Use of Rockwool mineral wool

Any residential or industrial building needs high-quality thermal insulation. The world market of heaters has long been taken over by the Rockwool company. So the best manufacturer does not raise questions. But in the presence of a huge variety of products on offer, it is important to understand the material and decide which one to opt for during construction. In this article, we will tell you in as much detail as possible about mineral wool and all the areas in which it is used.
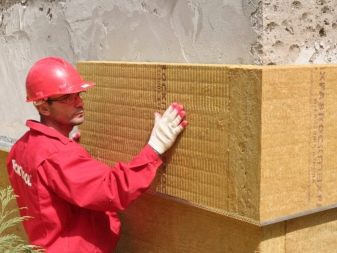

What it is?
First, you need to figure out what mineral wool is as a heater. The material is also called basalt or stone wool. This is one and the same insulation, which consists of a heat-insulating substance.
There are different technologies for its production. Rockwool mineral wool is made with the addition of special components that perfectly protect the material from moisture. You can also highlight such distinctive features as lightness and high elasticity.


The technology itself is always more or less the same and the basic element is basalt stone. It is melted at very high temperatures, after which special resins are added. This is how the fibers that make up the stone wool are formed.
Rockwool has long been the world's leading manufacturer of non-combustible rock wool insulation. Over the years of its existence on the market, the company has developed unique production technologies, some of which are kept secret.
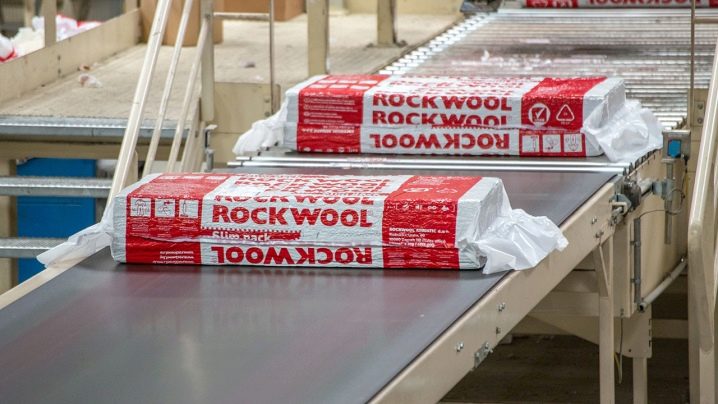
Rockwool divisions are dedicated to the manufacture of suspended ceilings, artificial soil, decorative facades, road noise insulation panels, and even consult clients on energy efficiency in buildings. Now they own 27 factories in Asia, America and Europe.
In Russia, the company became known around the 70s. And the first Russian plant Rockwool was put into operation in 1999. Since then, the manufacturer has become a leader in the thermal insulation market, improving the technology of the insulation process from year to year. New products help to facilitate installation, ensure safety and save money for both the consumer and the customer.


Peculiarities
Mineral wool is safe for residential buildings, and its fire resistance will protect in the event of a sudden fire. Also, stone wool is able to "breathe", thereby preventing mold and dampness.
Rockwool stone wool is used in four main areas: sound insulation, thermal insulation, sound insulation and fire protection. Suitable for residential and industrial environments.
The material can be of different density and thickness in the form of plates, mats, cylinders and lamellas. This variety allows the use of stone wool in shipbuilding, industry and in the construction of complex buildings. The technical characteristics provide an almost unlimited service life.


Installation is quite simple: you just need to avoid gaps between the plates when laying and ensure the dryness of the material.
Basalt foil wool is well suited for the construction of premises with high humidity (baths, saunas, underground buildings). An additional aluminum layer provides the necessary vapor barrier.
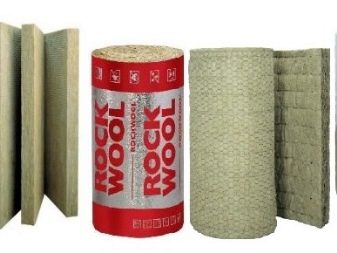

For finishing the walls of buildings, a special line "Facade Butts" was invented, in which they produce insulation in the form of slabs. They are attached with construction adhesive and dowels and can be the last layer before the final decorative finish.
The dimensions of such plates may vary depending on the application. Thickness varies from 2.5 cm to 18 cm. The latter are often used for acoustic insulation purposes.


