How to bend rebar at home?
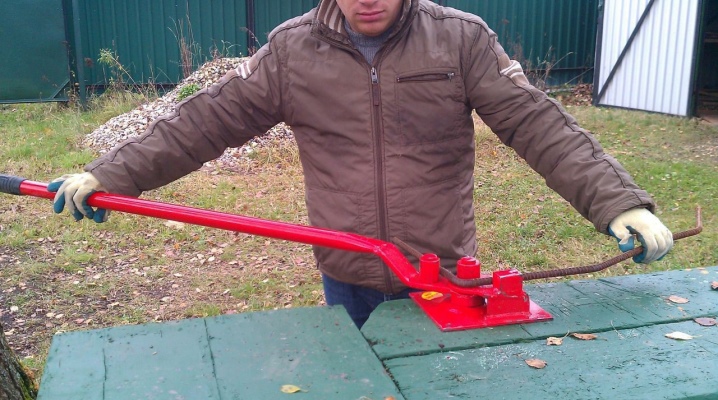
Gone are the days when a home craftsman bent rods and small pipes at night against an iron or concrete lamppost, a steel fence, or a neighbor's fence. Rod benders are produced in large quantities - like bolt cutters, grinders and hammer drills of various capacities, they are available to everyone.
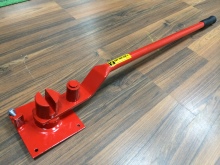
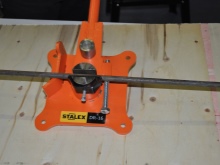
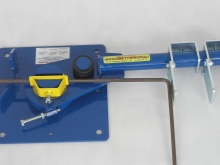
When do you need rebar bending?
A common reason for bending reinforcement is to create steel frames from it. Their primary application is to reinforce concrete slabs and foundations. Without a steel frame, concrete cannot withstand increased loads and cracks, crumbles not over decades, but over years.
Reinforcement is the "backbone" for any foundation and reinforced concrete panels. One of the highly specialized areas - self-made slab made of concrete and connected (or welded) reinforcement rods for a septic tank or a small homemade ladder... The second application of bent reinforcement is creation of floors and lattice structures by means of welded seams: bent reinforcement rods and profile steel are used for the manufacture of doors, railings, fence sections, window grills and much more.
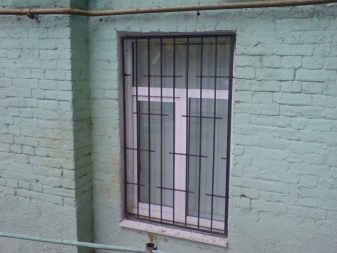
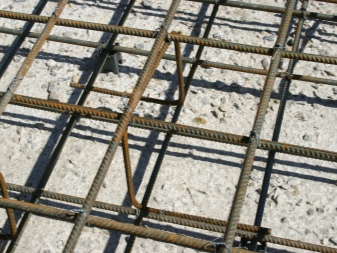
General rules
The fittings are bent by the cold method - without heating over a gas burner or in a fire (or brazier). This also applies to steel - when heated, it changes its properties, in particular, it loses its strength, it cannot be bent in this state. Composite materials, fiberglass will simply burn and crumble, as soon as you heat the rod to at least a few hundred degrees.
Do not file the bend - the reinforcement should not have sharp corners. It is unacceptable to bend it sharply and at an obtuse angle when heated, as pipes sometimes bend. Such methods of relief will lead to premature (at times) destruction of the entire structure.
The bending radius of the reinforcement should be equal to 10-15 rod diameters. It doesn't matter if the rod bends into a ring or an arc, it is not recommended to take a smaller diameter: more efforts will be required.
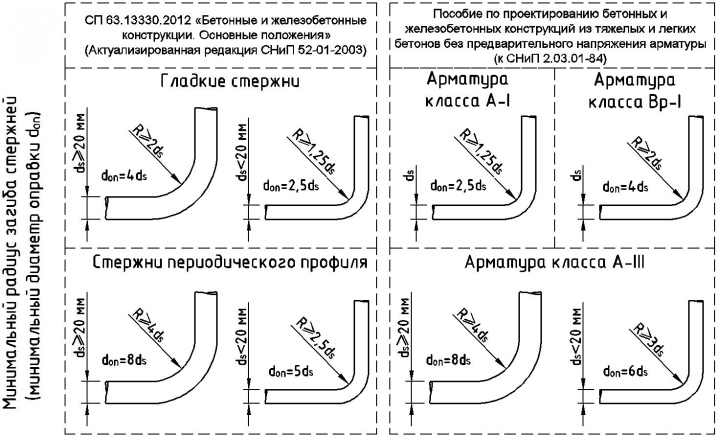
So, the bending radius of a rod by 90 degrees with a diameter of 12 mm is 12-18 cm, for a 14 mm rod - 14-21 cm, for a thickness of 16 mm - 16-24 cm. When creating a 180-degree (U-shaped staples, after turning the ends of which threads are tapped on them for nuts) or 360-degree bend, the same standard radius applies.
