Extruded polystyrene foam: what is it and how is it used?
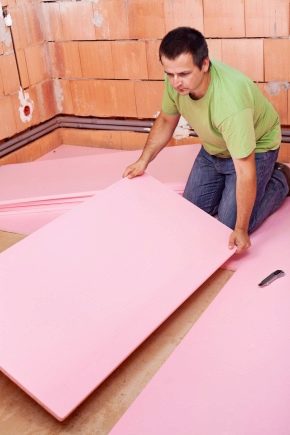
Currently, most construction and cladding work is not complete without the use of foam materials. One of them is extruded polystyrene foam, which is popular today. Today we will talk in detail what it is and how this material is used.
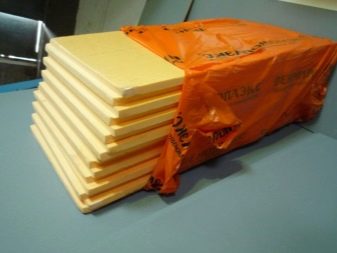
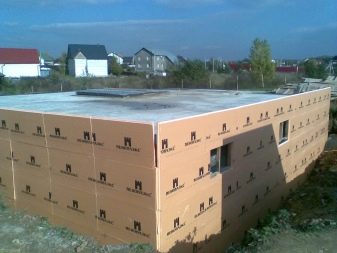
What it is?
Today, the assortment of various finishing materials is so great that one can simply get confused in its wealth. So, one of the most popular coatings with many positive qualities is extruded polystyrene.
This product is a special synthetic material that was first seen in the United States in 1941. Currently, polystyrene is used for a variety of purposes. It is to this raw material that they turn to when insulating structures such as foundations and roofs. In addition, extruded polystyrene makes good contact with facade plaster.
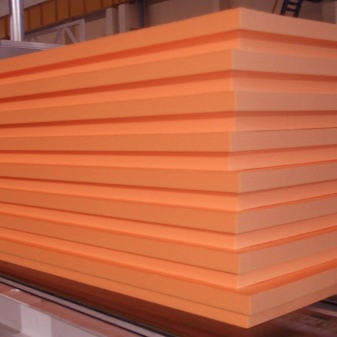
Features of production
Paying attention to the name of this popular material, we can conclude that it is one of the forms of deeper processing of foamed polymer raw materials, which is obtained due to the condensation of styrene under the action of catalysts in organic solvents.
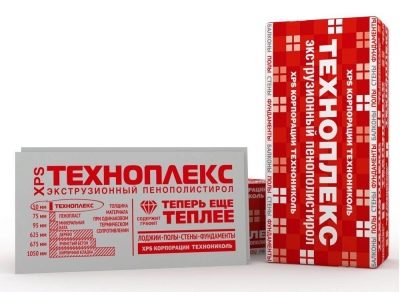
The performance characteristics as well as the advantages and disadvantages of this material are due to the process and its manufacture.
- First, the feedstock is taken, represented by small particles placed in the reactor. There, under conditions of high temperatures and pressures, these components are saturated with a special gaseous component.
- After the pressure is released, the mass begins to expand rapidly, like foam. At the same time, it gradually cools down and acquires all the properties necessary for a solid.
- The hot and viscous mass is passed through extruders. Thanks to these actions, the polystyrene becomes denser and similar to multilayer plastic.
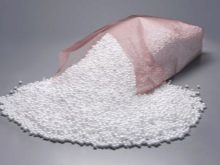
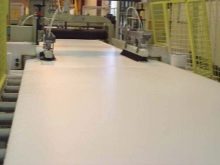
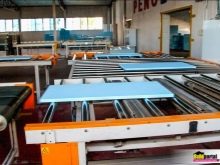
As a result of these stages of work, a special extruded material is obtained. In its immediate structure, polystyrene occupies only 1–2%. The remaining components are air purified from water vapor, which has a characteristic minimum thermal conductivity.
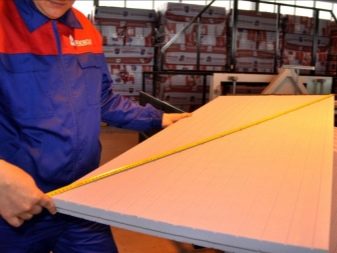
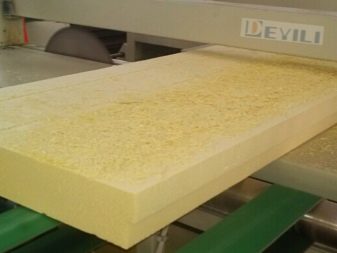
The main feature of extruded polystyrene (EPS) is its zero moisture and gas transmission. This modern and high-tech material does not allow water vapor to pass through its structure, like, for example, the well-known mineral wool. Over time, polystyrene does not fill with water and does not lose its thermal insulation characteristics. You will not have to face such problems even if the installation of the material was not entirely correct, and the dew point fell on the surface of the insulation.
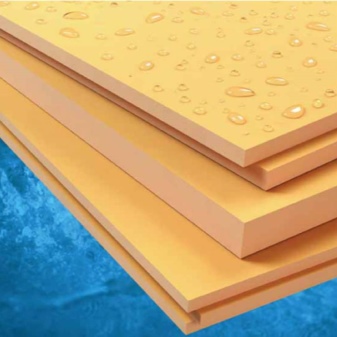
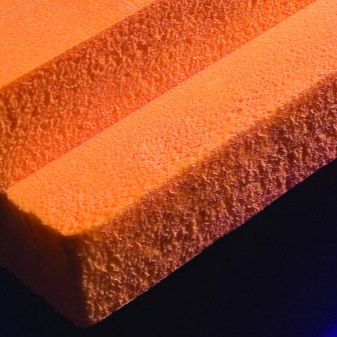
Difference from foam
Extruded polystyrene is the same plastic, characterized by a more homogeneous structure, in which there are many closed cells - their size is about 0.1–0.2 mm. As a result of mixing all the necessary components and passing them through the extruder, smooth, colorless or colored sheets are obtained. After complete drying, these materials can be used for their intended purpose.
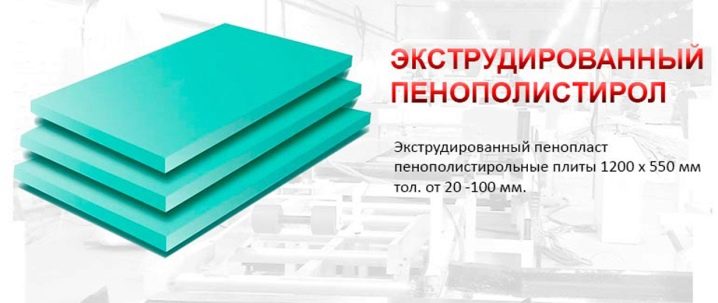
Extruded polystyrene foam has quite a lot in common with polystyrene foam. These products have a similar chemical composition, the main component of which is polystyrene.