Specifications
Understanding the technical characteristics, it is worth remembering that there are a lot of heaters and each model has distinctive features. Therefore, we will try to clarify by giving examples of averages.
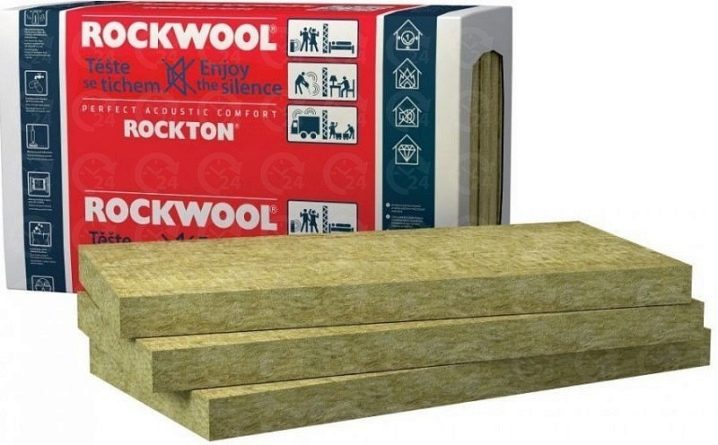
Density
The average density is 50–80 kg / m3. But it is necessary to determine the density of the material based on its specific purpose. For example, rock wool for a pitched roof will be almost weightless with the lowest possible density.
For equipment of a flat roof, on the contrary, cotton wool with a high density is needed.


Thermal conductivity
This is one of the most important indicators for any insulation. The average figure for mineral wool is about 0.038–0.043 W / m. This indicator speaks of good thermal insulation, which not all materials for insulation have.


Refractoriness
Absolutely all types of stone wool do not burn in a fire. She is also unable to collect water. The percentage of water absorption is from 0.5 to 2% of the total mass.
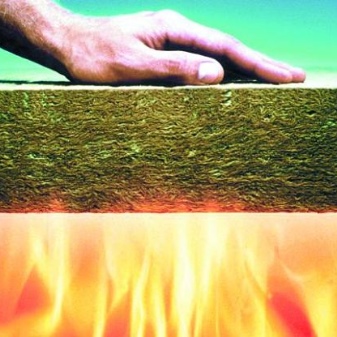
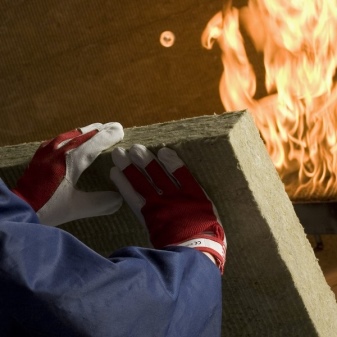
Vapor permeability
This important indicator makes it possible to use insulation when arranging breathing walls, roofs or any other structures with natural microclimate regulation.
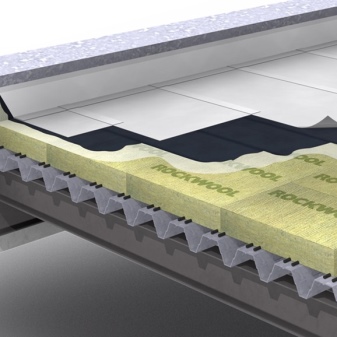

Compression ratio
This characteristic is directly related to density: the lower the density, the higher this coefficient. Mineral wool sandwich panels used for pitched roofs have a density of approximately 30–40 kg / m3. This means that they have a high deformation rate and can reach up to 50%. Such a slab can be compressed and reduced in size by almost half, while not violating the integrity of the structure. Working with such a material, you do not need to spend a lot of time adjusting the slabs to the size of the frame.
Sometimes the compression ratio is only a couple of percent, that is, the material practically does not compress. Such slabs have a high density index and are designed to withstand strong physical influences.

Working temperature
In this category, there are no large scatter in the indicators. Any stone wool can withstand -50 to +100 degrees Celsius. The material cannot catch fire, so the maximum indicator can vary upwards with short-term loads.

The main characteristics of Rockwool mineral wool:
- Low thermal conductivity... Due to the structure, consisting of very small fibers, the material does not conduct heat well.
- Soundproofing... Thanks to this same structure, vata is able to absorb sounds and reduce the strength of vibrations.
- Refractoriness. Even the highest temperature cannot cause the material to melt or give off smoke. Completely non-flammable material.
- Durability. With proper installation, stone wool insulation will last for decades.
- Environmental friendliness. Cotton wool is made of natural material, does not harm human health and does not have a negative impact on the environment.


Varieties
Speaking about the varieties of mineral wool, you can immediately distinguish its main forms:
- Rolls. Not the most common form and is used when insulating floors or attics.
- Cylinders... They are used for protection against condensation in pipes with low temperatures, central heating, pipes with hot water. They are made by cutting out elements from a stone wool sheet and then covered with glass wool or foil layer. Excellent for thermal insulation of pipelines.
- Plates. Used for interior and exterior wall cladding. The most popular form.Against the background of rolls and cylinders, it is easier to install: even under the ceiling, you can lay the slabs yourself.


