Where is ecowool used and what are its benefits?
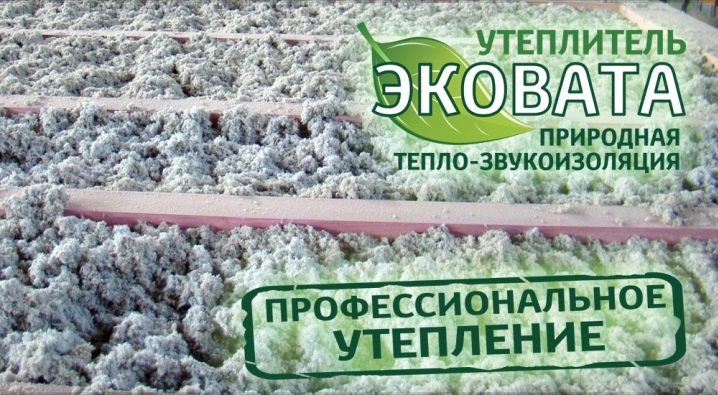
The use of each insulation material has its own characteristics and nuances. This fully applies to ecological cotton wool. You need to understand all the points in advance - before starting the installation work and even before choosing a specific option.
Origin and manufacturers
The thermal qualities of cellulose were familiar to people back in the century before last. It was then that the technology of thermal insulation based on recycled paper was patented. But such trends reached the post-Soviet space relatively recently, only in the 1990s. The fine fraction of cellulose fibers is crushed and foamed in production, but this does not end there. The mass must be treated with antiseptic and fire retardant compounds that suppress rotting and inflammation and prevent the material from growing mold.


The ecological purity of the material is not disturbed by special processing - this is a product that is produced only with natural ingredients. Flame suppression is provided by borax, which occupies up to 12% of the mass. To prevent ecowool from rotting, it is required to use up to 7% boric acid. In Russia, there are now about a dozen companies producing ecological cotton wool. The main positions in the market are occupied by LLC "Ekovata", "Urallesprom", "Promekovata", "Vtorma-Baikal", "Equator" and some others.
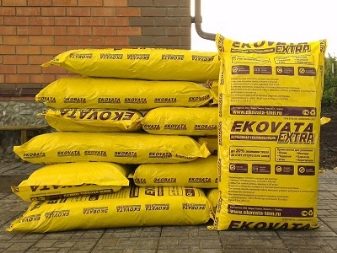

Properties and characteristics
The thermal conductivity of ecological wool is the most important indicator for any insulation, it ranges from 0.032 to 0.041 W / (m · ° С). The density of various samples ranges from 30 to 75 kg per 1 cubic meter. m. Depending on the technological features and other points, ecological wool belongs to groups of substances with low, moderate or normal flammability. In 60 minutes, 0.3 mg of water vapor can pass through a meter of cotton wool. Speaking about the technical characteristics, it is impossible not to mention that the cotton layer will be able to hold up to 1/5 of the water without losing its basic qualities.
Strict adherence to technological standards avoids shrinkage. The properties of the insulation help to install it very quickly, including in hard-to-reach areas and on geometrically sophisticated surfaces. During the repair and restoration of various structures, they can be insulated without preliminary dismantling. Moreover, cotton wool blocks can become a seal that corrects structural defects.
Manufacturers' recommendations point out that such a solution is optimal for old buildings and log cabins.


Advantages and disadvantages
The substance is fed into the deep part of the structure through a flexible hose under pressure, cellulose fibers fill all cavities and crevices by 100%, excluding the formation of the smallest seams and crevice areas. This is much more practical than insulation with plates or rolls, when the seams instantly spoil the overall picture.
In consumer reviews, it is noted that ecowool does not allow water to condense from the air circulating through the pores. Glass fibers and stone insulation can accumulate moisture, but the cellulose capillaries completely let it pass through themselves, no matter how much moisture there is.
Since ecological wool significantly simplifies the formation of the "pie", you can do without vapor barrier layers.

