All about glued board
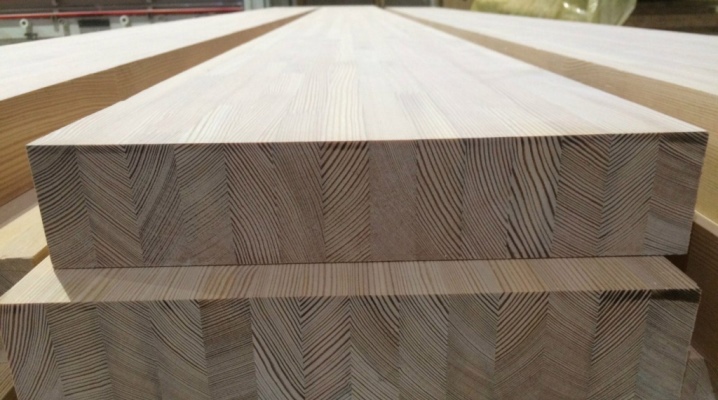
Currently, glued board is becoming more and more popular in construction. This wood material can be produced from a wide variety of wood species. It is manufactured using a special technology. Today we will talk about what the main characteristics of such boards have and how they are made.
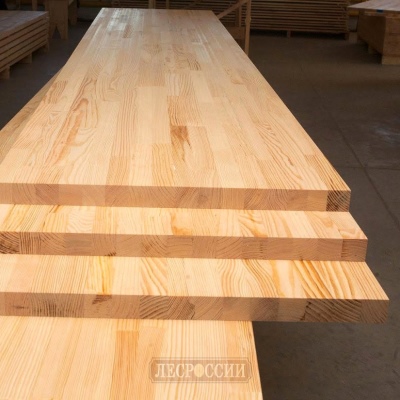
Characteristic
Glued board looks like a material consisting of wood surfaces glued to each other, sometimes beams, which is why it is called that. Such dry lumber is an environmentally friendly product, it is easy to handle even by hand, it is particularly durable and strong.
Such lumber has good fire resistance. They are difficult to burn materials.

Such wood bases, as a rule, undergo treatment with antiseptics and other protective solutions during the production process, which significantly extend their service life.
In addition, this type of boards has a relatively low cost, so it will be affordable for almost any buyer.... But at the same time, it should be remembered that such lumber during long-term operation can crack, deform a little. These bases also have some natural defects that reduce their resistance and durability.

Manufacturing technology
The production of glued material takes place in several stages. First, the selected solid boards are cut into separate parts, then the initial processing of the blanks is carried out. Prepared boards are allowed on small elements. After that, the wood is sent to the drying chambers.


As a result of its processing, the moisture content of the material should not be higher than 10-13%.
The dried workpieces are once again selected. The selected bars are trimmed, all irregularities, other defects are carefully removed from the surface of the tree. Later, the material is thoroughly machined, which allows you to correct the geometry of the products.

At the final stage of manufacturing, the processed workpieces are spliced together in width. The result should be smooth and neat lumber, ready to use.


Glued boards are sent to warehouses... There, the construction adhesive mixture finally hardens, the materials become as strong and resistant as possible. Before being sold, structures must be finished with special antiseptics and some other protective impregnations for wood.

Sizes and types of wood
Such constructions can be of various types. The following varieties can be distinguished separately.
- Materials made from pine and spruce. Such options are considered the most affordable, they perfectly tolerate high levels of humidity, temperature changes.

In addition, such species are distinguished by a special resinous content, which prevents insect damage to the wood.
- Products made from larch. These lumber are the most durable.
They boast excellent water resistance.

Constructions made of larch are practically insect-proof. But at the same time, the cost of these structures will be much higher compared to other glued materials.
- Cedar constructions.Cedar bases have an attractive external design, an unusual and neat natural pattern.Such boards are often used in the process of various finishing works.

This wood species has important bactericidal properties.
- Oak boards. Oak materials are particularly durable and resistant. They have a porous and beautiful structure, pleasant yellow or tan color. Like the previous version, oak boards are also often used for decoration. Cedarwood is fairly hard, dense and relatively heavy.

Oak is resistant to the formation of mold and mildew, the appearance of harmful insects.
This tree is used to make durable lumber.
Glued molded boards are available in various sizes... Samples with values of 50x200, 50x150x6000, 50x300, 200x50, 50x150 cm are considered standard.The thickness can also vary, most often there are products from 25 to 50 mm, thinner varieties with a thickness of 10 mm are also sold.

Which glued solid wood to choose?
Before purchasing such wood structures, it is worth paying attention to some significant nuances of the choice.
So, you need to pay attention to the type of gluing.

Popular options are considered:
- Microthorn connection. In this case, the fitting process will be as simple as possible, since the gap will eventually be hidden. But with insufficient press load, the seam can turn out to be too thick and very noticeable.

- Molded model with smooth connection. In this case, during manufacture, the thinnest, barely noticeable seam between the layers will be formed. But this gluing technology requires more careful processing and adjustment of the lamellas.

- Sandwich panel connection... This connection is considered the most economical option because it allows the production of finished material with almost no waste. But at the same time, the external design of such lumber will spoil the ends.

- Double gluing along the thickness and width of the product... Such a compound is used in production, where a thirty-millimeter board is taken. Such workpieces dry out more quickly. With proper adjustment, the result is the most durable array.

When choosing a glued board, you need to pay attention to the texture of the wood from which they are made.
Remember that the lamellas do not have to include the core.
Different options can have all kinds of lamella joining types.
Models with "furniture board" docking are special pieces of short length. In the process of creating them, all knots and other irregularities on the blanks are necessarily removed.

Also distinguish between a furniture board, which is sheathed with solid lamellas. In this case, the product is the same product as in the first version, but at the same time it will be additionally attached to boards on both sides, the thickness of which is from 5 to 8 millimeters.
In some cases, a set of lamellas of arbitrary or equal width is used. In this case, wood blanks of the required size are selected, on their surface there should not even be small knots, scratches and cores. Moreover, the longer the length of such products, the more difficult it will be to find a suitable material, in addition, the cost of such structures will be much higher.

Please inspect the surface of the material carefully before purchasing. Models made of low-quality wood will not be able to serve for a long time, soon the structure will begin to deform and collapse.
Also, when choosing, make sure all layers are made of well dried wood. Otherwise, the product will not be durable and reliable enough.

Do not forget that during operation the lamellas will change their parameters. When joining a tree, only a new shape is given to it, even an array treated with a protective varnish will change its characteristics... A properly glued structure can easily withstand all changes, but the dimensions can still vary (mainly across the wood fibers).

Applications
These types of wooden boards are often used in the manufacture of various furniture structures, including countertops, shelves, shelving, cabinets, chests of drawers, kitchen furniture.

In addition, this material is widely used in construction. It can be used in the formation of wall coverings, partitions, ceiling panels, window sills.

In any case, it should be remembered that it is not recommended to expose such wooden materials to sudden changes in temperature and humidity, because this can lead to a loss of strength of the joints between the layers.

The comment was sent successfully.