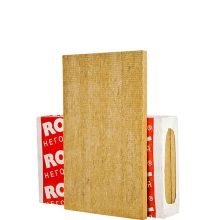
Now let's take a look at the individual material models for different types of finishes and thermal insulation. For stoves, fireplaces and other heating surfaces, Fire batts 30 Dm 110 wool with a foil layer is well suited. The material is able to withstand heating up to +750 degrees, which noticeably distinguishes it against the background of ordinary thermal insulation, which can lose its protective characteristics even at +250 degrees.
An additional aluminum layer will help warm up the room in a shorter time and save fuel.

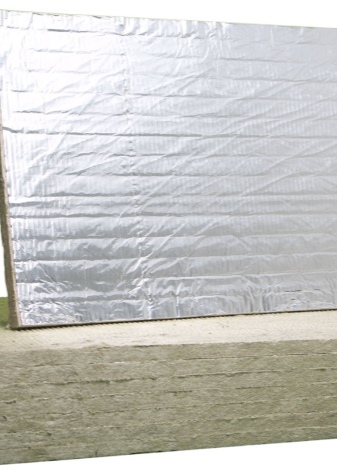
For the technical insulation of air ducts or tanks, Rockwool has developed the Lamella Mat. This is stone wool in the form of strips, which are glued in a layer of reinforced foil. This resilient shape allows the material to not deform in corners and folds. Lamella Mat can be used with all building materials due to its chemical inertness. For installation, wire or adhesive tape is usually used.
To work with facades, a whole set of compatible components has been created - Rockfacade. The set includes thermal insulation boards, fasteners and materials for finishing the facade, which are tinted at the factory.

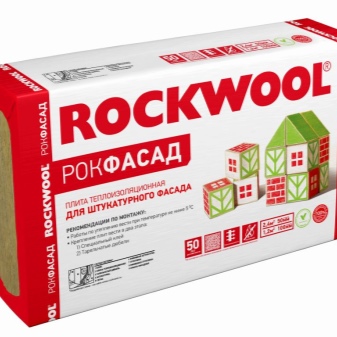
System advantages:
- All interlayers are breathable, which ensures high vapor permeability.
- Virtually zero fire hazard.
- High thermal performance.
- Many decorative variations, and therefore architectural possibilities.
- Durability.
- Environmental friendliness. All system components are made from natural materials.
- Ease of installation is ensured by the manufacturability of materials.
- All components are specially selected and you do not need to think about the color combination when finishing.


The Rockfacade system is used in buildings of any complexity and height. The mounting features make it possible to use it for buildings with broken architecture and uneven surfaces. Due to the large color and decorative variety, it is also used for the reconstruction of old buildings with the possibility of reconstructing all architectural elements.

For external wall cladding and facades, elements of balconies and loggias, a separate invention of Rockwell is used - Rockpanel. These are flat sheets, pressed from stone wool and painted with paint. These panels combine the advantages of wood and stone. A wide range of assortment allows you not to be limited when choosing a design.
Rockpanel perfectly protects the building from rain and can be used in the restoration of historic buildings and in the construction of new ones.

The advantages of the Rockpanel system:
- Strength and flexibility. Installation on surfaces with complex shapes is not difficult. This opens up great design and architectural possibilities. The material serves as a stone for a long time, and it is easy to process it, like wood.
- Fire safety. The facade system can be used in rooms with any fire hazard indicator. Mineral wool fibers do not change their structure at temperatures up to +1500 degrees, do not support combustion and are able to prevent the spread of flame.
- Vapor permeability... The fibers of the material are intertwined randomly and there are many small gaps between them. It is through them that water vapor passes.
- Stability of geometric dimensions. Stone wool slabs are able to withstand all weather conditions without deforming. They do not rot or delaminate over time. Following the manufacturer's recommendations, the boards can be laid end-to-end without seams.
- Ease... Low density of wool, standard thickness (6–10 mm) and excellent strength characteristics ensured small weight per square meter of material.

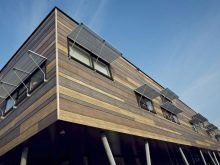
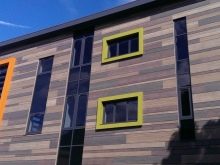
- Stable color. Rockpanel façade panels are UV resistant.They are painted with paints and covered with a transparent ProtectPlus layer on top, thanks to which the front surface becomes as even as possible.
- Non-repeating pattern... There is no pattern on the panels that should be observed during assembly. The appearance of the plates will be the same regardless of the direction and angle of their installation. This greatly simplifies the installation process and increases its efficiency.
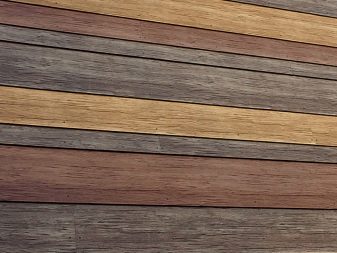

