Drill: what is it, how to choose, repair and use?

Any master will tell you without any doubt that the drill is one of the most important tools. Even professional builders do not argue with such a statement, who, at first glance, do not use it, but at the same time, many mixers, screwdrivers and electric screwdrivers from manufacturers are called a drill. The prototypes of modern drills have been around for a very long time. The first instruments appeared in the Renaissance, then they were based on muscular strength, but since then science has stepped forward - now you can find a large selection of electric and battery models on store shelves.

What it is?
A drill is a popular hand or power tool used to rotate the drill in order to make a hole in hard horizontal and vertical surfaces. It is widely used in repair and finishing, as well as carpentry, turning and locksmith's types of work. Hand mechanisms and are specialized mechanical type tools. They can be single-speed, which have only an overdrive, and two-speed, for which the user can choose to increase or decrease the rotation speed.





However, these days, hand drills are used quite rarely, their place has been firmly taken by electric and battery units.
The very first electric drills appeared back in the 70s of the XIX century, immediately after the invention of electric motors, then new mechanisms were introduced into many industrial sectors: in medicine and mining. As the models improved, their instrumental modifications began to appear, which found their application in shipyards and factories.
Today, a drill is an ergonomic tool, made mostly in the shape of a revolver. Its wiring diagram includes a traction converter along with a start switch, as well as a rheostat, reverse and an electric motor, and a special mechanism for engaging with a spindle is included in the design, a cartridge is placed on the shaft that holds all kinds of attachments. In modern versions, there are Morse tapers on the shaft, which are necessary to hold the drills in them.




Design features
Compact drills are usually made in the form of a cylinder, they are needed to create shallow holes and are able to be held in the palm of your hand like a handle. In the same version, angular products are also made, which are used for drilling in the most difficult-to-reach areas, while the latest modifications are additionally equipped with a gear drive for free changing the angle of inclination of the axis up to 90 degrees. This feature makes it possible to drill holes, for example, on the sides of rather narrow niches. All others are made in pistol-shaped form.
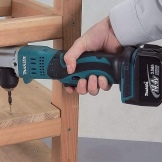



Any drill has basic structural elements.
Cartridge
For the most part, tool drills contain a jaw-type chuck. It is a small body made in the form of a cylinder; an adjusting sleeve moves along its surface. With its base, such a sleeve is fixed to the shaft on one side, and on the other, various attachments are fixed to it.The adjusting sleeve moves in the inner part of the housing along guides made of metal, which either approach each other or, on the contrary, move away.


A small threaded or tapered hole is provided in the chuck drum for fastening to the tool shaft. There are cartridges that are specifically used in rotary hammers with the ability to replace the cartridge. The structural features of the device allow you to attach nozzles with a shank of the most various configurations and practically of any size from 0.8 to 13 mm.


For the fastening to be more reliable, the cartridge must be tightened with a certain effort. Depending on the mechanism, there are two types of chuck: standard and quick-clamping. In the first case, the adjusting rings are opened and clamped under the action of a special key, in the second, a ribbed plastic sleeve is used, it is moved by hand without using a tool so as to keep the cartridge body from unnecessary scrolling. There are modifications in which the shaft is automatically blocked, then the blocking is done by pressing a special button on the outer part of the housing.

Both models have their pros and cons. The standard chuck is tightened with a wrench, so that the tightening force is increased and the bits do not loosen during use, but this work requires the wrench itself and the application of physical force. BZP is devoid of these shortcomings, but such models are an order of magnitude higher.
Reverse and speed control
For any drill, the ability to change the direction of movement is very important, it is for this that there is a special switch on the body of any model, as a rule, near the handle, so any user can switch the speed without being distracted from their work. The reverse is necessary for turning out the hardware and removing the stuck nozzles. Typically, a set with a drill includes: an adapter with a regulator, an adapter, a pump, a jig, a drill, and a dust collector.