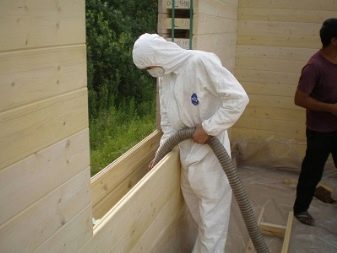
A fundamental rejection of harmful and volatile substances allows you not to fear for your health.Even if the house is completely engulfed in fire, ecological cotton wool will not release poisonous gas. Moreover, it will not burn itself and become an obstacle in the path of the flame. This does not mean that the material has only advantages, it also has disadvantages:
- it will not be possible to mount an insulation structure without complex machines;
- ecowool does not tolerate mechanical loads and fits only in the gaps of the load-bearing parts of the structure;
- moisture resistance is insufficient for many practical situations.
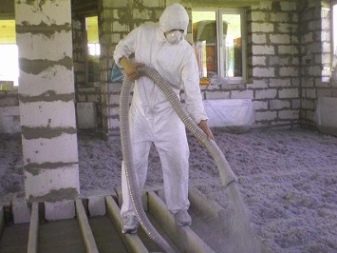

Composition and structure
Insulation can be confused externally with mineral wool. But there is an important difference - the flowability of the product. After all, the fibers do not have rigid mechanical bonds, they are held exclusively by the cohesion of particles at the micro level and by the forces of an electric field. It is recommended to find out in advance what the quality of the used waste is - the higher it is, the better the product obtained. The volumetric concentration of boric acid is from 7 to 10%, the same amount is added sodium tetraborate.


Application methods
You can use ecological cotton wool:
- applied by hand;
- blow out in a mechanized dry way;
- spray on the surface after wetting.
The manual method involves loosening with handy tools in any suitable container. Laying on the insulated surfaces is done in a uniform layer. If you need to insulate a cavity in the wall, then you will have to fill in ecological cotton wool there. The minimum density of laying in the wall is from 65 kg per 1 cubic meter. m, and inside the floors, this figure is limited to 40 kg per 1 cubic meter. m.
You should not think that it is so easy to put ecowool with your own hands. The work will require neatness, care and a significant investment of time. Such an installation is justified financially only with a small amount of work.
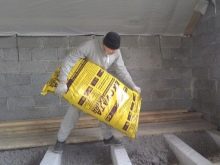


If it is required to insulate large building structures, it is advisable to use complex equipment. The dry mechanized method involves the attraction of blowing machines, in the bunkers of which the insulation is loosened, and then supplied in the air flow to the desired place. This technique has proven itself well in relation to:
- interfloor ceilings;
- floors of attics;
- basement gaps.


It doesn't matter if the building is being built from scratch or if the building has been in operation for some time. Blowing is carried out with a certain margin, because even loosening gives only a limited time effect. Gradually, the cotton wool will become denser, its specific gravity will increase by 5 kg per 1 cubic meter. m. Then, if no preliminary reserve has been made, the thickness of the thermal barrier will be reduced. How it will end for the residents of the house hardly needs to be explained.
Dry blowing is equally well developed technologically for surfaces directed in a horizontal or vertical plane, as well as for inclined structures. You can apply a similar method along the pediment and along the pitched roof, for thermal protection of walls covered with a layer of gypsum board. Preparation for the introduction of ecological wool involves the creation of holes in the film materials, and the flow of the substance must be fed into these holes.
The wet method is released only by feeding cotton wool mixed with water (sometimes also with glue). At the same time, completely different equipment is needed, which is not suitable for dry processing (and vice versa).



It is possible to simplify the work and not turn to specialists in some cases if you use a garden vacuum cleaner. Preparation begins with whipping cotton wool with a construction mixer - any container of the required size is suitable for this. Filling is carried out somewhere up to half in height, and you need to turn off the mixer when the material does not rise to its outer edge. Using a garden vacuum cleaner can save you money, but you will need to bring in an assistant. In addition, the vacuum cleaner will have to be modified, in its standard form it is not entirely suitable.
Important: this method only allows dry processing. If you need wet thermal insulation, you still have to call professional installers with special machines. It is undesirable to take a garden vacuum cleaner with an internal chopper. For work, you will need a flexible corrugated hose, the sleeve length is from 7 to 10 m, and the suitable diameter is 6-7 cm.
When selecting a hose, they are guided by the outlet pipe of the vacuum cleaner, on which the sleeve should sit as tightly as possible.