Industrial Batts 80 is used for sound and heat insulation of the surface inside the ventilation ducts. It is also used in the manufacture of sound-absorbing screens and chamber silencers. Plates are produced with a glass fiber coating on one side.
For fire protection of reinforced concrete slabs and floors of various buildings, special double-cavity FT Barrier mineral slabs are used. They have two layers - a strong upper (3 cm thick) and soft lower (5–17 cm thick).
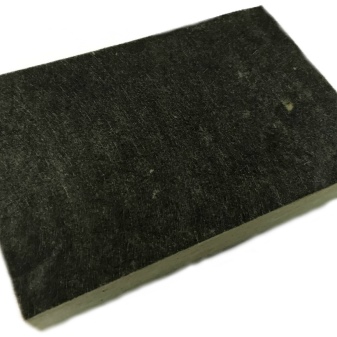

Advantages of FT Barrier boards:
- The combination of heat-insulating and fire-retardant characteristics in the material.
- Installation can be carried out at any time of the year: the boards are fixed without the use of glue.
- Possibility of renovation.
- Can be used as a decorative coating.
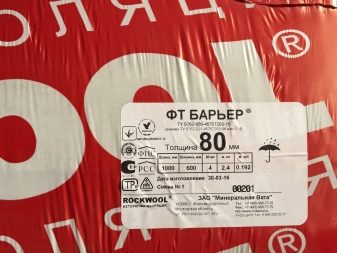

Rockwool has developed a wide range of SeaRox thermal insulation coatings:
- Reinforced foil... This type of coating is often used for vapor control. The maximum temperature that the surface can withstand is 80 degrees.
- White fiberglass. The coating provides a shock-resistant surface with an aesthetic appearance. The maximum operating temperature is the same 80 degrees.
- Laminated fiberglass... Used as a finishing layer, which does not require additional metal cladding. The foil layer provides protection against condensation and vapor barrier. The maximum temperature is 80 degrees.


There is also a product specially designed to protect buildings near hot surfaces of a fireplace (firebox) or equipment operating at high temperatures - Fireplace Butts. They have a dense structure and are coated with aluminum foil on one side. The material is made on a natural basis and has high fire safety indicators.
The product is mounted in the inner frame of the fireplace at a distance of at least 4 cm from the firebox with foil inside.

The ideal sound-absorbing material is Rockwool "Acoustic Ultrathin" mineral wool. Its thickness is only 27 mm, it is used for soundproofing already finished walls and ceilings. Due to its thinness, it is very convenient for use in compact rooms. The product is capable of absorbing high and medium sound frequencies.
Considering all the characteristics, the material can be compared to a standard 5 cm thick sound-absorbing structure.

The most common product for the insulation of a residential building is Light Butts Extra. For added convenience, it comes in two shapes: standard (80 x 60 cm) and XL (12 x 60 cm). It is used for the equipment of pitched roofs of mansard rooms, interfloor ceilings, frame walls, partitions, balconies.


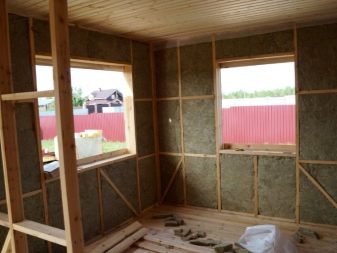

If the building does not imply important nuances that should be taken into account, then you can choose the material for cladding from the Standard or Economy categories.
Rockwool has provided products for buildings with completely different features and characteristics.

How to choose?
When choosing mineral wool, you need to familiarize yourself with all the indicated areas of construction, in which it can be used for thermal conductivity indicators. If the material is intended for facade insulation, then it will not work for working with a roof, ceiling or floor. It is worth paying attention to the service life, it is desirable that it be at least 10 years.
If all heaters are divided into groups according to directions, then the following can be distinguished:
- For the facade.
- For the roof.
- For the floor.
- For interior and exterior walls.
- For soundproofing equipment.
- For the pipeline.


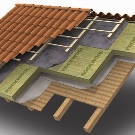



Facade
Here the most popular and frequently used is the Venti Butts product line, which is used for the arrangement of ventilated facades. This material is not able to absorb moisture and is not affected by atmospheric and domestic phenomena. In addition, the slabs of this line are made specifically for finishing frame houses.
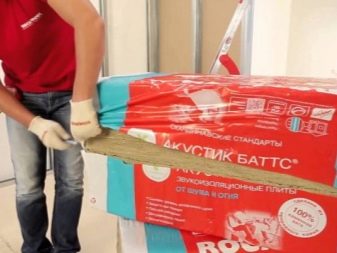

Roof
Slabs "Ruf" and "Light Butts" have been specially developed for roofing equipment. The latter have a low density and a high compression ratio. Thanks to this feature, they can be mounted literally wherever you want and need. You can call it a universal insulation.
For other purposes, "Ruf Butts" is suitable and has directly opposite indicators of density and compression ratio. These slabs are very dense and can withstand very heavy loads.
Both options described above are easy to install, durable and waterproof.
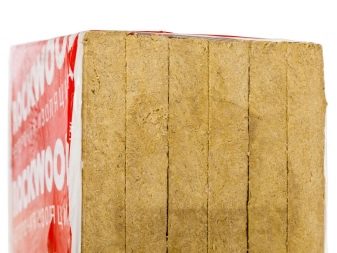

Floor
Rockwool Light Butts is also perfect for installation under logs. Only the logs should first be firmly fixed and sheathed with a board. Rockwool Floor is purchased under a screed. These are strong slabs with a low compression ratio that can withstand enormous loads without deformation.