As for the functional component, here EPPS and foam cannot be compared. Styrofoam does not pass through the extruder during production, and for expanded polystyrene this is a standard procedure. In this case, extrusion gives this material a completely different transformation, and therefore completely different performance characteristics.
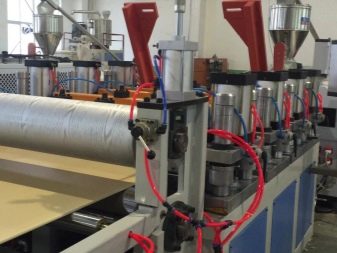
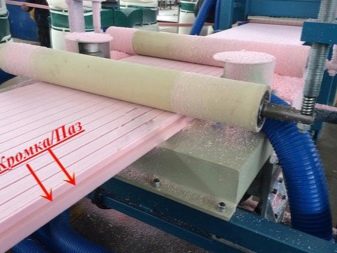
Advantages and disadvantages
Today, extruded polystyrene is known as a reliable and practical material you can trust. Its relevance is due to many positive qualities, which should be discussed in more detail.
- This material is waterproof. In case of unfavorable contact with liquid, the floors of expanded polystyrene are filled - no further movement of moisture occurs.
- Extruded polystyrene foam is characterized by a low level of thermal conductivity. If we compare it with other insulating coatings, we can conclude that the thermal conductivity coefficient of EPS is less or equal (the only exception to the rule is polyurethane foam).
- A characteristic feature of EPS is low vapor permeability. The coefficient of this parameter is considered to be the lowest among the insulating components.
- Expanded polystyrene is not subject to deformation even after a very long time.
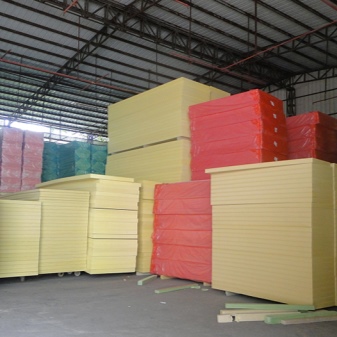
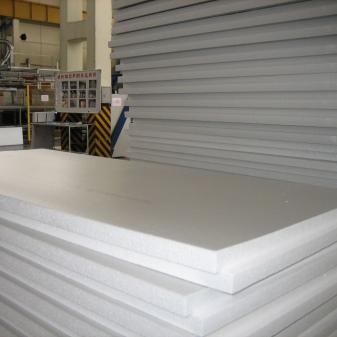
- This material is not afraid of temperature jumps. In such conditions, he does not lose his useful qualities and remains as practical / effective. Its working temperature ranges from -100 to +75 degrees.
- Installation, as well as dismantling of expanded polystyrene, is not difficult, and it does not take as much time as it seems to many.
- This material boasts a long service life, during which it does not deform and does not lose its qualities.
- During operation, extruded polystyrene foam is not subject to destruction.
- Extruded polystyrene foam is not afraid of inorganic solvents.
- It is very easy and simple to work with this material, as it is light in weight and low in thickness.
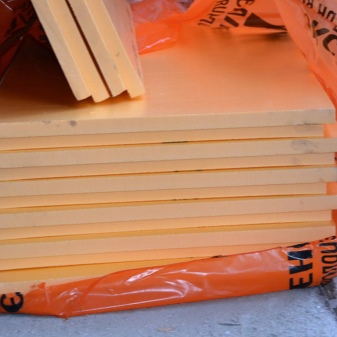
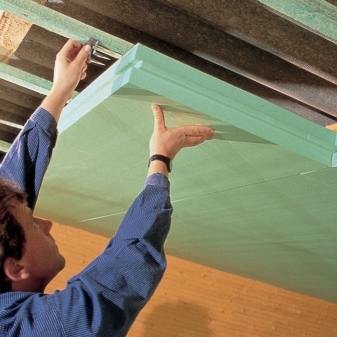
- Such material is relatively inexpensive. Many consumers can afford it. In this case, the price-quality ratio is good news.
- When installing EPS, you can do without the use of additional hydro and thermal insulation coatings, which will significantly save money.
- According to experts, EPPS is not dangerous to human health. Moreover, when working with it, the master will not experience allergic reactions.
- Such material is not afraid of low temperatures, therefore it is ideal for finding in the harsh and changeable Russian climate.
- The durability of extruded polystyrene foam is also confirmed by the fact that it is not subject to decay - not every building and finishing material can boast of this quality.
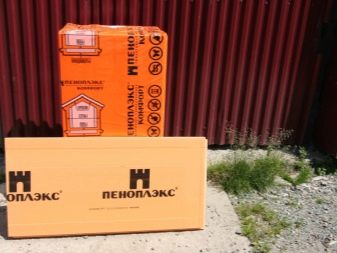
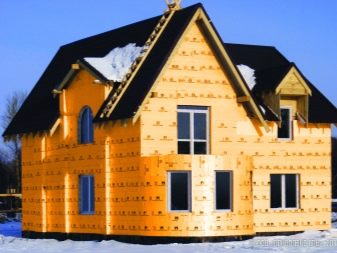
As you can see, EPS has a lot of advantages. That is why today it occupies one of the leading positions in the insulating materials market. However, such a practical and reliable coating has its own drawbacks, which you should also be aware of before purchasing it.
- This material is flammable.
- Being at temperatures above 75 degrees, polystyrene foam can emit harmful substances that are dangerous to human health.
- According to experts, this material is afraid of contact with infrared rays.
- Mice can start in EPSS, although many manufacturers deny this fact.
- When interacting with various solvents, this material can be destroyed.
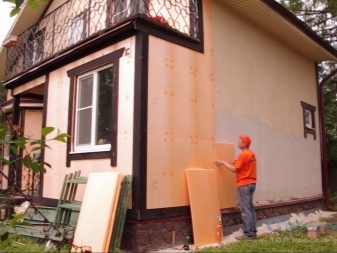
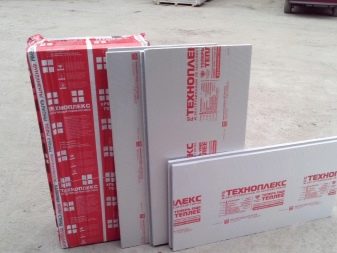
If the listed disadvantages do not scare you, then you can safely proceed to the acquisition of this modern material - it is used in many areas.
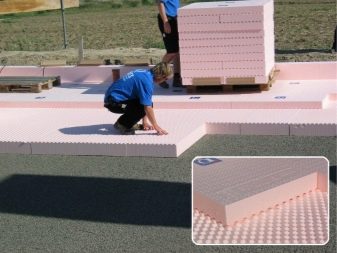
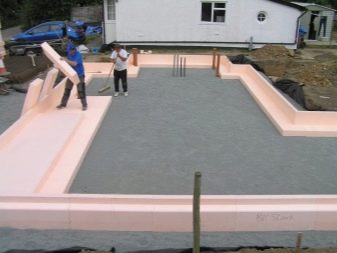
Properties and characteristics
Currently, extruded material is produced by many large and well-known manufacturers.Typically, the performance and properties of different products are almost the same. This also applies to their dimensional parameters.