A waste collection bag is useless in this case. Instead, a corrugation is put on the pipe. To facilitate the removal of the bag, the destruction of the teeth holding it with pliers helps. It is recommended to use scotch tape or insulating tape to secure the corrugation. In either case, you will have to check whether air will leak out through the joint.
Floor insulation begins with whipping ecowool in a barrel with high walls. It is not necessary to increase the volume of the material very much. The pipe nozzle is immersed in insulation, while someone at this time holds the tip of the hose to the floor. This technique allows you to reduce the emission of dust to the outside. Better to cover the floor with a boardwalk and reserve a free board for each of the cells, then you will have to deal with dust less.
Walls insulated with ecowool are initially sewn up with oriented slabs. At 0.1 m from the ceiling, holes are prepared corresponding to the diameter of the corrugated pipe. The hose inserted there must not be brought to the floor by about 30 cm. When saturating the walls with cotton, carefully monitor the sound of the vacuum cleaner. As soon as the suction tone is changed, the hose must be immediately raised another 30 cm (several holes will increase the accuracy of the work).


Application
Thermal insulation of the wall of a wooden house with ecological cotton wool is attractive because it does not impair the sanitary, ecological properties of wood. In this case, 1.5 cm of cotton wool reduces the intensity of the incoming sound by 9 dB. This material dampens extraneous noise so well that it began to be used even in airport buildings and recording studios. Dry installation of wadded insulation requires wearing a special insulating suit and respirator. If ecowool is applied wet, such problems will not arise.
The wet technique requires harsh conditions:
- air temperature at least 15 degrees;
- drying time - 48-72 hours;
- in unfavorable situations, drying is delayed.


We have to reckon with the fact that cellulose thermal protection is less rigid than expanded polystyrene, and it can only be mounted in a frame. It is inappropriate to insulate the room with ecological cotton wool next to sources of open fire or heating surfaces. It is not allowed to insulate stoves, fireplaces, sections of the ceiling and roof directly in contact with the chimney with it. In such places, heating can cause the insulator to slowly glow. When insulating an attic roof, it is recommended to first saturate all cavities with an insulating material, and only then sew up the frame.
Doing the reverse can save money, but not being able to directly observe the results can play a trick on homeowners. A waterproofing layer is placed under the metal roof up to the cotton wool. No more than 35 kg per 1 cubic meter can be blown into the roofing cake. m. The minimum set of overalls for those who cannot use a full-fledged protective suit - a respirator and rubber gloves.
When filling the facade from the inside or outside with ecological wool, you will need to prepare a hole for a hose with a diameter of 8 cm.


Thermal insulation of the floor does not present any particular problems technologically. Installers can use any of the standard methods, but mostly dry. All horizontal planes should have an insulating layer of ecowool from 150 to 200 mm - this is quite enough in terms of technical characteristics. Waterproofing is not required when forming a ceiling heat shield.When the lining of the ceiling from the bottom is made with boards with a small gap, parchment paper is pre-laid to prevent the cotton wool from shedding in the house.
Based on operating experience, ecological wool is suitable for insulating walls built from:
- concrete slabs;
- bricks;
- wooden beam;
- stone blocks of industrial production.


It is not difficult to calculate the consumption per 1 m2, if you take into account a few points. The weight of one package ranges from 10 to 20 kg, its volume is 0.8-0.15 cubic meters. m. Therefore, the specific gravity varies from 90 to 190 kg per 1 cubic meter. m. The packing density is determined by:
- quality (category) of ecological wool;
- by the method of obtaining it;
- the amount of added additives.
The denser material is characterized by increased thermal conductivity. But it is also not recommended to reduce the density to a minimum, because this reduces the resistance to fire and makes the shrinkage of the laid layer stronger. Horizontal insulation with ecological wool is made in the amount of 30-45 kg per 1 cubic meter. m. Inclined sections of walls and roofs are insulated by adding 45-55 kg for the same volume. Most of the consumption is on the walls, 55-70 kg are required there.