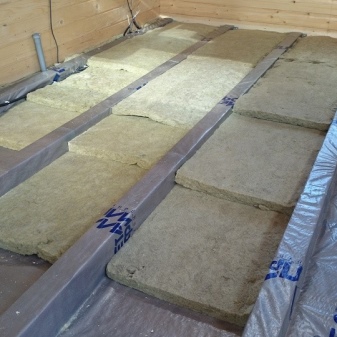
Internal and external walls
For this type of work, the Light Butts Scandic product is ideal. To work with the insulation of partitions, the Acoustic model is often used. Plates for such work are capable of dampening various noises. With the help of such partitions, you can divide the space into smaller zones. Waterproofing boards "Sauna Butts" are specially designed for thermal insulation of bath rooms and saunas.
So, having clearly defined the progress of construction and the vision of the end result, you can choose a suitable stone wool insulation and be sure that it will not let you down.


Pipeline
The cylindrical product ROCKWOOL 100 is specially designed for thermal insulation of pipes. The cylinders have two longitudinal cuts for ease of installation. The material is intended for thermal insulation of heating pipes, ventilation systems, air conditioning and others.
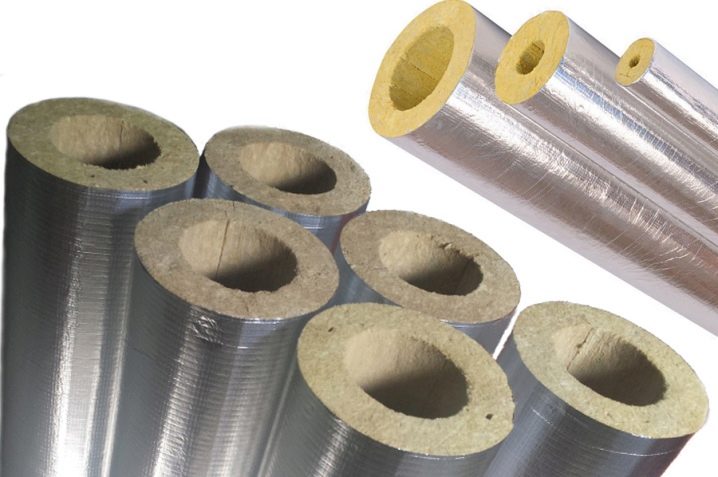
How to insulate?
Briefly, the thermal insulation process can be described as follows: mineral wool slabs are glued to the cleaned surface and fixed with dowels. Then the slabs are covered with glue, and a reinforced mesh is placed on top. After another layer of glue, you can plaster the walls. Users have long noted that Rockwull stone wool works well for insulating pitched roofs. Often, the roof has a frame system; insulation is placed inside it. The order of stacking layers is shown schematically in the figure below.
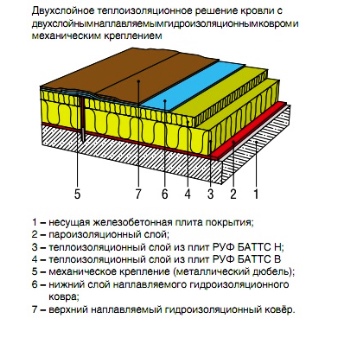

If you follow the installation rules and do not neglect the nuances of the work, you can cope with the insulation of a small room in just a day.
There are many reasons why most people opt for external wall insulation over internal insulation. First of all, this will save living space. Also, in the process of installing thermal insulation from the outside, you can reconstruct the facade and carry out the necessary repairs.
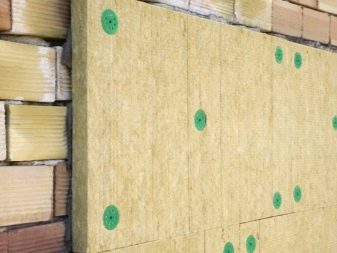
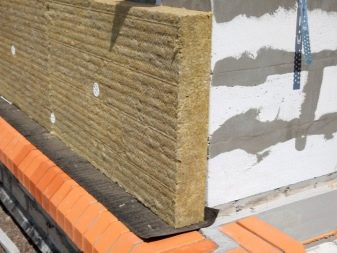
Preparing the walls
If the walls have a decorative coating, then it must be removed to the base (brick, wood or concrete). Differences in the level of the primer over 2 cm must be combed out or repaired. For these purposes, it is better to choose a deep penetration soil solution, having previously removed all dirt and dust from the wall.

