Thermal insulation of the walls of the house: what is it and what materials are needed?
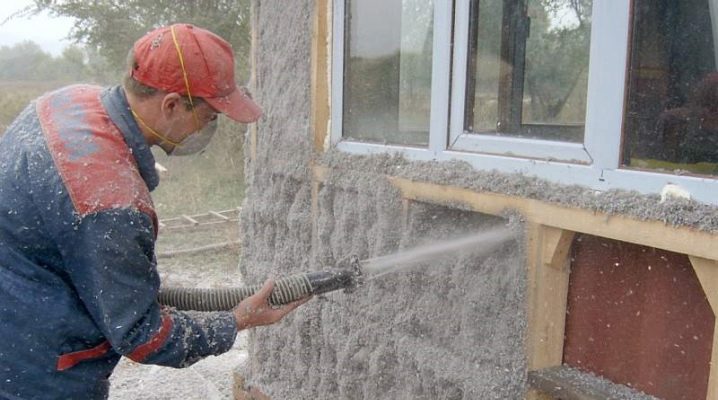
When building houses, people care about their strength and external beauty, trying to make the most of the available space. But the problem is that this is not enough in the Russian climate. It is imperative to provide enhanced thermal protection, even if construction is carried out in a relatively warm area.
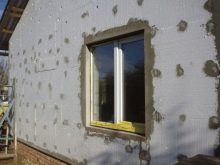
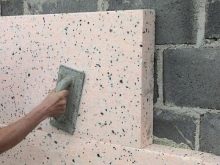
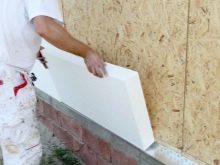
Features and Description
Thermal insulation of the walls of a house is a combination of materials and technical solutions that prevent heat from leaking out through the walls. To solve this problem, you need:
- reflect infrared rays into the interior of the house;
- block, if possible, the escape of heat outside;
- make its convective leakage as difficult as possible;
- guarantee the safety of the main structures;
- to achieve stable waterproofing of the insulating layer (even a waterproof one is better protected additionally).
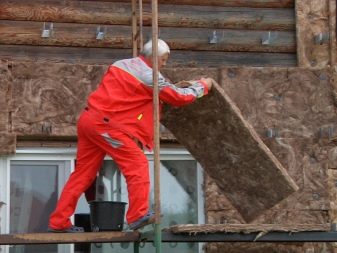
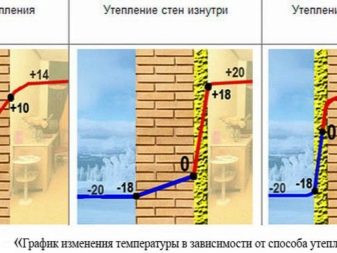
Unfortunately, such a definition has to be corrected in reality. After all, the creation of a shell around a house that is impervious to thermal energy in practice is either very difficult and expensive, or completely unrealizable for technical reasons. Big problems are brought about by the so-called cold bridges, which break the solidity of thermal protection and reduce its effectiveness. There are only two ways to solve this problem fundamentally - using foam glass or gunning from the border with the basement to the ridge. But both schemes have significant drawbacks that must be taken into account.
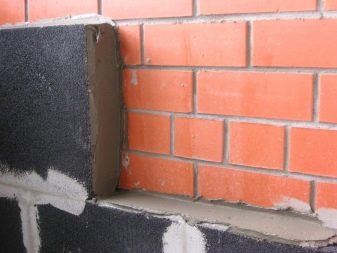
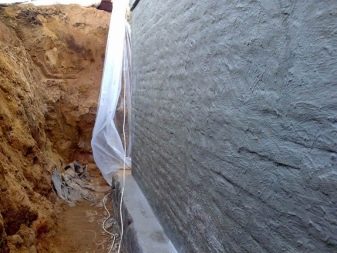
In addition to cold bridges, you will have to pay attention to:
- ventilation of materials and structures;
- their interaction with moisture;
- the need for a vapor barrier or vapor-permeable shell;
- fastening strength and its nuances;
- sunlight intensity;
- average annual and maximum snow depth.
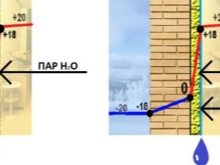
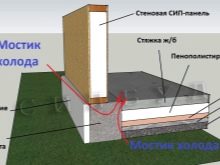
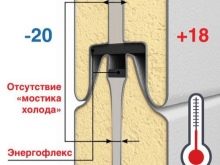
Raw material overview
The accuracy of the choice of the base material is of great importance for the thermal insulation of home walls. So, organic thermal protection means are represented primarily by foam of dissimilar density. They have a specific gravity of 10 to 100 kg per 1 cubic meter. m. This allows you to choose the optimal load on the foundation and thermal qualities of the scheme. But there is a serious drawback: poor fire resistance, so there is a need for structural protection with non-combustible materials.