- So, the thickness of expanded polystyrene plates most often ranges from 20 to 150 mm.
- The standard dimensions of expanded polystyrene plates are 600 x 1200 mm, 600 x 1250 mm, 600 x 2400 mm.
- Their level of thermal conductivity can range from 0.03 to 0.032 W / mS.
- With regard to the index of density in compression, then at 10% linear deformation, it is 150 x 1000 kPa.
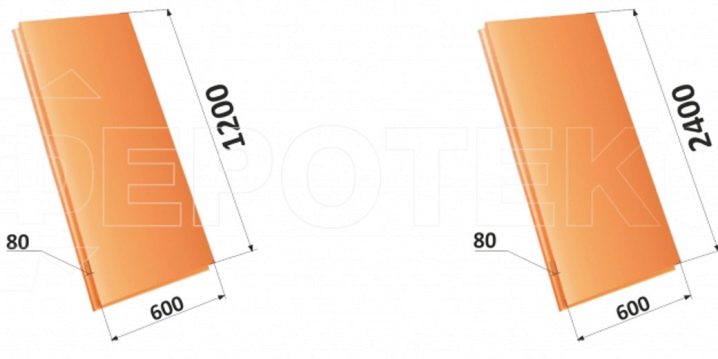
- The percentage of moisture absorption is usually 0.2–0.4%.
- Flammability class from G3 to G4.
- The level of vapor permeability is 0.013 Mg.
- Density - 26–45 kg / cu. m.
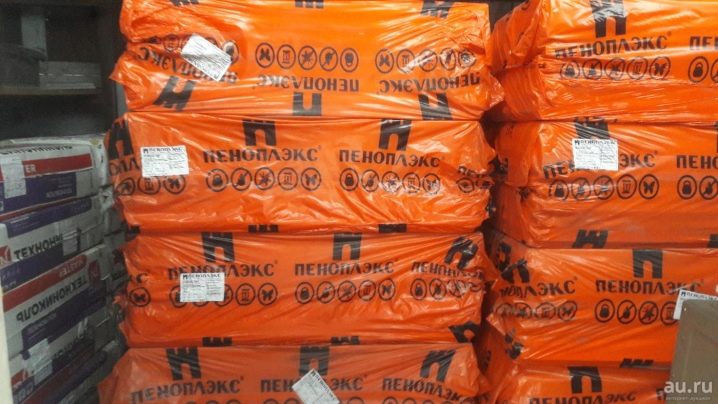
Manufacturers and sizes
Modern manufacturers produce extruded polystyrene foam with various technical characteristics. Currently, there are three leading brands, whose products are considered the most popular and widespread:
- Penoplex;
- Technoplex;
- Ursa.
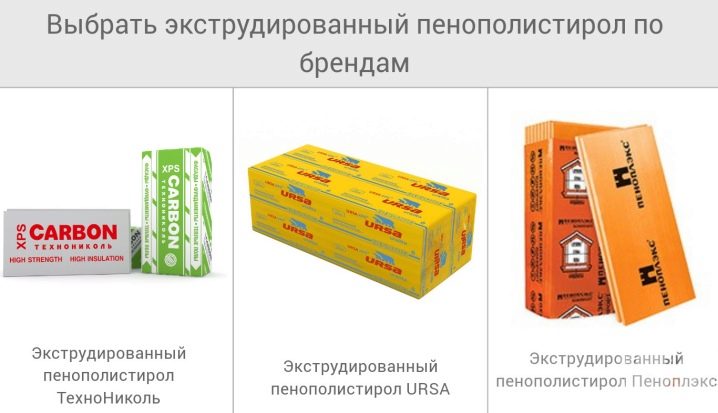
Let us consider in detail what characteristics and properties the EPS of these manufacturers have.
Expanded polystyrene "Penoplex" is a popular domestic product that is found in many stores and is in great demand. Such materials are used for both civil and industrial construction. Let's get acquainted with the main characteristics of polystyrene foam of this company.
- The thickness of EPS "Penopless" can be - 2, 3, 4, 5, 6, 7, 8, 10, 12, 15 cm.
- The dimensions of the sheet are - 60 x 120 cm, 60 x 240 cm.
- The level of thermal conductivity is 0.03-0.032 W / m C.
- Compressive strength is 0.2–0.5 MPa.
- The level of water absorption does not exceed 0.4%.
- The flammability class of the material is G4.
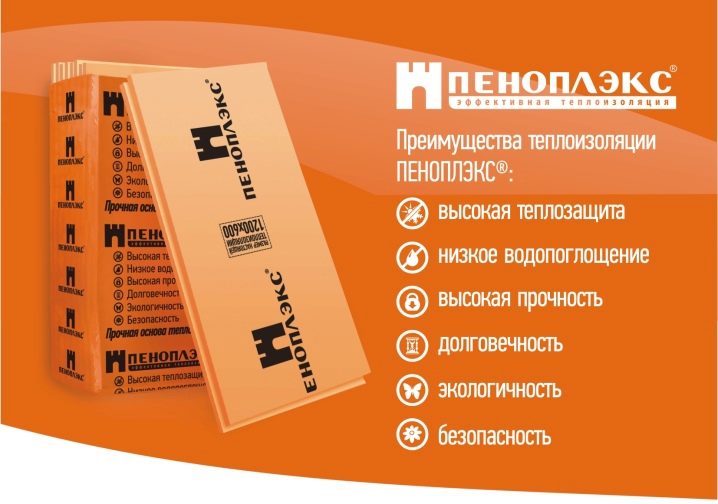
Ursa is a large international company with representative offices in Russia. At the moment, this manufacturer produces three types of extruded polystyrene foam. Ursa materials have the following technical characteristics.
- The thickness of the materials is 3, 4, 5, 6, 8 and 10 cm.
- The length and width of all EPS sheets is the same and is 60 x 125 cm (there are also other dimensions on sale, for example, 50 x 600 x 1250 mm).
- The level of thermal conductivity of EPSP sheets is - 0.032-0.034 W / m C.
- Compressive strength ranges from 0.25 to 0.5 MPa.
- The material absorbs moisture by 0.5%.
- Flammability class G4.
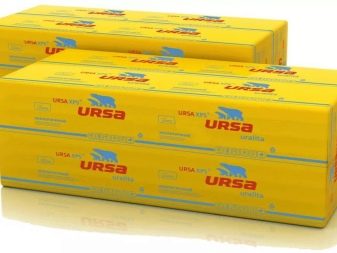
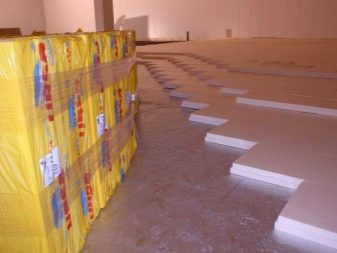
Technoplex produces expanded polystyrene sheets with the following parameters.