A larger radius, on the contrary, although it will preserve the integrity of the rod, will not give it sufficient elasticity.
The only exception is a ring, the ends of the rod on which are welded, or an arched (rounded at the top) structure of many rods, used to create wall (door) vaults and ceiling-roof domes.
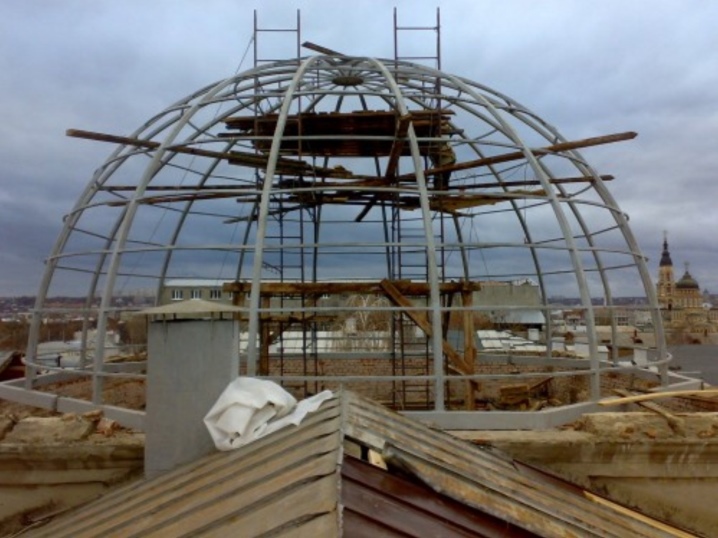
Steel, despite its relative unbreakability in comparison with the same aluminum alloys, carbon and sulfur-containing iron, can give a slight break, while heating up from internal friction, which violates the technology for 100% cold bending. Some varieties are easy to damage. That is why the standard for the bending radius was adopted. They approach fiberglass even more carefully - like fiberglass sheets, fiberglass gives a "blurred" break, the exact middle of which is impossible to determine. This is evidenced by the change in the brilliance of the surface of the rod at the point of bending to a matte sheen.
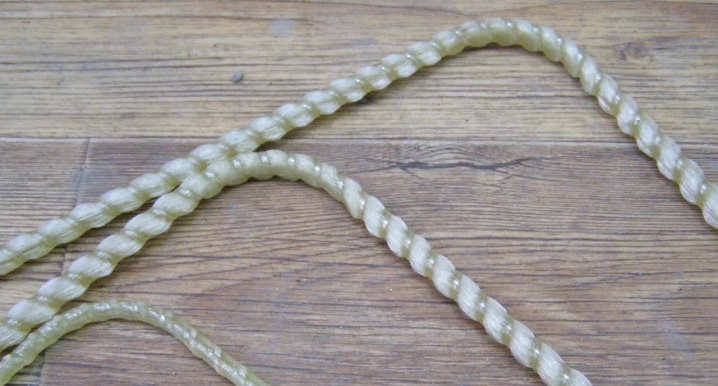
Special devices
The bending machine (rod bending machine) can be either manual or mechanical.And on both of them, you can not only bend the rod into a ring, into a "turn" and "turn", but also make letters, numbers and other symbols from pieces of such a rod, make tiles (curls) for railings and gates. The last area of application is for creating the basis of a luminous sign.
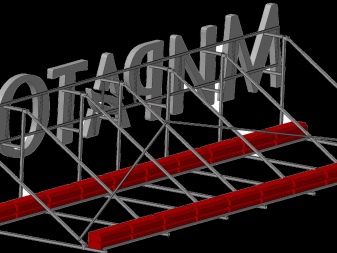
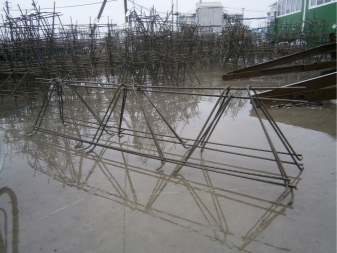
Manual
The simplest rod bending machines appeared after the reinforcement. They are used both for bending smooth round and square rods and for forming ribbed ones. It is not easier to bend any of the rods - both the smooth and the ribbed rod have the same diameter. The same machine can handle both. The thicker the rod, the more and more powerful the rod bending is needed for it. Too large a machine will "stretch" the bending radius, a small machine will break itself.