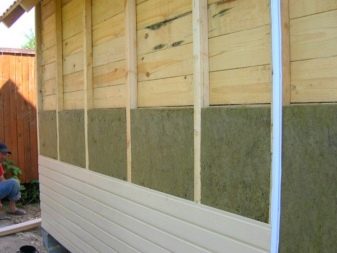
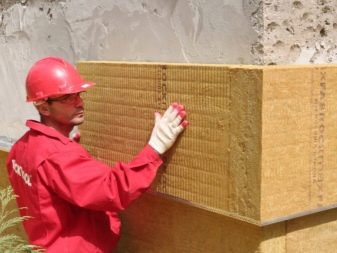
Other organic thermal insulation products are:
- products of processing forest waste and waste wood;
- peat-based slabs;
- agricultural waste (structures made of straw, reeds, and so on).
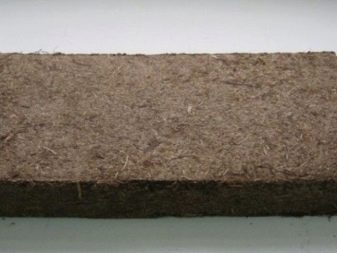
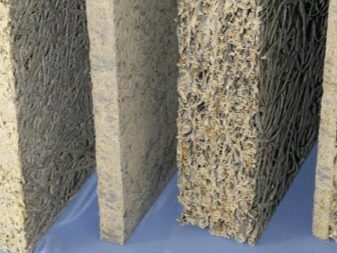
Heat-resistant protection by such methods is quite possible. But you will have to put up with poor resistance to water, to destructive biological agents. Therefore, in modern construction, such blocks are used less and less as thermal insulation. Mineral materials are much more in demand:
- stone wool;
- fiberglass;
- perlite and vermiculite blocks;
- cellular concrete and a number of other products.
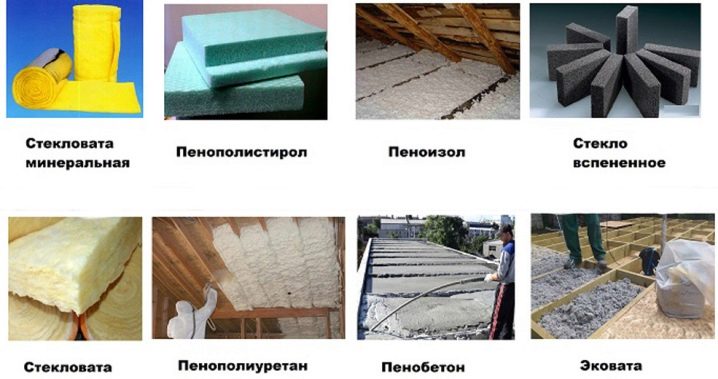
Mineral wool slabs They are made by processing the melt of rock stones or metallurgical waste to the state of a glassy fiber. The specific weight of the products obtained varies from 35 to 350 kg per 1 cubic meter. m.But with a remarkable level of heat retention, mineral wool is not strong enough and is easily damaged by water. Only the most modern varieties have the required degree of protection.
By tradition, some people use to insulate walls. expanded clay... But such a solution can hardly be called optimal. Even the lightest grade of expanded clay exerts a significant load on the base. And you will have to use it a lot, because three times more heat will go outside (with the same layer) than through the most effective insulation. And, finally, the expanded clay layer gets wet easily and dries very badly. It is not surprising that films of various types are becoming more widespread. It helps to increase the waterproofing of the inner part of the walls, polyethylene is especially good.
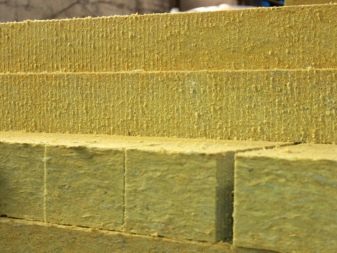
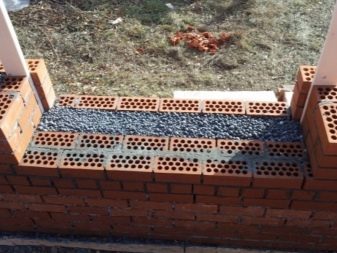
In some cases, for thermal protection of walls, it is used polyurethane foam... The reliability of such a coating is appreciated by the builders. But you will definitely have to wear protective equipment to apply it. Foam insulation allows steam to pass through and restrains water ingress. It can be used to close gaps when installing a plastic window into the wall.
