Features of modular houses
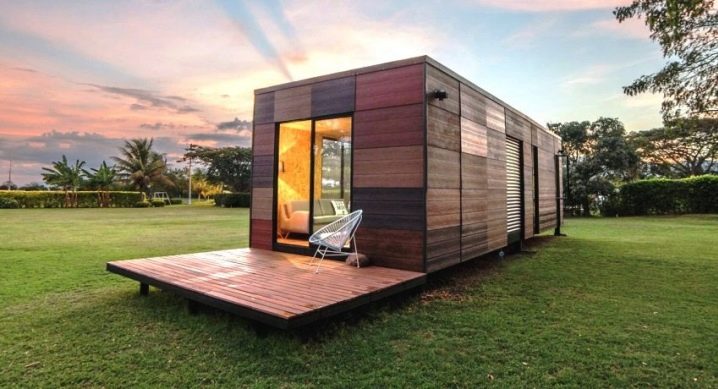
It is useful to know the features of modular houses for everyone who decides to equip their territory, at least just as one of the possible options. Having studied the projects of houses for year-round living and the peculiarities of their construction, it will be possible to assess the real prospects. You will also need to familiarize yourself with mini-houses from block containers and with the features of the production of prefabricated houses.
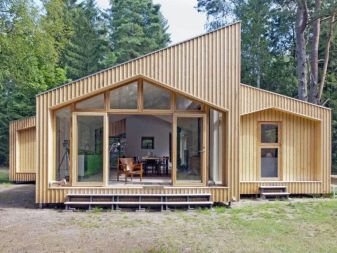
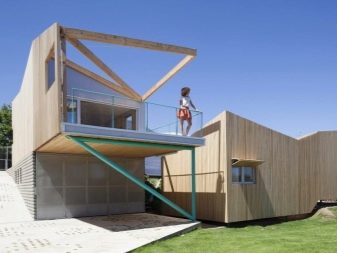
What it is?
The production of prefabricated modules of residential buildings in Russia has not yet become a mass business. This undertaking appeared relatively recently. It is worth mentioning right away that such an option is fundamentally different from the frame construction approach that is already familiar to many. Completely finished blocks are brought to the sites, there is no need for revision.
In many cases, there is a factory-completed, controlled finish immediately; sometimes even communications are laid in advance.
Modular elements do not contain fragile materials. This technology is also not designed for the use of "wet" processes, that is, brickwork, the use of foam concrete blocks. Therefore, the variety of designs is forced to limit, however, it still remains very large.
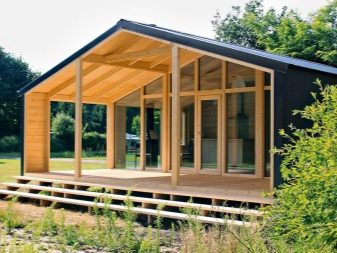
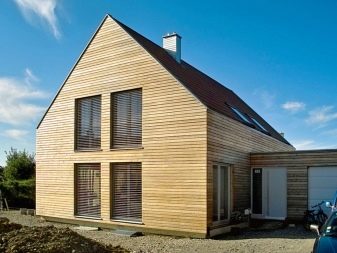
Mostly modular houses are placed on pile-screw foundations with simple strapping. More complex solutions are practiced only for areas with obviously unstable soil.
An important role is played by the sealing of the joints, in many respects it depends on this work how high-quality dwelling will be in the end. The gaps between the components are preferably filled with mineral wool. Modular housing can be used for both permanent and temporary residence. Projects of bath and country houses of this type have also been worked out. At the request of customers, any architectural and structural details can be added, which makes it easy to get away from the stereotyped monotony.
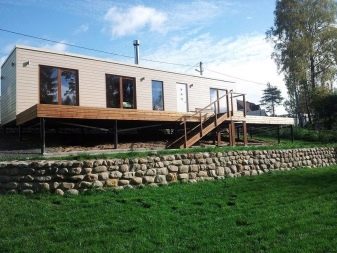
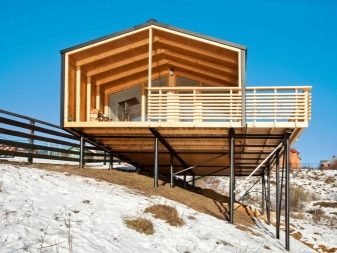
Advantages and disadvantages
Those who need economical and at the same time fast construction tend to choose modular houses. Even in the middle zone, the number of warm sunny days is limited, and this greatly complicates the work. Modular technology allows you to fit into a much narrower "weather window" than frame or even more brick housing construction. All the main units and elements of the house are created in the factory floor, in fully controlled conditions. Therefore, the impact of temperature and humidity jumps, which are inevitable with the usual construction option, is excluded.
