Disc bits for a drill: features, types and tips for choosing
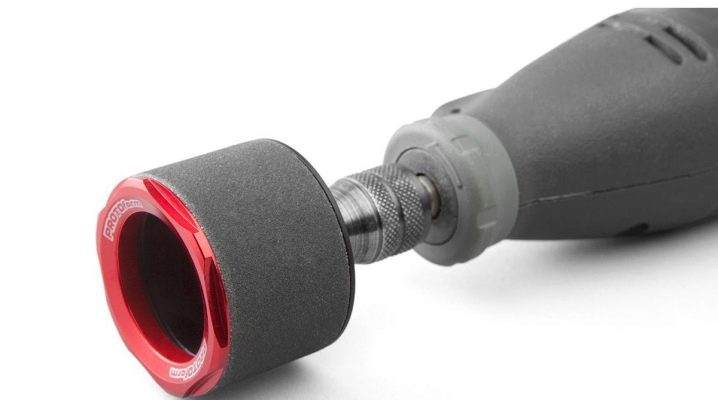
The drill is a multifunctional tool that is used everywhere: during construction work, repairs, or when assembling pieces of furniture. The use of all kinds of devices (nozzles, adapters, attachments, adapters) on the device makes its field of activity more extensive. One of the possible functions with the use of an electric drill is grinding a variety of surfaces made of concrete, wood and metals. We recommend that you familiarize yourself with the various attachments for an electric drill.
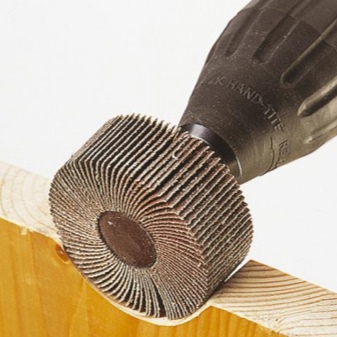

Areas of use for drill bits
Thanks to a solid selection of all kinds of attachments for an electric drill, it is able to replace many highly specialized devices. So, in particular, grinding discs make it possible to eliminate the need to purchase a grinder, and the attachment for screwing screws and screws will replace a screwdriver. With the help of such additional equipment, the following works can be carried out:
- grinding;
- polishing;
- cutting (cutting disc for cutting);

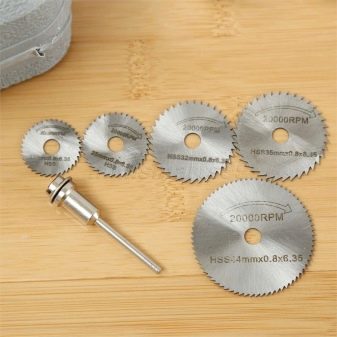
- mixing;
- screwing;
- drilling holes of various diameters;
- sharpening (grinding disc) and milling.



Such a device becomes really necessary when grinding or polishing of various coatings and objects is planned.
This could be:
- paintwork (LCP);
- wooden and metal surface;
- small elements made of steel or other material;
- glass.

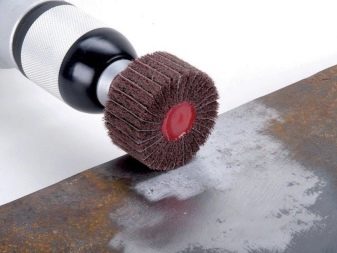
It should be said that individual nozzles (cleaning disc) make it possible to clean all kinds of objects from rust, scale, paint fragments and various defects. In addition, it turns out to be able to sand the glass edges.
With the correct use of attachments, the effect will be the same as when performing the same work using specialized single-purpose equipment.


Positive and negative properties of the nozzles
Some specialists, when purchasing an electric drill, take a batch of products at once, which includes nozzles for polishing and grinding. This is due to the considerable number of positive properties of these devices.
- Reasonable price. Thus, it will be possible to process the surface without spending money on the purchase of specialized equipment.
- Multifunctionality and diversity. Now on sale you can freely find a variety of grinding tools, thanks to which it will be possible to carry out even the most difficult work.
- Practicality of application. Certain types of nozzles are capable of treating even the most inaccessible areas.
- It's easy and simple with them handle all sorts of small items.


The disadvantages of grinding and polishing agents include the following points.
- Poor performance due to small size.
- Discomfort when using certain specialized devices.

Basic types of rigs for selection
Experts have over ten samples of attachments for electric drills. All of them are realized in the form of a core on which a grinding or polishing material is fixed. The conversation is about abrasive: sandpaper, felt, diamond dusting and so on.
Despite the strong similarity, such tools have a number of fundamental differences.
- Tray type fixtures equipped with a rod, with which it turns out to fix the element in the cartridge. The most comfortable are adjustable rods, since in this version it will be possible to reproduce the outline of the surface with jewelry, compensating for the displacement of the tool. Rigid fixation is easy to use, but it can ruin the work.
- From poppet nozzles specimens made from soft materials, including rubber, are ideal. In this case, the hard mate is taken into account. It should be noted that any nozzles are equipped with sandpaper with a special coating placed on the opposite side.