Monolithic sheet thermal insulation is easier to install than foam insulation, and usually does not require specialized equipment.
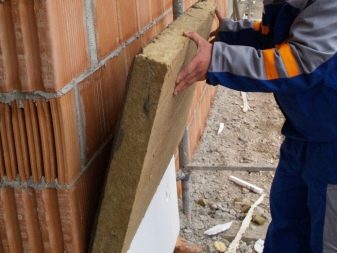
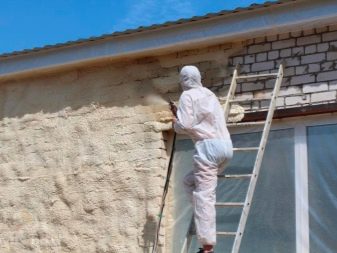
Modern manufacturers have learned to make sheets that can work in a wide range of temperatures and maintain elasticity. With the help of these structures, it will be easy to provide heat protection for pipes and other communications entering the house. Thermal insulation membrane there are two main types: the first restrains the penetration of water vapor from the inside of the room, and the second allows the steam generated inside the wall to escape freely. When choosing the second type of materials, the key value should be given to their vapor transmission capacity, that is, the amount of outgoing vapors per unit of time. Flexible multilayer thermal insulation is used either for insulating pipes or for reflecting heat rays inward with an outer foil sheath.
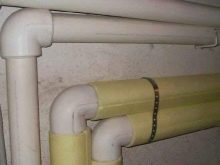
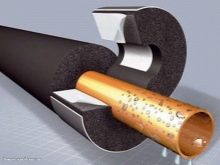
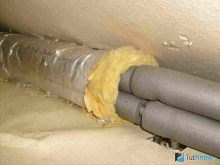
Specifications
High-quality thermal insulation almost always plays the role of sound insulation at the same time. The choice of such a solution is justified, because it is required to reduce construction costs as much as possible and reduce the overall thickness of the walls. Reliable sound damping is impossible to implement, if we do not take into account the differences between airborne noise (moving in the air) and shock (transmitted by vibration of structures). Walls should fully isolate people from airborne noise. At the same time, external walls have an unequal level of protection, which is not standardized.
The standard values for noise protection are only minimum guidelines, they should not be less in any case. In practice, it is recommended to completely exceed these indicators by 5-7 dB, then the situation will become comfortable. For external walls, airborne noise absorption is recommended to be from 55 dB, and near railways, airports, federal highways - at least 60 dB. Sound absorption is provided by porous or fibrous heavy materials; mineral wool and sand are most often used for this purpose. Relatively recently, polymer-based membranes with a spongy structure having a thickness of no more than 0.5 cm have begun to be used.
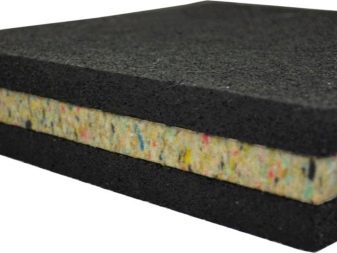
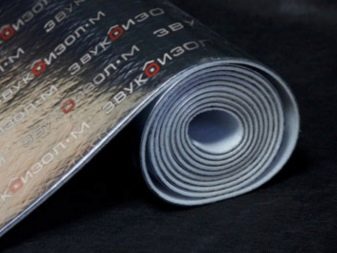
In most cases, a noise absorber is placed between materials that reflect sound. But sometimes a two-layer, four-layer or five-layer coating is practiced.
To minimize the penetration of sound inside, it is necessary to break the bridges of the acoustic transmission using special fasteners. You will definitely have to use acoustic mounts, which are presented in many types. Only specialists will be able to choose the right option correctly.
