Fiber-reinforced concrete panels: types and applications in construction
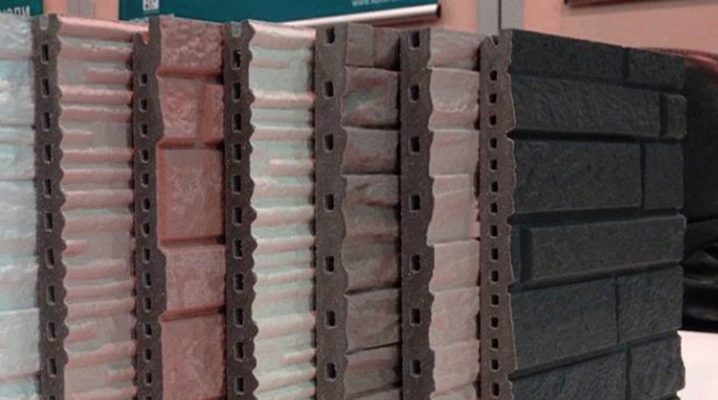
Fiber-reinforced concrete panels are a new generation of finishing building materials. As an alternative to plastering, they have all the advantages of their predecessor, but without the characteristic disadvantages. This building material allows you to finish the house with high quality and in a short time, which will delight you with its high strength and long service life, and also decorate the facade of the building with an excellent texture that imitates various finishing materials, for example, masonry and brickwork, wood, and so on.
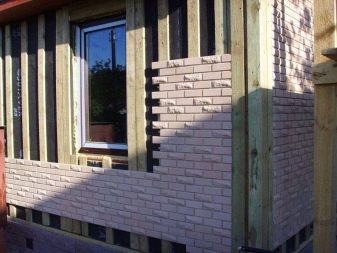
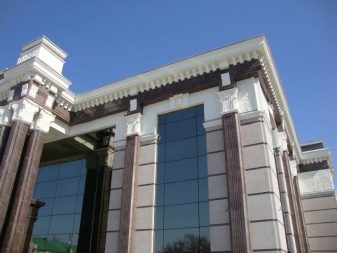
What it is?
Fiber concrete - synonymous with fiber cement panels - is a type of finishing material produced in the form of slabs and siding panels. The main part of the composition - from 85 to 90% - is cement, about 10-15% more - various minerals and fiber (cellulose or synthetic fiber).
The latter serves as a reinforcing component that reinforces fiber-reinforced concrete panels, giving them elasticity and, as a consequence, increasing bending strength.
The front of the panels is a weather-resistant coating that imitates brick or masonry. In addition, the composition of fiber-reinforced concrete panels contains hydrophobic additives that increase the moisture resistance of the material by reducing porosity, but contribute to the vapor permeability of the panels, a property responsible for the normal ventilation of the wall.
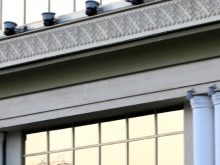
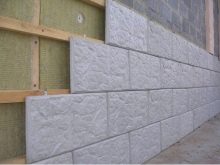
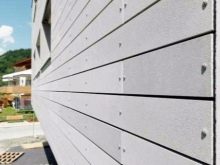
Specifications
Approximate characteristics showing the possible parameter values for various types of fiber-reinforced concrete panels. These include:
- density - from 1.5 g / cu. cm;
- panel weight - 16-26 kg / sq. m;
- bending strength - from 20 MPa;
- impact strength - from 2 kJ / sq. m;
- moisture absorption - 7-20%;
- panel thickness - 6-35 mm;
- panel length - 1.2, 1.5, 1.8, 2.4, 3.0, 3.6 meters;
- panel width - 190, 455, 910, 1200, 1500 mm.
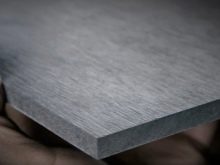
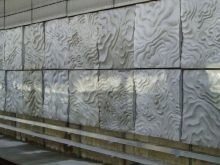
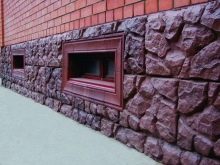
Varieties
Fiber-reinforced concrete panels are made with various external designs that imitate various finishing materials.