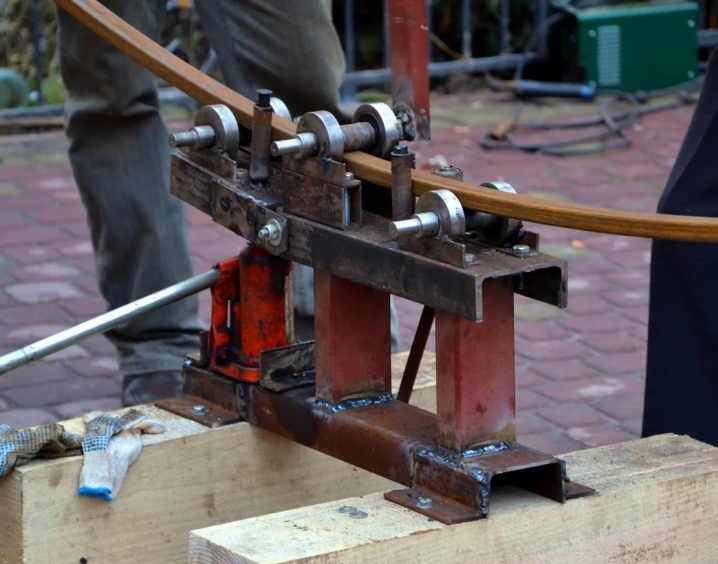
The manual machine is operated by one person. Or several - when the rod is rather thick, and the efforts of one worker are not enough, despite the long, comfortable and durable pressure levers. The simplest model includes a bending disc, on which there are several pins, much thicker than the largest rod, up to 10 cm long. The disc in the center is rigidly connected to an axle (hub) rigidly connected to the drive shaft. Not far away (at a distance of one or two disk radii) there are stops, between which the rod is inserted in order to avoid its deflection during bending. Additionally, the rod can be fixed so that it does not move along unnecessarily. The entire bending mechanism is mounted on the frame of the device.
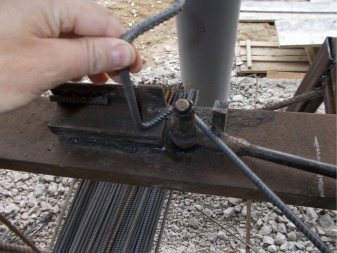
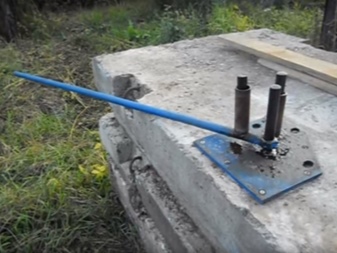
A protective screen made of sheet steel can be used - it will protect workers from fragments of the bending rod and its sudden jumping off the rod bending. The worker on the other side of the device rotates the disc by turning a long lever.
A powerful bolt cutter with levers 1-1.5 m long is used to cut the rods. In special cases, a pipe bender is used - with its help, rods are also bent, and not just pipes. Both the pipe bender and the rod bender are easy to fix - holes are drilled in its working (bending) part. With their help, the device is fixed on any supporting structure, in which holes for bolts are pre-drilled.
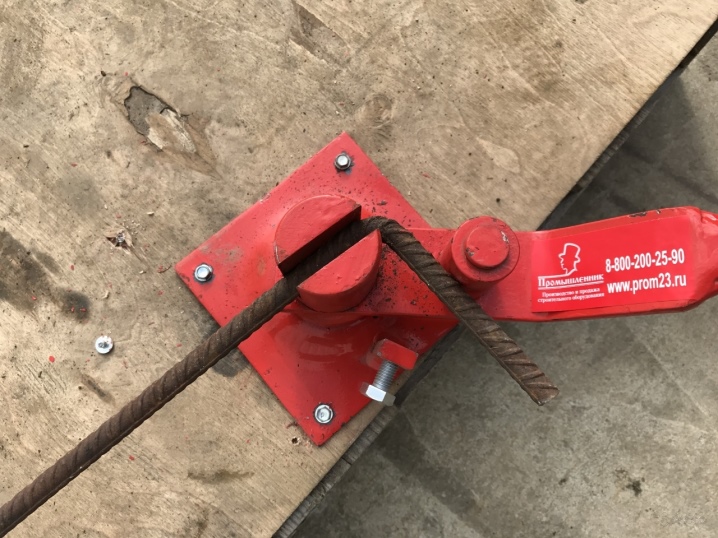
Mechanically driven machines
The mechanized rod bending uses the torque from the gearbox driven by a powerful motor instead of the efforts of the workers... It is quite difficult to make such a machine at home: for rods with a diameter of up to 16 mm, a mechanism would be required that can lift the elevator car.
