Drill machines: what are there and how can you make?

An electric drill is a versatile tool. In addition to its intended use (drilling holes), it can be used for many types of work. After all, the drill chuck allows you to clamp not only drills, but also cutters, grinding elements and even wooden blanks for turning. Therefore, from this tool, you can make several types of full-fledged home machines for processing and manufacturing various materials and parts.

Features of the use of machines
Working with a drill while holding the tool with only hands significantly limits its capabilities. The weight of the tool and vibration do not allow the drill to be rigidly fixed in the desired position. But if you think over and design a special bed, where it will be stably attached, then an ordinary hand drill will turn into a professional, almost industrial equipment.
You can independently make the following types of machines from a drill:
- drilling;
- turning;
- milling;
- grinding.




Moreover, after replacing the working or cutting element, the machines become interchangeable. Provide two-in-one function, such as drilling and milling machine, lathe and grinding. It all depends on the installation conditions and the needs of the owner.
The power of the machines and their capabilities will depend on the type of drill (the power of its electric motor), the method of fastening, since it is in this case that it acts as the main working part of the equipment.

Types of machines
Despite the self-made assembly, each machine allows the production of a wide range of parts of varying complexity and configuration. With the correct installation of the unit, it will practically not be inferior to professional factory counterparts in terms of accuracy and speed of operation.
If you use a high-power drill, designed for long-term uninterrupted operation, then on such a machine it is possible to establish serial production or processing of various elements.
At home, such machines are able to fully satisfy household needs for the repair of furniture, cars, bicycles and many other things of everyday use. They will help you implement many design solutions without the need to go to specialized workshops.
Each type of machine provides for different work and has its own characteristics.
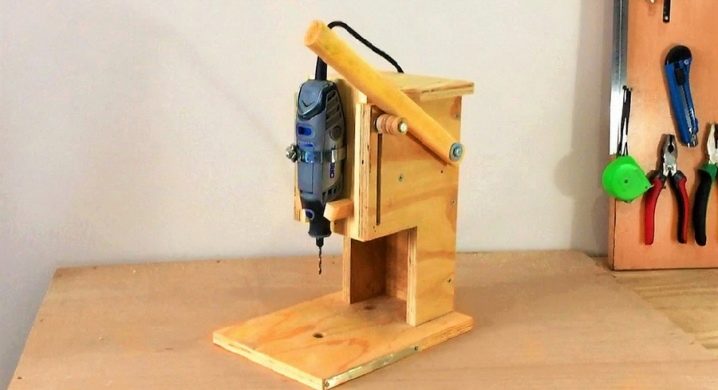
Boring
A drilling machine is necessary to form holes in various surfaces - both flat and multifaceted elements made of wood, metal, plastic, glass. The diameter of the hole and the material of the part are determined by the type of cutting element used - the drill.
The principle of operation of the unit is based on the fact that the mechanism that provides the torque of the cutting element (in our case, the drill) is located directly perpendicular to the surface to be treated on a special bed - a spindle fixed to the rack. When the spindle is lowered, the drill enters the surface and makes a hole in it.


The main advantage of working on a machine over manual processing is the hole is more accurate... A fixed drill can be sharply focused and directed to the desired location.
You can fix the drill on an additional longitudinal bar located perpendicular to the lowering / raising spindle on its body - this will allow you to move the fixed tool not only in the vertical, but also in the horizontal direction.

Turning
The processing of parts on a lathe occurs due to the rapid revolutions of the workpiece around its axis, which are provided by a spindle rotating from an electric motor, in this case it is a drill chuck. The cutting element is fed manually from the side, perpendicular to the rotating workpiece, or penetrates, depending on the type of work being performed.
The lathe is used for internal and external machining of metal, wood or plastic parts:
- threading;
- screw-cutting works;
- trimming and processing of ends;
- countersinking;
- deployment;
- boring.

The workpiece is clamped in the machine between the torque-providing element (drill chuck) and the clamping guide sleeve. The clamping sleeve is placed on special runners and is fixed in the desired position with a nut. The length of the runners will determine the size of the workpiece that can be installed in the unit..
In this case, with the independent manufacture of the machine, the length of the runners is determined individually according to the wishes and needs of the owner.
The drill is fixed in the frame "tightly".