- Their thickness can be 3, 4, 5, 10 cm.
- All sheets have standard dimensions - 60 x 120 or 58 x 118 cm.
- They are characterized by a high coefficient of thermal conductivity.
- Materials from Technoplex absorb moisture worse by 0.2% than raw materials from Penoplex.
The products of these brands are in great demand in our country and comply with all GOST standards. High-quality expanded polystyrene of these companies is in demand due to its excellent performance, long service life and easy installation.
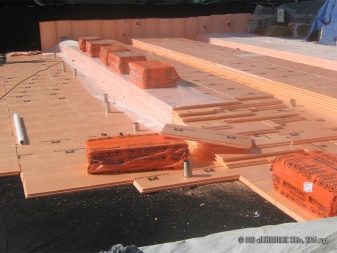
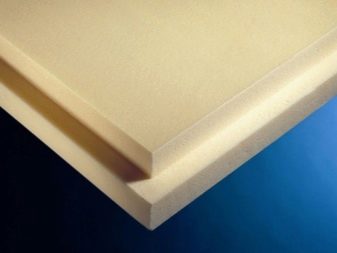
Of course, these are not all large manufacturers whose products are popular today. For example, today the products of KTpleks, Ecotherm, Onda LLC, TechnoNikol (a popular product - XPS) and many others are no less in demand.
If you want to buy really high-quality polystyrene foam, then you should contact a trusted brand store. Don't look for too cheap materials - EPS is already an affordable thermal insulator.
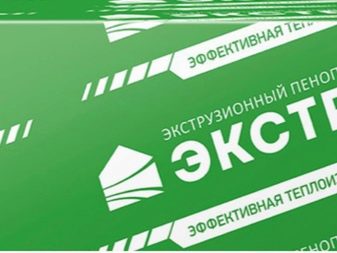

Where is it applied?
Extruded polystyrene foam is used in various fields due to its positive qualities and performance characteristics.
- This material is very useful for private construction. With its help, both internal and external insulation of the floors of houses is produced. In addition, they can insulate roofs, communication lines and even basements. Often this material is consulted in the course of waterproofing work.
- EPPS is a popular material in state industrial construction.It is ideal for high-quality thermal insulation of various buildings, underground rooms, as well as various trunk lines.
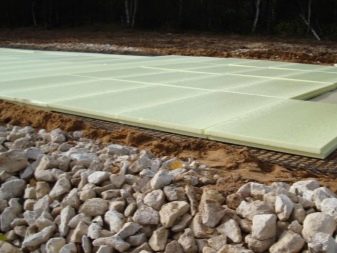
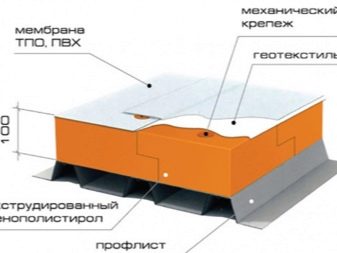
- Expanded polystyrene is also useful when laying highways or large runways.
- It is used by EPS for the production of refrigerators and refrigerators.
- Extruded polystyrene foam is a wonderful material that is often used in the construction of economic buildings. These include large vegetable stores, farms, greenhouses of various sizes, and greenhouses.
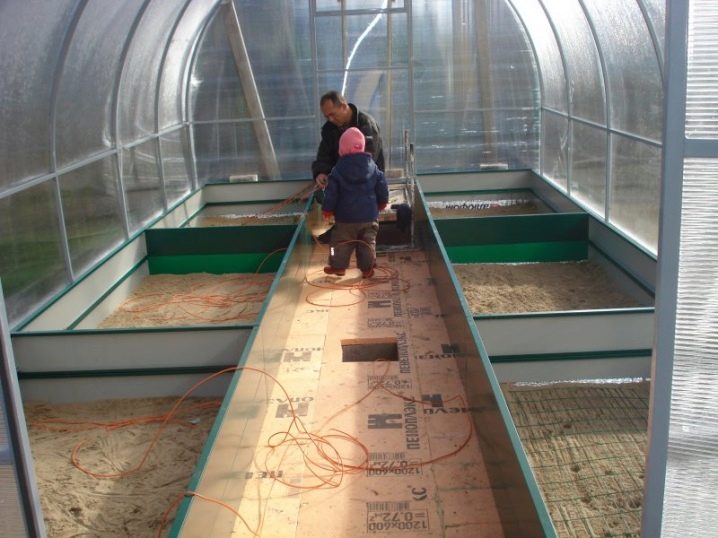
Whatever this popular material is used for, its main focus will remain the insulation of wall ceilings, foundations and roofs.
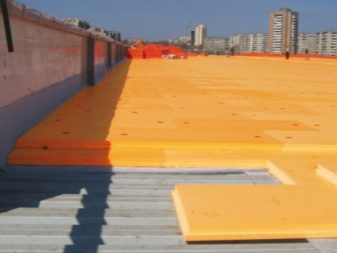
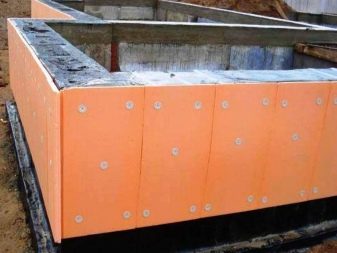
Insulation technology
Extruded polystyrene foam is very popular not only for its excellent performance, but also for its long service life, as well as easy assembly / disassembly. You can install it on various bases with your own hands, without resorting to teams of specialists.
The main thing is to adhere to a simple technology of work, and then the result will definitely not disappoint you!
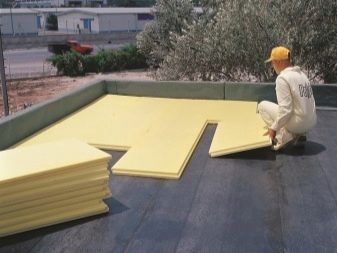
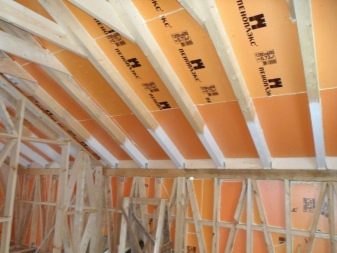
Paul
Many people choose floor insulation in the house with expanded polystyrene. The way it is laid largely depends on the material of the base, and on its type, and on the immediate requirements that are imposed on it.
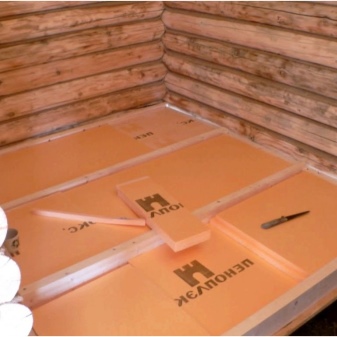
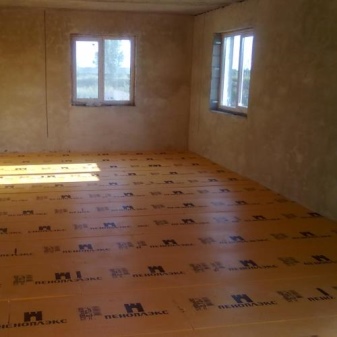
On the ground
EPPS is quite often laid on the ground floor located on the first floor, when it is planned to install laminate, parquet, ceramics or linoleum on top of such a base. Expanded polystyrene is perfect for the future arrangement of a spectacular self-leveling floor.