Experienced manufacturers of home building modules try to control the process meticulously. The likelihood of marriage is therefore minimized.

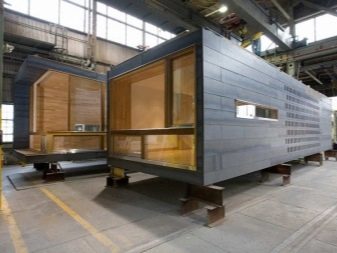
Practically finished structures are obtained mainly in 14-22 days. It also takes about 7-10 days to assemble the house on the site and equip it to complete harmony. Even taking into account the subsequent fine finishing, an undeniable time saving is achieved. Additionally, you can save it by preparing the foundation during the period of factory production of structures.
The cost, of course, may differ, taking into account the design, the volume of the building, the materials used and other nuances. However, these circumstances, and even the preparation of an individual project, do not lead to an excessive rise in cost. Since the mass of a modular dwelling is relatively small, it is allowed to put it on lightweight simple foundations. Energy efficiency is also well ensured.
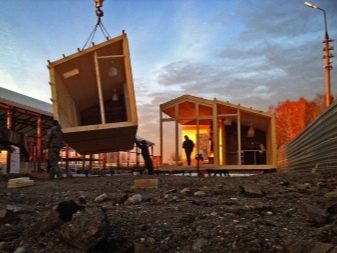
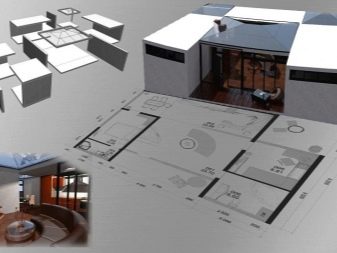
However, even advanced modular construction has a number of weaknesses:
- when choosing an individual project, you will have to wait a long time;
- typical options do not always satisfy the entire range of parameters;
- the size and number of floors are limited (despite the possibility of adding new rooms);
- the number of manufacturers is not as large as when choosing traditional building materials;
- modular construction is carried out only with an advance payment, because manufacturers must purchase materials and incur other costs.
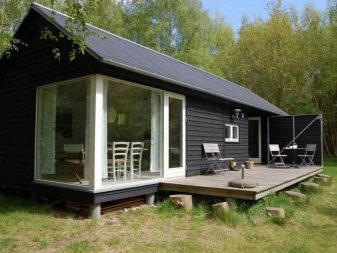
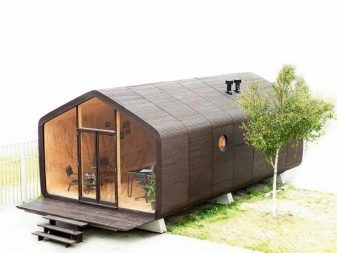
Overview of types and projects
Two-story
For year-round living, that is, for permanent use, the "Flagman" project is well suited. Its total area is 246 m2. The building has dimensions of 10x14 m. Notable features include:
- providing energy needs with solar panels;
- use of Fakro roof windows;
- insulation with basalt wool;
- pile foundation;
- autonomous sewerage;
- 38-meter terrace;
- 5-meter vestibule of the 1st floor;
- kitchen-dining room with an area of 21.2 sq. m on the 2nd floor;
- 4 meter balcony on the 2nd floor.