Milling
A milling machine is used to process metal and wood blanks using a milling cutter - a tool with special cutters, teeth. During operation, the cutter, turning around its axis, removes a part of the outer layer from the workpiece, giving it the required shape.
Grinding and other works are performed with the help of a cutter:
- cutting;
- sharpening;
- facing;
- countersinking;
- scan;
- threading;
- manufacture of gear wheels.



In the case of a homemade mini-unit, the milling nozzle is clamped into a drill chuck attached to the bed. The workpiece is fed by hand or is also fixed in a special clamping device.
Grinding
With the help of a grinding machine, various surfaces are cleaned, making them smooth. Also, grinding helps to change the shape of the workpiece, to give it the desired structural appearance, for example, in the woodworking version of the equipment.
Sandpaper is usually used as a grinding element.... A special nozzle is clamped into the drill chuck, which has a rough surface - a grinding block.
There are nozzles that provide for the replacement of the grinding material - a sheet of sandpaper is fixed on their flat working surface with the help of special "Velcro" located on the back.


The grinding process is carried out by processing the workpiece with a nozzle with a grinding coating rotating in the drill chuck. Thanks to abrasive spraying on sandpaper, it removes part of its surface from the workpiece.
During the manufacture of the machine, the drill is clamped and fixed in the bed in one position, and the workpiece is fed manually.
An additional stand can be used as a stop for the workpiece - for convenience, it can be placed on runners, just like in the case of a lathe.
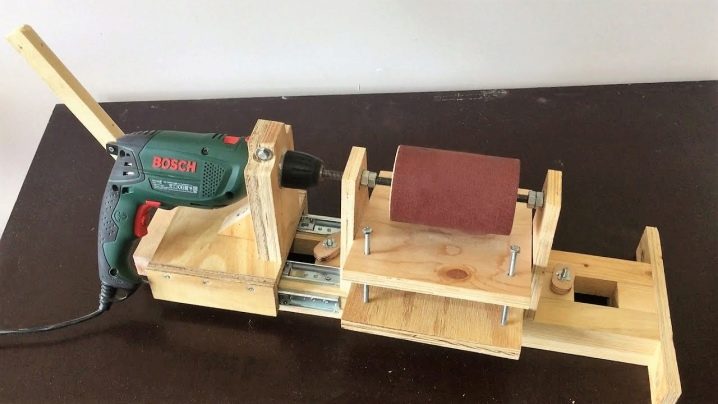
Required materials and tools
The torque-generating element, and accordingly the main working part in each type of machine is a drill. The type of processing will largely depend on the nozzle installed in its chuck. Therefore, they will need identical materials to assemble them.
To assemble a lathe, grinder:
- rectangular metal or wooden base, bed;
- clamping sleeve;
- a pressure headstock, which will be attached to the drill chuck;
- runners for the clamping sleeve;
- seat for fixing the drill.

Materials for assembling a drilling, milling machine:
- square bed;
- a metal stand on which the spindle with a fixed drill will move;
- spring corresponding to the diameter of the rack;
- workpiece table;
- pin for fixing the table.

Of the tools you will need:
- screwdriver;
- pliers;
- hacksaw for wood or metal;
- fasteners - bolts, screws, nuts;
- welding machine.

If you plan to manufacture a metal machine, then a prerequisite will be the presence of a welding machine. Since the machine is intended more for home use, its drawings and dimensions of the constituent elements are set individually.
Manufacturing algorithm
Considering that by the type of processing, home machines will be interchangeable, and the nozzle installed in the drill will play a decisive role, we will consider two main options for homemade units - horizontal and vertical.
The assembly procedure for a vertical machine is as follows.
- Cut a 50 x 50 cm square base from a piece of metal or wood, 10 to 20 mm thick.
- Exactly in the center at a distance of 1-2 cm from the edge, drill a hole in it for mounting the rack. The diameter of the rack must be at least 5 cm.
- Install the stand, center it with a level and weld with a welding electrode. If a wooden machine is made and the rack is wooden, then rigidly fix it with self-tapping screws.
- Fix the drill with metal clamps on the movable element, which will be put on the rack, forming a lowering / raising spindle.