To insulate such a floor, you need to thoroughly prepare the base. It must be strong enough.
In addition, the floor should not shrink in the future. For this, the ground level must be 50-60 cm below the design level of the surface of the future floor covering. It should also be taken into account that the base must be absolutely dry and tamped down.
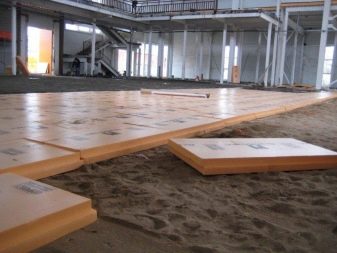
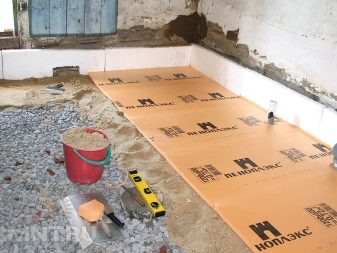
When the base is prepared, the first layer of dry gravel is laid on it (instead of gravel, you can take gravel). The height of such a coating should be approximately 30–40 cm. This layer also needs to be properly leveled and tamped.
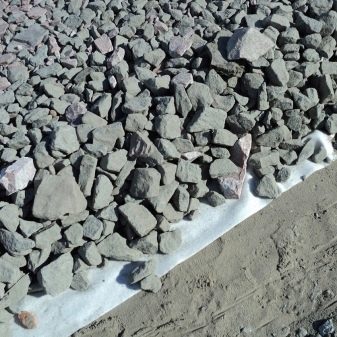
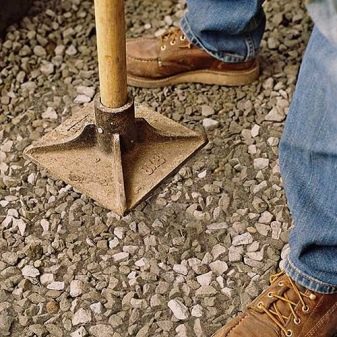
Then on the rubble you need to lay out a layer of granite screening or Mediterranean sand. The height of this layer should not exceed 10 cm. It must be leveled from above. To control the process, you should use the building level.
In rooms where there will be no high mechanical loads, polystyrene foam plates can be laid directly on a sand base. In this case, it is recommended to buy materials that have docking grooves at the edges. As for the joints of the plates, it is recommended to pre-glue them with a special metallized tape.
The thickness of EPS sheets can be from 3 to 10 cm - it all depends on the living conditions and the level of insulation of the foundation of the house.
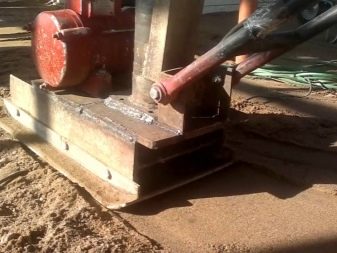
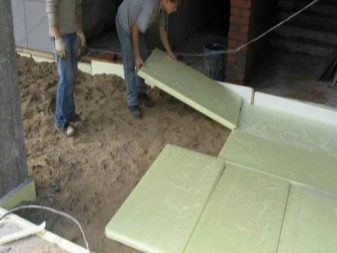
When you lay the insulating underlay on the floor, its surface should be covered with a waterproofing material. Next, you need to make a reinforced cement-sand screed along it. Always check the flatness of the surfaces. You can proceed to laying the floor covering only after the screed is completely dry.
If the laying of expanded polystyrene is planned in a room where the floor will be exposed to serious mechanical stress, then before installing the insulation boards, it is necessary to install a concrete screed (on a sand and gravel cushion and waterproofing). EPSP boards can be laid on the base only after it is completely dry.
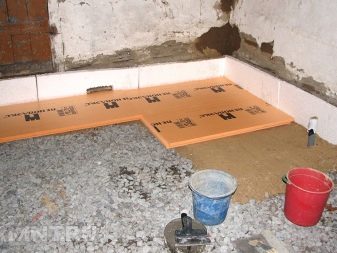
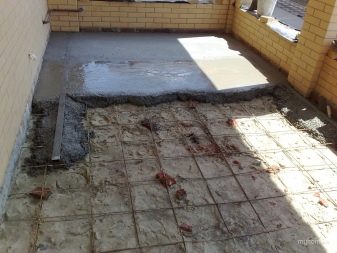
On concrete
If you are going to insulate a concrete floor, then you need to make sure that its surface is flat - without drops. Any crevices and cracks should also be removed.
If the concrete base is an overlap of a basement or basement, then the insulation is recommended to be laid on top of the waterproofing film.
Although expanded polystyrene is not afraid of dampness and moisture, these components can penetrate into the joints of the plates, so excess waterproofing in this case will definitely not be superfluous.
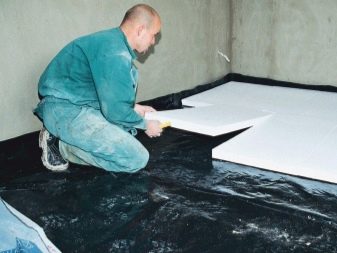
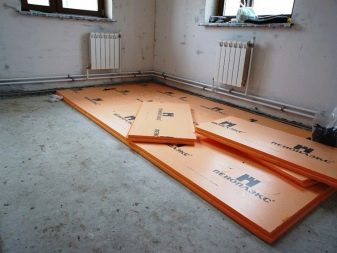
If there are irregularities on the concrete base, then first you need to get rid of them, and also fill up all the cracks and cracks. Make a leveling cement-sand screed. When the latter dries up, it is necessary to lay EPPS on it, and already on this layer - waterproofing. Insulation boards are recommended to be laid on a special adhesive designed for ceramic tiles. On top of the waterproofing, a screed is further made.
Insulation with expanded polystyrene can be used for floors in an apartment on a balcony or on a loggia. All work should be performed according to the same principle as above. However, it should be borne in mind that it is possible to start such a floor arrangement in an unglazed area only if the temperature there is at least 5 degrees.
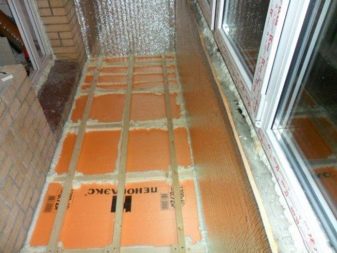
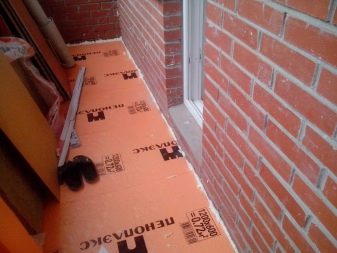
As for the glazed area, you can start work on it even if the temperature in this place is below 5 degrees. However, then it is necessary to additionally insulate the repaired area so that the screed dries to the end and it can be laid on it with expanded polystyrene plates.