Views
Drills are different: low-speed and powerful, large, power, air, straight, gasoline, gear and many others. However, the most basic difference between them is the mode of use. There are household tools for home use, and there are professional ones, and the latter are several orders of magnitude more expensive. The difference comes down to the features of the operation. Not everyone needs a drill in order to drill holes day and night; in most homes, the tool "peacefully" gathers dust somewhere in the garage until it becomes necessary to carry out minor repairs, for example, fix the kitchen cabinet doors or hang a picture on wall.

For such an application, household drill options are used. They are less powerful. According to the technical conditions, they cannot be used for more than 5 hours a day, and the work must be carried out according to the 1 to 1 scheme, that is, we work for 15–20 minutes, and then we take a break for the same amount. Such devices use rather simplified designs, less durable materials and weak engines.




The professional tool features motors with much higher power parameters, the parts are made of wear-resistant materials, and the drill itself is supplemented with multi-stage protection against water and dust ingress, as well as against vibration. Do not think that the functionality of household tools is limited - this is not at all the case. Usually, such devices allow you to drill, drill and even twist, but professional units are just distinguished by narrow specialization.




Household drills are characterized by fairly good ergonomics, they have a low weight, since low-power motors are used and there is no metal gear case, and all other parts are significantly lightened. The body has a lot of soft inserts and various types of linings. The chuck is usually keyless.Household drills are often used by inexperienced craftsmen, so the manufacturer was worried about limiting the power parameters of the product and improving the protection of operators. Typically, these drills are equipped with a set of drills, a spare chuck, a battery, and a bit holder. Household appliances do an excellent job with all the tasks assigned to them, but only if the load on the tool is moderate.

Professional drills should easily withstand 8-9 hours of work with short breaks every 40-45 minutes, so they are used only by builders, furniture makers and professional finishers.
Two-speed
In simple terms, this drill is a 2-in-1, that is, the high-speed gearbox at the first speed allows you to tighten or unscrew the screws, and at the second, it drills a hole in wood and plastic. At both speeds, there is a possibility of adjusting the speed, so both drilling and twisting are as comfortable as possible. Within reasonable limits at first speed it can be used as a mixer, suitable for paints and varnishes and dry mixtures. The disadvantage of such mechanisms is associated with their heavy weight and powerful dimensions.
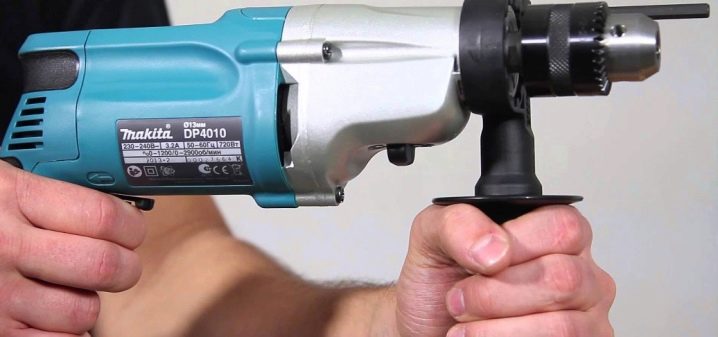
With speed control
The ability to adjust the speed is a very important function for any drill, since in most cases a high speed of rotation is not required at all, for example, when drilling metal surfaces, it is best to reduce the speed and drill the coating at low speeds, and if you drill the base at fast rotations, then you can just break the drill. And if you are working with wood, then, on the contrary, it makes sense to increase the speed of movement. Thus, some types of drills allow you to set the operating mode (it can be low-speed or high-speed, depending on the type of material in which drilling is performed).
Network
Everything is simple here: if the drill is powered by an electric current, then it is called a network. Such devices are characterized by increased power and ease of use. The only thing that should concern you is finding an outlet and connecting the power cord to it. However, this is the minus of such a unit: the operation of a power drill is impossible in places where there is no current source or in conditions of frequent power outages.

Grinding
In work, a wide variety of grinding and polishing specialized attachments for electric drills are often used. They will be required when performing the following types of work:
- polishing of various types of coatings: wood, metal, plastic and glass surfaces;
- cleaning metal from rust, removing old finishing coatings;
- grinding of metal, wood and composite materials;
- cleaning concreted shelters from sloppy sags and burrs.

