Technical characteristics and description of foam glass
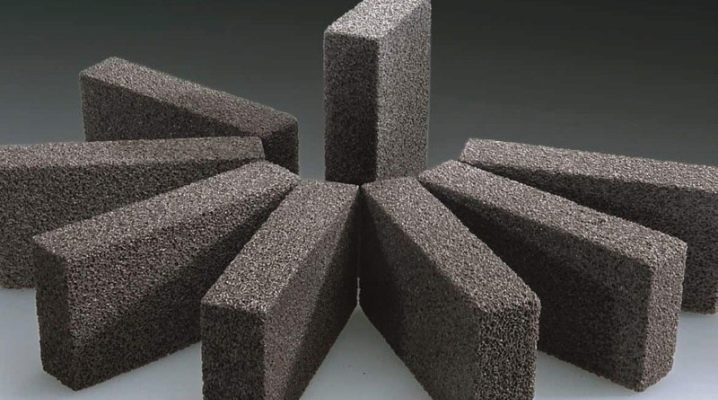
Professionals consider foam glass to be a material behind which lies a serious resource for reducing the cost of housing being built and increasing energy efficiency. This material began to be used relatively recently in mass construction, but you cannot call it "young" - foam glass was invented back in the 30s of the last century, and began to be used in practice in Canada several years later.
However, only half a century later, it took its place among popular materials - it was then that the technology was thoroughly worked out, and the costs of its production were reduced.
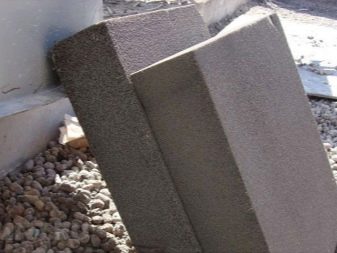
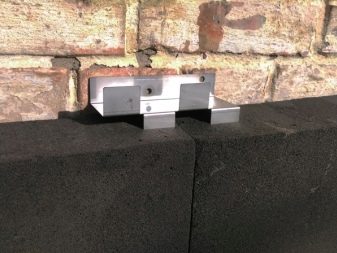
Peculiarities
When two different substances are combined in one material, it can have a very interesting effect. This is exactly what happened with foam glass - here they combined into one whole classic silicate glass, which in past years stood in most windows, and foam, consisting of small bubbles interconnected by thin layers of liquid.
The material is obtained by heating a silicate substance into which a gas-forming substance is introduced. Under the influence of elevated temperatures, it begins to melt, the gas generator decomposes in parallel, releasing small bubbles, they are "caught" by the hot melt and firmly fixed in it.
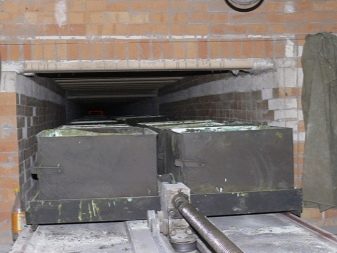
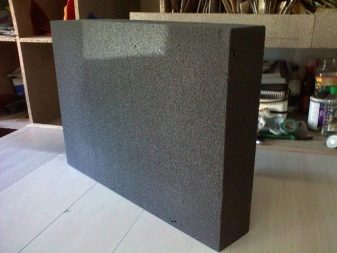
Foam glass has unique consumer properties:
- light weight:
- strength;
- waterproofness;
- flammability and heat resistance;
- inertness in relation to chemical reactions.
Part of its characteristics comes from silicate raw materials, and part from gas. For example, the material loses transparency of glass, but acquires high noise-absorbing and heat-insulating properties.
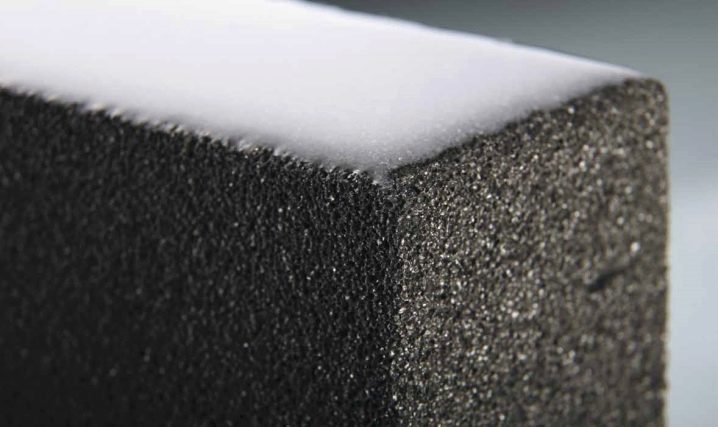
Separately, we should dwell on the physical and technical indicators of the composition.
