How much does the cube of the board weigh?
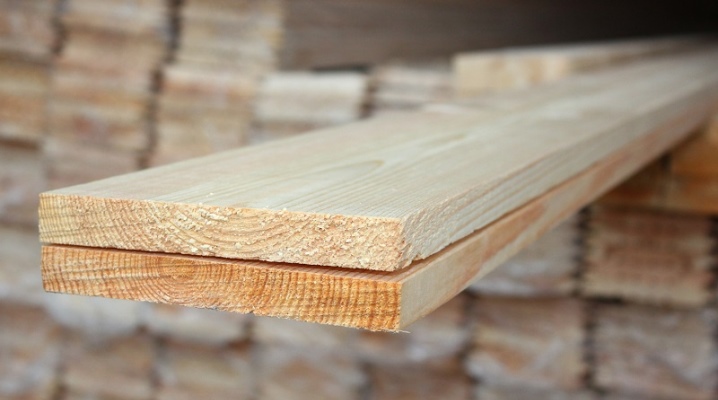
The weight of the board is an indicator that is important to know before starting work in order to select a material that can withstand the required loads without unnecessary weighting of the structure. It is customary to measure the weight of the boards in kilograms, the volume in cubic meters, and the density in kilograms per cubic meter. Common units of measurement allow you to compare different types of wood materials with each other by weight and other properties. You should know how much a cube of boards of different breeds weighs, what affects the weight, and how to calculate it.


What does weight depend on?
The weight of a cube of boards of different types ranges from 345 to 1040 kg. Such a wide range of values is explained by the fact that the weight of the tree from which the lumber is made depends on density (density is the ratio of mass to volume), and it is a variable indicator, which, in turn, depends on the species and moisture content of the tree.
The difference in density is due to the fact that the structure of the tree is heterogeneous. If a tree consisted only of a dense woody substance, the weight of a cubic meter would be the same for all species and species and would be 1540 kg. But the volume of the tree includes less dense areas: capillaries, pores, intercellular and intracellular space. Moreover, their size and proportion of the total volume differ in different types of trees and even in trees of the same species, depending on the growing conditions. That's why the density (and hence the weight) of wood is less than the density of woody substance and differs for different species.
The density and weight of the material also depend on moisture. After all, vessels, cells and intercellular space are not empty - they contain a certain percentage of water in a bound and unbound state. For a living tree, this is 70–80% water, that is, most of its weight. After the tree has been cut down, the natural process of drying begins - dying off, the cells give off water, shrink. This reduces the volume and weight of sawn timber compared to living wood.
But it is impossible to dry the boards to a dense, "stone" state - non-evaporated oils and resins, a certain percentage of bound water, pores and channels filled with air remain.

There are several stages of wood drying, at each of which its weight will be different.
- Wood of natural (initial) moisture - more than 45% moisture. Such an indicator is for a freshly felled tree or tree at the initial stage of drying; it has a maximum moisture content and weight.
- Wet - 24–45% moisture. This is the main stage of drying, the wood intensively loses moisture, its weight gradually decreases.
- Air-dry (equilibrium humidity) - 19–23% humidity. This is the level when equilibrium is reached in humidity with air, the natural drying process is completed.
- Dry - less than 19-20%. The moisture level of the material corresponds to that of a warm indoor environment.
Wood of natural moisture and damp wood is not suitable for work - their volume and density indicators are unstable, the material will shrink when it dries, it can deform and crack. The optimum level for sawn timber is 10–22%, that is, air-dry and dry wood. Moreover, wood of different moisture content is used for various tasks, therefore boards are sometimes called:
- furniture (dry) - manufacturing of furniture and interior finishing work;
- transport (equilibrium moisture content) - manufacturing of formwork, decking and floors, scaffolding, shipping containers, external finishing.