Continuing the calculation, you should pay attention to the required layer thickness. The minimum indicator is the calculated value of the thermal insulation resistance for a particular construction area. On the other hand, you also have to take into account the thickness of each beam, rafter assembly or tightening. It will be difficult to change arbitrarily the gap separating the rafters from each other, and even then not always. Conclusion - the second parameter is much more important than the first digit.
Suppose you need to fill in ecowool in the amount of 45 kg per 1 cubic meter. m. We will accept the required thickness of thermal protection in 10 cm, and the density - 50 kg per 1 cubic meter. m with a layer thickness of 12.5 cm, the density of the insulation backfill is 60 kg per 1 cubic meter. m. When calculating, it should be remembered that the layers of the walls are not limited to insulation. Also take into account the width of the boards used for puffs and rafters.
The external fencing of the conventional insulation layer is made of fibrous plates with a thickness of 0.3 cm.

Multiplying the ceiling area (let 70 m2) by the selected thickness (16 cm), we get the volume of the insulated space in 11.2 cubic meters. m. Since the density is taken 50 kg per 1 cubic meter. m, the weight of the insulation will be 560 kg. With the weight of one bag of 15 kg, 38 bags will need to be used (for even counting). Similar schemes are used to calculate the need for inclined walls and floors, for vertical structures. Summing up all the indicators obtained, you can get the final figure. There is no need to correct it, because all the main nuances have already been taken into account.
When installing from the outside, the insulating layer must be covered with a new cladding. The installation of the frame, on which the facing material is attached, helps to solve this problem. Dry heat protection with cellulose begins with fastening the bar in the longitudinal direction, the cross-section of each bar is selected for the future insulation layer. Then they stretch a film that protects against wind and other atmospheric influences. The film is slightly notched, the insulation itself is blown into the intervals obtained.



Immediately after this, it is required to glue the membrane and quickly proceed with the installation of the facing material. The wet option implies saturation of ecological wool with water and spraying it into the crate cells. Experts recommend this approach for thermal protection of a log house and a brick. Important: you should not create a layer less than 100 mm. Even if, according to calculations, such a figure is obtained, it is better to play it safe. To create a crate and process the original surface will help:
- electric drill;
- scraper with an electric motor;
- screwdriver.



All other things being equal, a metal frame for ecowool is better than a wooden one. Yes, it comes out more expensive and technically more difficult for builders. Ultimately, however, an increased wall cake life is achieved. Wet insulation of the facade has no significant limitations.The usual cleaning from traces of dust, dirt and grease is enough.
Be sure to remove everything that can interfere with the surface being trimmed - an air conditioner, a drainpipe, lighting fixtures. When self-warming the facade in a mechanized way, it is impractical to buy the necessary equipment. It will be much easier and more profitable to rent it from a service company. The step of the lathing is exactly 60 cm.
Facades with complex surface relief are more efficiently insulated if a small amount of glue and lignin is added to the water.


How to do it yourself?
Do-it-yourself thermal insulation with the help of ecowool does not present any particular difficulties for any skillful people. You should not be afraid of serious problems - almost always the disadvantages of ecological wool are associated either with its improper use, or with a deviation from the standard technology when blowing. It is required to strictly follow the basic rule for any insulating cake: the permeability of materials to water vapor when moving outward should increase.
A professional team will take for 1 cubic meter. m of space to be insulated at least 500 rubles, and often this rate is even higher.


When working, you may not even need any complex apparatus. Scattering of cellulose in the floor is done with brooms, shovels and scoops. In addition, self-warming of a house with ecowool has other advantages:
- there is no need to wait until the brigade is freed from other orders until it receives the necessary equipment;
- all work is done at a convenient time;
- many other finishing and repair works can be carried out at the same time;
- the house will be much cleaner (even the most accurate installers, moving in different directions, cannot help but litter);
- and the mood, self-esteem also rises.