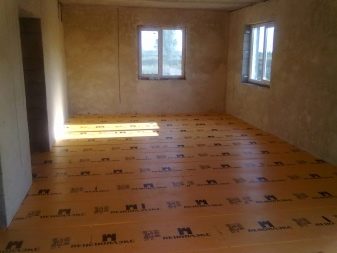
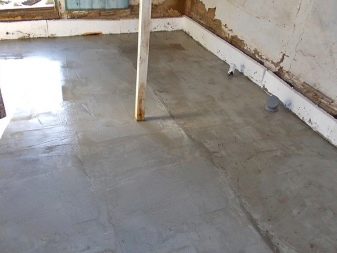
Roofs
High-quality thermal insulation is necessary not only for the floor, but also for the roof. In this case, it is also permissible to use extruded polystyrene foam. In this case, its slabs must be correctly laid out under the roofing material.
Consider what should be the order of arrangement of all the constituent elements (we look from the inside - out):
- first comes the decorative coating (the roof itself);
- then comes the inner crate, designed to support the insulation and ventilation material;
- vapor barrier film;
- insulation;
- waterproofing film;
- external lathing required for additional ventilation and installation of roofing;
- roof covering.
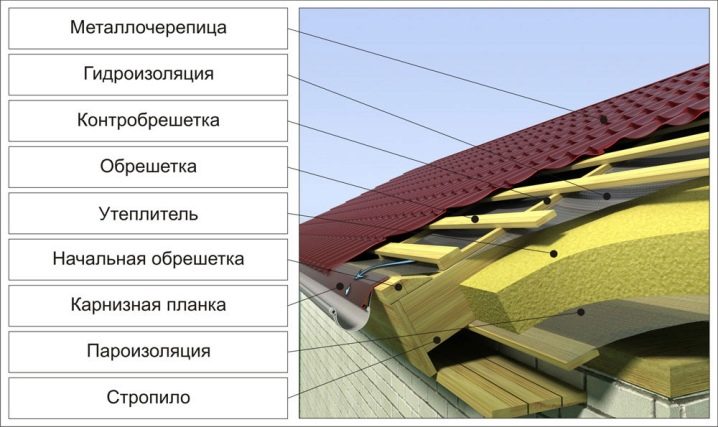
At the same time, many home craftsmen neglect the installation of steam and waterproofing films. This is a big mistake, since these components will protect not only the insulating layer from moisture and moisture, but also roof structures made of wood.
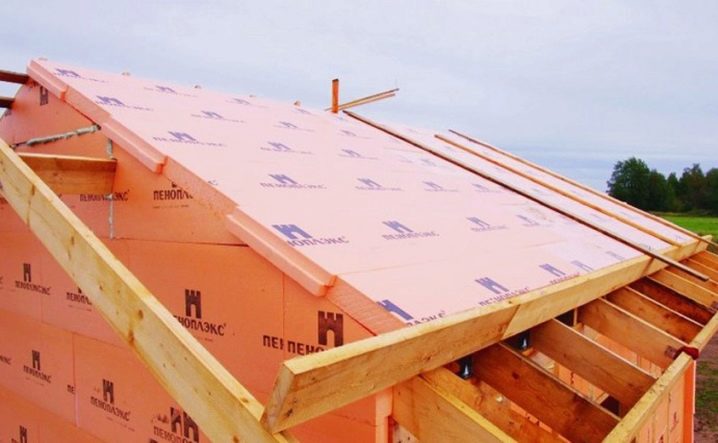
Also, EPS roof insulation can be done on the finished structure. Consider what you need to do for this:
- install waterproofing material on the rafter;
- then fix the insulation on special suspensions;
- cover the insulation with a vapor barrier;
- nail the grating to the rafters (this frame structure will hold all the insulation, and also play the role of a ventilation area);
- Finally, install the finishing material.
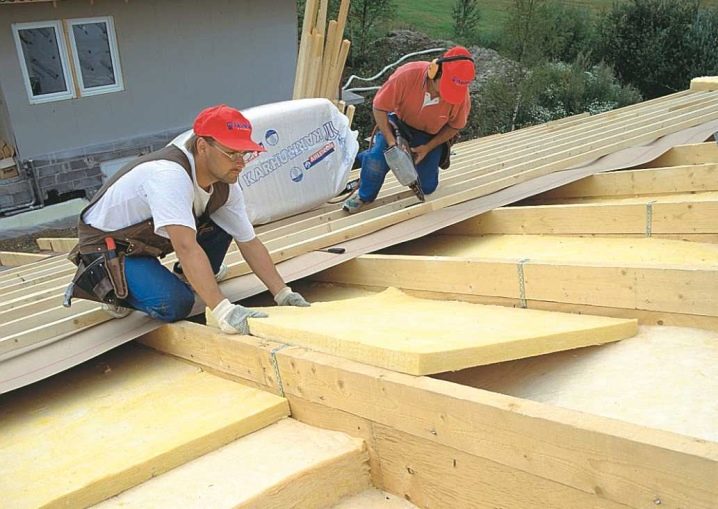
In this case, you need to take into account one drawback - when installing polystyrene foam on an already finished roof, you will hide a certain amount of usable area. In the event of leaks, such a design will have to be changed to a new one.
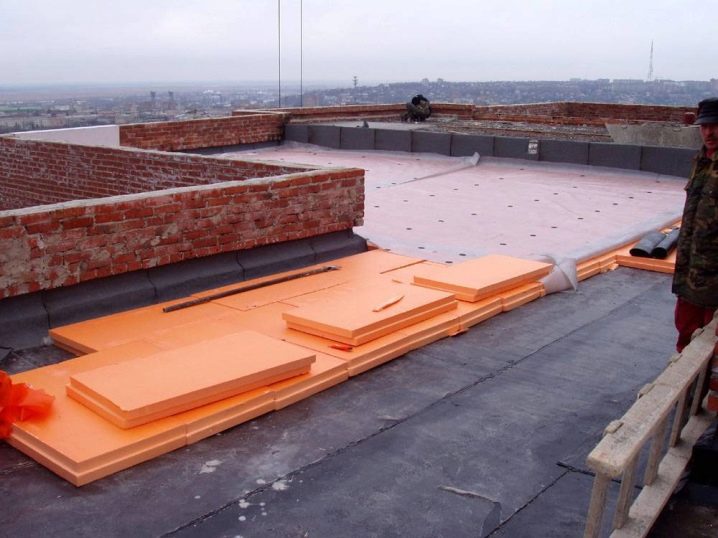
Of the foundation
With the help of expanded polystyrene, you can also insulate the foundation. To do this, you should also adhere to a certain technology. Let's get acquainted with all the necessary stages of such work.