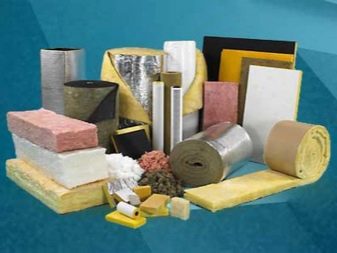
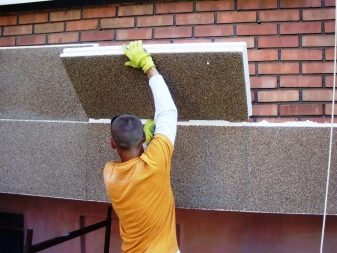
Manufacturers rating
It is logical to supplement the comparison of the properties of individual materials with a comparison of the level of specific manufacturers. Basalt wool brands "Tizol" it is mounted very easily, the size of the sheets is 100x50 cm. But it must be borne in mind that the sheet can crumble due to the heterogeneous density in different places, and flaws may also appear in it. During the season, cotton wool drops by 15-20 mm. You can buy "Tizol" in any specialized store.
Competing firm "Rockwall" can offer basalt wool with a density of 37 kg per 1 cu. m. Here, too, everything is in order with the installation with frame openings of 59 cm. One package allows you to cover about 6 m2 of the wall. Finding the company's products is easy in many retail outlets. The container is very reliable, even rough handling (within moderate limits) will not damage the material; service life will delight homeowners.
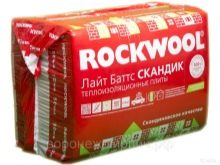
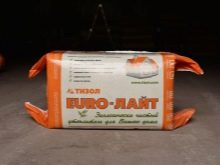
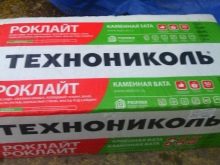
Techno-Rocklight is also one of the easily installed materials. There are four key standard sizes that allow you to choose the best look for a particular case. But the shortened fibers easily crumble, therefore it is permissible to work only with gloves and with a respirator on. It will not work to buy Rocklight in certain regions of the Russian Federation. The container is not reliable enough, in the process of loading the bales may fall apart.
Mineral wool firm "Isover" sold in rolls and slabs. Technologists have managed to overcome their traditional barbs and increase their strength. Such a product is sold in all specialized stores. Cutting and styling is pretty straightforward. But there are also problems - unpleasant odors, the need to use protective devices, insufficient information content of the labels on the packaging.
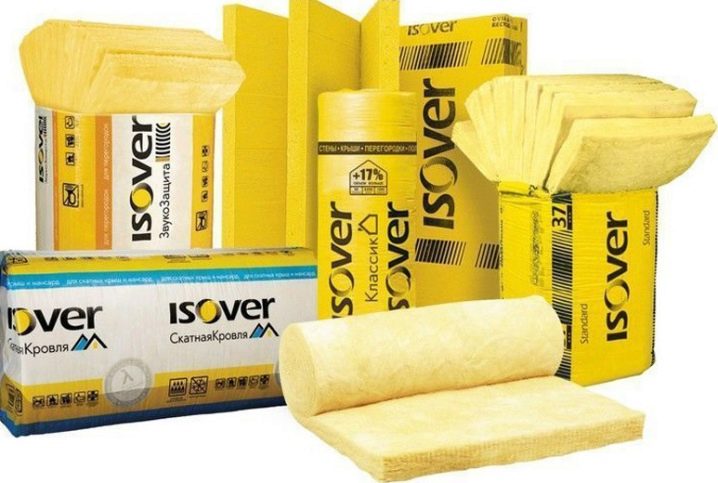
Products and services Knauf has a wide range of options and effectively dampens sound. The mineral wool of the German concern does not contain toxic phenol-formaldehydes and many other components. The crumbling of the material is excluded, the blocks are very light.
You can put the stove at a comfortable angle. As for the problems, again you need to use protective equipment.
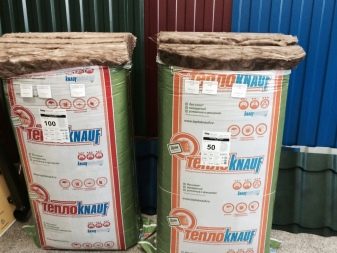
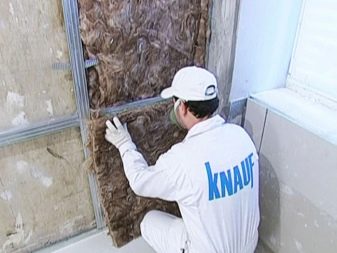
How to choose?
Having dealt with the brands, it is worthwhile to study the features of specific species again. Experts recommend to precede the study of reviews by determining the appropriate type of insulation material. It is extremely rare now to use bulk fillers, mainly rolls and plates are used. Additionally, a distinction is introduced into fibrous, liquid and cellular formats. It can be difficult to use the second type without special equipment.