Foam glass has a fairly low density, which is 100-250 kg / m3. For comparison, the density of wood varies from 550 to 700 kg / m3. By the way, this is why foam glass has been repeatedly tried to be used as a floating building material.
The volumetric weight is approximately 70-170 kg / m3, and the sound insulation of a 10 cm block is 52 dB.
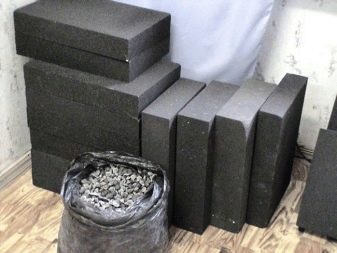
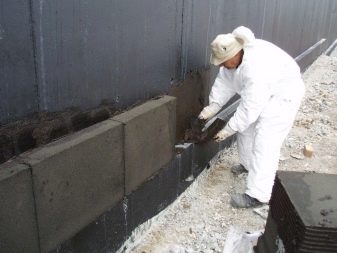
The material is resistant to combustion: fire resistance class A1 (non-combustible compounds). It does not decompose under the influence of unfavorable atmospheric factors, and also does not emit harmful and toxic substances.
The compressive strength of foam glass is quite high - the material can easily withstand pressure up to 100 tons per 1 m2, other characteristics also inspire optimism for craftsmen who intend to use foam glass for construction work.
Thermal conductivity at standard temperature is 0.04 W / mC, which is higher than that of wood (its indicator is only 0.09 W / mC), but the ability to absorb sound waves is comparable only to mineral wool and is 45-56 dB.
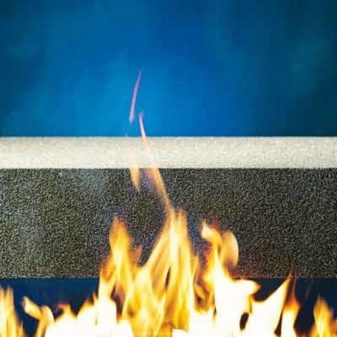
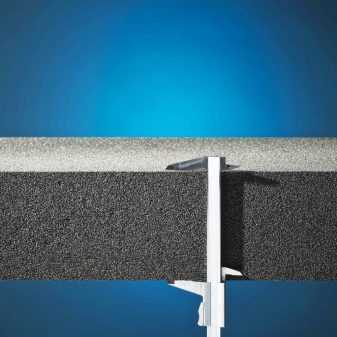
The water absorption coefficient does not exceed 2%. This means that the foam glass practically does not absorb moisture, and the vapor permeability is almost zero - 0.005 mg / (m.h. Pa). This material can be called an ideal vapor barrier.
The blocks can withstand elevated temperatures, retaining their properties even at 300 C, and if the composition contains special additives, then the thermal resistance threshold can reach even 1 thousand C. At the same time, the material is not afraid of low temperatures and easily tolerates contact with liquid nitrogen (-200 C) without any signs of destruction.
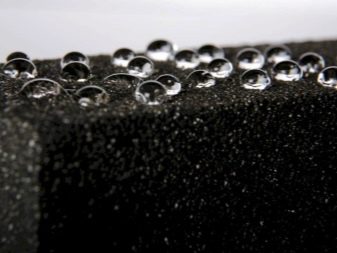
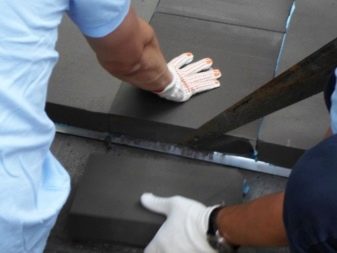
Chemical inertness is a very valuable quality along with high environmental friendliness. Perhaps there are not many modern heaters that would be equally harmless.
Another plus is durability.... In comparison, polymers age rapidly, losing their performance characteristics, and begin to release toxic substances into the environment. Foam glass is devoid of such disadvantages - its use is more justified than the use of PVC plastics or expanded polystyrene. The service life of foamed glass blocks reaches 100 years.
