies:
- self-tightening;
- turning;
- angular;
- with Morse taper;
- with a ratchet.


By the type of fastening, the cartridge can be:
- conical;
- threaded.

The self-locking, like the quick-locking, has its own advantages: you do not need a key to use it. Unlike the second, where the clamping occurs automatically, with a self-clamping chuck, you need to use your hand. By hand, the user pushes the element towards himself, thereby loosening the fastening, and you can remove the nozzle. This position is held until another drill is placed, then released, and the chuck again fixes the nozzle, holding it tightly. In the design, a blocker plays the role of a clutch.

The cone chuck is put on without using a thread, respectively, the threaded chuck is screwed onto the stem. This is their main difference.
The lathe chuck can be manual three- or four-jaw, as well as mechanical two- or three-jaw. Some models are self-centering. They are installed on the front spindle flange or on the adapter flange.
Corner is used when it is necessary to make a hole at an angle of exactly 90 degrees or in a hard-to-reach place. It looks like a specialized nozzle with a key cartridge in the design.

The Morse taper element is used for equipment with an appropriate attachment. The equipment must necessarily comply with the requirements of GOST. The main purpose is to reduce the radial runout of the drill and the distance at which the drill is fixed in the chuck. It is a mandatory requirement that the dimensions of the cone on the tooling and inside the chuck coincide.
Few of the users know what a ratchet chuck is, and what is its peculiarity. A ratchet in the design is used to adjust the torque. It is thanks to her that the user gets the opportunity to adjust the depth to which the drill enters or the screw is screwed in, which is very important when working with drywall, when it is easy to pass the screw through.
For information on what kind of drill chucks are, see the next video.
Choice
Most portable drills have the chucks screwed onto a threaded spindle that is connected to the drill and then held in place with a set screw. To understand which element you need to buy to replace the old one, you need to open the petals to the widest point and look into the base with a flashlight. If you can see the screw at the bottom of the chuck, you should pay attention to the type of head. If it is missing, then it is probably a tapered spindle.

When buying, it should also be borne in mind that the element must ensure the proper rigidity of the fastening, taking into account the number of revolutions. More expensive models reduce the radial runout.
Last but not least, the usability of the cartridge, in this case quick-release in the first position, but when it comes to durability, it is better to buy with a key.
If carbide drills are used, then the chuck must self-center as this tool has poor buckling resistance. It is important to know that the rigidity of the attachment is always compared with the length of the nozzle and the material from which it is made.
Operating tips
During operation, breakdowns often occur, for example, in conical species, parts may fall out. If the element flew off the instrument, then the situation can be easily corrected. To do this, it will need to be heated in oil to a temperature of 110 C. After that, put on a cone.
If the clamping tabs become jammed, the user will need to remove the chuck, disassemble, clean and lubricate well.

But in the event of a runout, it is better to replace the part with a new one than to look for the cause of the breakdown, since it is often not possible to restore the previous functionality.
It is worth remembering that it depends on the user how long the cartridge will last.
In addition, it plays a role:
- quality;
- features of operation;
- how the user works with the tool.

The comment was sent successfully.