Reversible
The reversible drill is responsible for the reverse rotation option, it is used in situations where the drill, for example, gets stuck in the work base. From a design point of view, this modification is an almost weightless small-sized technique equipped with a cam chuck. It is ideal for drilling spot holes in a wide variety of materials.

Brushless
Already from the name it becomes obvious that there are no brushes in the engine of such a tool; instead, the model is equipped with electronics. This structure has many advantages:
- the engine will receive a longer service life;
- the range of speed adjustment increases;
- the tool becomes more durable and reliable.

However, there were some drawbacks. Users note that despite the increase in resource, all other parts, for example, bearings, constantly fail.To shift their resource to the resource of the engine, high costs are required, which in general only increases the final cost of the product. That is why brushless drills in our country are rather exotic, and very, very expensive.

Wireless
A very convenient version of the drill is the battery-powered version. The cordless drill is ideal when access to the power supply is difficult. In addition, the absence of a power cord greatly facilitates maneuverability and freedom of action when working with a drill. When working with such a device, it is necessary to constantly monitor the charge level and even periodically replace the battery with a spare one.

The most popular type of battery is considered to be lithium-ion: such units are lightweight and are practical and durable. Nickel-cadmium batteries perform well in low temperatures, but have a memory effect.
Let us explain with an example. Suppose that you have 20% of the charge left on the battery, and you set it to charge. In this case, it may happen that the next time the tool stops working when the charge level drops to the same 20%. Of course, this significantly reduces the efficiency of work, therefore, nickel-magnesium batteries are often used in drills, which do not have such a pronounced effect, and weigh much less.

How to choose?
It is not so easy to choose the best option from all the variety of Russian and imported drills on the modern market, especially if you are a non-professional builder. Pay special attention to important characteristics.
Power parameters
In most cases, the power of the instrument varies from 400 to 900 watts. There are more powerful mechanisms, but they are applied in the professional field. The higher the power setting, the higher the torque required to drill deep holes. At the same time, with an increase in this indicator, the weight of the instrument also increases, be sure to take into account the physical characteristics of the person who will work with it. If this is a flimsy man, then he may not be able to hold the overall mechanism in his hands for a long time.

Another parameter that you need to pay attention to is the rotational speed. Typically, the operating manual indicates the rated speed, calculated at idle. It turns out that the larger it is, the cleaner and the final hole will turn out, and even for a low-power unit, this parameter opens up great opportunities. In addition, higher speeds should be selected for impact mechanisms, for example, if you plan to use devices for grinding and polishing. But to work with hardware, speed is not required, here 450-500 rpm will be quite enough.

The parameters of power and speed of torque are very closely related to each other, when any of them changes, the other immediately changes, so the choice must be made in a comprehensive manner.
Assistive devices
The reverse allows you to unscrew the fasteners, and also to free the stuck equipment from the "captivity". The multi-piston reducer is used to increase the torque and thus reduce the gear. Usually, the first speed means higher torque and low frequency, and the second, on the contrary, means higher frequency and low weight. Such tools are much more effective than all the others, since the finishing power does not change with the change in the speed parameters.

Pay attention to the features of the cartridge. We have already mentioned that they can be conventional and quick-release. The first type is considered more reliable, but is usually installed in professional tools.For domestic use, it is better to give preference to quick-clamping mechanisms, which allow you to change the drill if necessary in a matter of seconds and without any effort. If you have a tool with a metal gear case in front of you, then this clearly indicates that the drill belongs to the professional category. Due to this design, the heat dissipated for the moving parts is more efficient, and thus the required durability of the assembly is determined. However, the result will inevitably increase the weight of the product as a whole.