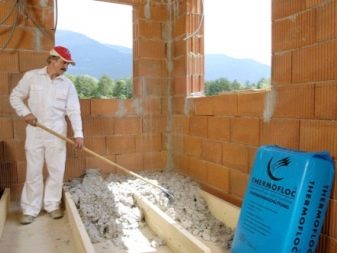
There is also a limitation: only mechanized filling of insulation is allowed in the walls and ceilings. No amount of manual effort will make it possible to achieve the required quality. You cannot put concrete logs on the floor, this material is too cold in this case. The height of all lags should be at least 0.12 m. Conclusion - you need to buy or do it yourself a bar with a section of 120x100.
The attached parts (with a pitch of 0.7 - 0.8 m) are supposed to be treated with impregnation and varnish. After all, harmful insects do not like cotton wool, but they simply adore wood. Instead of blowing, ecowool is poured out of the bag. At the same time, they carefully monitor that it is evenly distributed over the cells, which should be filled even with excess. The reason is simple - gradually the cotton wool will settle by about 40 mm.
The homogeneity of the mixture is achieved in various ways. Some amateur builders operate with a wooden rod, breaking pieces to dust. But it will be much faster to complete this work with a drill with a special attachment for an electric drill - then you need to spend only a few minutes. When the mixture is homogeneous, it is leveled over the entire area of the cell and covered with boards.

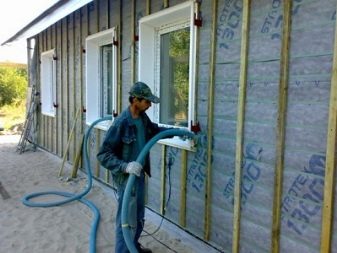
Above the logs, the ecowool should be raised by 40-50 mm, because it is by this amount that it will gradually settle.
Insulating the floor without taking into account this consideration will lead to the formation of voids in which the wind will appear. To insulate from 15 to 18 sq. m, no more than 30 kg of ecological wool will be required. You can save as much as possible if you make ecowool with your own hands. This requires a device that includes:
- an electric motor that develops 3000 revolutions per second and consumes at least 3 kW;
- blunt steel knife (it will have to grind the raw material);


- shaft (increasing the frequency of the knife action);
- capacity (200 liters will be enough for household purposes);
- belt transmission.

An ordinary steel barrel is useful as a container, and the metal recommended for a knife has a thickness of 0.4 cm. After assembling the device, you need to test it several times, making changes if necessary, until the cotton wool is no longer thrown out of the barrel.Usually the problem is solved by adding a cover and welding a "skirt" on the knife about 50 mm from the blade. Direct use of ecowool, both factory-made and self-made, is possible using paint mixers 0.6 m long and 10 cm in diameter (when starting the drill at the highest speed).

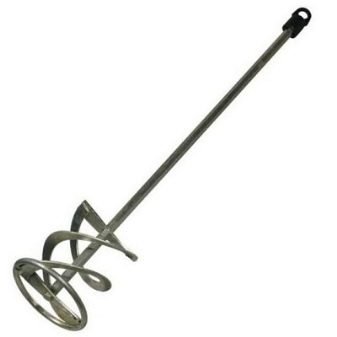
Such an improvised device allows you to fall asleep 2.5 cubic meters into the walls in 180 minutes. m of insulation. There is no point in waging an intense struggle with noise and vibration, it is better to endure them. Mounting the bearings and securing the drill to the holder drastically reduces productivity and efficiency. You can replace a garden vacuum cleaner using a design made of:
- triple plastic pipe number 110;
- a drill attached to the board;
- perforated tape suspension for gypsum board;
- a bell that helps to serve large portions at once.