It is very important to pay attention to whether a particular insulation is suitable only for internal or external wall treatment. When choosing, it is also worth finding out how large the coefficient of thermal conductivity is - the smaller it is, the more heat remains in the house. If it is necessary to achieve a long service life of the coating, preference is given to materials that absorb water minimally. The same circumstance directly affects the resistance to the appearance of the fungus. The next important parameter is flame resistance; individual materials, even when heated to 1000 degrees, do not lose their original structure.
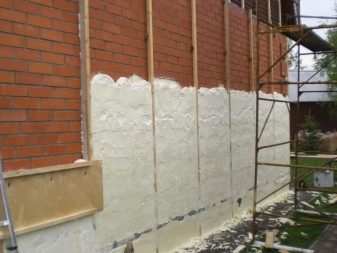
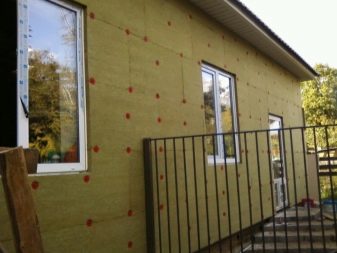
Even if the insulation meets these requirements, it is useful to find out how well it:
- resists deforming forces;
- stops steam;
- withstands exposure to rodents and microorganisms.
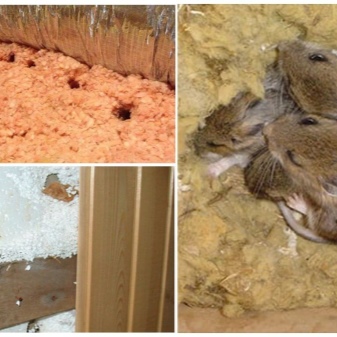
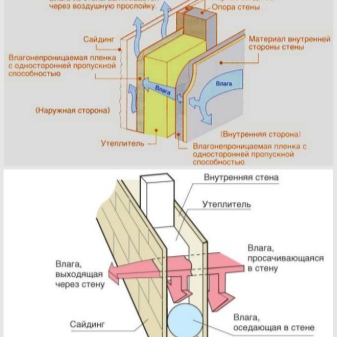
For the internal thermal insulation of the walls of the house, it is difficult to find something more perfect than expanded polystyrene. Slabs made from it are always thin and do not reduce the available space. The elimination of moisture absorption helps to bring the dew point outward and reduce freezing of the walls. Equally important, in many cases it is possible to do without vapor barrier.
But when it is planned to insulate the walls from the outside, it is better to use PPU.
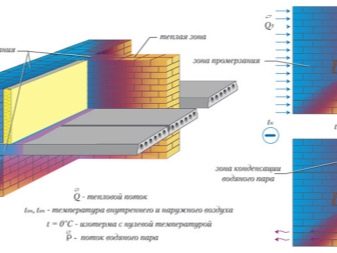
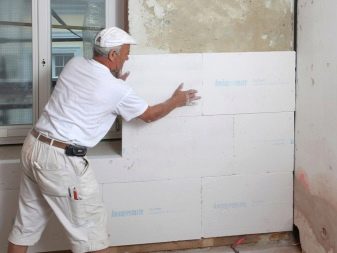
Polyurethane foam is mainly sprayed onto the protected surface, creating a monolithic canvas that does not have a single joint and area where heat would escape. Excellent adhesion makes it possible to use this material on any surface. Among organic heaters, mineral wool products are in the first place.Their economical option is always equipped with a foil layer. Do not put financial considerations first, then the result will be of poor quality in any case.
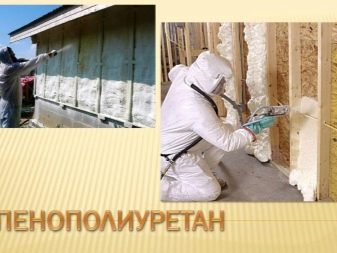
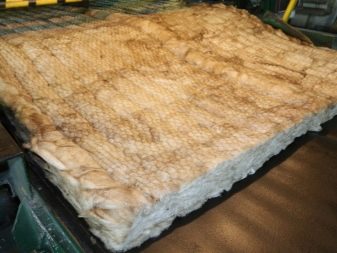
Process technology
The use of mineral wool for thermal insulation is justified in a situation where insulation from the outside is not possible. The first step is naturally cleaning the surface from dirt. It is especially important to get rid of traces of mold and treat the affected areas with antiseptic mixtures. The slightest grooves and cracks should be repaired with cement compounds. An effective method of dealing with shallow (up to 30 mm) holes is the use of polyurethane foam.