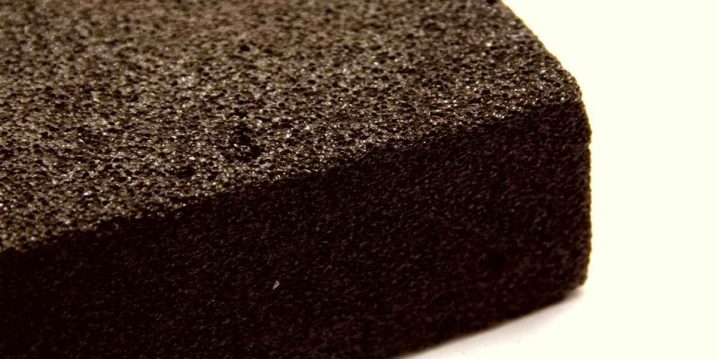
Advantages and disadvantages
Exceptional physical properties "rewarded" the material with a large number of advantages:
- ease of processing - the material is easily attached; installation work can be done by hand, even without much experience in construction and decoration;
- corrosion resistance - foam glass does not form rust;
- biostability - the material is resistant to waste products of flora and fauna, as well as to microorganisms of all types;
- chemical inertness - foam glass does not react with acid-base solutions;
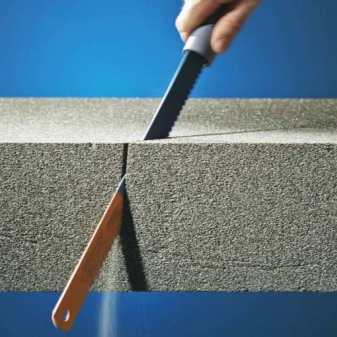
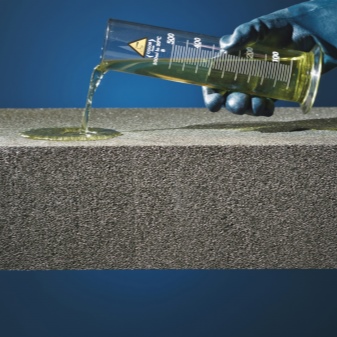
- constancy of block sizes - throughout the entire period of use, the blocks do not shrink, do not stretch or shrink, their dimensions are unchanged in any conditions;
- resistance to mold and mildew - foamed glass is not an environment in which mold and other dangerous microorganisms multiply, so you can always be sure that fungi will not penetrate the room and will not harm the health of households;
- high degree of fire resistance - the material does not ignite spontaneously and does not support combustion, protecting the walls from damage in the event of a fire;
- hygroscopicity - the product does not absorb moisture;
- vapor permeability;
- environmental friendliness;
- sound absorption.
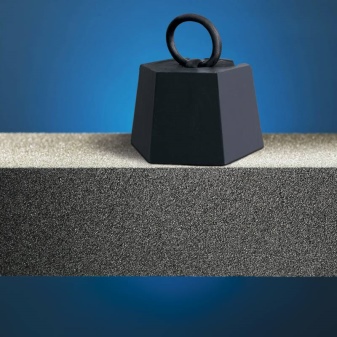
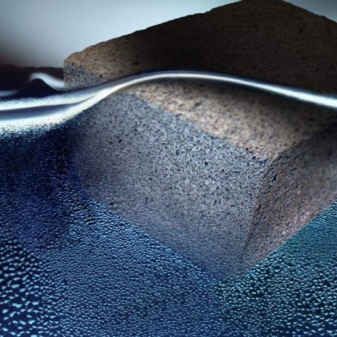
The material is recommended for use in rooms with increased sanitary and hygienic requirements.
Throughout the entire long term of use, the blocks do not change their shape, they are not destructively influenced by seasonal temperature drops and precipitation, the material reliably protects the structure from the occurrence of any cold bridges due to compression or sagging of the insulating coating.

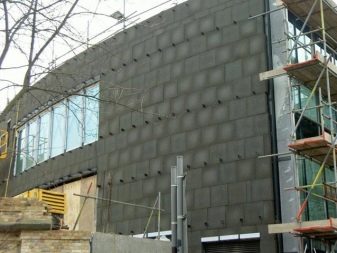
If we talk about the shortcomings, then the most important of them is the high cost. This is due to the fact that glass production technology is associated with high energy costs. In addition, the firing itself is a rather laborious and technological process. All this significantly affects the final price of the product.
The second disadvantage is low resistance to mechanical damage. However, this indicator cannot be considered critical, since heaters are rarely hit.
Foam glass is characterized by low elasticity, therefore, during installation work, it requires reliable fixation. In addition, it is very important to observe the exact laying technology, otherwise the blocks will begin to crack.