The following types can be distinguished:
- products imitation masonry, vary in size and shape, imitating different types of stone in color, texture, degree of detail and other parameters;
- imitating brickworkMost species mimic red and yellow bricks, although the choice is quite varied and unlimited with two options;
- panels imitating wood trim, a wide selection of breeds with their inherent color and texture;
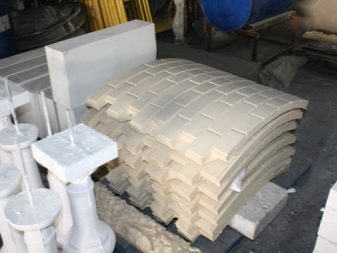

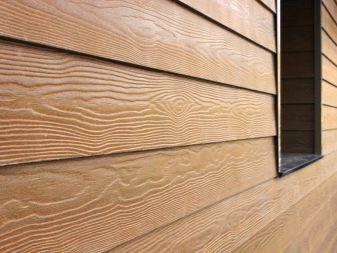
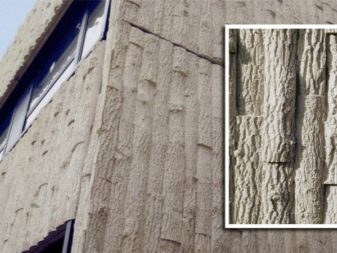
- fiber concrete slabs with a texture imitating stone chips, a wide range of colors, there are non-monochromatic types with the addition of other shades, and panels also vary in size of chips;
- monotone panels, imitating plastered walls;
- monotone slabs with a smooth surface mainly used for finishing large shopping centers, office buildings and similar structures, the surface lends itself well to painting and other decorative finishes.
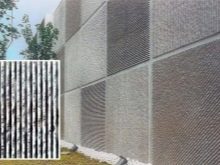
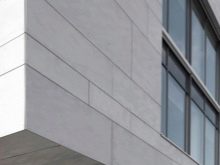
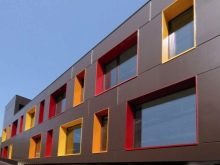
A certain percentage of panels are sold with an unpainted surface. This feature allows you to choose the color and shade yourself, if there is no suitable option among the manufacturer's assortment.
On the one hand, this feature expands the variety of external performance of the panels, on the other hand, additional painting work is required, which takes time and money. The cost of unpainted fiber-reinforced concrete panels is 10-20% lower than similar painted models.
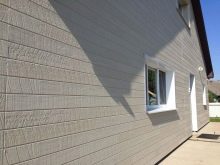

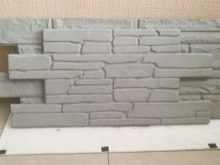
Purpose and scope
The use of fiber-reinforced concrete in construction works can achieve a number of positive effects, including:
- reduction in the total weight of the structure;
- preventing the formation and propagation of cracks on the wall surface;
- increasing the strength of the wall;
- thinning of wall structures;
- the use of new, more advanced construction technologies;
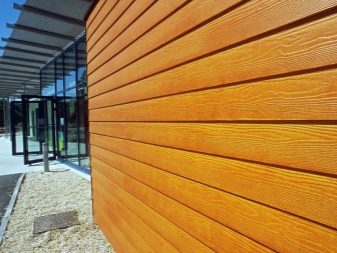
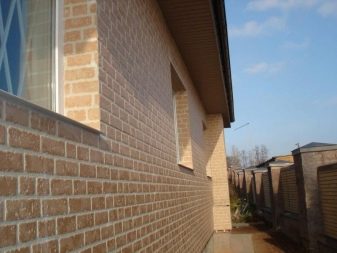
- obtaining the appearance inherent in wood and stone finishes, but with more optimal performance and a simpler installation process;
- finishing of facades with curved geometry;
- reconstruction and restoration of old buildings, the lightness of building materials is especially relevant in this matter;
- elimination of uneven sections of the facade;
- obtaining a durable and smooth surface for further decorative finishing work.