To create a control grid, along which it will be possible to navigate during further work, you need to fasten a strong thread with plumb lines to the screws.
It is recommended to use two types of mineral wool for insulating walls from the outside, which differ in density. Softer mats are mounted to the wall, for example, the material will fill the unevenness of a brick wall well. The denser and tougher ones are stacked on top, because. with their help, you can form a more or less flat surface, which will later facilitate the decorative finish.


The thickness of two layers of stone wool should not exceed 100 mm. The best quality will be the option of insulation, in which cotton wool is placed under the future brickwork. In this case, the insulation will be inside the wall between the layers, which will significantly improve the thermal insulation.

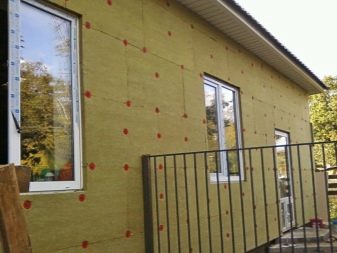
Here is a universal step-by-step instruction for the process of wall insulation:
- If work is carried out with wooden walls, before starting work, they must be impregnated with an antiseptic. Areas with dampness or fungus must be thoroughly cleaned and also saturated with a solution. Walls made of brick or concrete can be easily cleaned of paint. Damp walls need to be dried, the slopes of windows and doors must be removed for a while (as well as all decorative elements that can interfere with construction).
- A vapor-permeable membrane is placed under a layer of mineral wool so that the vapor-permeable side is located against the wall, and the other - against the insulation. This membrane is needed so that water vapor is removed from the walls.
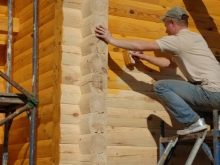


- On top of the membrane, wooden slats are attached using self-tapping screws. The distance between the slats should exceed the thickness of the insulation material by about 1–2 cm. At this stage, it is important to use a level or special hangers.
- The space between the slats is completely filled with thermal insulation. Installation should be started from the bottom, gradually moving upwards, if the mineral wool is in the form of rectangular mats. The roll should be laid, starting from the top, gradually fixing it to the wall with dowels.


- A layer of wind protection is laid on top of the insulation. The film is attached with a construction stapler to the slats, after which the entire layer of insulation is additionally fixed. To provide even greater waterproofing, the attachment points of the layers can be glued with a special metallized tape.
- One of the most important stages is the arrangement of a ventilated facade. The gap through which the wall will breathe should be about 5–7 cm. For this you need to attach additional slats or profiles.


Starting the insulation of the outer walls of the house, you need to remember that their thickness will increase markedly and you will need to make new window slopes, platbands and other decorative trim elements. But this method at least does not hide the space inside the room, so replacing some parts should not be a big problem.
Laying scheme of layers for thermal insulation of external walls is shown in the figure below.

Warming process
Work should start from the bottom and use not just construction glue for fastening, but special glue for stone slabs. It is often sold in packs of 25 kg. The width of the joints should be kept to a minimum.
It is imperative to reinforce the coating. This can be done using plastic dowels. This will increase the strength of the entire thermal insulation coating and prevent the formation of cracks in the walls.

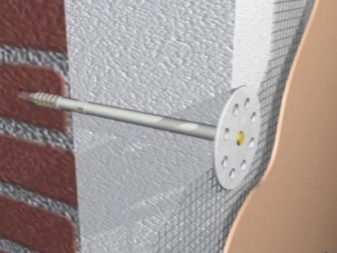
The order of the layers is shown in the diagram below.

Then you can start decorating the walls. Plaster or water-based paint is suitable for this.
There are several ways to apply decorative plaster:
- Bouffant. To do this, use a metal brush with a wire pile. The surface with a layer of plaster is literally combed, and the resulting pattern is left to dry for a day. When the surface dries slightly, you can lightly wipe the wall so that small and loosely fixed particles crumble.
- Stamping. Performs with a roller, on which a nozzle with a pattern is fixed. Everything is very simple here: you don't even need to repeat the passage of the roller over the same place. Decorating will take a few hours at most.
- Facing. It is done with a rubber or regular sponge dipped in soapy water. A drawing is applied to a fresh layer of paint, which can imitate the texture of a stone or any other.


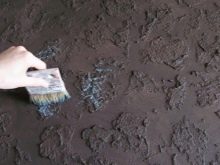
There is a wall decoration method that provides for a ventilated facade. This system allows moist air to evaporate freely.Mineral slabs have very good moisture resistance, but they still pass a small percentage through the fibers. Therefore, the ventilation system will not be superfluous.
The procedure for installing a ventilated facade is simple: first, a vapor barrier is mounted, then a small layer of air is left with the help of anchors. On top of the insulation, you can install a wooden grate or apply a windproof membrane in the form of a film. At the end of the work, a decorative finish follows.

