Insulation dimensions: how to choose the right one?
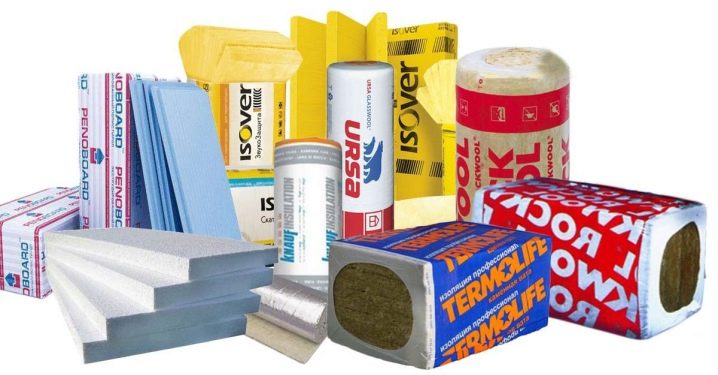
Thermal insulation of walls significantly saves the budget for heating the house. This article describes the size requirements for insulation and the best materials to use to create effective heat insulation in your home.
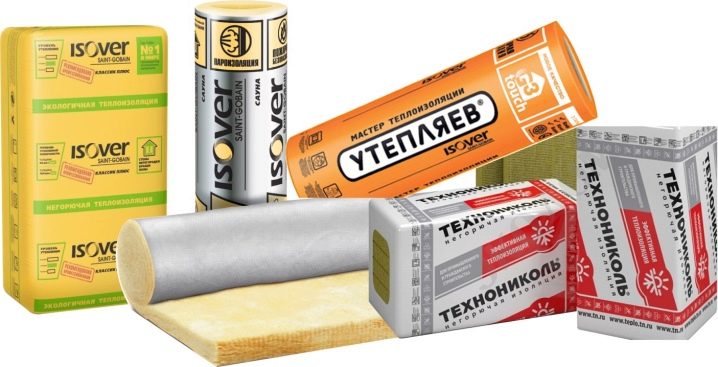
Peculiarities
The main property of any heat-insulating material is its thermal conductivity. In order to achieve the optimal temperature in the house, it is necessary either to reflect heat from the surface, or to prevent transmission along the wall of the building. According to this criterion, all heaters are divided into two categories:
- preventing type - in these products the thermal conductivity is very low;
- reflective type - here the level of infrared radiation is reduced several times.
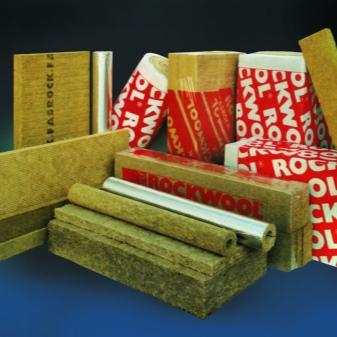
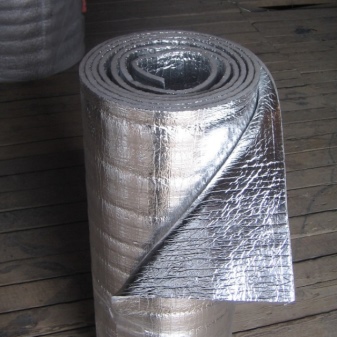
Varieties and forms
Styrofoam
In its shape, it is filled with air bubbles of polystyrene, later pressed into plates of standard sizes: 500x1000, 1000x1000 and 2000x1000 mm. Packing of material - in the form of plates of fixed sizes. Polyfoam is a white board material with a rigid foam structure, contains 2% polystyrene and 98% air. The thickness of this material varies from 20 to 1000 mm.