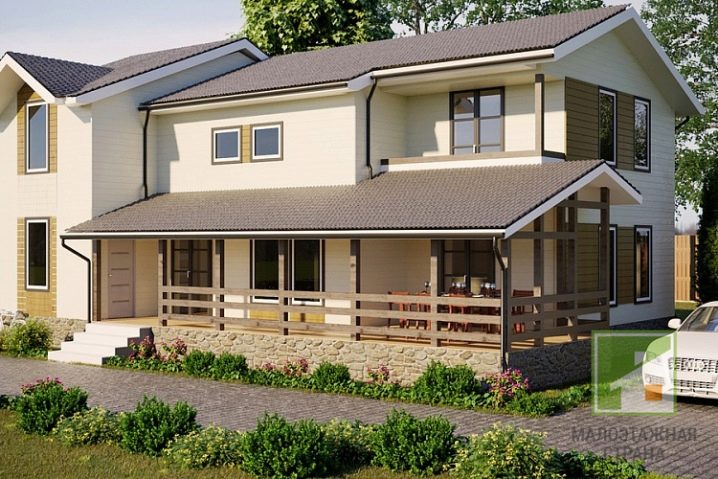
The Iron project is also very attractive. The area is 250 m2, and the dimensions are 13x14 m. The attic is not provided, the entrance doors are made of metal.
Foamed polyurethane foam is used for insulation.
The living room on the ground floor reaches 18.1 sq. m. The size of the hall is 20.7 m2. Tambour has an area of about 5 sq. m. A separate boiler room is provided. There is a second light on the top floor. The second floor also has a couple of bathrooms.
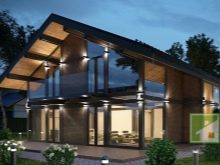
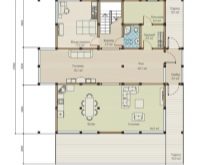
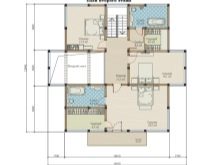
Speaking of modular mini-houses, it is worth taking a closer look at the Leader-Barn project. It is being built in the spirit of the barnhouse style. Even on the first floor, a second light is created here. Upstairs, it will also be equipped. The largest room in the lower tier is a kitchen and dining block with an area of almost 12 m2.
Also there will be highlighted:
- hall;
- bathroom;
- porch;
- living room for 8 "squares".
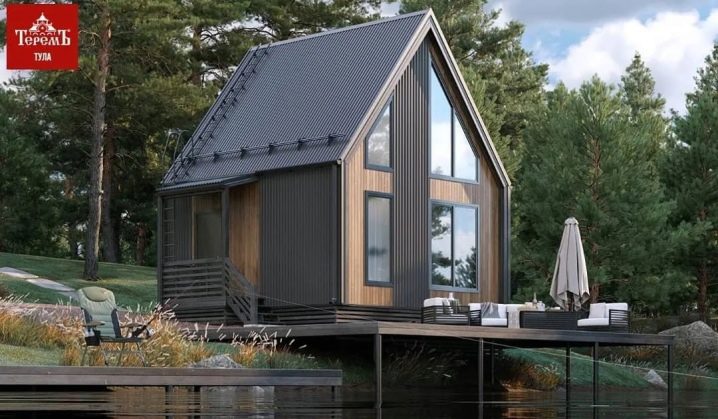
Another version of a two-story house involves the arrangement of a 15-meter terrace. Directly from it you can get into the kitchen-living room of 21 m2. After the kitchen-living room there is a hall, which communicates with the living rooms and a rather large bathroom. Upstairs will be:
- as many as 2 bathrooms;
- 3 living rooms;
- balcony;
- wardrobe.
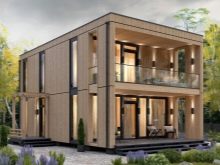
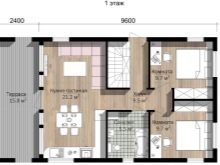
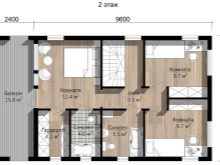
One-story
There are also quite a few options for ready-made modular houses with a height of 1 floor. The "Kama" variant has an area of 42 sq. m. The developers have provided for the deployment of all major networks, including:
- heating;
- power supply;
- sewerage;
- ventilation;
- water pipes.
The living area is about 38 sq. m. Provides for the use of vapor barrier membranes and mineral wool insulation.
When designing a flat roof, there will be a choice between metal tiles and galvanized corrugated sheet. The foundation is covered with wooden beams.
