How to make a drill stand with your own hands?

The presence of a stand for a drill allows you to significantly increase the range of applications for this device. By placing the drill on a special stand, which, by the way, is easy to do with your own hands, you will be able to get a real multifunctional machine.
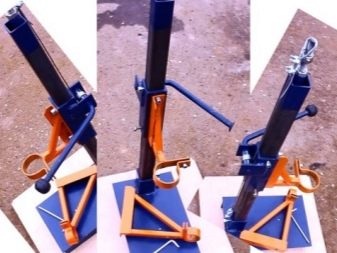
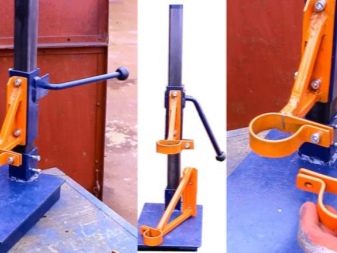
Peculiarities
A multifunctional drill stand that allows you to do various jobs, as a rule, consists of certain components. Firstly, a supporting frame is needed - it is on it that all elements will be fixed. Secondly, there must be a stand - a guide for the drill used to fix it. This element allows you to move the drill itself using a handle and other elements. Thirdly, the above handle is important, coordinating the vertical movement of the drilling part. Finally, there are also additional units, with the creation of which the machine becomes even more functional.
The size of the bed depends on the direction of work to be carried out using the device.

For example, when performing vertical drilling only, a sheet with sides of 500 millimeters is sufficient. In the case when much more complex operations are expected, the length should be increased to 1000 millimeters, and the width should be left the same. A stand is placed vertically on the bed, which is fixed with a special support. Usually, these two parts are joined together by screw connections.
Pros and cons of homemade racks
A DIY drill stand has both advantages and disadvantages. If we talk about the pros, then it is worth starting with the cheapness - it is much more economical to make the structure yourself than to buy it ready-made in the store. Moreover, you can even assemble a rack from things that are already in the household: various spare parts for obsolete or unused equipment. Drawings are easily found on the Internet for free access, in addition, you can also find educational videos that are easy to repeat. Finally, it is not forbidden to create a unique design that meets the specific needs of the master and has no existing analogues.

As for the cons, the first is the relative complexity of manufacturing. It so happens that some parts are impossible to make without special equipment, for example, for welding or a lathe. In this case, you will have to contact a specialist, which will undoubtedly increase the amount of money spent. The next disadvantage of self-made racks is called the frequent occurrence of backlash due to the fact that parts of the structure were incorrectly fixed. Backlash, in turn, negatively affects the further performance of work.
In addition, a homemade stand is not suitable for all operations required.
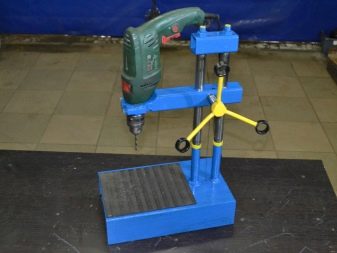

For example, it will not be able to drill holes at an angle.
How to choose a material?
The choice of material for the rack is determined depending on the further functions of the resulting machine. If you plan to only drill with it, then it is allowed to assemble the structure from ordinary wood blocks. If the stand should turn out to be more mobile and functional, then it is worth making some parts of steel. The drill stand is traditionally made either from a piece of wood with a thickness exceeding twenty millimeters, or from a metal plate at least ten millimeters thick. The specific choice of material and its thickness should depend on the power of the drill used. In addition, it can be reinforced with an additional layer of plywood of the required size - so the surface will turn out to be perfectly flat and more convenient for use.
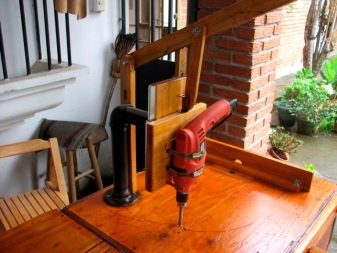

The stand on which the drill itself will be located is also made of either a metal or wooden plate. In addition to the guides, a clamp must be created on it to fix the drilling tool. The carriage, again, can be made of wood or metal.
Separately, it is worth mentioning the possibility of making a machine from an old photo enlarger.

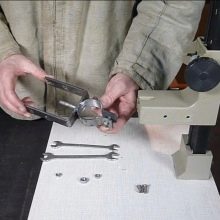

Such a system is usually equipped with a suitable bed and stand, and even a control mechanism equipped with a handle. In this case, the drill will be moved using the enlarger handle, which should be turned. Before use, it will be enough just to remove the tank with a light bulb and lenses and install a drill clamp on the vacant space.
In addition, it will be possible to create a machine from the steering rack. In this case, the part is taken most often from cars of the domestic auto industry, for example, VAZ, Tavria or Moskvich, and serves as a rack and lifting mechanism. The foundation will need to be made by yourself. The advantages of a handmade design are called the low price and availability of materials that can be purchased at enterprises or even found on their own among the waste - previously used parts are not a problem. Among the disadvantages of such a specific machine is called its unpresentable appearance, as well as not too outstanding accuracy.
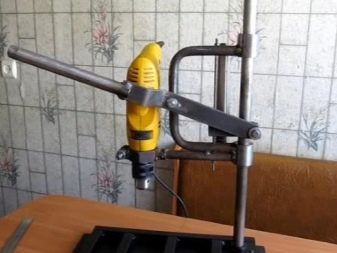
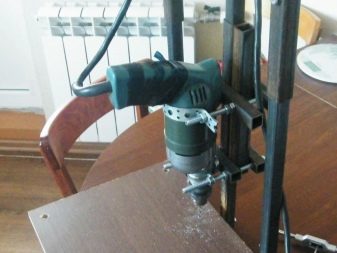
By the way, for the manufacture of a home-made machine, one important rule applies: the more powerful the drill, which is intended to be used, the stronger the entire auxiliary structure should be. In a situation when the stand is made of wood, it should be understood that this material is rather weak, capable of deteriorating when the humidity in the room changes, and is also often subject to backlash.