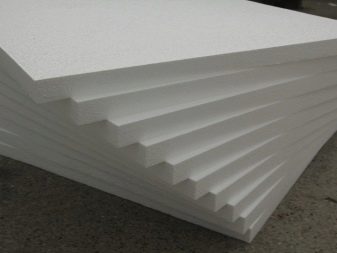
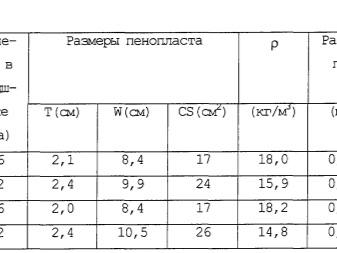
The material has the following advantages:
- low cost of foam and glue with which it is attached;
- the installation of polystyrene is very simple, in this regard, the work can be performed independently, without the involvement of specialists;
- foam is affordable - it can be easily purchased at any hardware store;
- the material is not subject to destruction by moisture.
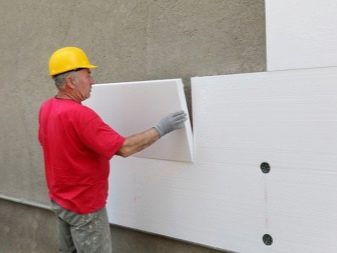
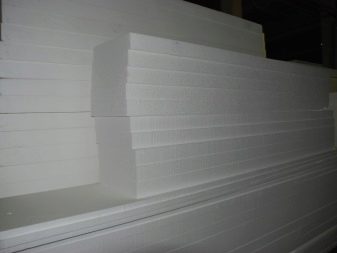
Long-term use of polystyrene as a heater revealed its disadvantages:
- on sale there is material of rather low quality;
- the material is subject to combustion;
- as a heater, polystyrene serves only 10-15 years (depending on its manufacturer and quality);
- the material does not "breathe".
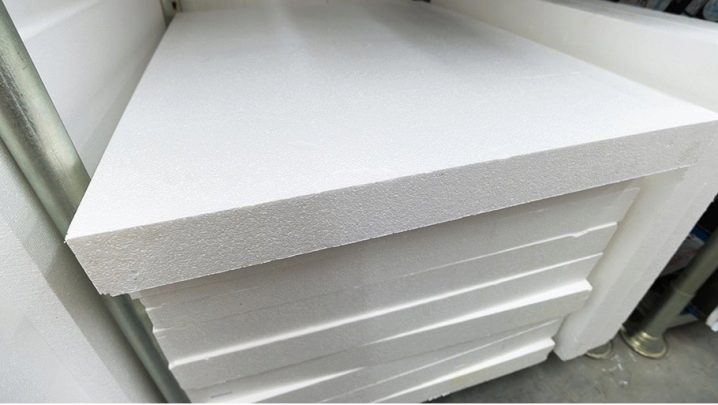
In order to start working with insulation, it is necessary to perform a number of actions that distinguish this type of material from products for other purposes. First of all, it is necessary to carefully prepare the surface to be insulated. To do this, it must be cleaned, leveled and primed. After that, you need to make marks with a plumb line for an even arrangement of the foam plates. Then the foam is carefully lubricated with an adhesive solution and gently applied to the wall.
It is not necessary to put too much pressure on the styrofoam when laying it - it is quite fragile, so damage may appear. The foam boards are stacked close to each other. Gaps can be filled with polyurethane foam. For secure fixing, the plates are best fixed with dowels. A reinforcing mesh is glued on top of such insulation - the final finishing is carried out on it.
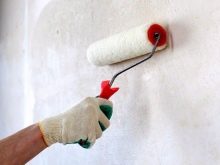
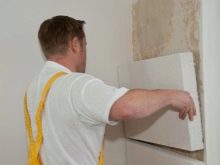
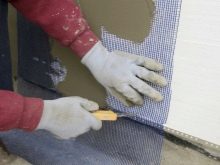
Penoplex
Such material is better than polystyrene in all its properties, and its installation is simple and convenient for self-installation.
This insulation looks like a waterproof tile with a thickness of 20 mm or more. The basis of the material is styrene foam, its granules are processed under pressure using high temperatures. The walls inside the house for the installation of styrofoam are prepared in the same way as for the installation of polystyrene (you need to remove dirt and clean, level and prime the surface).
A starting profile is installed to align the entire plane with the plinth. The profile also secures the first tiled row.