- Put the spring on the rack. Its length should be at least 2/3 of the rack.
- After placing the drill on the stand, mark the place where the drill will fall when lowering the spindle.
- According to this place, cut two through hollows in the bed crosswise.
- A table is installed in the hollow on a threaded pin, on which the workpiece will be attached. A nut is screwed onto the pin from the bottom side, it will fix the table in the desired position. From the outside, you can also attach the table to the pin with a nut, sinking it into the surface of the table so that it does not interfere with the stacking of the workpieces.
- It is important that after locking with the nut, the length of the outer part of the pin is flush with the top of the stage.

The workpiece is placed on the table (if necessary, it is fixed with clamps) and moves along the grooves in the desired direction. The drill is lowered by hand, raised back by a spring. To convert the machine into a milling or grinding machine, it is enough to replace the drill with the appropriate attachment - a milling cutter or a grinding block.
The assembly algorithm for a horizontal machine looks like this.
- Cut rectangular bed - dimensions are determined individually.
- On one edge, fix the seat for the drill with a hollow in the upper part corresponding to the size of the tool.
- Fix the drill on it with a clamp.
- Cut a through groove for the pin along the bed, and install two metal corners along the edges, along which the pressure sleeve will move.
- The width of the clamping sleeve must exactly match the distance between the guide angles (runners). From below, a threaded pin is screwed into it, which will move in the hollow.
- Having moved the sleeve close to the drill chuck, determine the place where a special headstock will be installed for fixing the workpieces.
- Attach a headstock with a centrally positioned metal tapered pin to the bushing.
- The sleeve is fixed in the desired position (for clamping the workpiece) with a nut screwed onto the pin from below.





Just like the previous one, this machine can be used not only as a lathe, but also as a milling or grinding machine. You just need to clamp the necessary working element in the drill chuck - a cutter, a grinding block, a drill.
In both versions, it is necessary to provide special adjustable legs for the bed.
If the bed rests flat on a workbench or table, it will become impossible to adjust and fix the clamping sleeve on a horizontal machine or a table for workpieces on a vertical one.

Tips from the masters of operation
It is recommended to make such machines only from metal elements - a bed, a clamping sleeve, a stand. The wooden structure is easier to assemble, but has a shorter service life. It can fail even from insignificant mechanical damage - accidental shock.
In addition, the wood post withstands less pressure, making it more difficult to drill a hole in hard material on such a machine.
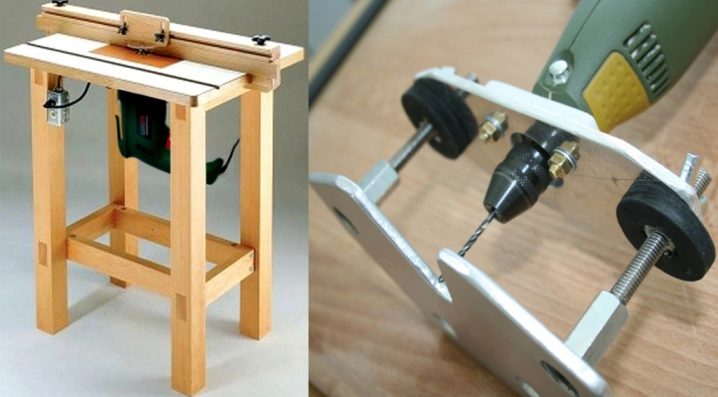
It is recommended to choose a drill model only from a series of professional tools designed for long-term and frequent use.
You should think in advance about the fact that you may have to process particularly durable materials, so it is better to have a drill with an impact function.
It is important to understand that the power of a hand drill and its speed is much lower than that of electric motors on industrial machines. Therefore, do not overload the tool in order not to burn its engine.

For information on how to make a machine out of a drill with your own hands, see the next video.
The comment was sent successfully.