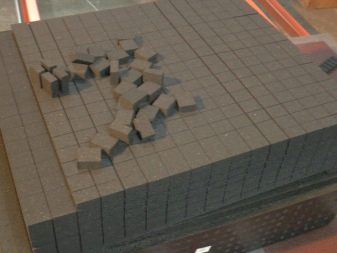
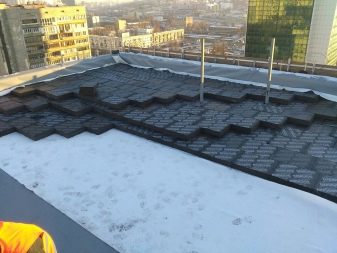
Views
Foam glass on the construction market is presented in two versions - granules of foam glass chips and blocks. They have a different production technology.
As you know, foam glass is obtained from ordinary glass waste, which is crushed to a powdery state and then heated with the addition of gas-forming components to 850 C.
The granular material is produced in metal tunnel ovens and, after processing, is sawn into blocks of the desired size. It looks a bit like expanded clay.
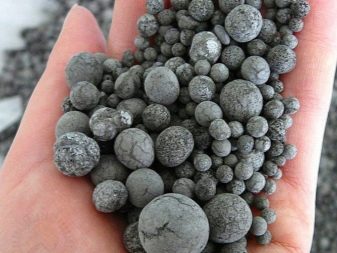
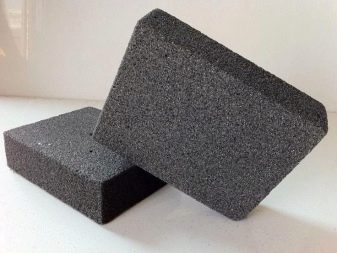
The technical properties of foam glass made in the form of granules can be considered unique - it is a lightweight material that is absolutely not subject to corrosion, mold with fungi does not take root in it, and destruction does not form. It has a very long life span.
Frame houses are most often insulated with granulated foam glass - it is added to the glue and kneaded. The result is a composition with high thermal insulation properties.
Blocks are most often used for ceiling insulation. These are tough, but at the same time rather light materials, which in their properties resemble expanded polystyrene plates or mineral wool products.
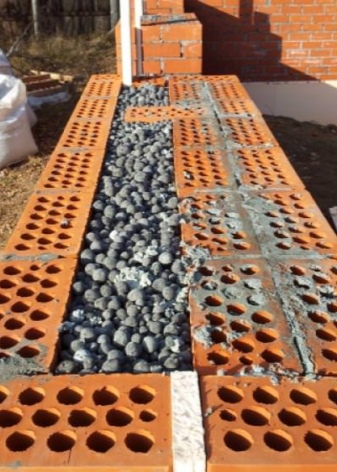
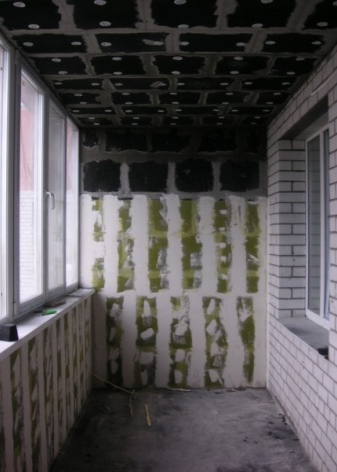
Scope of application
The scope of application of foam glass is due to its physical and technical properties. The material is widely used in almost all spheres of life.
- In housing construction... The material is used as a heater for utilities, roofs and floors. They cover basements and foundations, basement and attic floors, and are also often used to insulate facades from the outside and from the inside.
- In the construction of sports facilities - granulated foam glass is suitable for arranging sports arenas, as well as swimming pools and sports grounds.
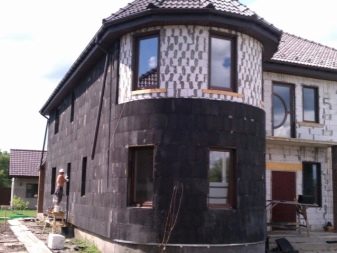
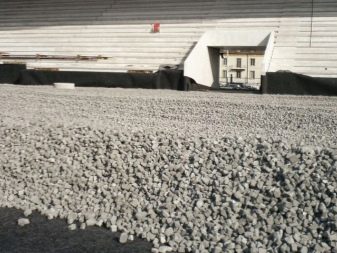
- In industrial facilities... Built-in glass can significantly reduce the cost of using objects due to their increased thermal resistance. Its use is justified not only in surface structures, but also in underground facilities, for example, in buried reservoirs.