Analogs
Despite the big name and demand all over the world, Rockwool products have several disadvantages:
- Compared to analogues, Rockwool insulation is quite expensive.
- Protective clothing and goggles must be worn when mounting or cutting material. This may cause some inconvenience, but this is unlikely to be a problem for an experienced builder.
- The water-repellent characteristics of the material are achieved by treatment with special solutions that do not provide 100 percent waterproofness.
Therefore, it will not be superfluous to install an additional membrane to protect against moisture.

On the Russian market there are quite high-quality, but cheaper analogs of almost all varieties of mineral wool. These are such manufacturers as Isover, TechnoNICOL, Knauf, Paroc, Isoroc. On specialized sites, you can compare manufacturers for any characteristics using special tables.
Many could hear about such material as slag. This is a heater made from blast-furnace slags. It was widely popular during the Soviet era and was manufactured at metallurgical plants.

Having high levels of hydroscopicity, the insulation was not very effective. Notable disadvantages also include a fairly high level of acidity and low vibration resistance. Not the best set of characteristics, but at the time it was the only thermal insulation material of this kind. Naturally, over time, new manufacturers ousted slag wool from the market, but many buildings insulated with this material are still standing today.
Do not forget about such material as glass wool. He, too, was quite popular before. By the way, it is used for insulation now, but rather with the aim of saving on material and, accordingly, on quality.
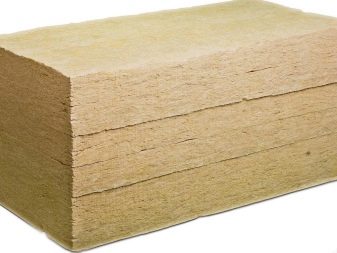
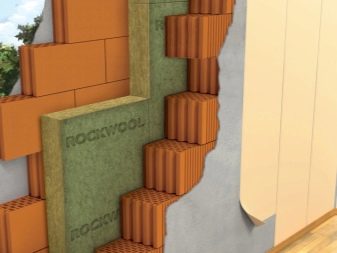
Broken glass and quartz are taken as the basis for its manufacture. There is a common misconception that glass wool is not a mineral. This is not true. It belongs to the same category as stone wool - mineral wool. There are some of their characteristics, having familiarized yourself with which, you can understand the nature of such a delusion.
Like rock wool, the material is heated in an oven at high temperatures and then stretched into very thin fibers, which are later bonded together.

The material cannot be called absolutely safe, since formaldehyde resins serve as a binder for the fibers.
At a cost, glass wool is much more affordable than stone.
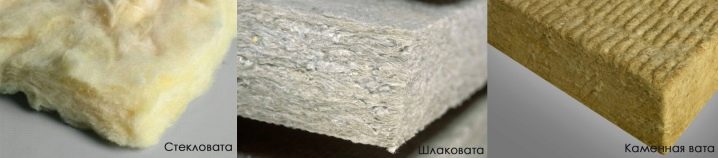
This can be explained by the cheapness of the raw materials used. Transportation costs are also lower, because the packed material takes up very little space. After unpacking, the glass wool returns to its previous shape.
It does not burn, does not cause corrosion in contact with metals, and has a low density. And the sound insulation performance is even higher than that of stone wool. Along with these obvious advantages, there is a rather tangible disadvantage: glass wool shrinks over time as a result of the crystallization of the substance fibers.
It is quite difficult to work with the material. It irritates the skin, eyes and respiratory tract. Therefore, protective clothing should never be neglected.
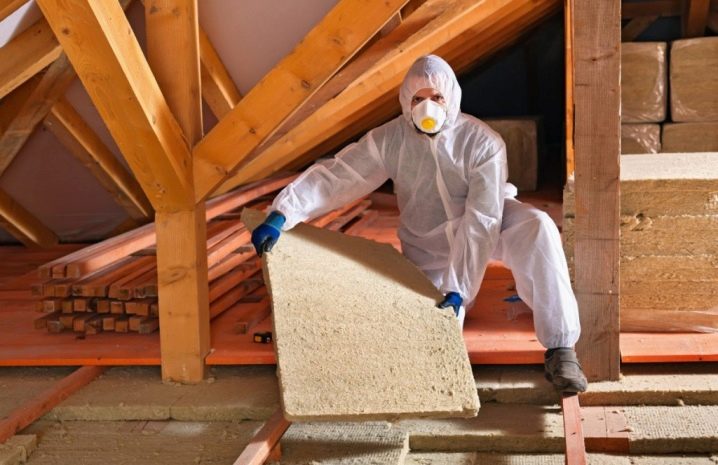
If you do not use gloves during the installation of the insulation, the smallest particles of glass will penetrate into the skin and it will be quite problematic to get rid of them later.The impact of small particles on the mucous membrane will be individual for everyone, but it is better to buy ordinary protective glasses in advance and not bring the situation to a doctor's appointment.