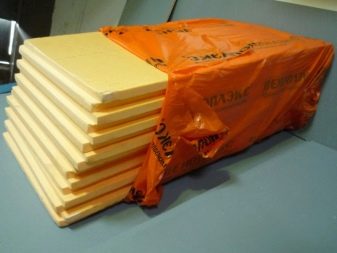
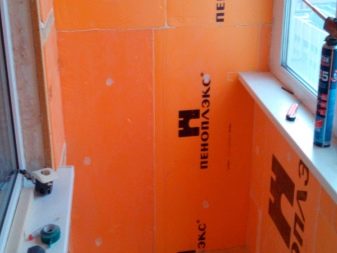
Finishing work:
- primer for works on the facade;
- basic finishing (a variety of plasters can be used, both acrylic and silicone);
- selection of the final texture;
- painting.
The easiest way: the surface is leveled, a finishing putty is applied, primed, painted. In construction, material is used with a thickness of 20-100 mm, a width of 600 mm and a length of 1200-2400 mm.
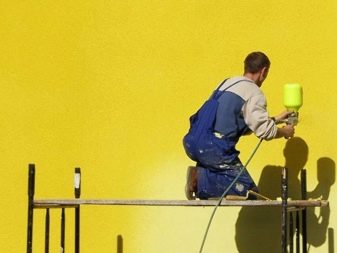
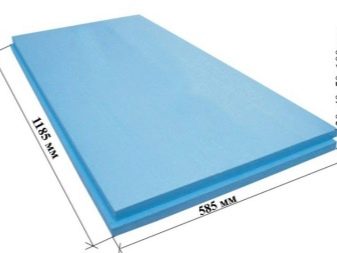
Mineral wool
All types of mineral wool are also suitable for thermal insulation.
Mineral wool properties:
- not flammable;
- heat conductivity is very low;
- rodents do not eat mineral wool, but they love to settle in it;
- service life from 30 to 80 years.
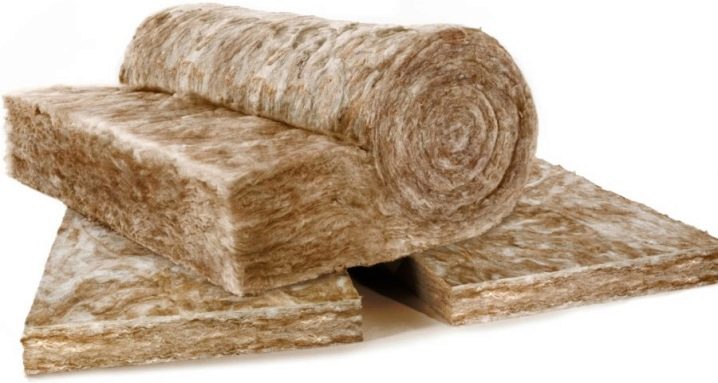
Disadvantages - this cotton wool absorbs moisture and is much more expensive than foam. When working on thermal insulation with mineral wool, it is imperative to use special clothing and a mask.
Heat insulators of this class are of three types:
- slag;
- fiberglass;
- stone wool.
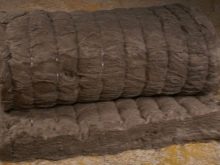

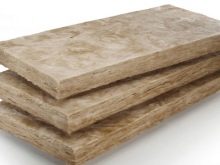
The material is produced in several varieties:
- in the form of plates (mats);
- rolls;
- in a formless form.
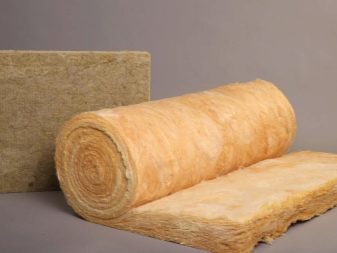
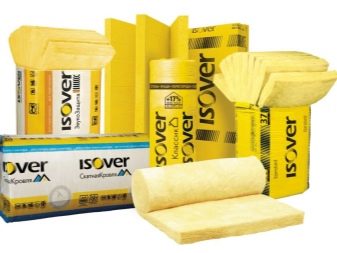
Mineral slabs are made from ordinary glass: first it is heated, and then pulled into a thin fiber. The most common dimensions of such a product are 1000x500 mm. However, each manufacturer has its own size. For example, Isover products have the following parameters: 1170x610 mm with a thickness of 40-150 mm.