- First you need to competently prepare the foundation. It is possible to insulate such structures both for those under construction and for finished buildings. Make sure that the foundation is completely excavated and free of dust, grease, construction waste and other defects.
- If there are remnants of the previous waterproofing on the foundation, then you also need to get rid of them.
- Keep in mind that such a base can be insulated both from the outside and from the inside, however, external insulation is considered more effective.
- Find the right styrofoam. For the foundation, it is recommended to buy materials with a density of 35 kg / cu. m. The flammability class in this case is not so important.
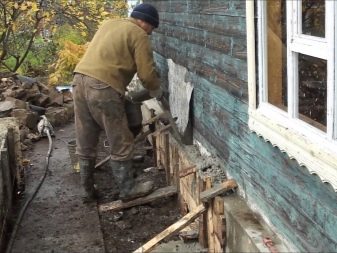
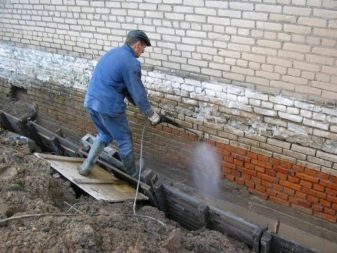
- Get your foundation waterproofed. Thus, you can prevent materials from getting wet during the appearance of groundwater.
- Waterproofing can be installed under the insulation in any way. The only exception is the isolation of the base with the help of a special bitumen filling - EPS in contact with solvents can be severely damaged and even destroyed.
- Next, you will need to attach polystyrene to the foundation (its underground component). At the same time, insulating plates are attached to a special glue designed specifically for expanded polystyrene.
- The adhesive mixture must be applied around the perimeter of the board and in its center in several strips. Then you need to wait about 1 minute and press the polystyrene foam to the base. Wait a couple of minutes and proceed to the installation of the next part.
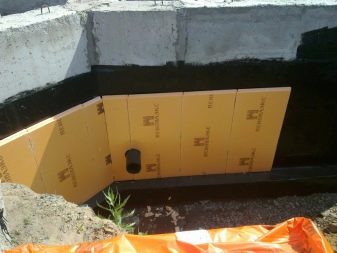
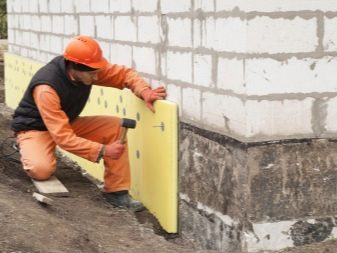
- It is recommended to fasten the plates using a level so that there are no distortions at the joints.
- If you need a thicker insulation, then polystyrene foam is allowed to be installed not in one, but in two layers. In this case, the plates must be glued in such a way that the second layer necessarily covers the joints remaining between the tiles of the first layer. If, after installation, the gaps remain on the material, they must be closed with ordinary polyurethane foam.
- Next, you need to protect the insulation itself. To protect expanded polystyrene from mechanical damage and attack by rodents, it is recommended to supplement this material from above with a reinforcing mesh or special shields. These components must be fastened along the perimeter of the foundation using dowel nails.
On top of the mesh, the foundation can be covered with a cement mixture with the addition of special waterproofing ingredients.
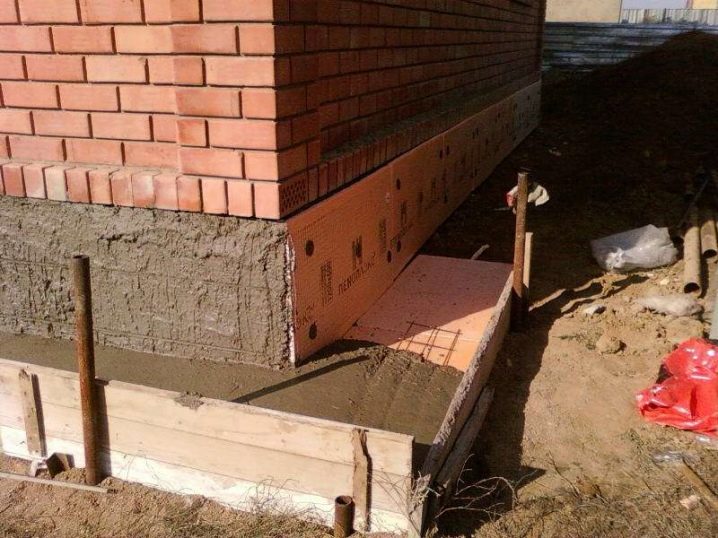
- If the house is located on damp ground, it needs to be provided with good drainage. It is installed around the entire perimeter of the foundation and taken out into the lowland or a special well.
- Next, you need to insulate the base. This part of the foundation also needs additional insulation. The previously prepared surface, protected from moisture and moisture penetration, is now ready for the installation of EPS materials. They should be attached to the same adhesive.
- After a couple of days, it is recommended to additionally fix the expanded polystyrene plates on the plinth with special fasteners (for this, dowel-nails with wide heads are suitable).
- After these works, you can proceed directly to soil insulation (this process is described above).
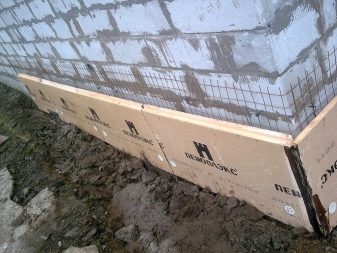
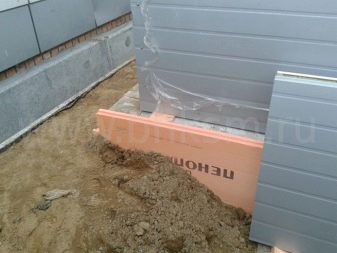
Walls inside
Insulation of walls with expanded polystyrene from the inside presupposes compliance with a certain technology. Let's consider what stages such work consists of.
- First you need to prepare the bases. It is necessary to thoroughly clean the surface of the floors. Be sure to remove the old coating, especially if it is paint and varnish materials. Otherwise, the solvents in their composition will destroy the structure of the insulation.
- Next, you need to level the surface of the walls. If the floors are made of bricks, then they need to be plastered, and if they are made of concrete, then you can do without plaster. For fine leveling of substrates, first apply an acrylic primer with a paint roller.
- After that, the layer will dry for 12-14 hours. Eliminate all defects on the walls with a putty. Then apply another layer of soil. This will complete the preparation of the wall slabs.
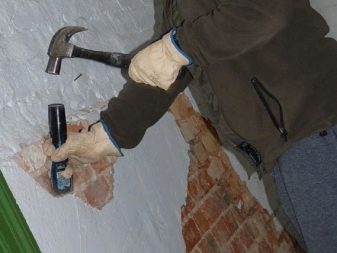
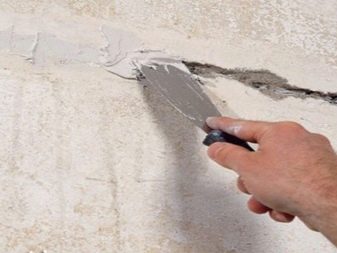
- Now you can start installing polystyrene foam plates. For this, you can use a special adhesive. It can be dry or ready-made.