In order to achieve the desired moisture content and weight, various technologies for drying wood are used.
- Atmospheric (natural) drying - drying under a canopy in the air, when the humidity decreases naturally. In this way, the moisture level can be reduced to 12-15%.
- Chamber drying - the use of special chambers, the temperature in which reaches 65–100 °. This method allows you to reduce the humidity level to 4%.
Atmospheric drying allows you to preserve the geometry of wood fibers as much as possible, to avoid deformations and defects (warpage, delamination, cracks) that can occur if water evaporates too quickly and unevenly. But it takes a long time: several months. Therefore, sometimes, in order to speed up the process without loss of quality, two methods are combined: the wood is dried first in air to a certain percentage or equilibrium humidity, then in a heat chamber it is brought to the desired final value.
How much less the final weight of the dried material will be depends on the breed. After drying, different species have a different number of cells, pores and woody matter per unit volume. The characteristic of this indicator is the specific gravity. Specific gravity - the ratio of the mass of the wood substance to the volume. Distinguish:
- specific gravity of solid mass of wood without voids (basic);
- specific gravity of wood at a certain moisture content (volumetric).
For practical tasks, the specific gravity at a certain humidity is primarily important. You need to know it to calculate the weight of the board. For popular types of wood, the specific gravity values are given in the reference tables.
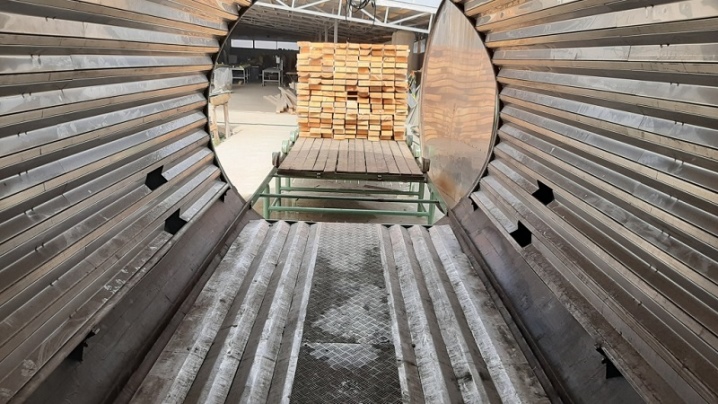
How much does a cube of different boards weigh?
We give reference data for some breeds, which will help determine how much a cube of different boards weighs.
By breed
Depending on the density and weight of a cube of different wood with 12% moisture content (all physical and technical properties according to GOST are determined for this level), all species can be divided into 3 classes.
- Lightweight - up to 540 kg. These are the majority of conifers, including spruce, Scots pine, fir, cedar. From deciduous - walnut, cherry, poplar, linden, alder, aspen.
- Medium density - from 540 to 740 kg. This category includes elm, drooping and downy birch, maple, ash, apple, elm.
- Heavy - over 740 kg. These are oak, wenge, iron birch, hornbeam, acacia, boxwood.
Density and weight greatly affect the properties of materials and, therefore, the range of tasks for which they are best suited.
- Hardwood boards are used where increased strength is required: the creation of load-bearing floors, floors, stairs, massive furniture, cladding of wet rooms. Due to their dense structure, such boards are not only very reliable, but also have a noble, aesthetic appearance.
- Medium density wood boards and light coniferous boards are in demand for finishing work and furniture making. They are not too heavy, but they are quite strong and have more flexibility than the boards of heavy woods. This is a good option in terms of price / quality ratio.
- Light wood boards are easy to work with due to their soft and pliable texture, so they are well suited for decorative finishes and wood carvings.


By humidity
To understand how much weight depends on humidity, consider how much a cube of wood of different species of different degrees of drying on average weighs. Natural moisture wood:
- soft hardwoods (aspen, linden, poplar, alder) - 800 kg;
- conifers (pine, spruce, fir) - 800 kg;
- hardwoods of medium hardness (birch, apple, ash) and larch - 900 kg;
- hard deciduous (oak, acacia) - 1000 kg.
Edged board of air-dry humidity:
- soft hardwoods - 550 kg;
- conifers - 500 kg;
- hardwoods of medium hardness - 650 kg;
- hard hardwoods - 750 kg.