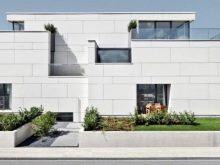
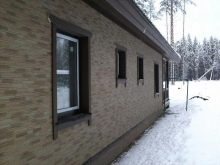
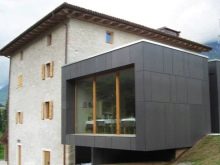
With the use of fiber-reinforced concrete, objects with various features are finished, namely:
- facing of apartment and private houses and cottages;
- decoration of shopping centers, hotels, sports complexes, airports, supermarkets, government and public facilities;
- finishing of ventilated facades;
- interior decoration;
- facing of balconies.
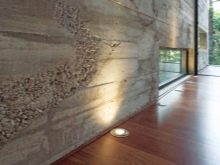
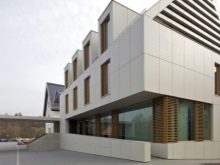
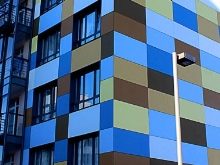
The technical characteristics of fiber cement are quite high. Today, more and more facade products made of glass fiber reinforced concrete and foam glass are used at construction sites. Such thermal panels reliably protect any structure.
Advantages and disadvantages
Modern equipment and new production technologies using high pressure and steam treatment make it possible to produce material with excellent performance and aesthetic qualities. Consumers choose fiber-reinforced concrete panels due to their positive qualities.
- Long service life. The duration of use of the panels varies in the range of 25-50 years.
- Low weight of products. Slabs and siding panels are relatively easy to lift, install, transport and store. And the load on the wall is also reduced, and less powerful means are needed to fix it.
- Simple and convenient installation. The technology of installing slabs is much simpler and less costly than that of plaster. The large dimensions of the panels reduce the amount of work and the mounting means required for fixing. In addition, it is easier to detect and correct unevenness when installing panels. Installation work can be carried out with a minimum set of tools and a small baggage of knowledge about the installation method. Moreover, work can be carried out in conditions of negative temperatures.
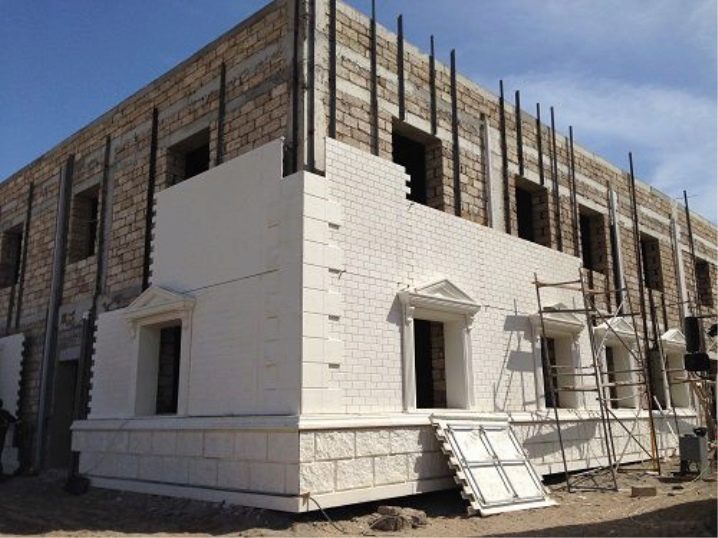
- Versatility. The panels are presented in various size and format options, which allows you to choose products for surface finishing with different features.
- High strength. Fiber cement panels withstand shock loads, vibration, friction, bending pressure well.
- Good thermal insulation performance. Provided by the use of cellulose filler, they reduce the power of the necessary heat-insulating materials in the finish, for example, the thickness of a layer of mineral wool.
- Frost resistance. Products retain their structural integrity and appearance over many freeze / thaw cycles. This fact makes them an excellent facing material for regions with a harsh and continental climate, in which hot summers are replaced by cold winters, which corresponds to almost the entire territory of the Russian Federation.