- It is permissible to apply the glue with a brush, or you can also use a roller, passing it along the surface of the walls.
- In this case, it is recommended to start installing the plates from the bottom. To begin with, they need to be cut out to size - for this they can be applied to the still dry floors. It is better to cut styrofoam with a hot string or a toothed hacksaw.
- The first row of slabs should be installed over the entire wall. After that, you can start installing the next row.
In this case, the slabs must be displaced relative to the lower elements in such a way that the joint between the first-row sheets falls on the middle part of the upper slab.
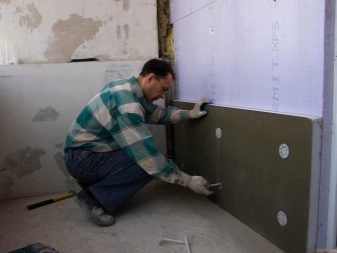
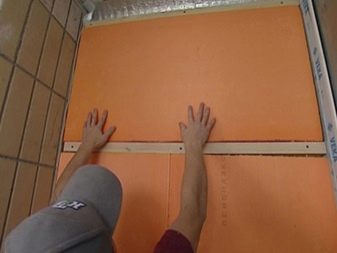
- Let the adhesive dry thoroughly. This can take 34–42 hours.
- It is recommended to additionally fix the installed insulation with dowels. In this case, the walls must be drilled directly through the EPS. Then you need to drive dowels into the resulting holes. The thermal insulation material should be attached with self-tapping screws. Large sheets can be installed in 6 locations.
- Now you should proceed to the sealing of the seams. If their dimensions exceed 30 mm, then the remaining scraps of expanded polystyrene can be glued into them.
- At the end of all work, the joints must be treated with polyurethane foam. Make sure that it does not contain toluene - this component corrodes plastic.
Excess mortar must be quickly removed with a knife, and then the seams must be treated with glue solution.
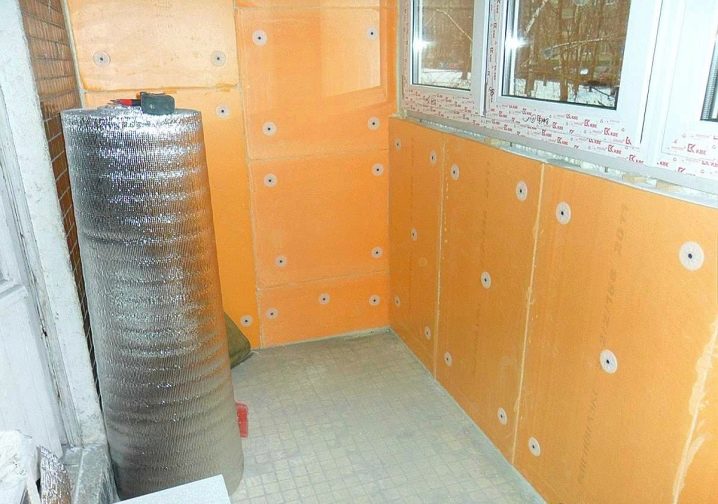
- Now you need to apply a reinforcing layer (for example, a fiberglass mesh).
- Place on top protective coatings, as well as vapor and waterproofing.
- Finally, cover the walls with a finishing coat such as plaster.
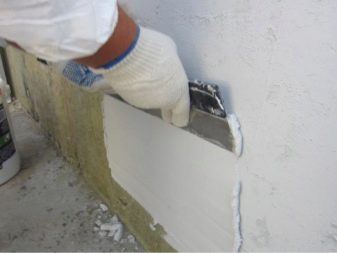
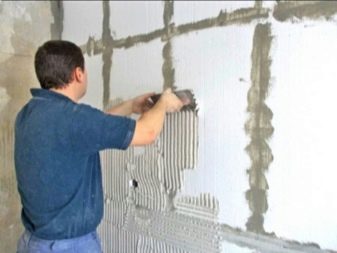
Facade
Many people turn to EPS insulation for house facades. This work should be done as follows.
- First, the outside walls are scrupulously cleaned of all excess, as well as old finishing materials, especially if it is paint.
- If the overlaps have irregularities, then you must definitely get rid of them. This also applies to various damages, such as cracks or crevices.
- Now you need to spread glue on the polystyrene boards (no need to apply too thick a layer), and then these parts must be pressed tightly to the bases and additionally attached with dowels.
- Attach EPS boards to all façade surfaces.
- After that, the sheathed bases need to be properly sanded.
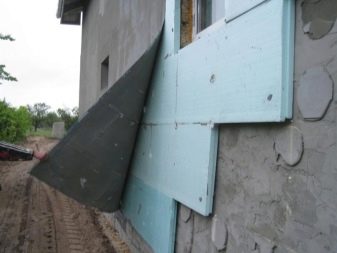
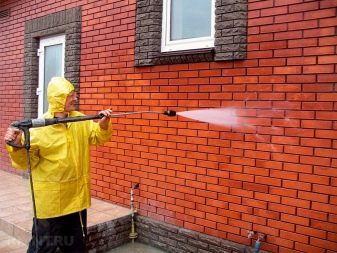
- Install a reinforcing mesh over the entire area of the installed insulation. Immerse it in the sticky solution.
- Next, be sure to wait until the surface covered with plaster is completely dry. Until then, no work can be started.
- After complete drying, the base must be covered with a high-quality primer.
- Only now is it permissible to go directly to the decorative design of the facade. For such bases, it is recommended to purchase only high-quality and high-strength coatings that are not afraid of temperature changes and precipitation.
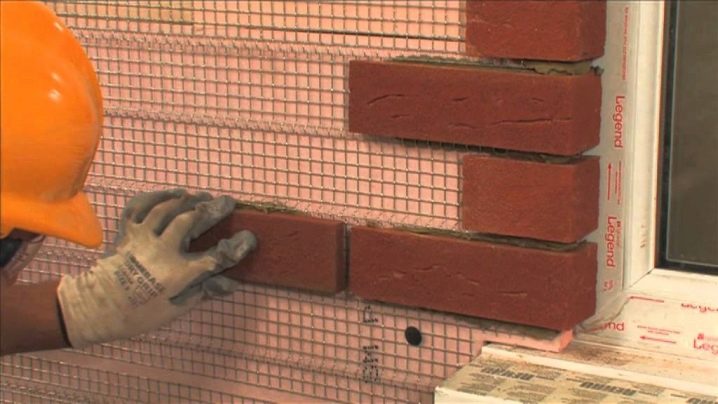
It is recommended to insulate the facade only in the warm season. During such periods, the humidity of the air is significantly reduced, therefore, adhesive and cement compositions adhere much better, and dry out very quickly.
For an overview of some insulation (foam, extruded polystyrene foam and PIR), see the following video.
The comment was sent successfully.