If their depth is greater, you will have to supplement the foam with tow. Apply antiseptics and primers carefully, each layer must dry before applying the next layer. To maximize the efficiency of work, it is necessary to level the surfaces, ensuring an especially tight pressing of the structure or frameless heaters. On the surface of brick, foam concrete or aerated concrete, plaster is applied, and a layer of liquid waterproofing is made on top of it. The frames are formed from timber or steel profiles.
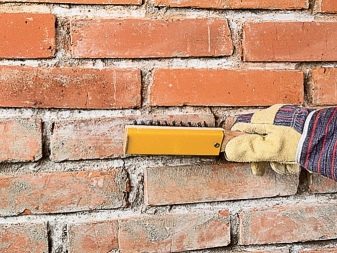

The distance dividing the vertical supports is made slightly smaller than the width of the insulation rolls. Then the connection will be very reliable. The gap to the wall structures is made so that the slab fits there and a few tens of millimeters of air gap remain. This is achieved by spot application of adhesive mixtures.
Plates are preferable to rolls as they roll less; the use of horizontal strips finally helps to cope with this problem.
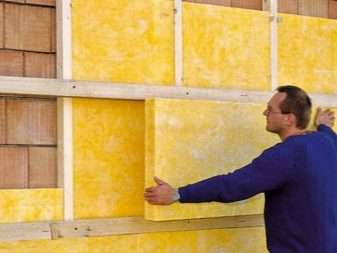

Installation of vapor barriers is carried out from the upper lobes of the structures, during operation they move horizontally. The main fastening method is double-sided tape. On wooden substrates, you can attach a vapor barrier film using a furniture stapler. It is recommended to make an overlap of at least 100 mm, while at the same time, overlaps must be made on corners, floors and ceilings. Mounting tape and duct tape are ideal for sealing joint joints.
Moving the film closer to the surface means filling such areas with liquid sealants. Above the "pie" is placed a rack counter-grill, its mounting width is from 1.5 to 2.5 cm. Thanks to the counter-grill, it is possible to make a full-fledged ventilation gap. A front decorative shell is placed on top of it. To refuse to use a vapor barrier, foil is mounted from the inside, which should be turned into the interior of the room.
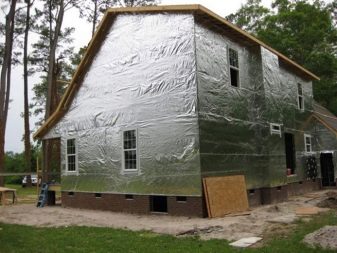
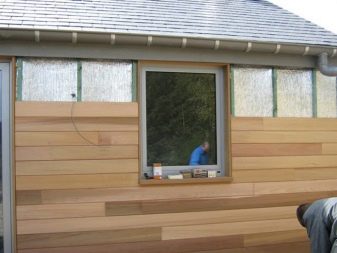
Otherwise, work is carried out when using roll blocks. Brackets in the shape of the letter "P" are placed on the surface, they will allow you to install metal profiles. Typical vertical distance is 0.6m and horizontal distance may be slightly shorter. When measuring the required amount of mineral wool, one must not forget about a tolerance of 0.1 m. The ears of the staples will block the vertical movement of the insulation. When they are pressed, they put the profiles and attach the gypsum board.
According to professionals, the insulation inside is much worse than the external insulation of living quarters. This is the most effective option in practice, in addition, it does not take away useful space and avoids the formation of condensation. Another important advantage of this solution is the prevention of cold bridges. External frost insulation is carried out using a wet or dry technique. The wet option involves the application of an insulating layer directly to the wall and subsequent finishing along it.
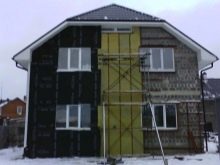
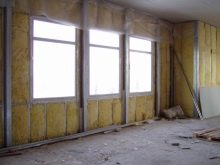
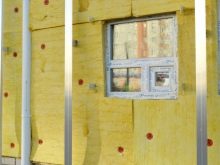
The total thickness of the insulation block reaches 150 mm. Mineral wool is "planted" on glue or umbrella hardware. It is recommended to reinforce the base. After that, face finishing is carried out, which at the same time has a protective function. A similar solution is recommended for brick and aerated concrete buildings.Frame houses before laying mineral wool are covered with rigid flooring of oriented slabs.
It is unacceptable to install mineral wool during rain and high humidity. In theory, it can dry, but it will take a very long time to wait. The insulation outside is always covered with a moisture-proof film. A metal apron is placed on the slopes, which reliably protects from contact with precipitation, and from wind and rain. All gaps around the double-glazed windows must be closed with polyurethane foam; it is advisable to take care of its protection from moisture.