It is worth noting that perfect different sizes of such material are used for different designs. For example, for thermal insulation of frame structures, mineral wool is used with the following optimal parameters: length - 1175 mm, thickness - 46-213 mm, width - 566-612 mm.
Also, for the insulation of multilayer walls, builders use this material with the following parameters: length - 1176 mm, thickness - 52-206 mm and width - from 614 mm.
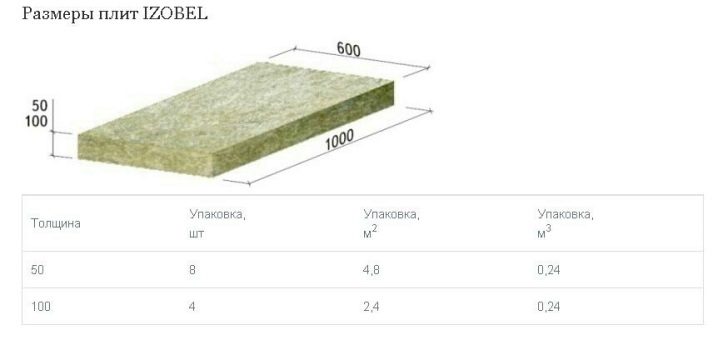
Izolon
This insulation belongs to the newest generation of heat insulators. The material is an elastic polyethylene foam with a cellular structure of various thicknesses and densities. It has a very thin structure - the thickness of this material is only 2 to 10 mm. In terms of thermal conductivity, one centimeter of an isolon is comparable to a brick wall or eight centimeters of mineral wool insulation.
The insulation consists of polyethylene foam, which is responsible for thermal conductivity, and aluminum foil, which retains heat.
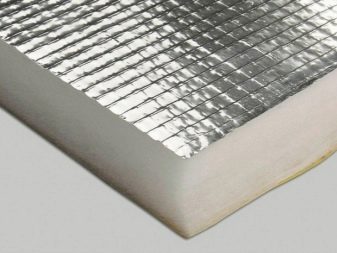
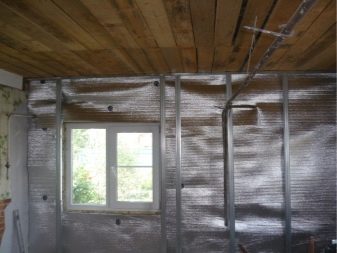
Izolon does not absorb moisture at all and is not subject to decay. The material lasts up to 30 years. This insulation is non-toxic, it is completely odorless. Environmental friendliness and compliance with sanitary standards allow it to be used even in places where food is produced.
The material is produced in the form of rolls of various sizes: material thickness - 3.5-20 mm, length 10-30 m. One roll can contain from 6 to 36 sq. M. m of material.
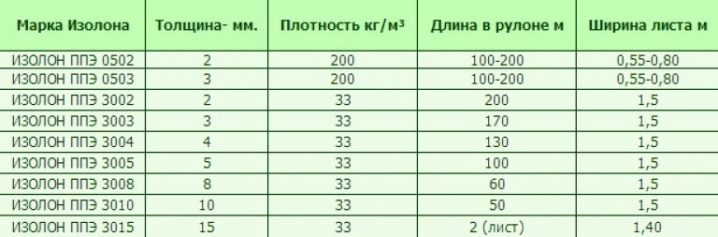
Expanded clay
This insulation is made from various types of clay. It is usually used as a concrete filler. But nowadays it is also used to insulate walls.
The material is produced in the form of gravel and crushed stone. The first version has an oval shape, the second - a cubic one with sharp edges. Packing takes place in fractions - the higher it is, the better the thermal insulation properties.