The most advanced modifications are equipped with special winding heating sensors, due to which the likelihood of damage to the electric motor at increased loads is minimized. In any emergency situation, the power is automatically stopped and the indicator LEDs are activated.
If you are buying a fairly powerful drill, then an option such as a smooth descent will be useful: it accelerates the rig rather slowly and completely eliminates starting jerks. There is no room for little things when choosing a drill - every detail counts, so take a look at what the tool looks like. When inspecting the tool, shake it a little, make sure that the rubberized handle is comfortable, feel all the calcinations - preferably, their surface is grooved. Enjoy the accessibility of all control systems and the ease of switching buttons.

Inspect the power cord. Firstly, you need to make sure that it is intact, and secondly, that its length matches the characteristics of your room. If possible, give preference to models with an anti-lock clutch: it protects the mechanism from burnout in the event of a mechanical collision, and also protects the operator from the risk of kickback. The most expensive products usually have an anti-vibration system.

Look for a spot light that illuminates dim work areas. It will not be superfluous to purchase a tool with a dust collector. In this case, the tool will independently collect dust that appears when interacting with concrete and stone bases. Pay special attention to the configuration. Many manufacturers sell a charger, a spare battery, a set of drills and other elements together with an electric drill.If you are sure that all this will be useful to you, it is better to buy the maximum sets right away: it will be cheaper than if you then buy all the necessary additions separately.

Rating
The greatest demand among buyers is for drills of only a few trusted manufacturers. Bosch Is a company specializing in the manufacture of household and garden equipment, including power tools. It has been operating on the market for over 100 years and has successfully conquered the market of more than 150 countries.

DeWalt Is an American brand that is famous for the high quality of its tools. The products are manufactured at production facilities in Brazil, Germany, and Canada.
Metabo - a brand that sells its tools all over the world. This company can rightfully be called the leader in the segment of power tools in the global market.

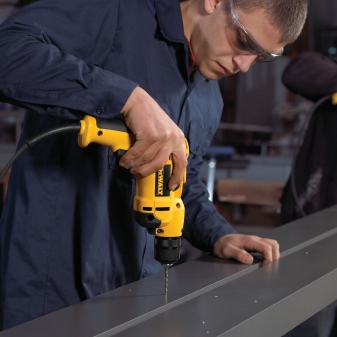
Makita Is a Japanese company that has gained fame for the production of high quality electrical and gasoline equipment. The company has its factories in 8 countries, and the scope of supply of drills is much larger - the company's products are presented on the shelves of more than 150 countries around the world.
Hitachi Is a Japanese company that has gained fame as a manufacturer of household tools, as well as air conditioners and other industrial equipment.


Applications
The scope of use of a drill largely depends on its type.At its core, the drill is a multifunctional mechanism, however, for more comfortable performance of certain tasks, individual models have structural features and an individual mode of operation.

Hammer drill
This tool is necessary for drilling in aerated concrete or masonry; upon contact with soft materials, it immediately turns off. Note that an impact drill is not a perforator at all: its power at impact is an order of magnitude lower and the principle of mechanical action is completely different. In an impact tool, the main role is played by the brush, which consists of sharp toothed couplings: when a load is created, one of them slides off the second, they are separated, as a result, the shaft begins to move progressively.

In a hammer drill, the impact is the result of the interaction of a special bearing and various pneumatic elements. An impact drill is needed for infrequent drilling operations; it is not suitable for frequent use.
Drill for screwing in hardware
Working with fasteners is considered one of the basic functions of the mechanism. In fact, it is possible to insert a self-tapping screw into absolutely any chuck, but some types of drills are more suitable for this than others. They have the following characteristics:
- the presence of a reverse;
- the ability to change the rotating speed;
- work in the mode of short jerks;
- closing force adjustment.

Drill mixer
In theory, all types of drills can mix viscous solutions, usually for this they are additionally equipped with various handles, and also equipped with a multi-speed gearbox. The power of such models is relatively low, so they work, but they do not overheat. Drill mixers are used for mixing dry building mixtures, as well as varnishes and paints.