Super-thick rods (20-90 mm in diameter) can be bent only in production. The more powerful the machine, the more thin rods (from 3 mm) it is able to bend: it is not easy to do such work alone with pliers or a vice. Professional rod and pipe benders use a hydraulic drive - its power is not less than the efforts created by a jack.
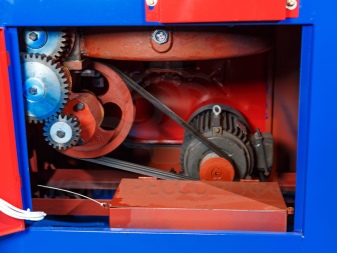
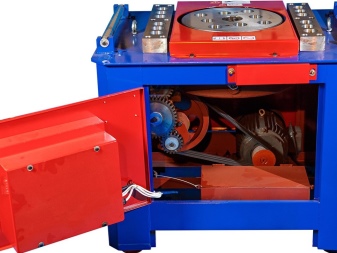
Homemade devices
Not every master will immediately acquire a ready-made pin-and-pin. But that's why he is a master, to get out of the situation without spending almost a penny to bend the reinforcement... Having looked at the design of the finished machine, the master will easily make a device that replaces it. This is especially necessary for those who are building a house "from scratch" and faced with the laying of a reinforced concrete foundation, and also cooks wickets, fences, gates, doors from reinforcement to order.
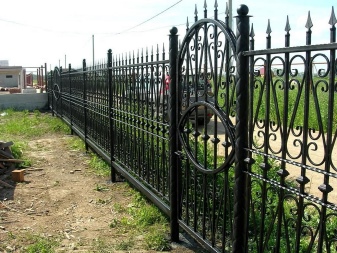
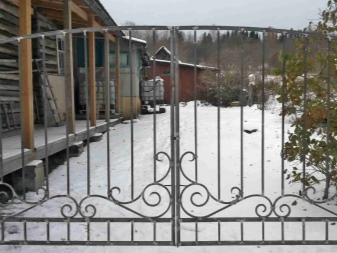
The main part in a homemade machine is a steel frame - a casing. A lever drive and a bending disc with thrust pins are attached to it. Instead of a pin, an angle profile is also used. A rotating platform with a lever, on which the bending and thrust pins are located, is built taking into account the thickness (diameter) of the pin and the amount of reinforcement being processed. Such a pin is fixed either to the workbench or to the floor of the working room.
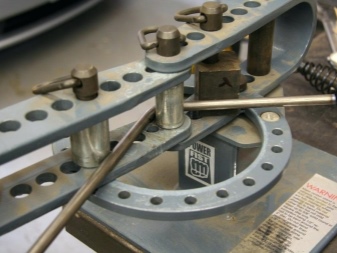
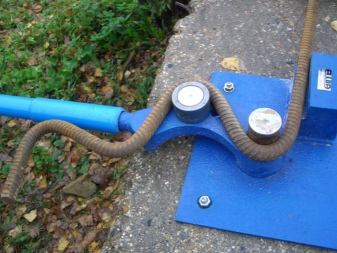
How to bend by hand?
Rods of small thickness - up to 8 mm - are bent with their own hands, for example, with the help of pipes. One of them - persistent - is fastened in a powerful vice.The second - bending, replacing the main "finger" in the machine - is put on the reinforcement, and with its help this rod is bent. No "handicraft" method can compare with the quality of work performed on the machine. The fact is that it is more difficult to control the correctness of the fulfillment of the main requirement - 12.5 rod diameters - manually.
In the machine, the worker is secured by a thrust wheel, on which the pin bends.