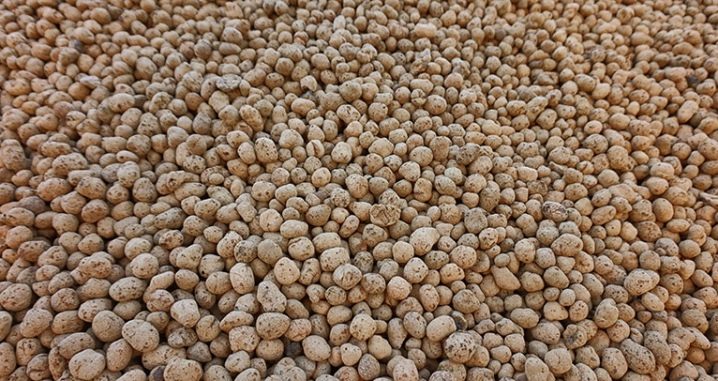
Expanded clay gravel has a size of fractions from 5 to 40 mm.
Expanded clay fraction 5-10 mm is used to create expanded clay concrete blocks, 10-20 mm - for warming floors and ceilings, fraction 20-40 mm - for warming basements, roofs, heating mains, floors in garages. Crushed clay from expanded clay has the same size as gravel.
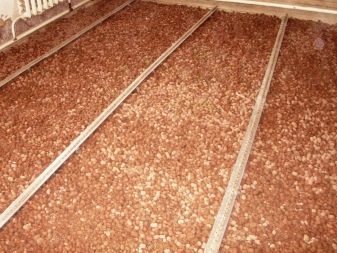
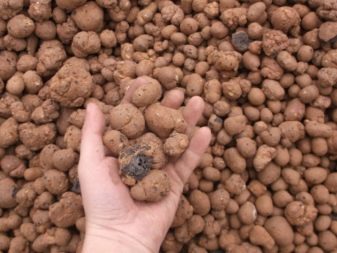
Penoizol
Penoizol is a liquid foam. With the help of special equipment, it is created directly on the construction site. Formwork is made of brick, and penoizol is poured into it.
Such material is produced using foamed urea resin. Once applied and cured, it resembles hardened shaving foam. Having a service life of 50 years, in comparison with all the above types of heat insulators, penoizol significantly benefits from heat preservation, its incombustibility, moisture resistance and non-susceptibility to rodents and fungal organisms.
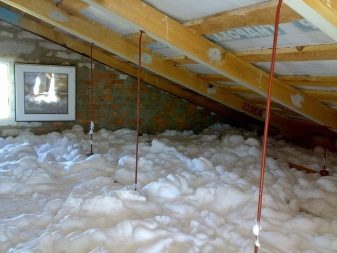
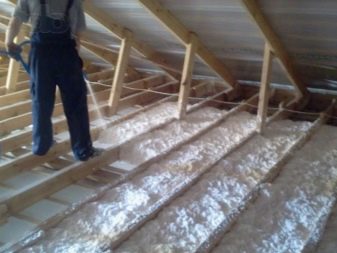
Arbolit
The material has the following technical characteristics:
- density - up to 710 kg per cubic meter;
- thermal conductivity - up to 0.13 watts;
- ultimate bending strength - up to 1 kgf / cm2;
- compressive strength - up to 3.5 MPa.
The appearance of the material resembles a chipboard, and the color is a concrete coating. The release of the material is made in the form of volumetric square blocks, which include a filler in a sheath of a binder. The composition of the filler is shavings, straw and sawdust (up to 90%), cement, calcium chloride, soluble glass and alumina sulfate are also added here.
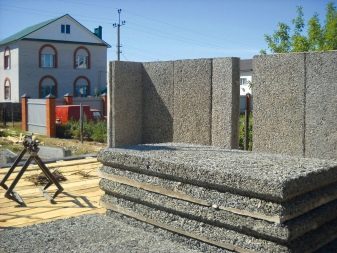
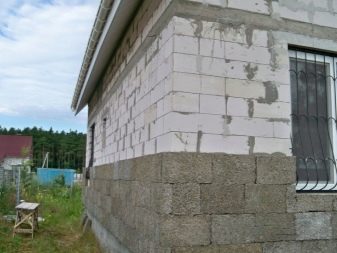
These blocks come in the following sizes:
- 500x200x250 mm;
- 500x300x250 mm;
- 500x400x250 mm.