Preparation
There are two main steps to take in the preparation phase. The first is to find drawings of the most suitable design on the Internet. The second is to prepare the required tools and materials.
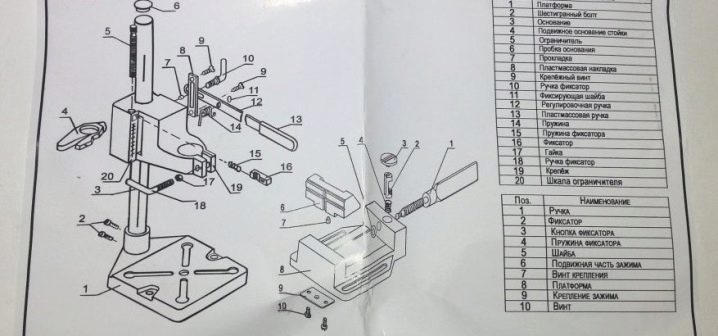
For example, to create the simplest drill stand you will need:
- wood planks, the thickness of which reaches twenty millimeters;
- medium-sized wooden box;
- furniture guides;
- a threaded rod, which is responsible for the possibility of movement in the structure;
- about twenty screws and thirty self-tapping screws;
- joiner's glue.


In addition, it is worth preparing a saw, a clamp, screwdrivers, sandpaper and, of course, the drill itself.
Manufacturing instruction
In principle, the assembly of almost any stand for a drill follows the same scheme. After the frame has been selected, and the corners are attached to it, if necessary, a support for the rack is fixed on it. In the next step, the post itself is connected to the base using screw connections. Then each rail must be mounted on a rack, which is convenient to do with furniture fasteners. It is important to mention that the guides must be free of lateral play.
At the next stage, a carriage is installed on the moving element, on which the holder for the drill itself will be located.

The dimensions of the carriage are dependent on the dimensions of the drill. It is possible to fix the drilling device in two ways. Firstly, it can be clamps that will pass through specially drilled holes in the carriage. For a secure fit, they will have to be tightened very tightly.
Secondly, the device is fixed using a special block - a bracket.


It is usually made from a wooden plate, attached to the base carriage at an angle of ninety degrees and reinforced with metal corners. In the block itself, you will need to make a circular cutout for the drill, the diameter of which is half a millimeter less than the diameter of the drill, as well as a slot to fix the drill in the hole. The hole is created either by a cylindrical nozzle or by a simple instruction. First, the diameter of the drill is measured and a circle is drawn on a wooden plate. Several holes are made along the circumference on the inside. With a file or a special tool, the gaps between the small holes are cut off, and the resulting hole is processed with a file.
In order for the drill to move quietly up and down, you will have to create another important node from the handle that starts the movement of the carriage, as well as a spring that returns it to its original state.

The latter can either be docked with the handle, or it can be placed separately at the bottom of the carriage using special grooves. In the second case, when the handle is pressed, the carriage with the fixed device goes down, and the workpiece is drilled accordingly. At this time, the springs store energy, and when the handle is released, the carriage will return to the top.
Additional nodes
Additional units allow you to make the machine more functional, for example, to be able to drill holes at an angle, perform some turning operations or even milling. For example, to ensure the latter, you will need an attachment that will allow you to move the part horizontally. For this, the horizontal table is given mobility, and a special vice is mounted that will clamp the part. For example, it can be a helical gear, which is activated with a handle, or a conventional lever, activated with a handle. In other words, a second stand is installed on the machine, but already horizontally, and a vice will be placed on it instead of a drill.


You can drill at an angle if you use an additional rotary plate with holes located in an arc. On this rotating axis, the carriage will move along with the drill, and the axis itself will be fixed on the bed. The holes with which it will turn out to fix the position of the working head, as a rule, are cut at an angle of sixty, forty-five and thirty degrees. Such a machine equipped with a rotating mechanism can also be used for turning operations if the additional plate is turned horizontally.
The rotary mechanism is made as follows: a hole is made on the stand and in the rotary plate, suitable for the axis.


Following in a circle on the additional panel, you need to drill holes at angles, which are measured using a protractor. At the next stage, the holes for the axes of both parts are aligned and fixed with a feint. Then, through the additional panel on the stand, you will need to drill three holes, and fix the first one at the desired angle with pins or a combination of screws and nuts.
How to make a stand for a drill with your own hands, see the video.
The comment was sent successfully.