- In the national economy... On swampy soils, foam glass crushed stone is often used - that is why the material is optimal for the construction of farms that are designed for breeding cattle and birds.
- In improvement works. Bulk foam glass is often used in the construction of greenhouses and greenhouses, as well as in the formation of garden paths. The material has found its application in the construction of a drainage system.
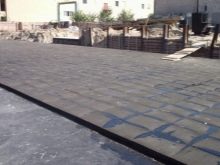
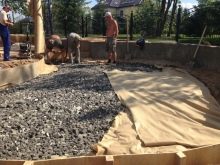
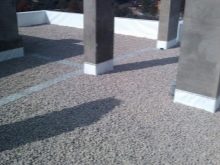
Manufacturers and reviews
Several enterprises are engaged in the production of foam glass in Russia. Some of them are presented below.
- "Saitax" (Moscow region) - production of block and granular foam glass is established here.
- "Neoporm" (Vladimir) - the material is produced in the form of tile material and shaped products (shells, knees).
- "Penostek" (Moscow region) - mastered the manufacture of granular insulation.
- "Izostek" (Krasnoyarsk) - produces foam glass in the form of slabs.
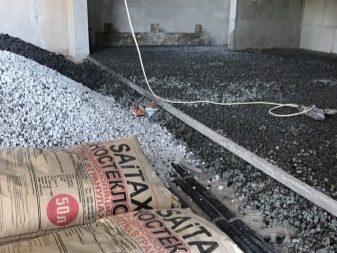
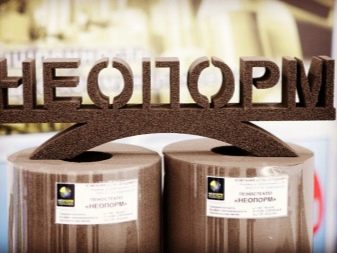
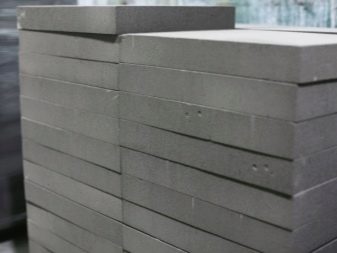
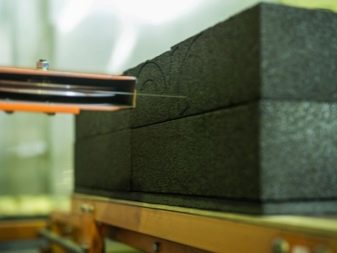
- United Industrial Initiative (Kaluga Region) - is engaged in the production of crushed foam glass.
- "Thesis" (Sverdlovsk region) - sells foam glass chips. Unclean material - contains astringent additives, due to which vapor permeability increases.
- "Termoizol" (Yaroslavl region) - granulated glass.
- Penosital (Perm) - slab and block coverings are produced.
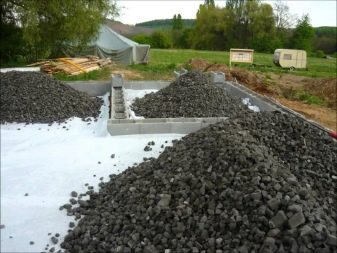
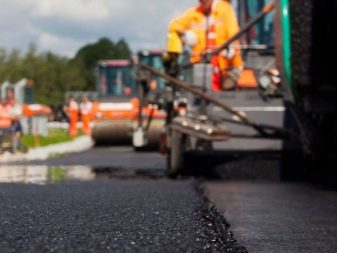
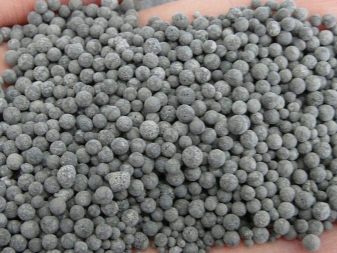
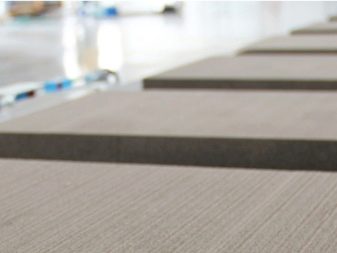
The producers of Integra, Etiz and Neftezol are also known to the Russian consumer.