Angle drill
These are drills that are needed to form holes and tighten self-tapping screws in the most difficult-to-reach areas where it is not possible to drill a perpendicular hole. They are equipped with an angle-type gearbox, the tool is characterized by low power and no impact function. Depending on the technical characteristics, drills can be used to drill wood, stainless steel and even cast iron.
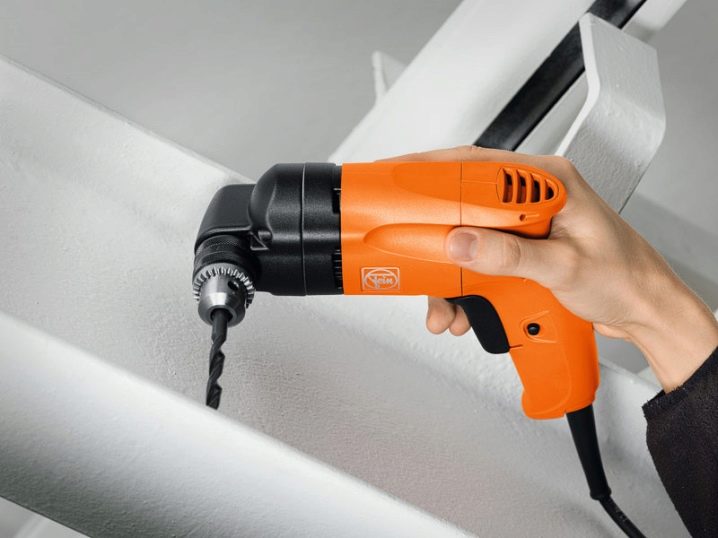
How to repair?
No matter how high-quality the tool is, it periodically fails. The most common faults are:
- breakdown of the stator or armature, which lead to failure of the electric motor;
- complete wear of the brushes;
- failure of bearings;
- breakage of the rotation adjustment button;
- oxidation or burning of the button contacts;
- cartridge breakage.

If you intend to repair a failed tool on your own, then first you should disassemble the tool, carry out a full diagnosis and find the cause of the malfunction. It should be noted that it is quite difficult and almost unrealistic to repair a broken part, therefore in most cases it is simply changed to a new one. If there is a loss of power or sparks, then inspect the cable. In most cases, such a malfunction is the result of a breakdown of one of the wires. In this case, you need to disconnect the device from the mains, check the cable with a multimeter. After that, the section is cut off, the wires are stripped, new contacts are formed.

The switch button starts to junk due to the fact that dust gets clogged inside the unit. Such defects are removed with a regular brush. Some inexperienced craftsmen try to lubricate the button with oil - this is a big mistake, because in this case the oil will mix with dust, and this will lead to a complete breakdown of the unit. If the shutdown button is broken, you need to remove the wall of the drill and clean off the carbon deposits on the contacts with fine sandpaper. Gearbox brushes periodically fail, they cannot be repaired, since they are erased during use. However, they can be replaced.

If the bearings do not work, then flush in kerosene, replace the internal oil seals and renew the lubricant.If the gearbox is damaged, you will need replacement gears. If you have a model from a well-known manufacturer, then finding spare parts in the store will not be difficult. But fixing the cartridge is quite difficult. If it was he who became the cause of the malfunction, you should contact the services of a specialized service center.

Operation and storage rules
In order for the drill to serve faithfully for many years, you must follow all the rules for its use and storage. At the stage of preparation for work, it is necessary:
- make sure that all foreign inclusions are absent;
- fix the workpiece with maximum reliability and do not hold it in your hands during the work;
- check the reliability of the fastening of the tooling in its chuck.
During the work you need:
- when working with hard and surfaces and viscous materials - hold the steering wheel with both hands;
- do not press on the object with a drill in order to hold it, otherwise it may jam;
- it is strictly forbidden to use the reverse switch if the engine is on and running;
- it is forbidden to release the tool from the hand if it is turned on and working;
- when working with the ceiling, it is better to wear safety glasses.

At the end of the work, hold the drill until it is completely turned off. After a while, do not touch the drills, even after the engine has stopped: this could result in severe burns. The drill should be stored in a special case or box.
For how to properly use the impact drill, see the following video.
The comment was sent successfully.