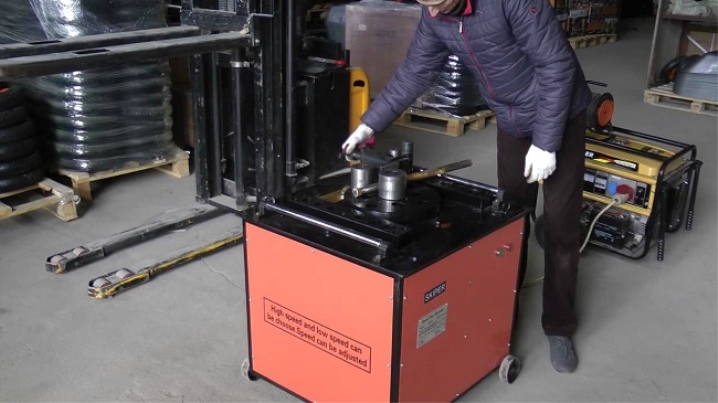
Typical mistakes
To avoid one of the common mistakes, bend correctly.
- Do not bend composite and fiberglass - it cracks, after which it is easy to "finish off". As a result, it will break. It is more correct to cut it into the required segments and tie their ends, leaving a small indent.
- An insufficiently powerful machine will break when you try to bend a too thick rod on it. If in the process of bending either the pin itself breaks, or the machine, the worker bending the armature by hand, is injured either by a splinter or by loss of balance (according to the laws of physics). An incorrectly set motorized machine breaks the motor and / or gearbox.
- A thin rod inserted into a powerful machine bends too quickly - this can cause it to heat up. As a result, the process technology itself will be disrupted. The fact is that inside the bend, the metal or alloy undergoes compression, outside - stretching. Both should not be too impetuous.
- Do not work on a machine that does not have protection against particles of bending reinforcement. This is especially true of non-metals, of which the composite base is made.
- When bending with the "super heavy" machine, designed for fittings with a diameter of 4-9 cm, thinner pins are placed in a row, and not in a bundle resembling a wiring harness. This will give you the same bend radius.
- Do not bend the reinforcement on nearby trees. Prepare the simplest workplace. One of the best ways is to concrete a thick-walled pipe in the ground. Short - up to 3 m - pieces of reinforcement are easy to bend directly in it. Some craftsmen weld a funnel with curvilinearly diverging walls to such a pipe, simulating the working surface of the bending (axial) wheel of the machine.
- Do not jerk when bending the rod. - they will provoke the appearance of microcracks even in a pin made of the most flexible, torsion-resistant steel.
- Do not bend the reinforcement using an adjustable wrench, bolt cutter, pliers (even the most powerful ones) and other tools that are not suitable for such work.... Such work will do little - it is more likely that one or another instrument will be damaged.
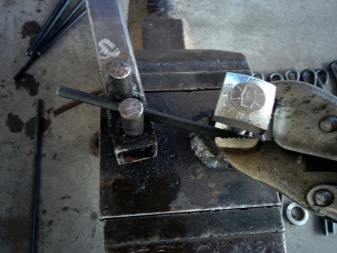
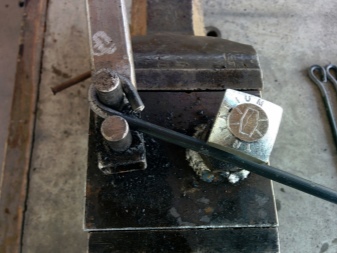
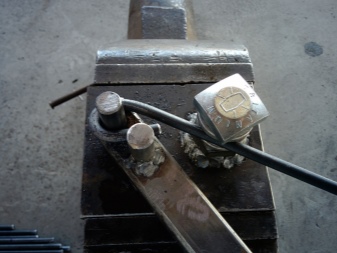
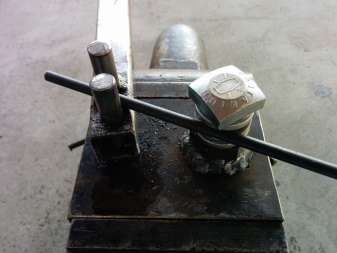
Compliance with these rules brings excellent results - even bending - even in completely "artisanal" conditions.
An experienced craftsman can easily bend fittings even without a machine with his own hands. The disadvantage of "self-bending" is increased trauma.
If rebar bending is not a "one-off" "make and forget" exercise, but a service delivered to the stream for a large number of local customers, then get a machine - at least manual, but quite powerful, and set it up correctly.
For information on how to bend reinforcement without tools, see below.
The comment was sent successfully.