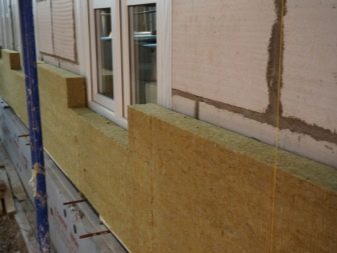
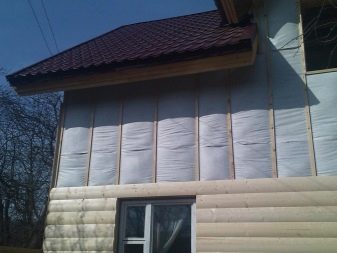
You cannot limit yourself to the insulation of some walls, it is very important to provide for thermal protection of the roof. Up to 1/5 of all heat leaves the building through the ceilings.
Since most pitched roofs are equipped with flammable materials, only non-flammable insulation material should be used. In addition, it must freely pass water vapor and not absorb water itself. For a flat roof, the insulating layer must be set as strong and stable as possible, otherwise it will not withstand the resulting load.
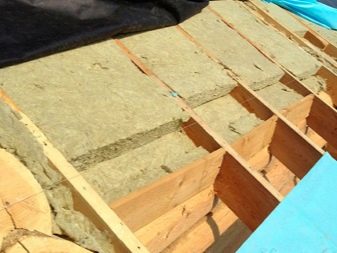
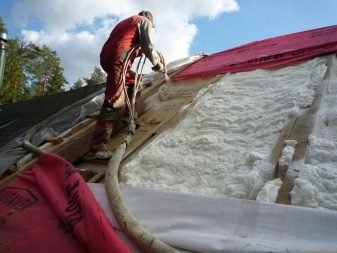
How to Prepare?
Calculations of insulation elements are extremely important. If carried out poorly or not at all, serious problems can be encountered. So, weak insulation will not allow maintaining a comfortable temperature in the premises of the house. In addition, it will move the dew point to the inside of the wall. The formation of condensation provokes infection with mold and other putrefactive organisms. Too strong thermal insulation solves this problem, but it is economically unjustified, since an increase in layer thickness only slightly improves practical qualities.
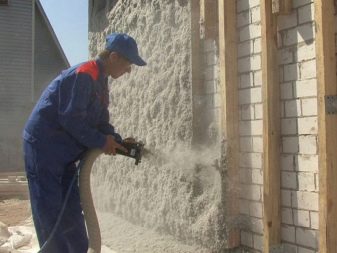
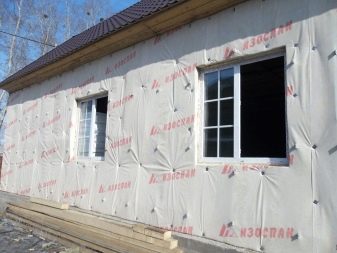
It is necessary to take into account the thermal resistance, which is normalized for different regions and key settlements. Competent calculation allows you to build the thinnest (as possible) wall and not worsen the consumer qualities of the house. The standard formula for calculations looks like αyt = (R0tp / r-0.16-δ / λ) λyt. To the left of the equal sign is the required thickness of the insulation. On the right, following the normalized resistance, there are:
- wall thickness;
- coefficient of heat loss through their bearing part;
- indicator of heat loss through the insulation;
- material homogeneity index for heat flux.
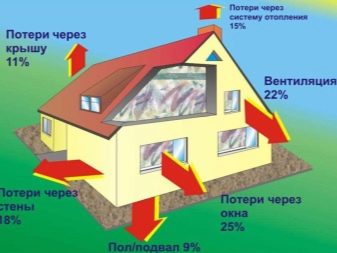
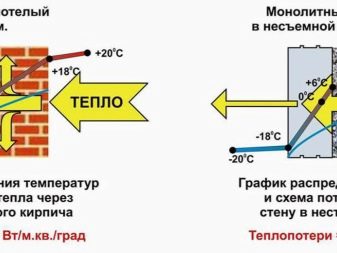
Thermal characteristics in wall cakes with air gaps may not be considered for the outer cladding and the ventilated pause itself. The choice of a suitable width for a single roll or board is due to considerations of ease of use.
At the same time, we must not forget that the fewer joints are made, the higher the reliability of the mounted structure will be.