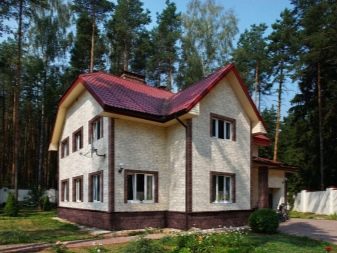
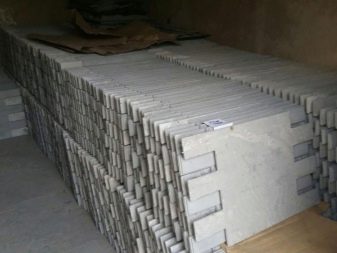
- High waterproofing performance. Thanks to special additives, the panels are not afraid of moisture and can be washed using water both from the front and from the back.
- Resistant to temperature extremes.
- They do not corrode, do not rot, do not dry out.
- Completely environmentally friendly composition. In production, natural raw materials and non-toxic additives are used, microparticles of the material do not provoke allergic reactions and do not contribute to negative processes in the body. No asbestos or harmful resins.
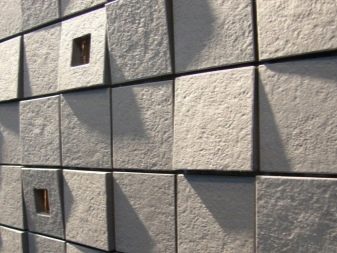
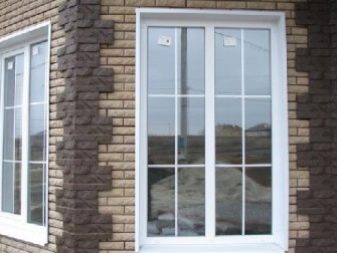
- Resistant to sunlight. The color of fiber-reinforced concrete does not deteriorate under the influence of infrared radiation throughout its entire service life. Ultraviolet light does not destroy the structure of the coating - it does not lead to cracking, as in some finishing materials.
- Good insulation. Decreases the level of incoming and outgoing sound.
- Wide choose. The choice extends not only to the color and its shades, but also to the shape and texture of the panel coating.
- Easy cleaning. The material is self-cleaning in the pouring rain, in addition, you can wash the surface with a garden hose.
- Absolute fire safety. The material is 100% non-flammable and non-smoldering, and does not melt from direct fire.
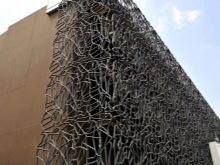
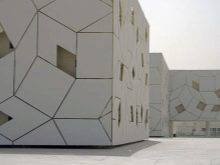
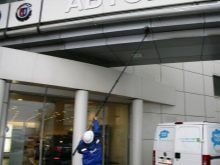
In addition to the positive qualities, fiber-reinforced concrete panels have several disadvantages.
- Vulnerability to prolonged exposure to moisture. Despite the high waterproofing qualities, with prolonged exposure to water, the cement in the composition of the products still begins to absorb water. The saturation can increase up to 10-20% and lead to slight deformation of the panels - up to 2%, which does not affect the appearance or structural integrity in any way, the flexibility of the panels fully compensates for this phenomenon.
- Specificity of installation work. With all the positive aspects in this matter, there is one caveat - large panels require installation by at least two people, which can cause some difficulties.
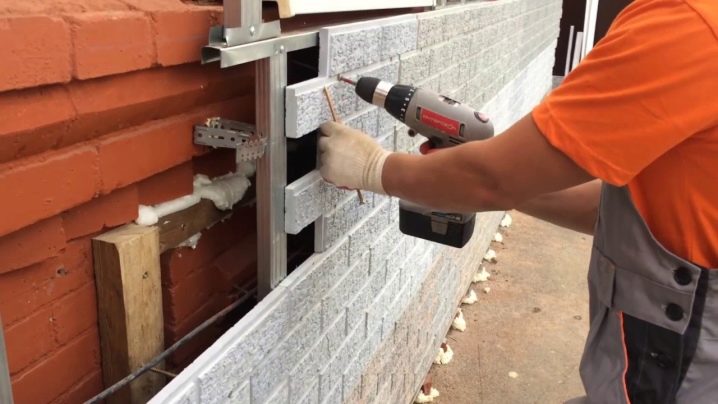
For what fiber concrete is, see the next video.
The comment was sent successfully.