You will get not only high labor productivity, but also a minimum amount of dust. At the same time, it is possible to save significant funds. The disadvantage is the inability to fully insulate verticals and surfaces that have a slope. In such cases, garden vacuum cleaners and branded equipment perform much better. Even when buying units and corrugations, independent work is more profitable than inviting a team.
When insulating interfloor ceilings, it is quite enough to put 100-150 mm of ecowool. Only in the regions of the Far North is it worth increasing the thickness to 200 mm. On the floors of non-residential attics and attics, 300-400 mm of insulation is consumed. The reason is simple - the rise of warm air in the room upwards makes heat leakage especially dangerous here.
Since no state standard has been developed for ecological wool, each manufacturer has its own approach. Therefore, before buying, you should delve into the nuances of the chemical composition and technology. Other unscrupulous suppliers add components hazardous to health. When choosing, it is worth shaking the workpiece, and if something spills out of it, this is a very bad sign. Experienced craftsmen carefully check whether the original packaging has been broken.
High-quality insulation is always gray, and yellowing or the appearance of light tones indicates the use of unusable raw materials in the production.

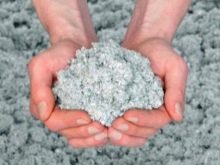

It is undesirable to buy ecowool, the fire-retardant properties of which are provided by a mixture of boric acid with ammonium sulfate. Such a substance smells very bad and loses its characteristics in a short time. It is recommended to give preference to the products of well-known companies, and when buying an unfamiliar product, check it three times carefully. Responsible owners always control the choice and methods of work, including when hiring a team. The smallest depth of the cells for laying the insulation is determined by the thickness of the thermal protection layer.
You can save money if you equip a subfloor at the required depth, it will not allow the powder to seep or penetrate further. Some builders whip the mixture in the same bag in which it was packed in production.
Regardless of the choice of capacity, one must not forget that fluffed ecowool doubles or triples the volume. The readiness of the material is judged by squeezing it in the palm of your hand. The fully cooked mixture will be held in a tight heap.
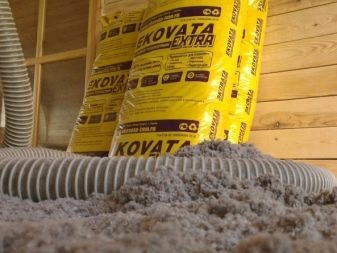

Lignin can be activated by spraying cotton wool with a spray bottle. Then the fibers will stick together and form a crust. It will be more difficult for water to penetrate through it. The finally dried insulation is covered with a water-impermeable film. In addition to the manual method of insulation, it is possible to fill the floor with the help of mechanisms. For this, a flooring is required, which makes the space under the partitions closed.
An externally inconspicuous section of the board is chosen and a hole for the hose is made there. Then the hose itself is inserted into the holes, brought to the point where it rests against the wall, and pushed back half a meter. The gap separating the pipe from the floor is sealed with improvised means. The capacity of the blower is filled with cellulose. After specifying the mode, turn on the device.


Having filled the gap from the pipe to the wall, the hose is pulled out 50 cm and the mass continues to be fed down. The last stage of work begins when the hose can only be inserted into the gap by 1 cm. Having finished blowing, the hole is immediately sealed. Attention: when using homemade devices, it is better to work with small portions of ecowool. Otherwise, the apparatus sometimes cannot move the mass.
The ecowool ceiling is predominantly insulated from the side of attics. Since the insulation is lightweight, this technique is acceptable even for a ceiling hemmed with thin boards. If the material is applied from below, it must be blown out through the technological holes in the inner lining. Dust emission can be reduced by covering the layer with polyethylene. Having laid the ecological wool by hand on top, it is rammed a little.


When in the cold season the average temperature in the attic is 23 degrees, you need to put 150-200 mm of ecowool. Cold attics are insulated with a layer of 250 mm. It is necessary to use a mixture of water and glue if the ceiling has insufficient adhesion. For your information: wet and glue insulation methods imply the use of only 100 mm of ecowool. Trim rollers will help to remove excess insulation.
It is very important to take into account the widespread mistakes when insulating houses with ecological wool. The chimney passage assembly outside is laid only with completely non-combustible substances. The thickness of the insulating layer is selected in accordance with the requirements of fire regulations. An open backfill with a 10% margin allows you to fully compensate for the shrinkage of the insulation.
It is recommended to insulate the house with ecowool in the warm season, and plan the waiting period so that other work can be performed.

You can learn more about how to prepare the roof for insulation with ecowool.
The comment was sent successfully.