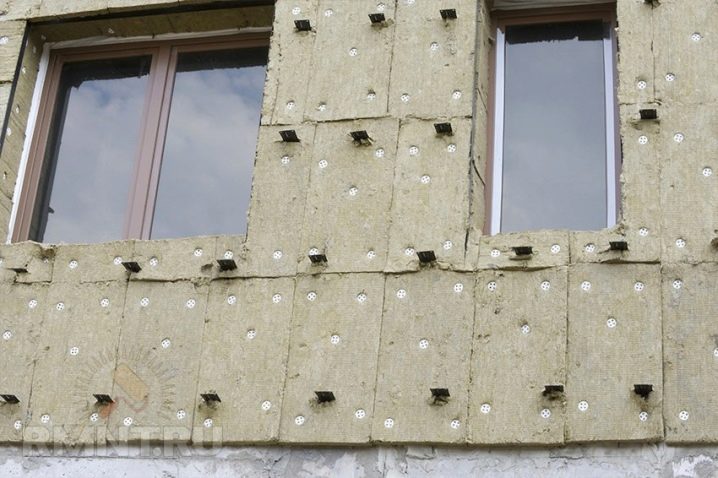
How to do it yourself?
Do-it-yourself installation of wall insulation is quite simple. But there are a number of nuances that are often overlooked by amateur craftsmen. So, in the cold period of the year, it is worth covering the exhaust ventilation ducts a little and completely blocking them in case of a long absence. Since up to 80% of all losses through walls are due to heat rays, reflective heat insulators are preferable to conventional ones. In already operating houses, it is often necessary to do internal insulation, which requires additional installation of a vapor barrier.
Thermal insulation of the walls gives a positive result only if the basement thermal protection has been prepared in accordance with all the rules. VA ventilated facade is created by attaching an insulating layer to dowels or using a frame with external finishing in any convenient way. If the wall is made of brick, you can resort to well masonry. The inability to ventilate it means that moisture-resistant solutions will have to be used. Insulating plaster plays only an auxiliary role, in addition to it, it is imperative to make a substrate from a mesh covered with a primer.
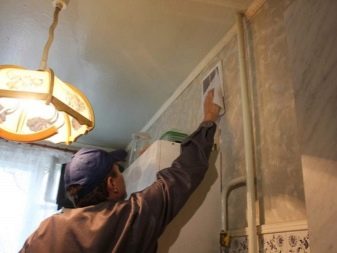
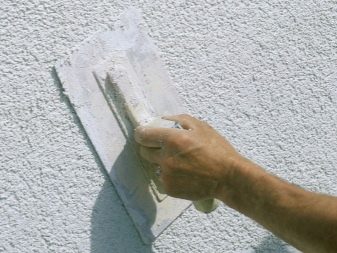
Helpful tips from the pros
Do not ignore the advantages of plastering an insulated wall. Yes, it is more time consuming and messy than dry block finishing, but allows for a combination of finishing and additional heat savings. The permeability of the wall cake for water vapor should gradually increase from the inner surface to the outside; any other ratio of layers is fundamentally wrong. Vermiculite is extremely expensive, but it is not difficult to get around this difficulty - you only need to apply it not autonomously, but as part of a warm plaster. This solution, due to its excellent vapor permeability, can be used almost everywhere.
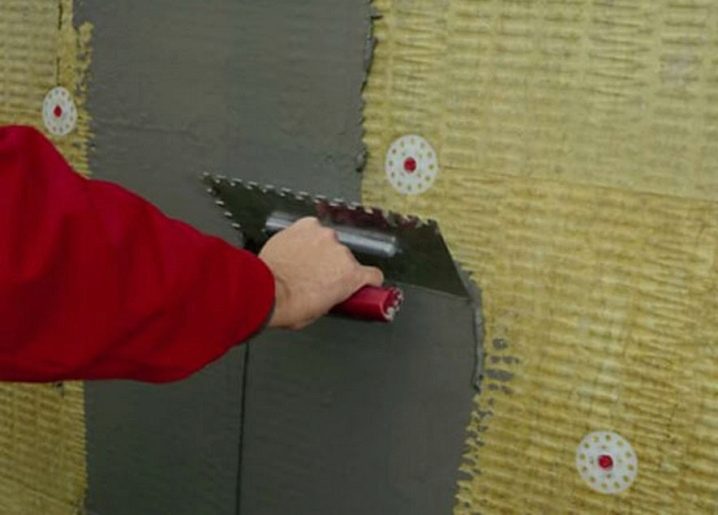
For the intricacies of choosing a heater for the walls of the house, see the video below.
The comment was sent successfully.