Of the features of the material, it is worth noting high thermal insulation, environmental friendliness, biostability, high installation speed and low cost. However, the material is not resistant to moisture, and the block sizes are not precise, which will require leveling the surface.
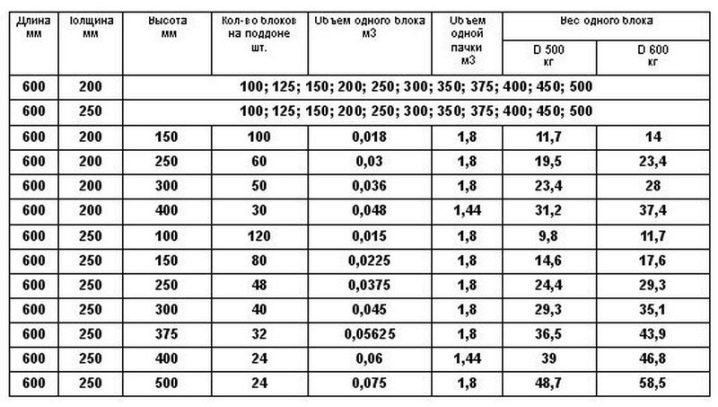
Chipboard heat insulator
The material is a pressed board made of sawdust and shavings (90%), bonded with formaldehyde resins. It is produced in sheets with a thickness of 10-22 mm. The dimensions of such material are as follows: 2800x2620 and 1830x2070 mm.
The product has the following specifications:
- material density - 500-1000 kg / cu. m;
- humidity - up to 13%;
- tensile strength - 0.6 MPa;
- ultimate bending strength - 26 MPa;
- water absorption - 31%.
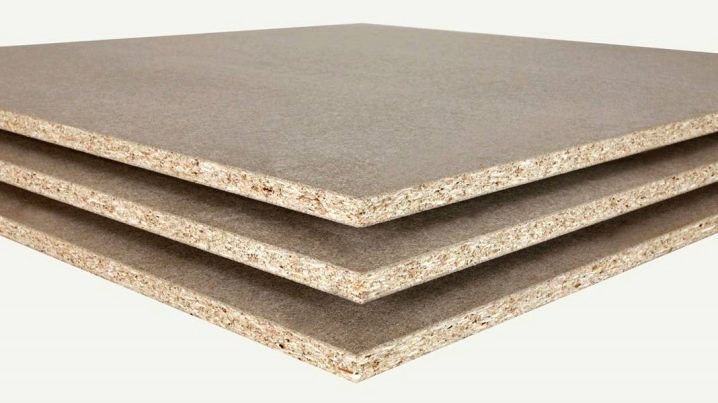
Polyurethane foam
Available in gas-filled plastic. The material is divided into hard material and soft material. This product contains polyester, water, emulsifiers and diisocyanate. The material has good sound absorption and high moisture resistance.
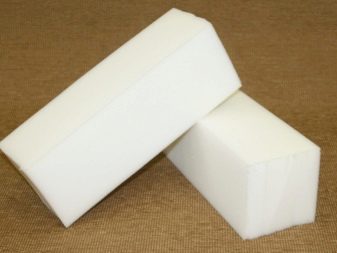
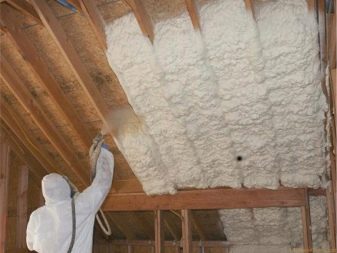
Foamed polyethylene
It is an elastic fabric with a cellular structure. It can be produced both in rolls and bundles, and in sheets. Differs in high vapor barrier properties, as well as excellent sound insulation. This material is obtained by adding a foaming agent to polyethylene.