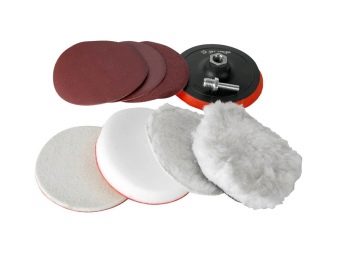
- Cup-type attachments. They can differ in their own structure. So, some samples are an iron case, equipped with a rod. Coarse iron "bristles" are placed inside the casing. This device for an electric drill is used in the processing of surfaces made of wood and steel. Additionally, it makes it possible to remove rust and old paintwork.
- Other cup parts without padding. Here, plastic is practiced to create the casing. In the course of work, scrupulousness is fundamental, otherwise you can spoil the material due to the incorrect location of the electric drill.
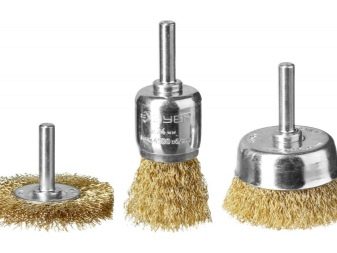
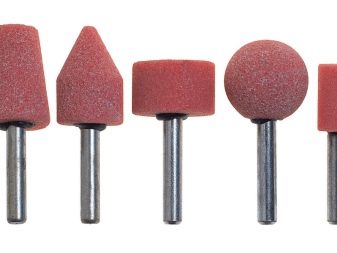
- Disc nozzles. Disc-shaped polishers consist of a pin, an abrasive and a shell. These are direct prototypes of cup types, since they have a similar structure. They stand out among the devices presented above in that the wire ("bristle") has a different direction: from the middle to the edge. Fan-type devices are also related to such nozzles, or - a petal disk (when the petals from the sanding paper are fixed parallel to the base). Such products are practiced for cleaning inaccessible areas and require some skill and experience.
- Another modification of the fan disc is also practiced: when absolutely all of its small components are assembled into a single cylinder. Such devices are used when cleaning aluminum radiator elements for cars, ends and side planes from solidified solder after being removed from a special oven, where they are soldered.
It is advisable to use such means extremely carefully, otherwise you can damage the material or get injured. Disk devices are considered critical when handling inaccessible areas and compact elements.


- Drum attachments have a cylindrical shape, on which a sanding cloth is fixed. Such designs for electric drills are produced soft and rigid, it depends on their purpose. The sanding tubes are fixed by inflation or tension. Through them, the processing of iron, glass and wood is carried out. With proper use, it will turn out to polish even small round holes.
- Fan or lobe radial the devices look like a mini-disc in the middle, and petals of sandpaper or other similar material are fixed to its edges. Such structures are extremely necessary when processing interior spaces and all kinds of inaccessible places. Due to the design features, it turns out to process products of almost any configuration. A suitable rod is used to fix the fixture itself.

- Soft modifications are fixed by a rod and clamping washers. In the role of grinding and polishing materials are used: felt, leather or foam coverings. In addition, sometimes other varieties come across. Due to such a nozzle, it is possible to produce high-quality polishing of various surfaces.

- End devices Looks like a cone soldered rod made of specialized material. Certain types visually resemble a spherical electric soldering iron or a bullet.Strong steel alloys are used to make the tip under all conditions. With the help of the end nozzle, it turns out to bore holes, eliminate a variety of flaws and make the surface very smooth. As a consequence, such devices are most often practiced in jewelry production.

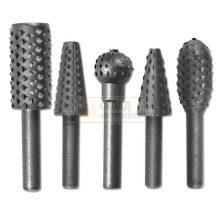

Grinding wheel selection options
The main criteria for choosing a material are:
- the properties of the grinder - they must match the consumable;
- sanding surface - select discs with an abrasive coating that is optimal for working with it;
- expiration date.


Selection by type of polishing
For metal
Any metal polishing disc has flexibility and elasticity. Thanks to this, the nozzle adheres firmly to the plane.
For polishing iron, products are practiced from:
- sheepskin;
- x \ b;
- cloth;
- coarse calico;
- fur;
- sisal.


For stainless steel
Stainless steel processing involves a number of steps. First, use discs with grit P180 with alumina. It is worth starting with the smallest grain. If there are no changes on the polished surface, after 4–5 strokes it is necessary to resort to a harder nozzle.
After initial polishing, the surface roughness is gradually reduced. For this, attachments with Velcro alumina with different grain sizes are methodically replaced:
- P320;
- P600;
- P800.
Finishing starts with a dense felt wheel and polishing paste. You can remove all irregularities after felt with soft felt.


For glass
For glass, take disks made of felt or with a felt base. The discs are supplied with various abrasives. Its share is recognized by its color:
- green - rough polish;
- blue - medium scratches;
- brown - small scratches;
- white - eliminates roughness and small scratches.


For wood
Apply:
- felt circles;
- with replaceable sandpaper;
- fabric;
- foam rubber.
Fan devices are used as final ones, since they give the smoothest plane.

For an overview of the necessary drill bits, see the following video.
The comment was sent successfully.