Raw edged board:
- soft hardwoods - 550 kg;
- conifers - 500 kg;
- hardwoods of medium hardness - 650 kg;
- hard hardwoods - 750 kg.
Dry (furniture) edged board:
- soft hardwoods - 500 kg;
- conifers - 450 kg;
- hardwoods of medium hardness - 600 kg;
- hard hardwood - 700 kg.
Average values can be used for preliminary calculations. In this case, you need to take into account some of the nuances.
- The actual weight of a cubic meter of edged board will be 1–3% less than the table. This is due to the fact that although, due to the correct shape, such boards are stacked evenly, it is still impossible to fit them so tightly that they weigh like a whole cube of wood.
- The weight of the unedged board will be 20-30% less than the weight of the edged board. This difference is due to the weight of the unfilled beveled edge.
- The closest to the tabular values of the specific density will be the parameters of the planed board.

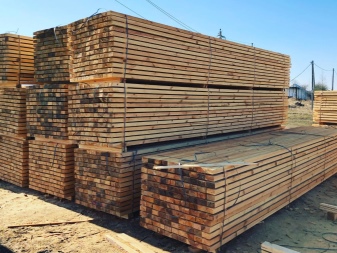
How to calculate?
The algorithm for edged and unedged boards is somewhat different. The exact weight of the cut is determined by the formulas.
- Calculate the weight of one board by the formula: length * width * height * density. The resulting value must be expressed in kilograms.
- The weight of one product is multiplied by the number of boards in a cube. The number of boards in a cube can be found from tables or calculated (divide the weight of 1 m 3 by the actual weight of one board in kg and discard the remainder of the division, the resulting integer is the desired value). For example, let's calculate how much a cubic meter of pine planks 50X150X6000 will weigh at a humidity of 20%.
- We determine the volume of one product: 6 m * 0.15 m * 0.05 m = 0.045 m 3.
- Using the table, we determine the density of a cubic meter of pine at a given moisture content - 520 kg / m3.
- We multiply the calculated volume (0.045 m3) by the density and we get the weight of one board 23.4 kg.
- The calculated value is multiplied by the number of boards per cubic meter. In this case - 22. We get the weight of a cubic meter of such material - 514.8 kg.
For unedged and one-sided edged boards, the section has the shape of a trapezoid, therefore, to calculate the volume of one such board, you need:
- calculate the arithmetic mean for the width of the larger and smaller layers (in accordance with GOST, the width is determined without taking into account the bark and bast in the middle of the length of the lumber);
- calculate the weight of the board by the formula length * width value (arithmetic mean) * height * density.


The specificity of unedged boards is that the parameters of each board may differ in width. Therefore, if the volume of one board is multiplied by their number in the party, the result will not be very accurate. To avoid this, OST 13-24-86 suggests 3 ways to calculate the volume.
- Piece by piece - measure the dimensions of each board using a tape measure, calculate the volume, and then - the total volume of all boards in the package. This method is laborious and time consuming. It is used for small batches of material or special assortments from especially valuable breeds.
- Sampling method - Selectively measure the parameters of some boards from the batch, calculate the arithmetic mean for the volume and use this value to calculate the weight of the entire package or batch. The number of boards for a sample must be at least 3–7% of the lot size and depends on whether they are all uniform in size (for example, for uniform in size - at least 3% of the lot handed over, but not less than 60 boards).
- Batch - determine the volume of the package in which the boards are placed, aligned on one side. Then, a reduction factor from the table given in the OST is applied to the resulting volume value.
After the volume has been calculated in one of the ways, it remains to multiply it by the density indicator of the board from a particular tree at a given moisture content. This allows you to quickly and fairly accurately determine the weight of any batch of boards. For example, find out how much 2, 3, 4, or even 10 cubes of boards weigh.


The comment was sent successfully.