It may seem that in Russia there are a large number of enterprises that have established a serious production of foam glass that meets all quality requirements. This is not entirely true. There are production facilities in our country, but the production volumes are negligible, and the quality is seriously inferior to imported counterparts.
The situation with glass production in other countries, for example, in the CIS, is a little better. The products of the Ukrainian enterprise from Zaporozhye and Shostka gained fame all over the world. The consumer parameters of their products are very close to the world requirements, but the production volumes are small, so the products, as a rule, are fully sold in Ukraine.
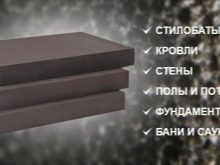
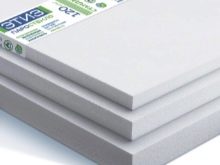
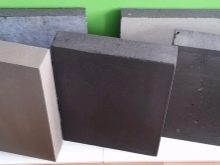
Slightly lower performance characteristics of the Belarusian "Gomelglass". However, the volume of its production is sufficient to provide our country and neighboring Russia with foamed glass - this brand is considered the absolute leader in sales in our country. By the way, this company is one of the first to start producing foamed glass back in the middle of the last century.
The products of the Chinese company "NeoTim" are very popular, as well as Pittsburgh Corning, whose facilities are located in the USA, Czech Republic, Germany and Belgium.
According to consumer reviews, it is the products of this concern, produced under the Foamglas trademark, that best meet all the declared parameters of foamed glass.
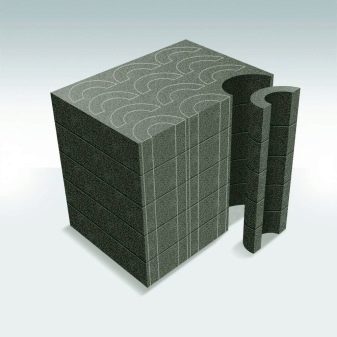
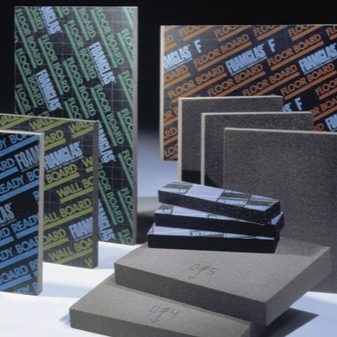
Tips & Tricks
Below are some tips on how to improve the performance of your foam glass.
When buying this material, the thermal insulation parameters of the product should be taken into account. For example, for walls built of brick or concrete, slabs with a thickness of 12 cm are used, and for structures made of wood, material of 8-10 cm is sufficient.
For internal work, it is worth stopping at 6 cm slabs. They are attached with glue and reinforced with steel brackets and thin dowels.
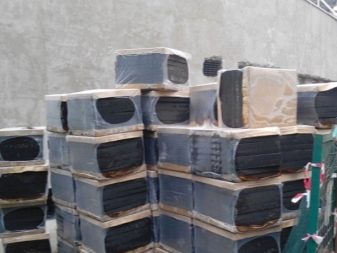
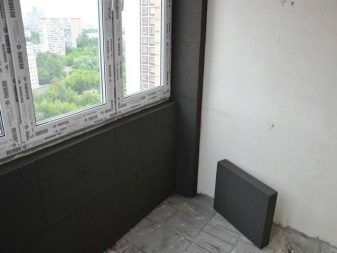
If foam glass is used to create a warm floor system, then it is worth giving preference to granular material, which effectively fills all voids and creates the necessary degree of thermal insulation.
Today, foam glass meets all the requirements that apply to building materials in terms of their reliability and safety.
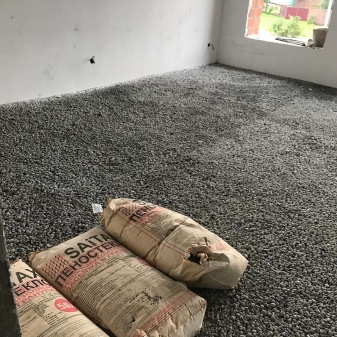
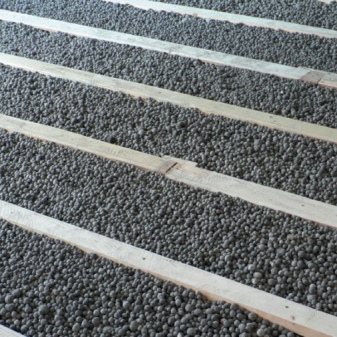
For information on how to insulate the floor with foam glass, see the next video.
The comment was sent successfully.