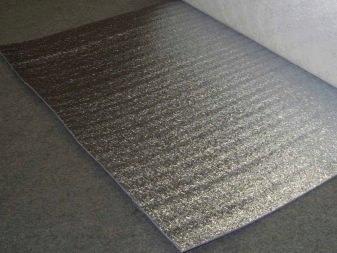
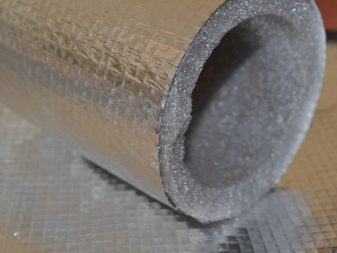
Also used, but used much less often, the following types of insulation:
- Fibrolite. It is produced in pressed plates (length - 2400 or 3000 mm, width - 1200 or 600 mm, material thickness - 30, 50, 75, 100 and 150 mm). The material does not react to chemical and biological influences, it is resistant to fire.
- Ecowool. It is produced from cardboard production waste and waste paper. The structure resembles cotton wool with large fibers. Differs in good sound insulation, does not form seams when sprayed. However, it absorbs moisture well. The material is produced both in rolls and in slabs.
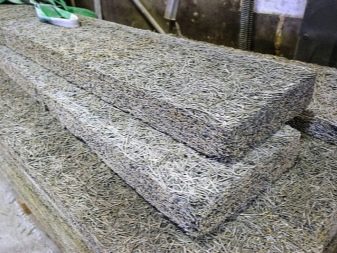

- Glass wool... It has longer fibers than mineral wool, so the material is resilient and durable. Also, the product can withstand high temperatures (up to 453 C) and does not corrode. The material is produced both in rolls and in plates. The dimensions of the product produced in slabs are as follows: length - 1000 or 1200 mm, width - 500 or 600 mm, thickness - 20, 40, 60, 80, 100, 120 and 150 mm. Rolls also come in a variety of sizes. The material does not burn, has good sound-absorbing properties and, when heated, does not emit substances harmful to human health.
- Ceramic wool. The basis of such a material is aluminum or silicon oxide. This material has good thermal conductivity properties and is resistant to high temperatures. The product is produced by the blowing method or in a centrifuge.
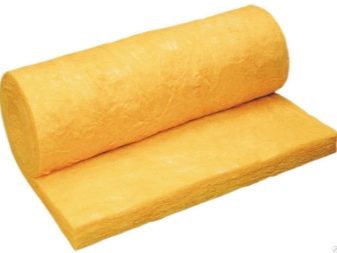
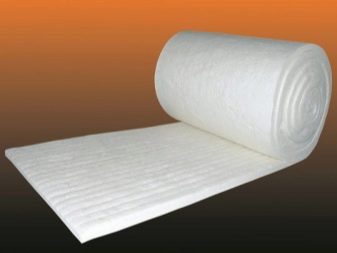
Tips & Tricks
When choosing a heater, you need to be guided by simple principles: the roll area in square meters is usually indicated on the packaging of the thermal insulator. Based on these figures, you can find out in advance how many rolls are required for insulation. But it must be remembered that, for example, mineral wool is always subject to shrinkage.
For better density, it is better to lay this thermal insulation material too much. Therefore, it is always necessary to add a few percent to your calculations. This applies to all heaters.
To calculate the required amount of material, you must perform the following calculations:
- the area of the house is calculated;
- the volume of the house is calculated (the height is taken from the floors);
- the whole amount is multiplied by 2 (floor and ceiling for one floor);
- to the obtained value, add 15%.
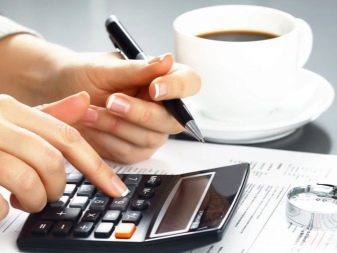
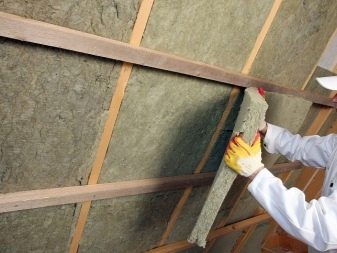
For an overview of heaters, see the next video.
The comment was sent successfully.