16-meter terrace and almost 20 sq. m kitchen-living room are quite comfortable; the bathroom, however, is relatively small.
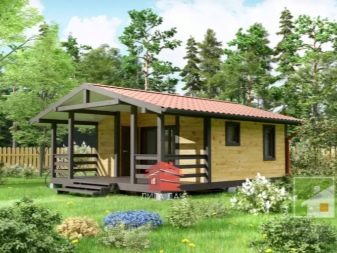
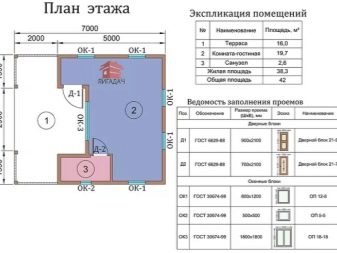
From block containers
Prefabricated houses can be created not only from blocks, but also from containers for sea transport. In one of these options, the total area reaches 60 sq. m. However, it can be easily increased if necessary by attaching new containers. The designers preferred the use of an advanced hardfacing roof. The walls will be covered with a material imitating timber, the ceiling will be made of Euro lining.
Choice of flooring is formed with laminate or ceramic tiles. The water supply to the shower stall will be supplied by an 80-liter boiler. Ventilation is improved by an exhaust fan. The living room-kitchen area reaches 25 m2, and there are also 3 bedrooms inside; the terrace area is 30 sq. m.
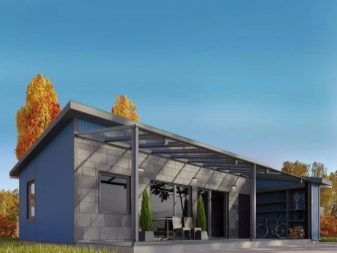
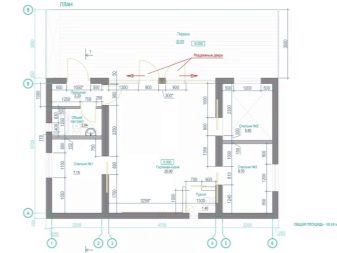
Combined
The above-mentioned opposition of block-modular dwellings with frame dwellings is not entirely correct, because these options for modern construction may well be combined.In the project under consideration, the total area reaches 73 "squares". The developers have provided for many types of insulation to choose from - not only popular basalt and mineral wool, but also ecowool, stone wool, and mezhventsovy insulation. Inside the house are:
- 2 bedrooms 11 sq. m;
- 4-meter bathroom;
- kitchen and guest space of 24 m2.
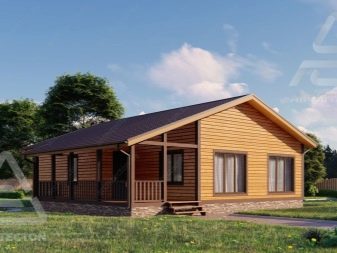
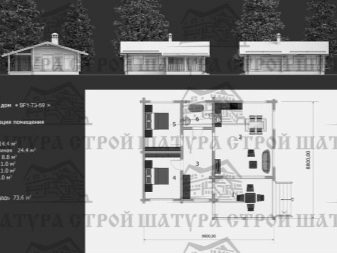
Scandinavian
Small modular houses are also available in Scandinavian style. One of these projects involves the use of dry calibrated planed boards.
The roof is equipped with a well thought out drainage system.
A 3-meter bathroom has a 100-liter boiler. The total area reaches 28 m2, which is quite impressive by the standards of city apartments.
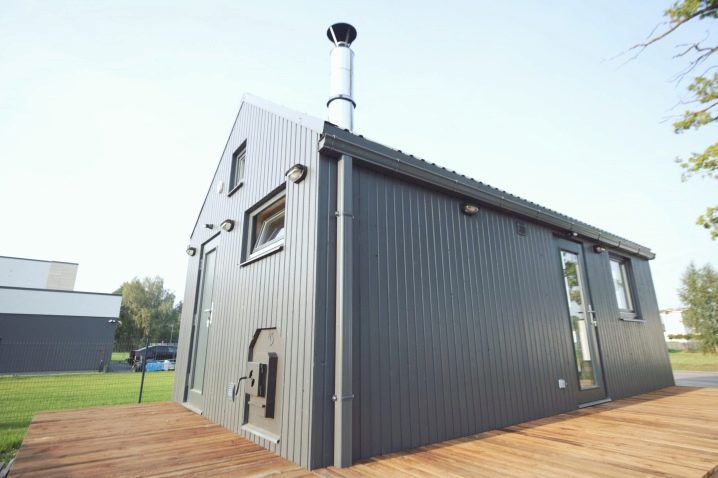
Nuances of construction
The choice of technology is determined by how the dwelling will be used. Houses for permanent settlement must have thick, reliable walls. This is due not only to the protection against cold, but also to other safety considerations. It is imperative to consider the vapor barrier and thermal insulation. The requirements for the "pie" during construction are no less high than in other cases.