Helpful hints
Feedback from regular customers speaks for themselves: Rockwool products have become the best in the world for a long time. But in order for the insulation to serve for a long time and meet all its characteristics, you need to follow some rules:
- It is important to pay special attention to the transport of the material. Mineral wool is capable of absorbing moisture from the air, therefore it must be transported in closed machines, and then stored in a dry room.
And in order to reduce the occupied area, the mats are recommended to be transported in a compressed form.

- Stacks with slabs for transportation should not be less than two meters, and rolls and mats should be stacked in an upright position. This will facilitate subsequent unloading.
- It is undesirable to walk on stone wool without packaging, because this can damage it.
- To adjust mineral slabs to the required dimensions, they are usually cut with a long hacksaw, leaving 1–2 cm allowances at the edges. They are necessary so that the material completely fills the space, shrinking a little, the cotton wool will enter the frame more tightly. The slabs are cut individually, and the rolls can be cut without unrolling.
- When cutting products, it is recommended to wear construction gloves and protective clothing made of dense fabric, the eyes must be protected with special glasses, and the face with a mask.
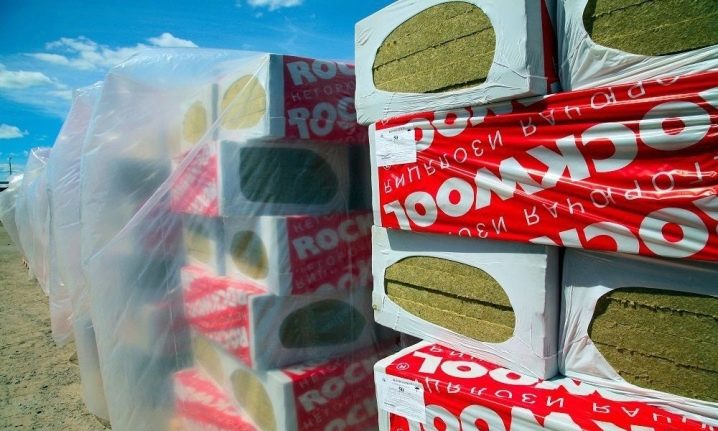
- There are some universal tips that will help when using any kind of mineral wool: when insulating a flat roof, it is better to put insulation in two layers, granular stone wool is perfect to improve sound insulation, slabs with grooves for ventilation are considered to be the most durable, they are also often used to insulate attics two layers of cotton wool.
- To give the roof a slope for water drainage, the use of mineral mats with a variable cross-section is suitable.
- When constructing one-story buildings with three-layer walls, it is not at all necessary to leave a ventilation gap.



- To perform the work on thermal insulation as efficiently as possible, you need to take material with a width of 1.5-2 cm more than the distance between the frame supports.
- Do not forget that the vapor barrier and waterproofing layer can provide good ventilation of the insulation layer.
- For thermal insulation of walls, it is most convenient to use mineral wool in rectangular slabs. They clearly fit together and help to reduce the gaps between the plates or prevent them altogether.
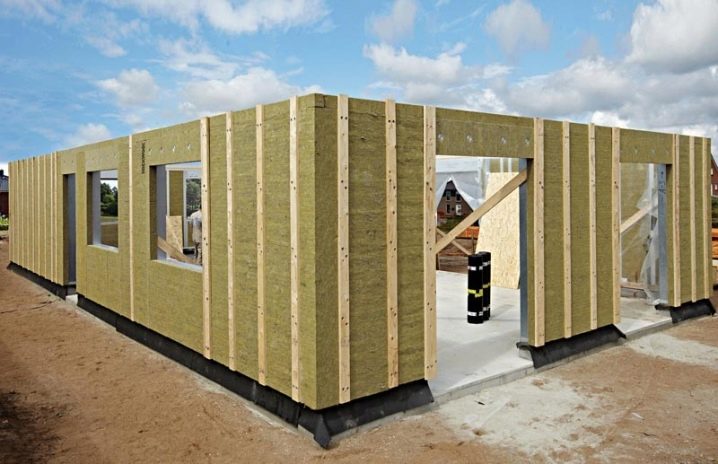
- Before starting the installation work, all cracks and cracks on the surface must be properly repaired. For this, polyurethane foam or felt is suitable.
- Professionals do not recommend laying a thermal insulation layer on cables and wires. Always leave wiring on top to reduce the risk of fire.
- When pipe thermal insulation is laid in several layers, it is necessary to provide that the joints between the plates on different layers do not coincide with each other and do not overlap.
When buying a sealing material, you need to pay attention to its edges: they should not be torn or uneven. This will help prevent gaps between the plates during installation and other damage that may result from this.



Watch the life hacks for using Rockwool mineral wool in the video below.
The comment was sent successfully.