Most often, basic modules on a steel frame are prepared with their own hands with the addition of insulation panels. In summer cottages, in suburban areas rarely visited, the walls can be made thinner.
Predominantly modular construction means choosing between a minimalist design or a high-tech exterior. Finishing possibilities inside are limited only by the area and design features of a particular project. It is worth noting that when self-building a modular dwelling, it is advisable to reduce the proportion of glazing in comparison with the branded design in order to simplify the work.
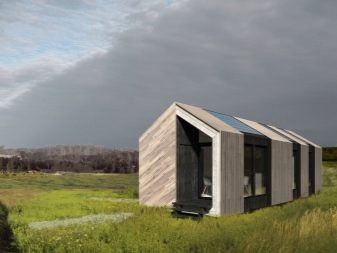
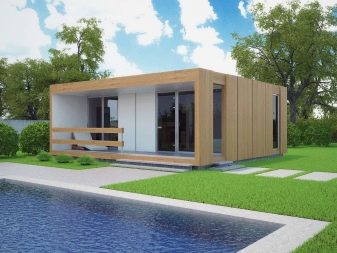
The veranda extension is not as difficult as it seems. And then it becomes a much better addition than a simple terrace. You can improve the appearance and make it more harmonious with the help of natural finishing materials. Lovers of the original look will be happy with non-standard textures. A romantic touch is easily created with fine tiles and original lighting.
It is useful to make a polished concrete floor inside. It is sequentially processed with a grinder using discs with increasingly fine grains. If you give the surface a gloss, it will not differ much from marble. But you can achieve a glossy effect by applying enamel on a polyurethane base.
For maximum warmth, the floor is covered with laminate, and tiles can be traditionally used in the bathroom and kitchen.
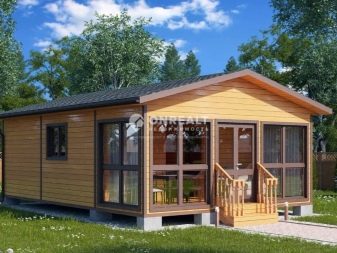
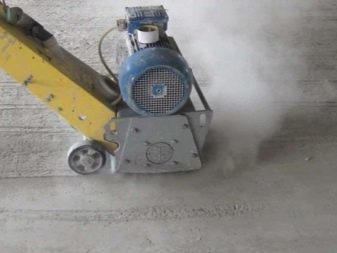
- visually ennoble the outside;
- equip with windows and doors (preferably anti-aircraft type);
- equip with an insulating layer.
Even with independent construction, it is more reasonable to turn to specialists in order to connect communications correctly. The choice between a gable and a pitched roof is at your discretion. Designing houses is possible using any simple software. The containers can simply be placed on level surfaces without any foundation. Under heavy load, however, you will have to lay out reinforced concrete slabs or form a strip support.
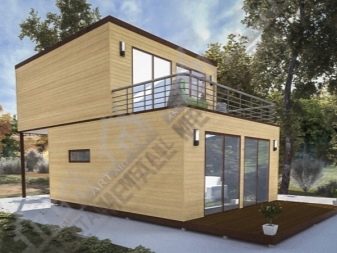
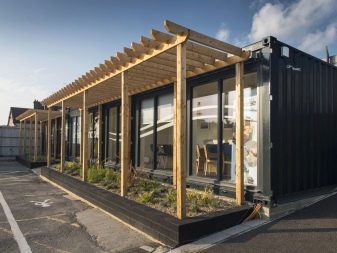
The comment was sent successfully.